The sequence impulse process developed by thyssenkrupp AT.PRO tec GmbH has long been used on cupola furnaces to increase cost-effectiveness. In over ten years of development work with Schubert & Salzer as their partner, Dr Rainer Klock and the team at AT.PRO tec also succeeded in getting the SIP technology to work on blast furnaces with the help of sliding gate valves.
Text by Sandro Caravita, Marketing at Schubert & Salzer Control Systems
The history of the blast furnace process is a story of great innovations and technical improvements. Again and again, courageous innovators have been willing to question common methods to optimise pig iron production process further. In the 18th century, Abraham Darby succeeded in using coke instead of charcoal. As a result, blast furnaces became considerably larger and more efficient. In the 19th century, Edward Alfred Cowper managed an innovation leap with the newly emerging blast preheaters. Today the so-called “Cowpers” are part of every blast furnace plant.
For over a decade, Dr Rainer Klock and the thyssenkrupp AT.PRO tec GmbH team worked on perfecting “sequence impulse process (SIP) with induced shock waves” to achieve the next evolution in blast furnace technology.
The basic concept of the new process is to activate the areas deeper inside the furnace. In the standard process technology, a cone of coke is created – the so-called “dead man”. Incompletely reacted fine particles block this coke bed. The gas flow and heat cannot penetrate deeply enough into the furnace.
The solution: strong intermittent impulses to enable the necessary deep penetration of the technical oxygen. This leads to a short-term, local surplus of oxygen and a more complete chemical conversion of the fine particles – even deep inside the coke bed. The shock waves associated with the impulses break open blockages at this point and mix the contents with strong turbulence. They ensure a more homogeneous gas distribution and a better flow-off of the molten metal and the slag.
Phase 1: ASIPGO – collaborative research project (2007-2011)
The technology has worked successfully for years on a smaller scale in cupola furnaces and enables a considerable increase in cost-effectiveness. Use on the much larger blast furnaces was, however, completely unresearched.
When AT.PRO tec approached RWTH Aachen and the Institute of Ferrous Metallurgy (IEHK) with the subject, Rainer Klock had just completed his degree thesis. RWTH looked for research associates for the new project, which was supported by thyssenkrupp as the industrial partner. “That was the perfect opportunity for me. Not only could I write my doctorate thesis directly following my degree, the project also offered me the possibility to work on one of the largest blast furnaces in Europe”, said Dr Klock. “The ASIPGO project pursued two goals over three years: firstly to improve the use of SIP on cupola furnaces through automation and secondly to enable the use of SIP on blast furnaces.”
Within the framework of his doctorate thesis, Rainer Klock focused on research into the use on the blast furnace. First the physical and chemical processes that made the SIP successful on the cupola furnace were examined. The research group, consisting of employees from thyssenkrupp AT.PRO tec, thyssenkrupp Steel Europe and RWTH Aachen, wanted to understand the processes in the raceway zone of a blast furnace and how they would probably be affected by oxygen impulses in order to be able to transfer the technology from the cupola furnace to the blast furnace.
Pulse valves
On the basis of these findings at the IEHK, a SIP test system for blast furnaces was constructed. Compared to the SIP system for cupola furnaces, significantly larger nominal diameters and pressures were now used, so the system had to be adapted and equipped with suitable components. One of the main focal points was the so-called pulse valves. These had to be capable of generating the strongest possible shock wave. Following a long series of investigations with different valve types, the sliding gate valve from Schubert & Salzer was selected.
The principle of this valve was fascinatingly simple: two slotted discs that slide over each other and seal against each other. A sealing plate, fixed perpendicular to the direction of flow on which another movable disc with the same slot arrangement is moved, changes the flow cross-section. The applied pressure difference presses the movable disc against the fixed disc and thus contributes to leak-tightness. The short opening times achievable by this principle and the pressure resistance with large nominal diameters were ultimately decisive.
Phase 2: From experiment to industrial use (2011 – 2020)
The first tests with the SIP test system on the Schwelgern 1 blast furnace yielded such promising results that thyssenkrupp Steel Europe decided to further develop the process beyond the research project. With its hearth diameter of 13.6 m, a total height of approx. 110 m and an internal volume of 4,416 m3, the Schwelgern 1 blast furnace has a potential output of 10,000 t per day. The welded steel construction, which is lined inside with refractory material and has a closed cooling water circuit, is one of the most modern blast furnaces in the world. Rainer Klock was to manage the further development of SIP as plant engineer and was appointed by thyssenkrupp Steel Europe towards the summer of 2010.
Whilst an industrially operational prototype had to be created on the basis of the SIP test system, this prototype was further optimised. “To further improve the effect of our process, we began to dedicate ourselves to the shock waves associated with each impulse,” explained Dr Klock, now a doctor of metallurgy. “We were convinced that, as part of the SIP, it was making an important contribution to the positive effect of the SIP on the process. We wanted to enlarge the raceway zone and break open blockages in the coke bed with strong shock waves. This would increase the permeability and consequently the efficiency of the blast furnace process with larger reaction surfaces.”
“The project team at AT.PRO tec explained what they intended to do,” said Marcel Mokosch from Schubert & Salzer Control Systems. “To generate impulses with even stronger shock waves, the high opening speeds had to be optimised still further to achieve extremely short opening times. In principle, sliding gate valves were the perfect choice for this application. The typical stroke between “open” and “closed” is only about 8 mm. This short stroke is accompanied by very small moved masses. For that reason, only small actuating forces are needed. As a result, the valve is ultimately more compact than most other valve types.”
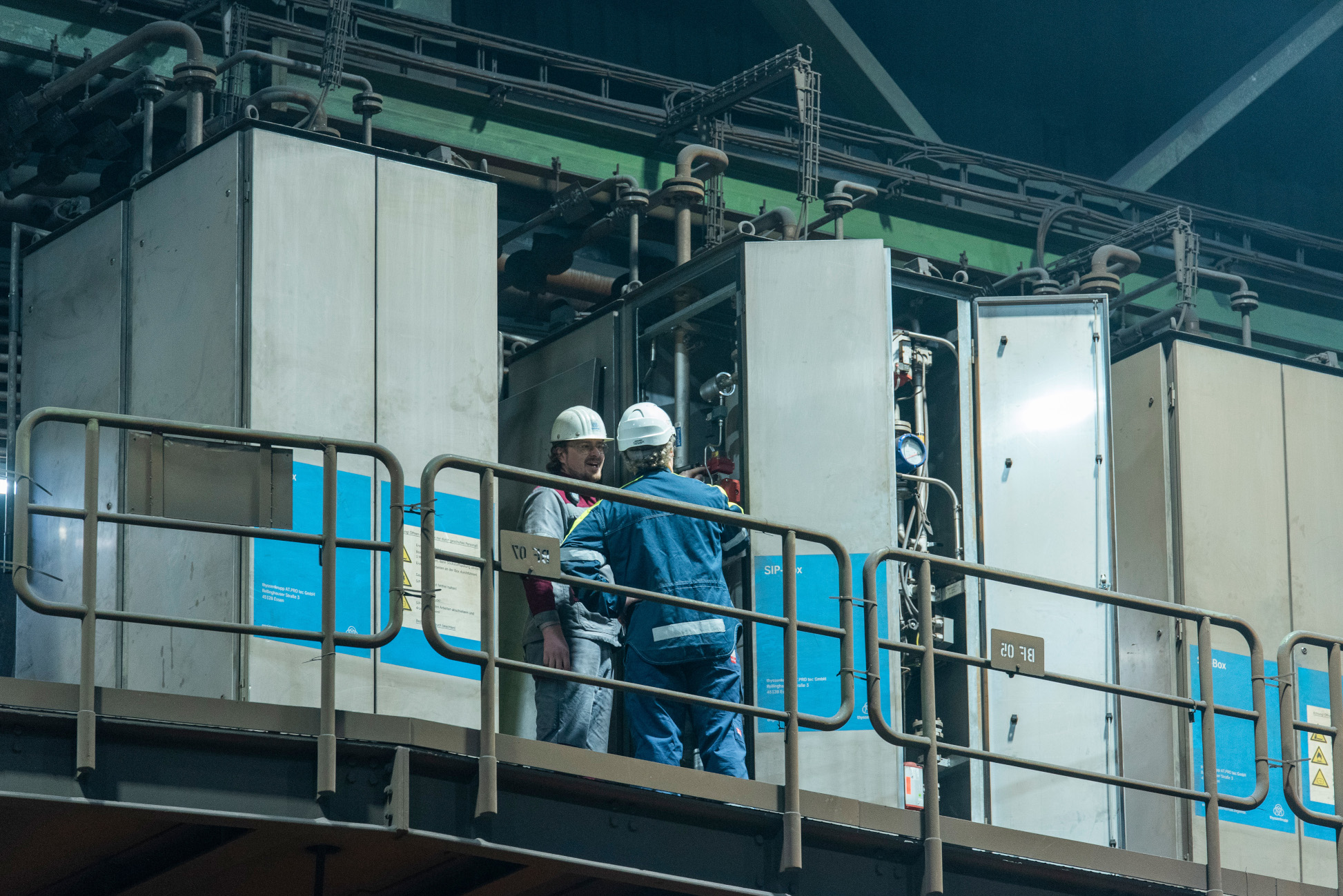
The first SIP box
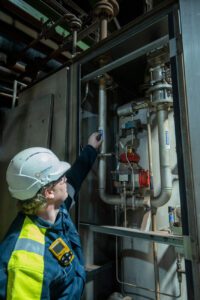
Following this meeting, the first “SIP box” – the prototype of the new system – ran in continuous operation for four to five years and was further optimised. Step by step, the original sliding gate valve design was developed together with the system and the process. Various design changes were made and then tested in practice to adapt the valve to the requirements of the application.
“Finally, we optimised the valve to a record opening speed of just 2 ms. This made it possible to generate impulses that reach deep into the coke bed with really strong shock waves,” said Marcel Mokosch. “However, the extremely fast switching speeds combined with high pressures and high switching frequency brought the valve to its load limits. This combination of requirements was really a challenge for us at the time, but we also saw it as a great opportunity for the sliding gate technology to prove itself. To achieve valve service lives that were acceptable to the user under these extreme operating conditions, their mechanical limits had to be extended by design changes. The declared goal was a service life of one year, in other words several million switching cycles.”
In 2015 the moment had finally arrived: thyssenkrupp Steel Europe and thyssenkrupp AT.PRO tec GmbH began with the development, installation and operation of a complete oxygen impulse process system on blast furnace 1 in Schwelgern. In the years that followed, the optimisation of the SIP boxes was finalised. SIP devices were installed on the 40 tuyeres of the blast furnace with the furnace in normal operation.
“Sliding gate valves were the perfect choice for this application.
Successful project completion
The SIP system was completed in autumn 2020. 40 SIP boxes were activated step by step over a period of several weeks. The effects on the process were awaited with excitement.
The SIP system on blast furnace 1 in Schwelgern paid for itself in less than two years of operation and now saves costs amounting to several million euros every year. Due to the increased efficiency, the total consumption of reducing agents (coke and injection coal) has been significantly reduced. This is also reflected in the CO2 savings of between 50 and 100 kg per tonne of pig iron produced, resulting in annual CO2 savings in excess of 100,000 tonnes.
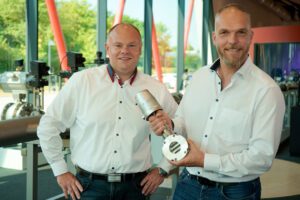
The entire project is a great success for thyssenkrupp AT.PRO tec: “After one and a half years of continuous operation, the Schubert & Salzer sliding gate valves have proven to be more than capable of coping with the extreme conditions. The many years of joint development work with Schubert & Salzer has more than paid off. Finding such a persevering and reliable development partner is not a matter of course,” explained Dr Klock, now the managing director of thyssenkrupp AT.PRO tec GmbH. “One of our future projects is to enable further automated process optimisations by linking the SIP technology and the blast furnace process with the help of a Level 2 automation system. First of all, however, our goal is to make the SIP technology a global success.”
When the technology was fully operational for the first time, thyssenkrupp.AT.PRO tec decided that partnering with one of the leading blast furnace plant and equipment suppliers would be helpful in achieving this goal. In August 2021 an exclusive worldwide marketing and sales agreement was signed with Primetals Technologies Ltd. “The intention is for our reliable partner Primetals Technologies to market this technology worldwide and to make it accessible to other steel manufacturers, too” concludes Dr Klock.
About this Featured Story
This Featured Story is an article from our Valve World Magazine, August 2023 issue. To read other featured stories and many more articles, subscribe to our print magazine. Available in both print and digital formats. DIGITAL MAGAZINE SUBSCRIPTIONS ARE NOW FREE.
“Every week we share a new Featured Story with our Valve World community. Join us and let’s share your Featured Story on Valve World online and in print.”