Performing fugitive emission testing on a butterfly valve.
Shutdowns – those planned outages required to conduct inspections, repair equipment, and comply with regulations – can be stressful times for all concerned. Having assisted with all manner of valve-related activities during numerous shutdowns, Colin Zegers has some simple yet powerful words of advice: take planning seriously and start well in advance, as proper planning makes for a more efficient shutdown and a quicker plant start-up.
By David Sear, Valve World
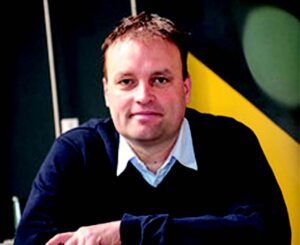
Mr Zegers’ recommendation to start planning shutdowns well in advance is, of course, based on his career-long experiences. During this time, he has seen planning become more and more of an afterthought. “Recently for example we were called in to provide assistance during a scheduled outage. We were brought in just a few months prior to the job and were additionally told that all preparation would need to be completed in just four weeks! That was a very challenging timeframe to say the least!”
It would have been better all round, he continues, if he and his team had been approached fully twelve months prior to the shutdown. “We could then have assisted in properly preparing the shutdown. For example, by identifying those valves not requiring maintenance, highlighting valves which could be repaired in-situ and especially in spotting those which needed to be removed from the line and taken to a workshop for thorough repairs. Also, we could have helped to plan workshop capacity. Your local shop may do a perfect job overhauling say twenty control valves a week, but you cannot expect them to suddenly process five or ten times that number in the same timeframe.”
Conducting a value audit well in advance would also enable any necessary spares to be ordered in good time, allow workshops to reserve capacity for the tasks ahead, and also for transport and logistics to be scheduled. “Some valves, especially when fitted with actuators, can be incredibly large and heavy, so you do have to stop and consider how they will be transported,” states Mr Zegers. “In some case, the workshop could even need to bring in a heavy-duty crane. If you are working against a tight deadline it is easy to overlook such basic but essential details, which can otherwise cause serious delays.”
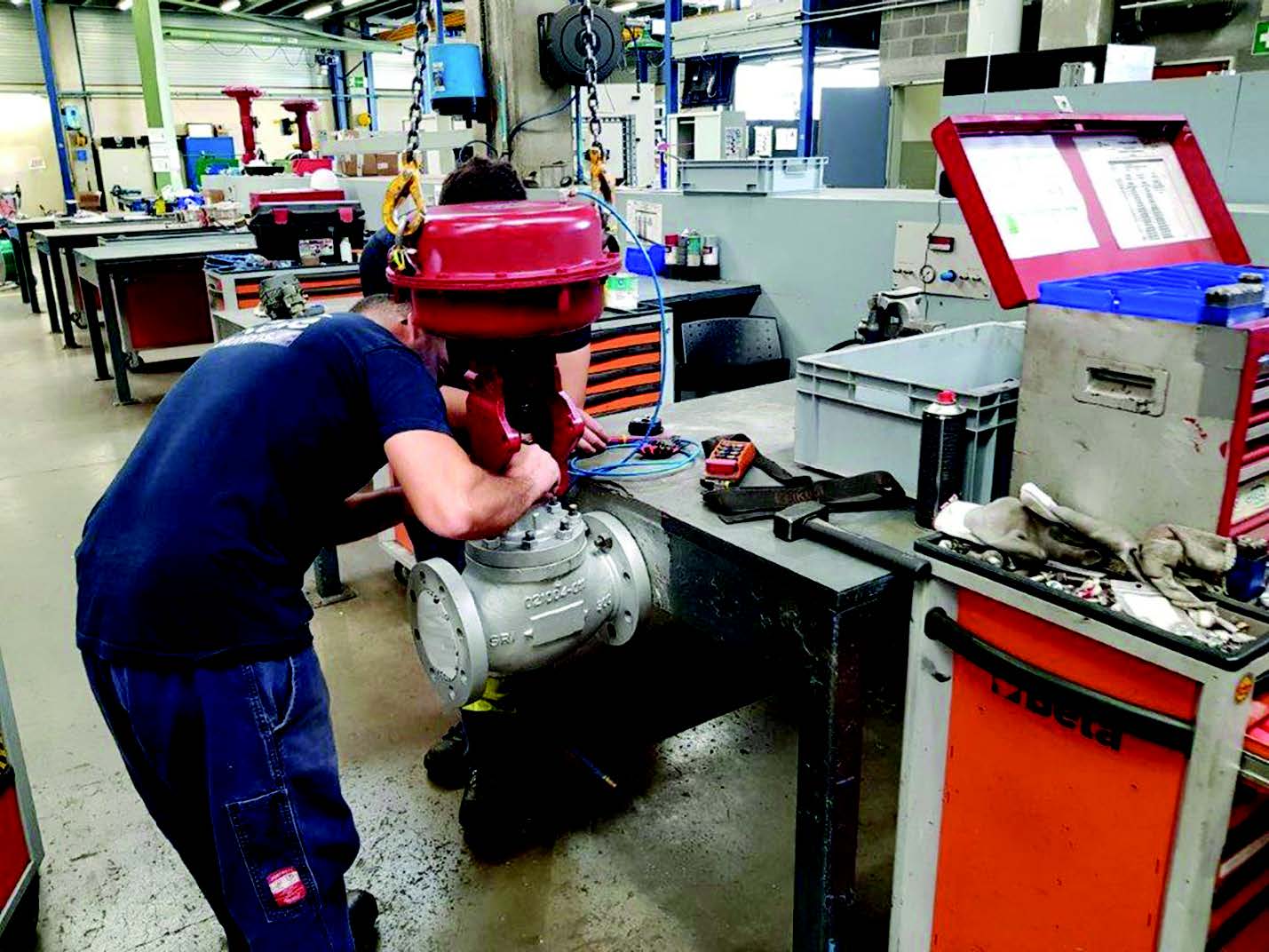
Facing the unexpected
In many sectors, it seems to have become the norm for companies to extend the time between scheduled outages. Whilst understandable in terms of boosting plant uptimes, this trend can add extra complications to the shutdown, notes Mr Zegers. “This development has been exacerbated by the Covid pandemic, when plants were understandably reluctant to have people on site unless absolutely necessary. Whatever the cause, the result can be increasing wear and tear on valve components, meaning that simple repair jobs can become more complex and time-consuming.”
From time to time, Mr Zegers also faces unexpected issues, such as corrosion in valves which had previously gone from shutdown to shutdown without needing maintenance. “In such cases it could well be that the process medium flowing through that particular pipework has changed since the time the plant was set up. Or perhaps the valve was not properly selected. That could be the type of valve, the (internal) materials or the Cv value in the case of a control valve. During the specification process it is most important to consider all the materials that the plant designer indicates might potentially be flowing through the valve. Simply looking at the pressure and temperature ranges is certainly not enough.”
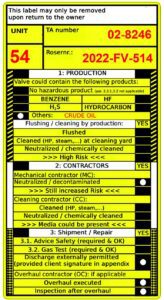
While discussing media, Mr Zegers notes that another issue which is occurring more and more regularly is failures in trunnion-mounted ball valves. “The problem here seems to be caused by the medium in the installation such as certain types of crude oil. If oil conglomerates behind the seats it can cause the valve to stick and/or lead to in-line leakages.” Fortunately there are solutions, continues Mr Zegers. “Options could be to fit a steam jacket or to consider using a different type of valve. For example, a rising-stem ball valve.” Asked about the origins to this type of problem, Mr Zegers indicates that refineries may have switched to a different supply source. “Crude oil is not a consistent commodity. Each well can produce oil with unique characteristics such as impurities and in fact even oil from the same well can change from sweet to sour over the course of time. I have seen hydrogen (sulphide) cause major issues with valve materials such as chrome or nickel plated balls, for example.”
Reducing bottlenecks
Whatever the challenges, Mr Zegers remains passionate about his job and is determined to keep finding new ways to help maintain valve populations in perfect working order.
“As stated, it can take quite a time for manufacturers to produce parts for certain valves. So one solution going forward could be to make more use of additive manufacturing. Even better would be if the repair shop itself could be authorised to 3D print the necessary parts, thereby eliminating transport delays. This is an option which I would really like to discuss with the valvemakers.”

Another benefit might accrue if manufacturers could agree on standards for components such as valve stems, suggests Mr Zegers.
“Right now, valve stems, cages, plugs, membranes, actuators and positioners can be found in a wide variety of brands, type and sizes. So suppose valvemakers were to agree to restrict sizes of some parts to a limited number? Yes, that would mean slightly more cost if instead of a 16 mm stem the manufacturer uses a 20 mm stem. But having fewer sizes would streamline manufacturing and also make it more attractive for manufacturers as well as stockists to keep inventories. And having ready access to parts would be a major benefit during a shutdown.”
Independent monitors
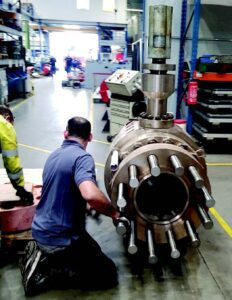
Mr Zegers is well-known throughout the valve industry, having set up a Dutch company that specializes in valve testing and inspection. However, he indicates that he is being increasingly approached by end users to act as an independent auditor and controller during shutdown activities. “Despite the fact that we do not advertise this type of work, we are receiving more and more requests from chemical and petrochemical companies to be the eyes and ears of the asset owner in the overhaul shops.”
Plants may of course decide to call in an expert like Mr Zegers, knowing that their own staff will be hard-pressed as it is during a shutdown. And that is quite understandable, given the wide scope of activities Mr Zegers is often tasked with. These vary from supervising safety, planning, sequence, progress, cost control, overview, parts supply, repair(s), QA/QC, testing, additional work, shipment, etc. In addition, this can necessitate monitoring the work of multiple revision shops. And the number and variety if valves involved can also be daunting to the inexperienced, taking in on/off valves, control valves and safety valves. “In short, we ensure that a valve is overhauled correctly, in the shortest possible time and within budget so that the valve can be quickly reassembled so that it can be used until the next turnaround,” concludes Mr Zegers.
Valve overhaul essentials
To help newcomers better understand the intricacies of a valve overhaul, Mr Zegers kindly noted some of the key steps involved.
- Identification: all valves to be overhauled are provided with a metal label, with a list of steps to be taken such as cleaning, chemical cleaning, repairs, inspection, etc. Black squares are cut/punched out once each step has been taken, providing an immediate and clear indication of the valve’s progress.
- Dismantling: valves should be removed according to a certain order, depending on the application. Valves in utilities such
as steam are often removed last and normally expected to be returned first. - Pre-test safety valves: a pre-test indicates if the current set pressure of the safety valve is still within tolerance compared to the previously applied set pressure.
- Cleaning on-site: all valves must be carefully cleaned to remove residual products, which could otherwise be released during valve disassembly in the revision shop.
- Transport: valves should be transported in the correct position. Eg, safety valves should be transported vertically.
- Registration: upon arrival at the revision shop, the valves are registered and provided with the valve data sheet with all relevant data. Information and additional actions on documents are also attached to the valve. Eg, helium leak test, different positioner, extra tests, legal inspection, etc.
- Inspection: each valve is dismantled and subjected to an initial inspection.
- Cleaning: certain parts of the valve are cleaned and then sampled if necessary.
- Painting: parts that need to be preserved are provided with the correct coating after blasting. Consider heat-resistant paint for high temperature applications, appropriate colours for control valves (normally open or closed) and safety valves (indicating whether or not fitted with a bellow).
- Reassembly: when rebuilding the valve, use all new soft spares and any other spares needed to return it to a good working condition. Use OEM parts wherever possible. And use the right parts as regards for type of material, temperature range, pressure range, tightness class (for stem sealing and gaskets) when OEM parts are not available.
- Testing & final check: necessary to ensure the valve’s proper functioning and fitness for service. Safety valves are tested for set pressure and seat leakage according to international standards and national requirements. Most control valves are tested for ANSI FCI 70-2 with on/off valves tested according to international standards like: ISO 5208 or API 598.
- Fugitive emissions: for safety and environmental reasons, more and more are valves to be tested for fugitive emission after overhaul. Fugitive emission tests evaluate the integrity of the external leakage of valve stem seals (or shafts) and body joints of isolating valves and control valves, intended for the application in volatile air pollutants and hazardous fluids. Standard ISO 15848-2 or end user procedures can be used to perform such testing.
About this Featured Story
This Featured Story is an article from our Valve World Magazine, April 2023 issue. To read other featured stories and many more articles, subscribe to our print magazine. Available in both print and digital formats. DIGITAL MAGAZINE SUBSCRIPTIONS ARE NOW FREE.
“Every week we share a new Featured Story with our Valve World community. Join us and let’s share your Featured Story on Valve World online and in print.”