Q: In a balanced cage trim globe control valve, if the test pressure is greater than the value quoted in the FCI 70.2 Standard, can it influence the result of the leak or, because it is balanced, does the test pressure value have no influence?
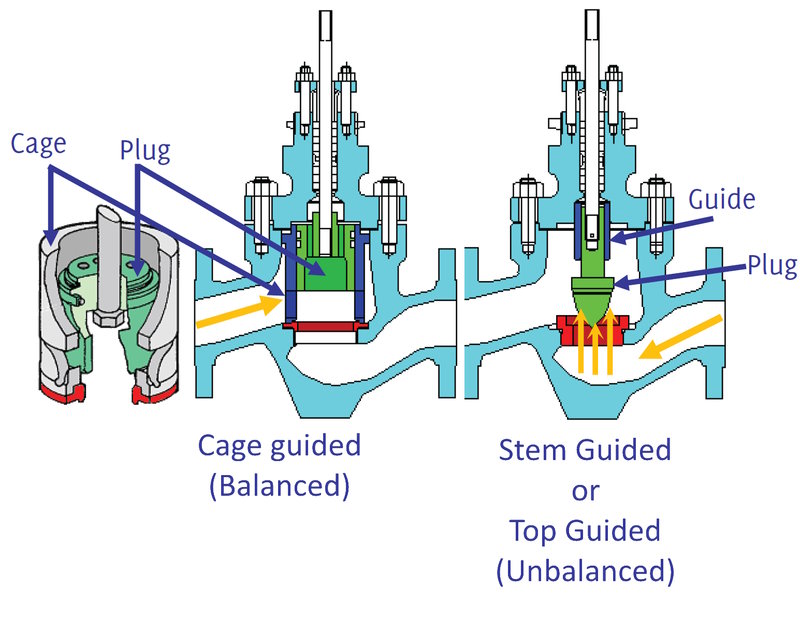
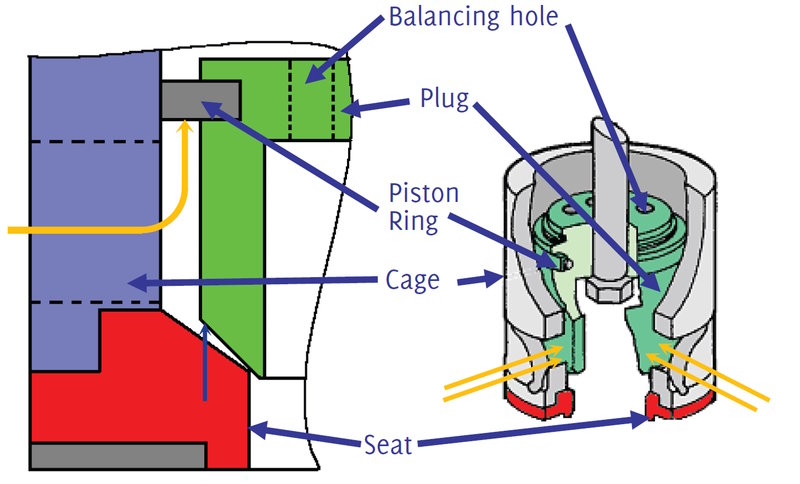
A: I will begin with some clarification of terminology. Globe control valves are usually grouped into two major categories. Cage guided and stem (or top) guided valves. Although cage guided valves are sometimes unbalanced, I will limit this discussion to the more common balanced design since that is what the question is about. In the stem guided valves, the entire process pressure is acting upward on the valve plug (and opposing the actuator). If the bottom of the plug in a small, unbalanced stem guided valve like the one pictured in Figure 1 has a surface area of one square inch, and the pressure the valve has to shut off against is 100 pounds per square inch, the upward force that the actuator would need to overcome would be 100 pounds. In that case, there would probably be no problem. But as the valve size increases (and thus the surface area of the bottom of the plug) and the process shut-off pressure increases, the actuator
size requirement can increase considerably, sometimes to the point that there is no suitable actuator. The stem guided valve gets its name from the fact that the plug is held in place (guided) by a guide bushing, most often in the valve bonnet. The problem is often solved by using a balanced cage guided valve like the one pictured on the left-hand side of Figure 1. Unlike the stem guided valve where the process pressure is pushing upward on the surface area of the bottom of the plug, the process flow (and pressure) is entering from the side and simply pressing against the side of the plug rather than the bottom of the plug, as seen in Figure 2. There are balancing holes drilled between the top of the plug and the inside of the plug so any pressure that is pushing up on the plug is also pushing down on the plug.
What the questioner has overlooked is that “balanced” cage guided globe valves are not perfectly balanced but have a small unbalance effect. Figure 2 illustrates the reason for this unbalance. On the right is a drawing of a cage guided valve’s plug, cage, seat and piston ring. On the left is a cross sectional drawing of the left-hand portion of the plug, cage, seat and piston ring. The tolerance between the cage ID and the plug OD has been exaggerated in the drawing. When the valve is closed, the process pressure comes through the triangular windows on the plug and pushes upward on the piston ring and on the portion of the plug that is not contacting the seat due to different angles on the plug and the seat. The process pressure force acting on these small areas is the only force trying to open the valve. There cannot be any difference in pressure between the top of the plug and the bottom of the hollow portion of the plug because of the balancing holes that are drilled through the top of the plug. Because of these small unbalanced areas, the answer to the question is that a test pressure greater than the value quoted in the FCI 70.2 Standard can influence the result of the leak test of a “balanced” globe valve.
About the author
Jon F. Monsen, PhD, PE, is a control valve technology specialist with more than 45 years of experience in the control valve industry. He has lectured nationally and internationally on the subjects of control valve application and sizing.
He currently hosts a web site, www.Control-Valve-Application- Tools.com, where he freely shares articles, training and professional development materials, and Excel worksheets that might be of interest to those who use or specify control valves. He can be reached at cvapptools@gmail.com.