Image © 2023 Swagelok
If the proper components are selected, hydrogen may well be the fuel that drives transportation in the future.
By Chuck Hayes, Principal Applications Engineer for Clean Energy, Swagelok
As the world moves away from traditional internal combustion engines over concerns about what carbon emissions are doing to the planet, it must find a more environmentally friendly method of powering its vehicles. One of the most promising options is hydrogen, which can be safe, cost-effective, practical, and sustainable. To enable its widespread adoption, fluid systems for hydrogen vehicles and their refuelling infrastructure must be constructed using only the highest quality materials. Components in these systems must be leak-tight throughout and durable enough to last for years and possibly decades, and not all components can deliver such performance. The nature of hydrogen presents its challenges, and requires the use of components that meet specific performance standards.
One particularly important category of components is the valves that control the flow of hydrogen within a vehicle and throughout a refuelling system. Choosing the most effective valves is critical to ensuring these applications work effectively and protect end-users in the process.
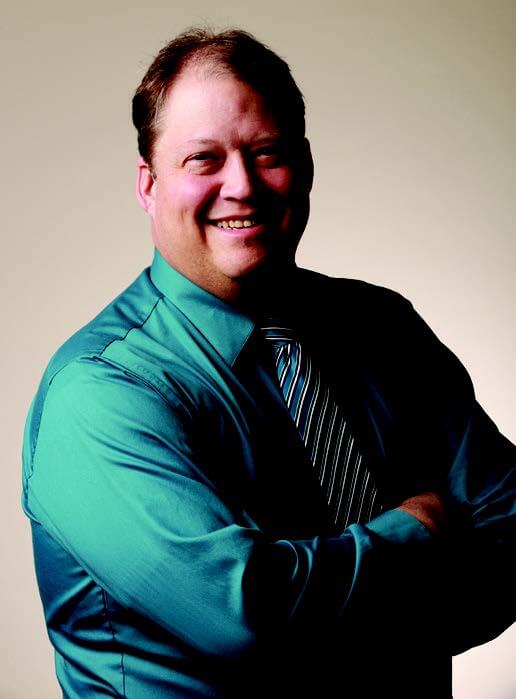
Advantages and challenges of H2 fuel systems
Hydrogen is less hazardous than other fuels because it is non-toxic and, if handled properly, is not as volatile as other compounds. In addition, hydrogen-fuelled vehicles are designed to incorporate safety equipment and protocols so they provide safe and reliable performance. Unlike traditional gasoline, hydrogen is so light that it will usually rise and disperse rapidly if leaked, making the risk of ground-level ignition much lower.
Furthermore, hydrogen can be produced much more sustainably than comparable fossil fuels. The hydrogen expended in a fuel cell does not emit carbon dioxide or other byproducts. Its sole outputs are energy and pure water, which will consequently reduce the amount of greenhouse gas generated globally and effectively help combat global climate change. However, despite all these advantages over carbon-based fuels, hydrogen presents challenges for vehicle and refuelling station manufacturers.
Hydrogen molecules within on-vehicle or refuelling equipment are extremely tiny and under varying degrees of pressure. Therefore, the importance of leak-tight performance from all components throughout the entire system is critical. If hydrogen gas escapes, it could pose a potential safety risk for end users, particularly during refuelling. In addition, leaks from vehicles or storage systems make the entire process less efficient.
Lower-quality stainless steel components may allow hydrogen molecules under pressure to diffuse into them, causing a phenomenon called hydrogen embrittlement. If left unchecked, hydrogen embrittlement can accelerate the spread of fissures and weaken components, allowing potential leaks over the service life of the equipment.
Hydrogen valves must perform
Given the critical role of valves in a fluid system, careful consideration must be given to meeting the specifications of the application. When specifying valves for a hydrogen fuel system, operators must take the following into account:
- Pressure: To achieve the desired density, hydrogen must be compressed in on-vehicle, distribution, and refuelling storage tanks at 350-700 bar.
- Stress and vibration: Systems must be able to withstand fast speeds, bumpy surfaces, and a variety of environmental factors such as inclement weather, corrosive substances, and changes in temperature.
- Safety: Refueling stations must be safely operable by the average end-user.
- Maintenance: Technicians must be able to easily and quickly install and remake leak-tight joints during servicing.
These criteria must be applied to all hydrogen valves to ensure they always perform at the highest possible levels. Leak-tight performance at the connection, shut-off, or regulation points is essential throughout on-vehicle and refuelling systems. Valves used in hydrogen fuel systems must be able to handle all the challenging operating conditions they may face, depending on the specific application and type.
Hydrogen ball valves
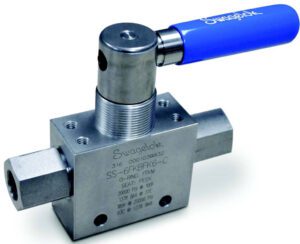
Hydrogen fuel systems use ball valves to start and stop the flow of hydrogen from one part of the system to the other. If ball valves are specified for specific applications, operators should seek valves with stem seal designs that will resist wear over time (Figure 1). Trunnion-style ball valves with direct-load designs can be an excellent choice. Their design enables leak-tight performance each time they are activated, and each time they shut off. Alternatively, bottom-loaded stem designs may prevent possible stem blowout, which could enhance the overall safety of the system. Experienced valve suppliers may be able to offer advice on which valves will work best in particular applications. Some ball valves offer two- or three-way functionality, different mounting options, and a range of flow coefficients that
can be customized to fit specific needs. Lastly, it is important to make sure that the ball valves selected are compatible with other components within the hydrogen fuel system.
Hydrogen needle valves
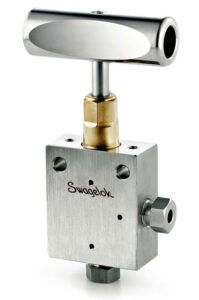
When the adjustments in a hydrogen system must be more precise, needle valves may be a better option than ball valves. Like ball valves, however, it is important to consider several factors when deciding which ones to specify. Typically, needle valves are all-metal in construction and need significant force to seal properly (Figure 2). If the specified needle valve is not able to withstand such pressure, it may deform the needle itself and possibly the seat, leading to potential leaks and expensive repairs. Secondarily, the pressure is usually applied by large air actuators to open and close the valves, which can cause the needle valve to be under intense pressure for as long as two minutes.
To handle such operating conditions, needle valves should be constructed from high-quality 316 stainless steel, which is better able to prevent deformation during repeated use. Not all needle valves are certified to the proper pressure ratings for common hydrogen applications, which means they may not be able to withstand pressures between 350 and 700 bar. A knowledgeable supplier should be able to provide pressure ratings for any needle valves and ensure they are compatible with other hydrogen-qualified components.
Hydrogen check valves
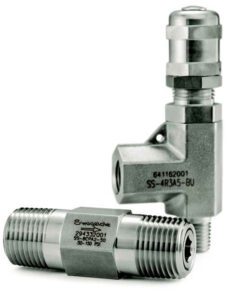
Finally, to prevent excess backflow, check valves are often used in essential safety functions at hydrogen refuelling stations (Figure 3). Unlike other general service applications, hydrogen check valves have even more challenging circumstances to endure. For example, check valves often contain springs, which are made with strain-hardened materials that can leave them more vulnerable to hydrogen embrittlement and loss of ductility than those made with high-quality 316 stainless steel.
When used in fluid systems within refuelling equipment, check valves are often subjected to large, rapid changes in pressure and temperature, which puts significant stress on their elastomer seals. That is why check valves are more suitable for hydrogen compressors than other hydrogen-fuelling system infrastructure parts. As always, material integrity is critical as well as compatibility with other components of the system. Suppliers with hydrogen expertise should be able to offer advice on such matters.
Why choosing the right valves matters
As the hydrogen mobility market continues to grow, the safety, reliability, and durability of its vehicles and refuelling infrastructure are paramount. Without appropriate standards, the long-term viability of the market could be in doubt. Ensuring the proper components are selected and specified for all hydrogen systems will enable hydrogen to reach its full potential as an alternative to traditional fossil fuels. Find a fluid systems supplier who can offer a wide range of ball, needle, and check valves specifically designed for hydrogen systems, and consider whether it can offer additional components that can make overall system operation safer and more reliable for both operators and end users. Suppliers should have hydrogen experts available to guide manufacturers on the journey to ensure their components will stand up to the rigors of operating in a hydrogen fuel system environment.
An original version of this article appeared on the Swagelok Reference Point blog: www.swagelok.com/en/blog/hydrogen-valves-what-to-look-for#.
About this Featured Story
This Featured Story is an article from our Valve World Magazine, January/February 2023 issue. To read other featured stories and many more articles, subscribe to our print magazine. Available in both print and digital formats. DIGITAL MAGAZINE SUBSCRIPTIONS ARE NOW FREE.
“Every week we share a new Featured Story with our Valve World community. Join us and let’s share your Featured Story on Valve World online and in print.”