Consumerism is growing rapidly around the world, placing increasing demands on natural resources, energy production, supply chains and our environment. This trend is guaranteed to continue in the coming years and so the pressures on our environment will continue to grow.
By Dave Anderson, Score Group
This resonates particularly in manufacturing and process industries, where ESG (Environmental, Social and Governance) issues are beginning to dominate investment and sustainability discussions, creating new compliance and reporting requirements for operating companies to meet. The United Nations have, for example, developed a 17-point Sustainable Development Goals model to help focus attention on where specific improvements in corporate social responsibility can be implemented.
Climate change resulting from greenhouse gas emissions is no longer disputed and if we continue to emit more of these by volume, scientists predict that we will see an increase in the occurrences and severity of extreme weather events, leading to a range of wider negative impacts, which we are already experiencing around the world.
Net zero emissions
The short to medium term solution is to move to “net zero emissions” as soon as possible, but what does that actually mean? A simple definition of ‘net zero’ I like, from The London School of Economics and Political Science, is: “‘Net zero’ refers to achieving an overall balance between emissions produced and emissions taken out of the atmosphere. Like a bath with the taps on, an approach to achieving this balance can either be to turn down the taps (the emissions) or to drain an equal amount down the plug (removals of emissions from the atmosphere, include storage of emissions in ‘carbon sinks’).”
It should be clear to all that ‘net zero’ is not the same as ‘absolute zero,’ which in today’s world would be an unrealistic goal to set, given our reliance on all forms of fossil derivatives and existing production processes.
Know your scopes
Understanding where and how emissions are being generated is critical to planning how we shall then take steps to mitigate them. According to the Greenhouse Gas Protocols (2001), there are three defined scopes for emissions.
Scope 1: these are the Green House Gas (GHG) emissions that a company makes directly from operating – for example during ‘production,’ while running its plant and vehicles.
Scope 2: these are the emissions it generates indirectly – for example, emissions produced in the generation of electricity or the energy the company buys for production, heating and cooling buildings, etc.
Scope 3: these are all the emissions the organisation is indirectly responsible for, up and down its value chain. For example, from buying products and services from its suppliers, and also from its own products when customers use them.
These three scopes form the basis for mandatory GHG Emissions reporting, however, the most important point to make here is that the complexity and effort required to measure and then reduce emissions in these areas increases with each step. It is also key to state that some of these GHG emissions are within process operators’ own direct control, whilst other are less so.
The Greenhouse Gas Protocol from the Carbon Trust has further broken-down Scope 3 emissions into 15 separate categories! According to Carbon Disclosure Project (CDP) and Concordia University research, Scope 3 emissions account for 89% of all emissions in the oil & gas sector, whilst in the chemicals sector, they account for 76%. However, many of these areas are difficult to measure, given they are outside organisations’ own direct control.
Focusing on those GHG emissions that are directly within your own operational control is the easiest place to start any emissions reduction initiative. Typically, this results in actions being taken to reduce GHG emissions in Scopes 1 and 2 first, over the short to medium term. Increasingly, future efforts will be focused on Scope 3. Emissions reduction actions should be formally detailed in short-, medium- and long-term plans… and then implemented. A clear shift from reactive response to proactive emissions management is highly recommended.
Emissions reduction strategies
There are 4 basic strategies which organisations can adopt to reduce their total carbon footprint. These are:
Reduce: this is all about being efficient in operations – for example, reducing energy demand and process emissions through proactive maintenance and repair of equipment.
Replace: replacing fossil fuels use with renewable energy and green fuels – for example using electric vehicles in place of conventional.
Remove: enhancing natural capital to sequester carbon and deliver biodiversity net gain – for example carbon capture and storage.
Offset: generating and exporting renewable energy to reduce national reliance on fossil fuels. Looking at these from a return-on-investment perspective, we can see that the law of diminishing returns applies. The biggest and fastest gains will be delivered in the short to medium term by focusing on reduction of resources consumption and replacement of traditional energy sources with renewables.
There are of course many companies currently working on combinations of renewal energy projects and energy transition technologies that will naturally reduce emissions over time, to deliver a positive impact.
Example – combination: remove/offset
One reduction strategy which has been promoted by some organisations is the planting of trees. Trees remove carbon dioxide from the atmosphere and so some organisations have looked to ‘balance’ their carbon emissions outputs with trees’ carbon consumption capabilities, to move towards a ‘net zero’ position.
Whilst this is something that will have an impact in the longer term (once the trees grow), it is important to look at the practicalities, resulting impacts, and any unintended consequences, in terms of resources required to deliver the anticipated benefits.
A recent Oxfam report warned that an over-reliance on planting trees to offset carbon emissions is unrealistic and dangerous – it could push up food prices, threaten indigenous communities’ rights, and distract from the vital hard work needed now to cut emissions and stop the planet overheating. (Over-reliance on tree-planting to offset carbon emissions could push food prices up 80% by 2050).
By way of illustration, using land alone to remove the world’s carbon emissions to achieve net zero emissions by 2050 would require at least 1.6 billion hectares of new forests: an area of land five times the size of India (just under 2x the land area of the USA).
Compliance standards
In addition to having strong internal ESG and business metrics drivers, there are a growing number of global and local compliance requirements that industries are having to address. It is reasonable to say that compliance requirements vary from region to region, however, in my experience, all regions globally are seeing at least some move towards increased measurement scrutiny and emissions management requirements.
One globally recognised benchmark – the Oil & Gas Methane Partnership 2.0 (OGMP 2.0) – is the United Nations Environment Programme’s flagship oil and gas reporting and mitigation programme. It is the only comprehensive, measurement-based reporting framework for the oil and gas industry that improves the accuracy and transparency of methane emissions reporting, and it is key to prioritising methane mitigation actions in the sector. The OGMP mantra is: If you can’t measure it, you can’t fix it.
Measurement data reveals actionable insights and Score Group’s emissions surveys have consistently shown that around 10%-15% of process components create the majority of fugitive emissions in process operations. This statistic was also reflected in a recent report by Carbon Limits AS, who stated that their findings were: “85% of components emit less than 0.07 kg/hr, while a minority of components represent the majority of the (total) emissions.”
Finding and quantifying your leaks
Commonly applied practice for emissions management is to set up a LDAR (Leak Detection and Repair) program, where specialised equipment is first used to inspect the likely emissions sources, to identify and document any/all detectable emissions. It is important to note that emissions can be directly to atmosphere (so-called fugitive emissions) from failed components or joints, but they may also be from planned and unplanned releases of fluids to atmosphere via flares, vents or drains.
I would assert that in terms of focusing on making the most impactful reduction of emissions, process operators should take a prioritised approach to emissions management. By this, I mean that a top-down prioritised approach seeks to mitigate the biggest emissions first, continuing as far down the chain of emissions eliminations as is reasonably practicable. This approach requires leak rates and/or volumes to be measured and quantified. In this respect, I passionately believe that we should be modifying the LDAR acronym to include this crucially important indicator, to include a Q for Quantification (LDQAR). Hopefully, over time, we can shift the market to recognise and include this critical element.
Detection, quantification and trending tools
A wide range of equipment and systems are readily available in the marketplace today, but which ones should you be using and what are their strengths/limitations/Eliminating emissions from the five most common sources within your process plant is not just to the benefit of our environment, or for meeting externally imposed targets, there are major operational benefits to be acquired directly by operating companies too.
Fixed and portable emissions detection and quantification sensor technologies should be selected according to their capabilities, sensitivity and reliability. Understanding the wide range of tooling and technologies available and the best-use cases (and in some cases, limitations) of each is a critical part of achieving the best possible emissions monitoring and survey results.
Some currently available / deployed emissions monitoring approaches and sensor technologies include:
- V isual ‘condition’ surveys
- Acoustic emissions (AE) sensors
- Ultrasonic detectors
- Acoustic imaging
- Optical gas imaging
- Thermal imaging
- Gas sensors
- Gas sampling/analysers
Some considerations when selecting sensor technologies include portability, sensitivity, speed and ease of use, location and proximity, required survey conditions, survey procedures, deployment at scale, frequency of inspection, resolution and granularity of data, certainty of results, reporting of results, analysis of results, etc. A macro to micro (or vice-versa) approach can be taken to collect data and report on detected emissions over a very wide area (satellite-scale) basis, all the way down to a highly localised area (with hand-held or permanently installed monitoring equipment). Consideration should be given to compliance with OGMP reporting requirements – especially level 5.
It is always advisable to consult with subject matter experts when deciding which monitoring technologies and equipment to use in which situations, to understand what results / benefits you can expect when each are deployed. According to the International Energy Agency (IEA), adoption of existing technologies and procedures for leak monitoring and management is behind where it should currently be. In their “Curtailing Methane Emissions from Fossil Fuel Operations” publication, they state that if all countries that have already committed to reducing methane emissions were to adopt existing policies, “methane emissions from global fossil fuel operations could be cut by nearly 15%.”
Monitoring data management and analytics
In emissions management, we must take the same ‘criticality’ approach as we do with risk management. Which detectable emissions are most likely to occur and what are the potential impacts of those emissions likely to be, if these emissions do occur? Knowing the criticality of each potential emission allows us to set a survey frequency aligned to risk (in some cases, this is externally mandated by authorities’ prescriptive compliance requirements).
When emissions monitoring data is collected, it is imperative that monitoring results are consistently processed and analysed, to drive mitigation actions (i.e. repair and maintenance) decision making. In any case, it is most desirable to have emissions detected and quantified at the earliest possible opportunity. This allows repair and maintenance decision making and action planning to start as early as possible.
The earlier an emission is detected, and the root cause addressed to eliminate (repair) that emission, the less process fluid (by volume) will be emitted. ‘Time is of the essence’ in major emissions elimination. Elements of automation and standardisation of data collection, storage and reporting (including emissions quantification and trending), using software solutions is highly desirable. This can accelerate the rate of response to emissions mitigation and ensure minimal total emissions.
Maximising emissions reduction: repair and maintenance
I have highlighted in all my previous conference papers on the subject of emissions management that it is not enough just to find and report emissions – the whole point of emissions monitoring is that we must find, quantify and then eliminate them. Total emissions are only ever reduced when the correct equipment is initially specified and then the correct maintenance and repair actions are consistently taken over that equipment’s life cycle.
It is therefore critical that your emissions monitoring programme is backed up with reliable in-house or sub-contracted engineering, maintenance and repair teams that understand the implications of equipment selection and the approved and/or acceptable repair methods and procedures for emissions management.
Some typical emissions mitigation (repair and maintenance) activities include:
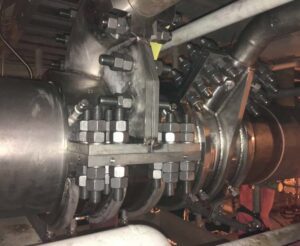
Temporary repair methods (inline)
Valve Integrity clamps (stem, gland & plug), pipe & flange integrity clamps, isolation barrier sealant injection, leak sealing solutions, gland packing adjustment, controlled bolting, composite techno-wraps, etc.
Planned repair methods (offline or during turnaround)
Joint integrity management, valve & actuator overhaul & repair, psv inline testing & recertification, lagging inspection & repair, instrumentation/control systems inspection, repair, assembly & supply, hose manufacture & supply, on site machining & fabrication.
New valve & actuator supply (i.e. replacement and/or upgraded equipment). It should be noted that repair of existing equipment most often offers the lowest total carbon footprint solution. Score’s carbon calculator indicates around a 70% to 95% lower carbon footprint is achieved when valves are repaired, as opposed to replaced with new.
In any operating process, it is highly desirable to improve reliability and therefore performance over time and we should not lose sight of the opportunity presented to us when emissions are detected. In completing repair and maintenance works, we have a unique insight into the failure mechanism and therefore can likely establish the root cause of the component failure. Capturing this extra layer of knowledge/data can add tremendous value in improving reliability over time as it can be used to inform recovery actions and decision making.
A simple example of this could be the change of materials used in the repair of a valve stem packing. Moving from standard packing material to ‘low E’ packing material may have a double positive effect on enhanced sealing performance and extended sealing life expectancy.
As mentioned earlier in this paper, it is always advisable to consult with subject matter experts when deciding which repair and maintenance solutions can be safely and effectively deployed, in which situations, prior to planning and commencing any active emissions mitigation works.
Business benefits
Earlier in this article, I mentioned some possible negative impacts resulting from the laws of unintended consequences. It is therefore appropriate to also mention the laws of potentially positive intended consequences before concluding. As the marketplace drivers are pushing reactive response to new compliance requirements, there must also be recognition that emissions management and sustainability should be part of the commercial considerations for any operator.
Effectively managing and eliminating emissions is a best practice that can deliver intended consequences of:
- Protecting the environment
- Minimising operational risks
- Increasing safety in operations
- Reducing product losses
- Improving process efficiencies
- Maximising operating profits
Conclusion: collaboration is key
We must all do our part and invest together in emissions elimination; no one can achieve the required results on their own! Let’s push forward together to deliver on our entire communities’ net zero ambitions.
Emissions Elimination Program™
Score Group’s Emissions Elimination Program™ provides regulatory compliance and reporting on emissions.
All work is managed through our software solution, enabling you to monitor the environmental performance of your asset and track failures through to repair. Published research confirms that around 75% of all emissions are valve related and, in our experience, around 15% of isolating valves are leaking to flares or vents. Score Group meets regulatory compliance and reporting requirements, whilst producing evidence of your efforts to meet or exceed your ESG goals.
Score differentiates itself from other service providers by offering a “one-stop” service model, through our unique Emissions Elimination Program™, which has 4 key steps: surveying with the best available technologies and tools, analysing the survey results, measurably eliminating your emissions, and lastly seeking to engineer out recurring failures.
For further information on Score’s Emissions Elimination Program™, email them at eep@score-group.com.
About the author
With 39 years of valve industry experience and 29 years of service in the Score Group, Dave Anderson is a highly experienced valve specialist and brand ambassador. He travels the world, enthusiastically promoting Score’s innovative products and services, to educate and help customers find and tackle their problem valves and measurably lower their emissions.