In their battle against fugitive emissions in industrial valves, Senseven provides an analysis of the challenges and possible solutions to the problem.
By Michael Hettegger, CEO and co-founder of Senseven
Industrial valves exist in nearly every production process. Their main function is to control flow, prevent backflow, control and relief pressure and to stop the process flow in closed condition. Intact valves safeguard media quality and safety for employees. However, studies show that 5-10% of industrial valves are leaking internally. This can be problematic, leading to economic losses, safety problems, contamination and in the worst case: environmental pollution. Valves require proper inspection and preventive maintenance to guarantee their functionality.
A well-established way to check for inner valve leakage is using acoustic emission technology. One advantage of this technology is that leak detection is performed without disassembling the valves. It is a so-called non-destructive testing method which uses ultrasonic signals that are emitted by a material under stress due to irreversible phenomena such as damage, corrosion, cracks, leaks or malfunction.
Applied to leaking valves, this means that internal valve leakage leads to high-frequency stress waves. They are created by turbulences due to the flow that occurs when a medium is pushed through the leak hole of the valve, as shown in Figure 1.
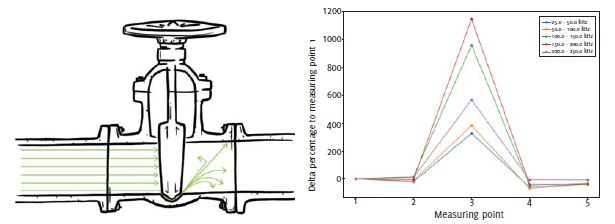
Through regular inspection, signal changes are detected early enough, and internal leakages are found before they can cause a major damage to the equipment or harm employees.
Collecting the raw signal
When a valve is leaking, it releases energy which travels in the form of elastic high-frequency waves. These waves are captured by an acoustic emission sensor that converts the energy into electrical signals which are then sent to a data acquisition system for processing.
In order to collect these acoustic emission signals on valves, the sensor is put on different measurement points before, on and after the valve body. The data acquisition system captures the electrical signals and records them as digital data. The broadband recorded signal is divided into sub-frequency bands in the background to better detect differences between the single measurement points. See Figure 2. Leaking valves create strong acoustic emission signals on or after the valve body.
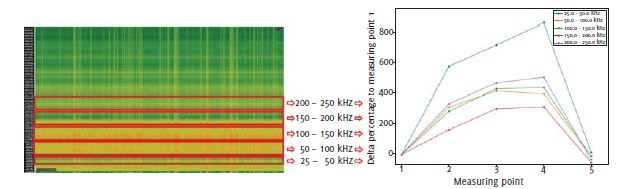
What are current challenges of collecting useful raw signals?
Despite the successful establishment of the acoustic emission technology, current solutions have shown some limitations. Among others, these limitations are the following:
- They are complex to use.
- Trained and experienced personnel is needed.
- Time to transfer and analyse the sensor signals is needed.
- Most often, solely proprietary and closed devices are used.
In addition, experts in the field encounter many factors that can influence the measurement result, as shown in Figure 3.
A more detailed overview of the challenges
1. Usage of the right sensor
Using the right sensor is essential to properly filter AE signals. Priorities for AE sensors are high sensitivity, consistent frequency response, high performance in working environments and ‘immunity’ to unwanted noise. The frequency bands of sensors play a crucial role in detecting leaks in valves of different size, type and material with different media flowing through them. The sensor must be properly placed on the valve surface to identify the motion of the AE waves and to provide a strong signal.
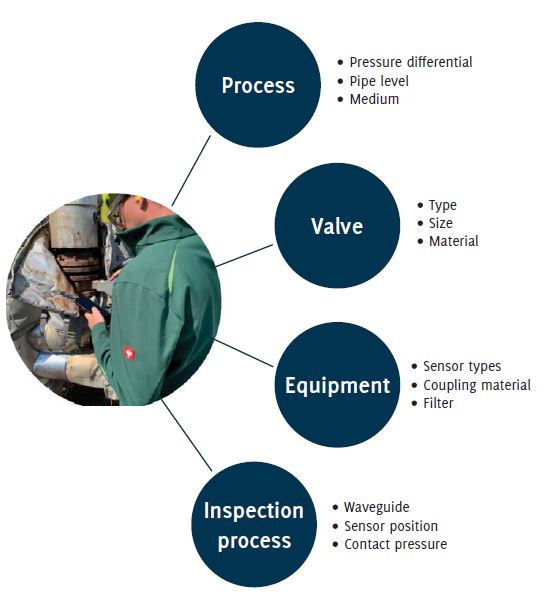
2. Ambient noise interference
Acoustic emission testing relies on the acoustic emission waves generated from the valve being tested. However, there can be significant amount of ambient noise in the testing environment, such as nearby machinery, pumps or other equipment, making it difficult to filter out the right signals.
3. Dependence on expert know-how
Inspections nowadays require specialised know-how and expertise. The operator must be able to accurately interpret the acoustic signals detected. This requires training and experience, and inexperienced operators may miss or misinterpret signals, leading to inaccurate results. In addition, the dependence on expert know-how makes it very difficult for companies to generate reproducible measurement results.
4. Valve geometry
The shape and size of a valve can significantly affect the detection of acoustic emissions. For example, valves with complex geometries or valves of a bigger size may require multiple measurements to accurately detect leaks. This can increase the complexity of the testing process and require more time and resources.
So how can these challenges be tackled, and valve inspection be made a standard?
In order to tackle that problem, Senseven has taken over 2000 measurements in laboratories together with more than ten different valve manufacturers during the last year. To replicate real production situations, leakages were also simulated in the field, considering different media/pressures/different valve sizes/nominal diameters and valve types.
The experience gained and the data collected were used to build a smart and mobile inspection system considering feedback from experts. The challenge was to build a system that could be used immediately after a short introduction, that could generate reproducible results, analyse data automatically and store it in such a way that companies could use it for predictive maintenance purposes. Figure 4 provides imagery of this setup.
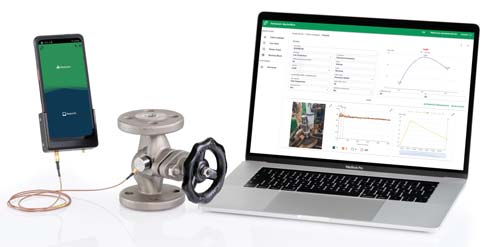
The Senseven process
- Introduction of standardised meta data acquisition
Through the usage of RFID tags or pre-defined input masks, the inspection process is put into a standardised format for meta-data collection. This simplifies the handling for the user, as data must only be entered once and is later automatically recognised by the system or can be called up by scanning the RFID tag. At the same time, it ensures that different inspections for the same valve can be assigned in a structured way. - Software assisted inspection process
Different components require different inspection procedures. A software-guided inspection process gives clear instructions, designs a simple inspection process, and provides the possibility to generate reproducible results. - Condition evaluation through algorithm and artificial intelligence
The greatest challenge for inspectors is the interpretation of measurement data. Specialised training and extensive experience are required to analyse numerous features of the measurement signal and evaluate the condition. The Senseven solution developed algorithms that automatically detect whether a valve is leaking or not and an AI should be able to calculate the extent of the damage in the future. - Automated and standardised reporting
All inspection data are automatically synchronised in a cloud-based Backoffice where maintenance personnel can conduct further analysis or auto-generate standardised reports.
Conclusion
Acoustic emission testing is a non-destructive (non-invasive) testing method and is state of the art today when it comes to early detection of damage in industrial components such as valves, pressure vessels, transformers or pumps. Experts use mobile testing systems to identify damage at an early stage. Nowadays, they are complex and time-consuming to use. The biggest problem and also the reason for the time-intensity is the interpretation of the measurement data.
Technical expertise, relevant training and several years of experience are required to evaluate this data correctly and derive the condition of the component from it. With the help of digitalisation, industrial inspection processes can be standardised. Features like machine learning can support maintenance staff with the interpretation of collected data, making inspections faster, easier and the results more reliable.
Further cooperation partners welcome
Mobile inspection systems are a crucial piece for predictive maintenance, among other things, for valve inspection. The generated inspection data can be combined with permanent monitoring solutions; they help to understand connections and support in ruling out problems. But most importantly, they help to predict defects and avoid downtime of machinery.
To further develop the Senseven solution, improve the algorithm and, above all, qualify the artificial intelligence for calculating the leakage rate, we are constantly looking for further cooperation partners. We would be pleased if other valve manufacturers are interested in getting to know the product live, understanding how they can use it in quality control and using test benches to help generate ground truth data for the AI.