“Tackle more problems through innovative casting” is Utmost Alloy’s core value. In fact, their strategy – to increase quality and cost efficiency for mass production through sophisticated automation solutions – is completely different from that of any other conventional foundry. Valve world spoke with Mr Yangyang Jia, General Manager.
By Laura Wang, Valve World
Utmost Alloy takes advantage of outstanding material capabilities and tackles pain points in various applications. Their mission is to push forward the creation and implementation of innovative solutions on the basis of its strong comprehensive strength, and to embrace the future challenges together with the application markets.
Utmost Alloy is a relatively new brand. However, the word “new” doesn’t mean that the brand only has been around for a short time. Instead, it stands for a development path which is completely different from that of other conventional foundries. Being lead by a team with over two decades of professional experience, Utmost Alloy is quite familiar with the conventional development model.
More importantly, it also knows about the long lasting pain points of this industry – high costs and large inventories, low efficiency and performance, and sluggish delivery and liquidity. Therefore, innovation was destined to be the major driving power of development when Utmost Alloy determined to benefit from its value by ‘unlocking’ more applications and improving customer experience with the ultimate aim of boosting the advancement of the casting industry.
Using automation to boost valve companies
The valve industry is one of Utmost Alloy’s specialisations. Casting is an indispensable part of valve products and their manufacturing process. Foundries and valve makers are especially interested in how to improve valve performance though high-quality castings.
In this regard, Utmost Alloy has made an ambitious strategic decision: to implement automation. The company has determinedly invested in automated systems and facilities on the foundation of capital advantage and powerful technical strength. The outcome is increased productivity and capacity. Production and cost efficiency are optimised by product standardisation, continuous production and inventory delivery. This specifically satisfies customers with more complex requirements regarding productivity, efficiency, and cost.
Moreover, Utmost Alloy always strives for great quality, even after achieving a high degree of efficiency and maintaining low costs, made possible by automated production. On the contrary, the company has become stricter with quality control. Automated production is more predictable than production by a massive work force. Because of this, Utmost Alloy offers high-quality products that are reliable and versatile that still contain a consistent uniformity. Utmost Alloy has built a fully automated casting plant.
It has been equipped with ERP and MES systems, is capable of real-time data collection and can be accessed though a central control system. This leads to a transparent data system and helps avoid supply chain risks. In fact, the establishment of a data system indicates that the company is developing towards an intelligent foundry.
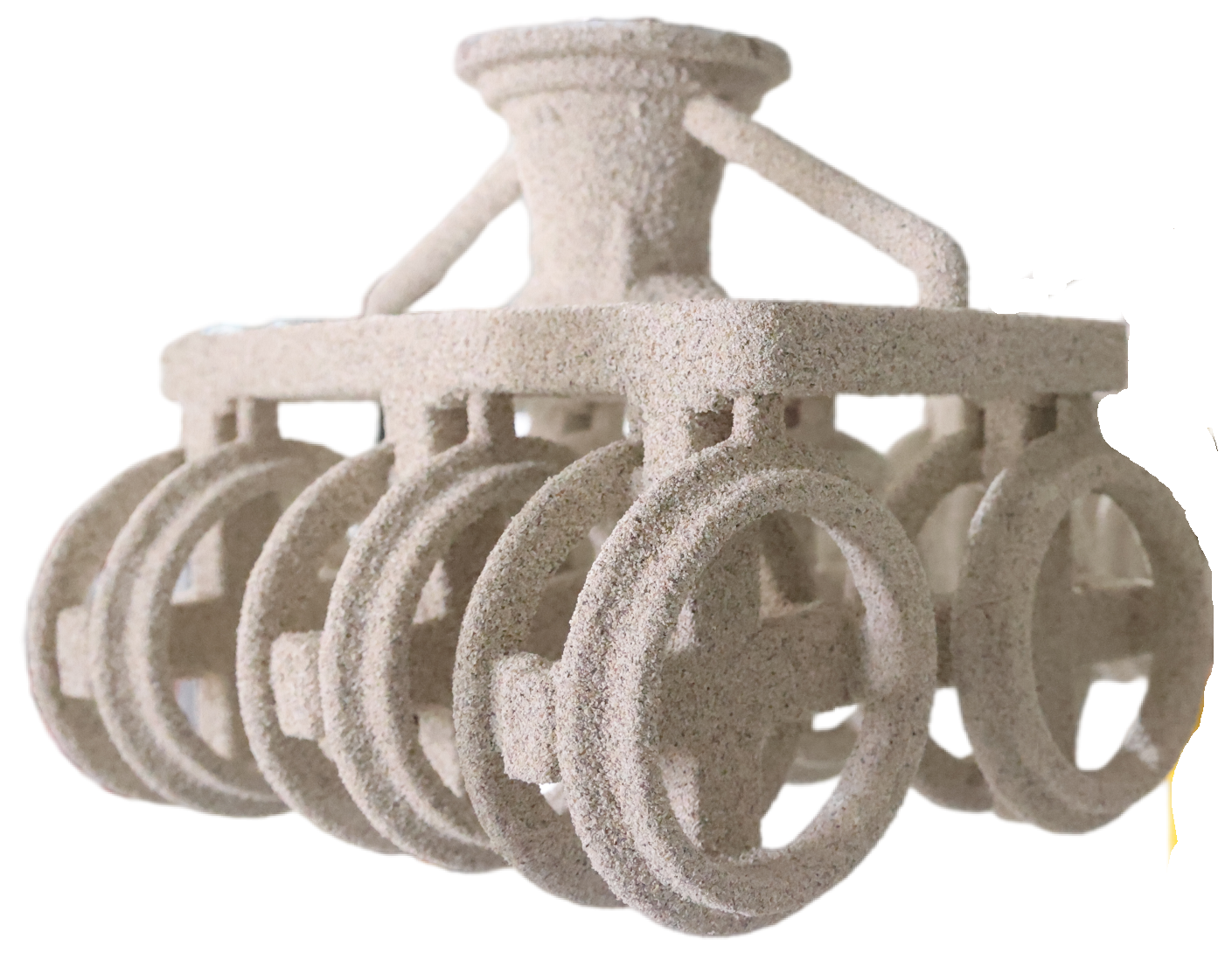
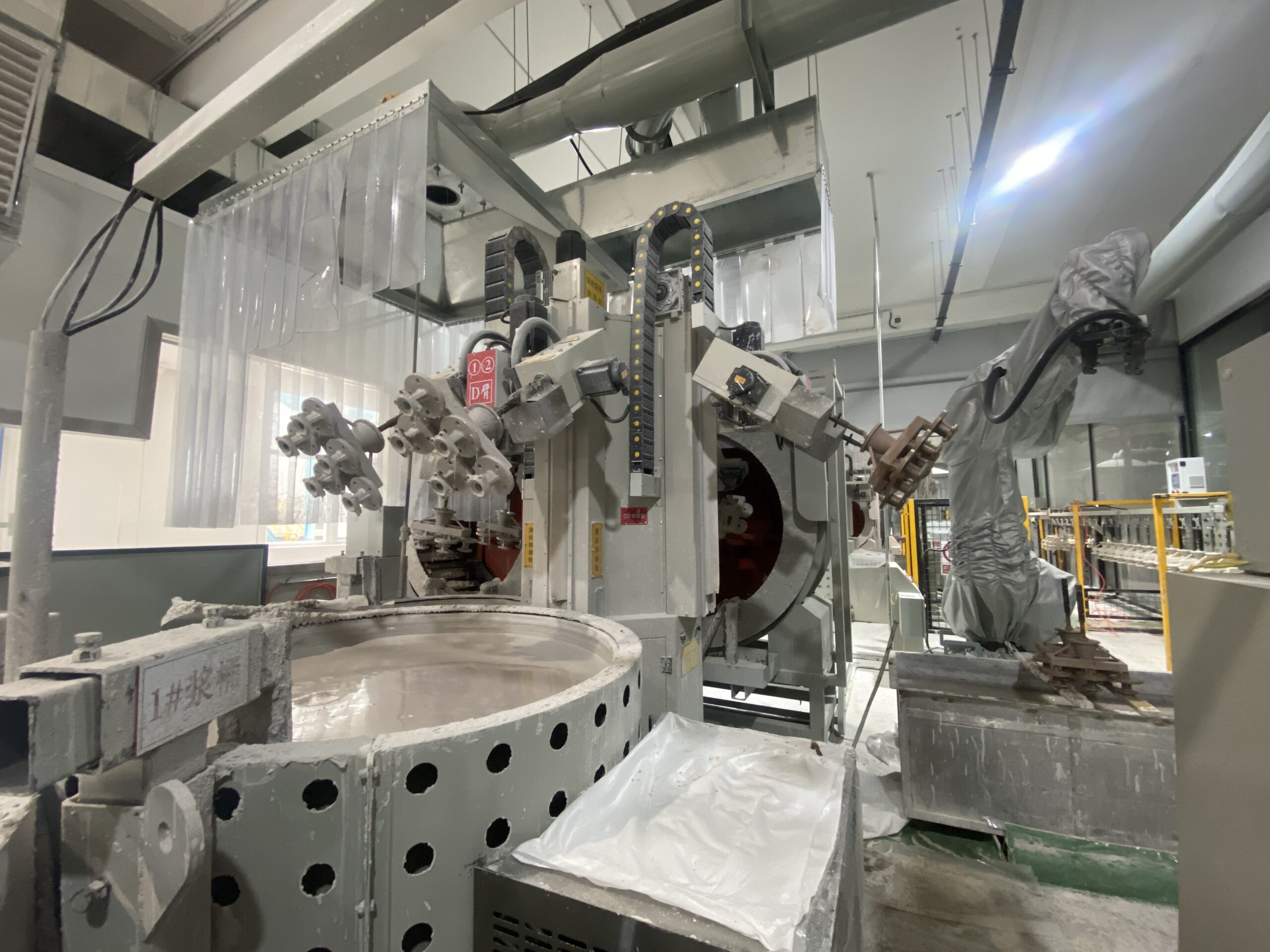
Mr Jia explains: “The major advantage of a smooth flow of data is real-time monitoring of our equipment and facilities, and this eventually reduces losses caused by any unplanned downtime. Besides, it allows digitised management of power consumption of our plant. This also helps reduce costs, and it can guide the development of data systems. From a quality perspective, a data pool about product quality might specifically indicate where the problem lies. This helps us to achieve our goal of digitising precision management of our foundry.
However, I think the most valuable advantage of intelligent production is its capability of evading risks in the supply chain, namely risk control. The most valuable advantage of digitisation is data liquidity. We’re forging a transparent data system. It’s both transparent to our customers and the up-stream supply chain. The real-time knowledge on product status helps each party involved mitigate supply chain risks. And it has an even more profound meaning – helping customers to reduce sourcing costs and mitigate any difficulties. When developed further, it can help relieve the inventory pressure on customers and release cash liquidity. Once this digitised service becomes more capable and realistic, our market development model might change from passive sales to an increase in sales.
This leads to a more steady relationship with our customers. We have also further raised our automation level; especially the in-depth design of our logistic system. Each element of the system, including ground and underground space utilisation, automatic trans-shipment, and smart stereo warehouse, is deliberately designed so that each step of the logistic system engages very precisely and efficiently with neighbouring ones. It saves time, and reduces surplus stocks and safety risks. Utmost Alloy has also managed become better for the environment, which made it a Grade A company.”
Material capability unlocks multiple applications
The intrinsic strength of this new-type foundry is not limited to mass production and high efficiency. Utmost Alloy focuses more attention on developing its material capabilities. The Utmost core team has unchangeable faith in the theory that the strength and level of a foundry is dictated by its material capability. In the past half century, casting technology and skill did not undergo any remarkable changes, although firms in this industry keep trying to improve their equipment, materials, and inspection measures.
The major difference and point of competition between them are their knowledge about materials. The level of knowledge directly affects a foundry’s position in the industry, and it also affects the added value of its products. That’s why Utmost Alloy invested in advanced equipment like a vacuum furnace. This made it possible for Utmost Alloy to work with special high-temperature materials like nickel alloy. Furthermore, the company actively communicates with universities, well-known scholars and experts during the course of preparing the construction of a national-level metal engineering centre.
Mr. Jia tells us about many breakthroughs in material development. Utmost Alloy has become skilled in working with martensitic and duplex stainless steel. Based on this, the company was able to work on special material development with regards to future applications. Within the company, many new types of material were successfully developed ‘at one stroke.’
This is a testament to the company’s technical strength, and the foundation of its sound service efficiency and competitive costs. Mr. Jia continues: “Many customers from around the world came to us with the same expectation for Utmost Alloy – to develop new materials for them. These clients were not able to have these needs fulfilled by conventional foundries, but it is exactly what we are specialised in. Regarding new material developments, the R&D capabilities and our equipment are both indispensable. In that regard, our capability to consolidate resources becomes really important and in-house storage is also of great importance. But when Utmost Alloy is handling diversified needs, the ultimate goal is to identify the balance between efficient use of resources and guest satisfaction. Besides, the company must endeavour to build up strategic partnerships with customers.”
By means of empowering valve and pump products with quality castings, Utmost Alloy has achieved a broad coverage of applications including nuclear power, chemical and marine. Besides, the advanced automation systems enable the company to provide many effective solutions to automobile, aviation and consumer product industries. More and more applications are being ‘unlocked’ by the company, which is aiming to tackle more pain points of the industry through advanced casting.
Building a future plant and talent pool
The comprehensive strength of Utmost Alloy, which includes capital strength, professional experience, technical level, facility & equipment, plant management, team building and marketing, is powering this young company to develop at a high speed. When asked about any possible change of development objectives when the company is growing so fast, Mr. Jia said with confidence: “Our objectives have never been changed. Our core value is to ‘help customers solve their problems.’ The purpose of investing in automated production is to be able to offer the best cost, efficiency, and quality to our customers.
We built up the flexible production line and keep developing new materials in order to become more capable of producing custom products. Since there are more issues to be solved by the casting industry, we define innovation as the core competitive power of the company. We encounter the same problem during our development as any other foundry.
We differ in our approach to solving those problems. We overthrew the conventional pattern because we know its defects. Innovation is the solution that tackles the root cause of the problems. However, innovation should not be based on any rash decisions, nor should it be the aim of investments and transformation. Real innovation requires a professional team which knows customer needs, material properties and is familiar with various applications. I believe that castings truly are tech products, and good quality comes with great complexity. Intuitiveness is of no help when working with furnaces.
The quality totally depends on the team’s knowledge and experience, and that is the foundation for innovation.” Today, Utmost Alloy has built up in-house capabilities for equipment innovation. It has applied for 27 patents, ten of which in 2021. Each of these patents was geared toward equipment innovation; 6 of these patents have been approved. 17 of the 27 patents were applied for in 2022 and three of these were applied for as a patent of invention.
Usually, fierce competition between established players is mostly due to the homogeneous properties of their products. Because of this, it’s difficult to create more added value for customers.
That’s why many foundries following the conventional track ended up in blind competition. Like Mr Jia said, the historical business model is susceptible to excessive wastage, low pass-rates, excessive cost of back-end processes and a high toll on the environment. The casting industry is in desperate need of changing. Utmost Alloy takes innovation as the major power for its development. It’s not simply about product innovation. Instead, the innovation fully covers the business model, inspection measures, supply chain configuration, marketing strategy, and more. More importantly, the ultimate goal of innovation must be reasonably specified.
Mr Jia revealed: “Regardless of intelligent production or automated facilities, the core purpose is to optimise the quality, delivery time and cost. In other words, the key problem is how to optimise the cost, the material performance and reduce delivery times through technical innovation. Those who have the solutions represent remarkable value for business, for the foundry industry and for society. We decided to change because the industry and the circumstance are both changing. By consolidating multiple aspects, we hope to reform the business pattern of the foundry industry and to reduce waste. Our goal is to propel the development of foundry industry and serve the market better, and eventually make our humble contribution to the low carbon world initiative.”
At a first glance, Utmost Alloy from Jining, Shandong province in east China, looks like a modern industrial park, rather than a typical foundry. When walking inside the facility, it really feels like a ‘plant of the future’ – neat, clean, well-equipped, and is outfitted with HVAC, which renders a comfortable atmosphere. High-level automatic production relieves the staff from heavy and tedious work. This means they can concentrate on work with more additional value, such as research and production process development. “Our increasing knowledge represents the foundation of our company’s strength. Foundries are highly specialised working environments, so we need a talented work force. They add vigour to the company, and they power innovation and development. We focus on building an advanced foundry which features digitisation, and intelligent and flexible production. A comfortable working environment and bright future both help attract more talent. Such a healthy cycle boosts our overall strength and prompts the upgrading of the foundry industry,” said Mr Jia.
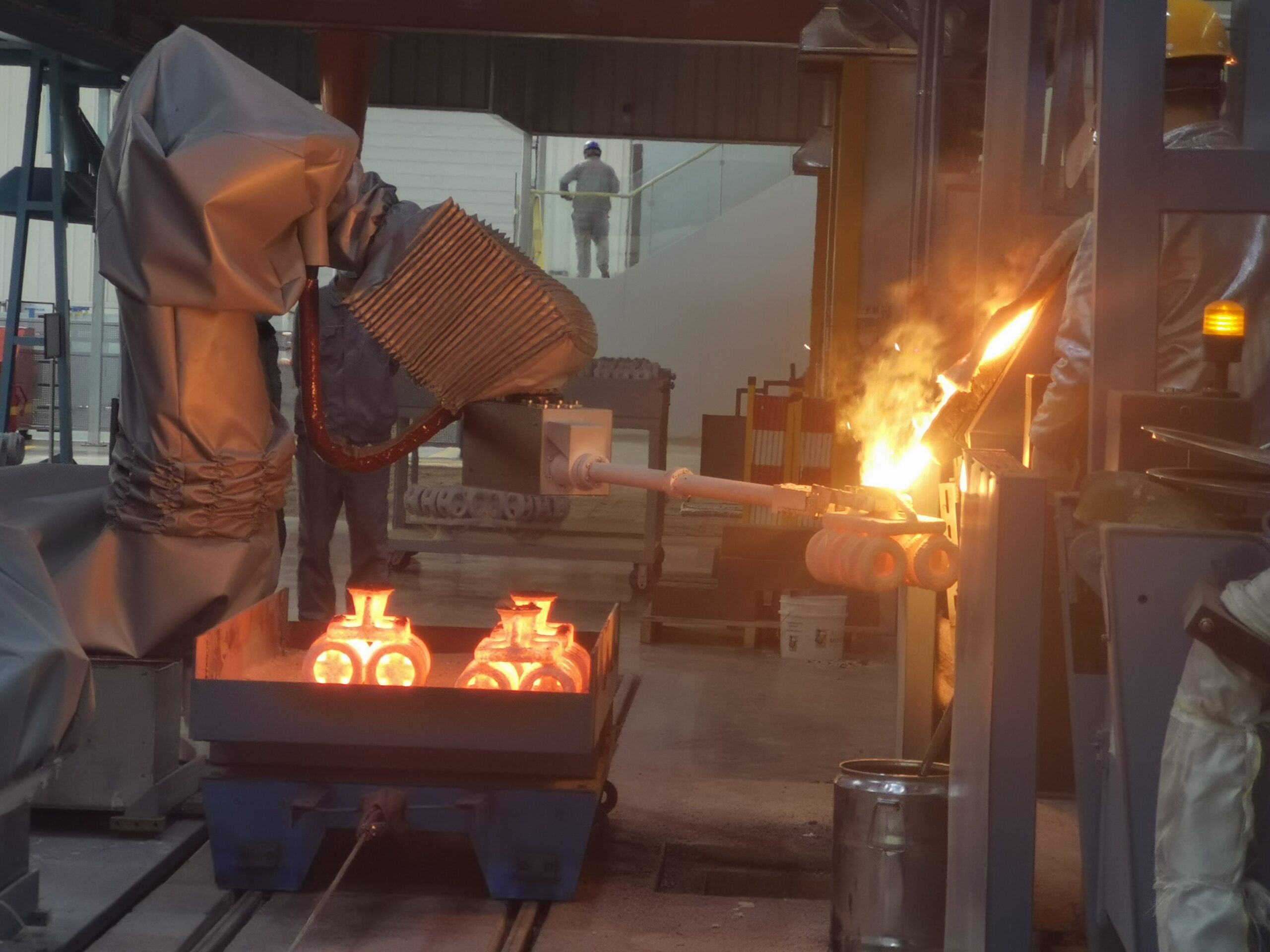
Utmost Alloy: facts and figures
Phase 1
Staff:
Capacity:
Area:
Phase 2
Staff:
Capacity:
Area:
Investment:
Service:
Service:
Application:
Application:
Material development:
Material development:
Address:
Telephone:
Website:
Utmost Alloy: facts and figures
Phase 1
300+
7,500 (3,600 ton sand 3,900 inv)
25,000+ sqm
Phase 2
500+
16,000+ (12,000 ton sand, 4,000 ton inv)
115,000+ sqm
About EUR 177M
Casting, machining, 3d printing, liquid die forging, finishing and assembling, computer simulation monitoring and analysis, etc.
Oil & gas, chemical, chips and semiconductor, marine vessel, food, health care, aerospace, energy, automobile, etc.
Stainless steel, martensitic and austenitic stainless steel, duplex, super-austenitic, nickel alloy, titanium alloy, etc.
No.1, Futang Rd, Beisu Town, Zoucheng, Jining, Shandong Province, PR China
+86 0537-5181 885
About this Featured Story
This Featured Story is an article from our Valve World Magazine, October 2023 issue. To read other featured stories and many more articles, subscribe to our print magazine. Available in both print and digital formats. DIGITAL MAGAZINE SUBSCRIPTIONS ARE NOW FREE.
“Every week we share a new Featured Story with our Valve World community. Join us and let’s share your Featured Story on Valve World online and in print.”