Valve malfunctions are often unexpected and always inconvenient. With pressure being put on maintenance crews to come up with quick solutions there can be scant time for root cause analysis. However, performing a proper failure analysis can help prevent future failures, delivering significant costs savings for plant owners.
By Bernard Horsfield
Every business will experience equipment failures, which are certainly not just found in valves. However, it is how businesses respond to such failures that is important. Correctly Identifying why equipment has failed not only saves time and cost but improves plant efficiency. There are also sound environmental arguments for understanding valve failures. Reducing the incidence of such failures will enable companies to lower their carbon footprints and reduce carbon offsets.
Consequences of equipment failure
Failure of an item of process equipment such as a valve can lead to one or more of the following: a process upset, increased potential of safety risks, impact on production/manufacturing output, logistic issues, increase in costs.
Given that an outage in a facility can easily cost tens of thousands of dollars, companies would do well to keep the incidence of equipment failures to an absolute minimum. Conducting investigations into failures will of course cost time and money. However, proper failure analysis is an investment which, over time, is recouped thanks to increased plant efficiency and a reduction in cost. In the author’s experience, many end users do not fully appreciate the value that improving functionality can deliver.
Even something as simple as carrying out more detailed inspections during scheduled service can provide valuable insights into whether items have failed, are likely to fail or are in good condition. This can help plants to better plan schedules and servicing, as well as to find better-performing products that will improve efficiency.
Causes of valve failures
In practice, valve failures and malfunctions can be due to a variety of reasons:
- mechanical operation
- design
- materials
- media
- operational (system), etc.
Let’s look at some of these aspects in more detail:
Design
The core design of an item (especially a valve) can dramatically affect its performance. With designers often following the ‘keep it simple’ mantra to reduce costs it is important to know which features may have been omitted. For example, if a specific valve design uses just one seal instead of the usual two, then that less expensive valve may only last a short time in service. Cost reduction usually means taking something away, the goal being to create a valve that is as simple as possible yet without compromising the product’s functionality. But ultimately, designing and manufacturing a product to last longer means higher quality and cost.
A proper knowledge of the design standards as well as field experiences is a considerable advantage during failure analysis. For example, an Indian petrochemical company installed low temperature valves carrying hydrochloric acid with the stem in the horizontal position. However, the standards only allowed for a 45-degree maximum. Needless to say the stem seals/packing failed and the valve was compromised causing the plant to leak hydrochloric acid everywhere which turned the whole facility brown (stainless valves and pipework).
Repairs can sometimes dramatically affect performance so the use of ‘Equipment passports’ identifying what work has been carried out on a valve/actuator during servicing is recommended. Ready access to details such as the service history, prior maintenance, etc, are of immense value during failure analysis. Details should also be recorded for actuators and especially the re-use of any scored or repaired actuators. These are known to have greater air leakage and lower operation times than undamaged actuators. Hence records of a scored actuator* will inform the operator that what he/she is seeing is actually ‘normal’ air usage for this scored actuator and not necessarily a cause for an outage.
As a pressure element, valves are obviously devices that firstly need to comply with international standards (minimum wall thicknesses etc) but should also be robust enough to withstand the stresses and strains applied in service. Using FEA (Finite Element Analysis) is often cited in this respect, but in itself FEA is not a panacea for stresses and strains. Far from it. The engineer needs to be able to read the results much like a doctor does an X-ray. It is very useful to have a background in testing valves as you gain the ability to correlate the FEA results with the actual results which is an important part of the FEA analysis.
As a tool, FEA can be used to identify weak points in multiple components and assemblies that may have failed, such as valves, support brackets, hangers, etc. Note that the Middle East is extremely vulnerable to corrosion – even onshore – hence the importance of building in a sufficient corrosion allowance etc.
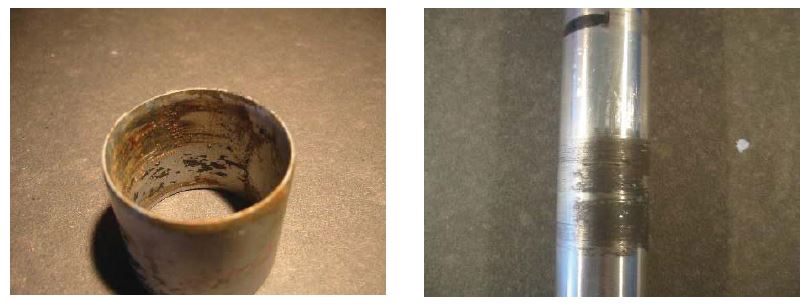
Materials
Material issues are often straightforward in that failures tend to be more obvious and there are plenty of third-party laboratories who can conduct microscopic, physical and chemical tests, as well as the FEA mentioned above. Afterwards, an expert is required
to interpret results and suggest the most suitable solution.
By way of example, an ammonia plant in China reported that a number of valves required an increased torque during operation. After dismantling and examination, it was discovered that the shaft bearings had galled and were inhibiting rotation. The primary cause was identified as incompatible design parameters, material and point loading. Erosion, chemical incompatibility or a galvanic reaction could all be due to the wrong selection of material for the specific process. This said, erosion due to pressure and media i.e. steam, is a world apart from erosion caused in a polymer discharge valve. Valve design is another factor that needs to be taken into account when reviewing materials.
Media
Failures caused by the media either in the pipeline or within the surrounding environment are usually quite obvious. Failure analysis is therefore often straightforward – typically the materials being used are incompatible with the application. However, it is not always obvious that the media is the cause. For example, there may be unknown elements or even contamination.
The Middle East oil fields are particularly difficult in that materials selected for internal valve components need to be suitable for sour service.
* Vane actuators can, unlike other actuators, withstand being scored in the air chamber through contamination through dirty air. The author has regularly seen them returned to service despite manufacturer’s recommendations.
Failure analysis in practice
Depending on the failure, analysis should ideally start whilst the valve is still in situ. Proper observation now enables potentially useful information to be gathered which may become compromised during the removal process. This can be an asset during the root cause analysis.
So, a step-by-step procedure – adapted to the failed item – will be extremely useful. This should apply to all items that require disassembly. There are tell-tale signs and marks which are easily missed yet can help to provide the whole story. The individual responsible for running the analysis should therefore have an ‘expert eye’. This can also prevent exactly the same equipment being re-installed to the detriment of the plant’s performance.
Proper inspection is also to be recommended during ‘regular servicing’ as this can provide the user and manufacturer with a great deal of information. As a result, the time between scheduled servicing can be extended. Take as an example; in the polyethylene business (gas phase) it is common practice to change out or service all reactor valves and actuators every two years. However, very few end users make any attempt to understand why this is required (other than one or two tag locations failing at that time) even though they wish to extend the service interval to every three years. Capturing this information could also be a real asset elsewhere, such as helping valve manufacturers to improve designs and assisting relevant authorities in producing new design standards.
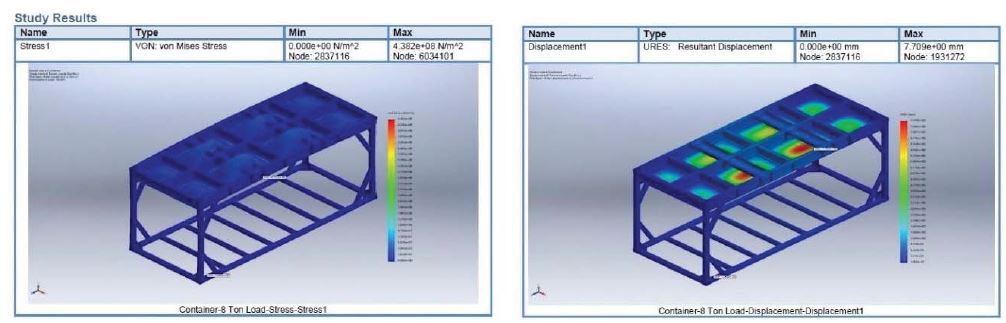
Working around time constraints
When a valve fails, this can result in a process upset or a manufacturing delay. In consequence, maintenance crews can be under significant pressure to resolve/repair/replace the item to get the production process running again. This urgency means that the time to analyse is very short unless of course a direct replacement is at hand, enabling a more leisurely examination of the faulty equipment. However, most items are quickly repaired or serviced with no attempt made to identify the root cause. Note that this does not mean that analysis is impossible, but it is more important than ever to have an experienced person available who can supervise the work and at the same time capture important information. Simply reviewing all the components after dis-assembly may be sufficient to reveal important insights. Creating an image file is highly advised; this enables a detailed analysis even after the valve has been reassembled and also facilitates the preparation of a written report at a later date. The equipment supplier may even provide this service.
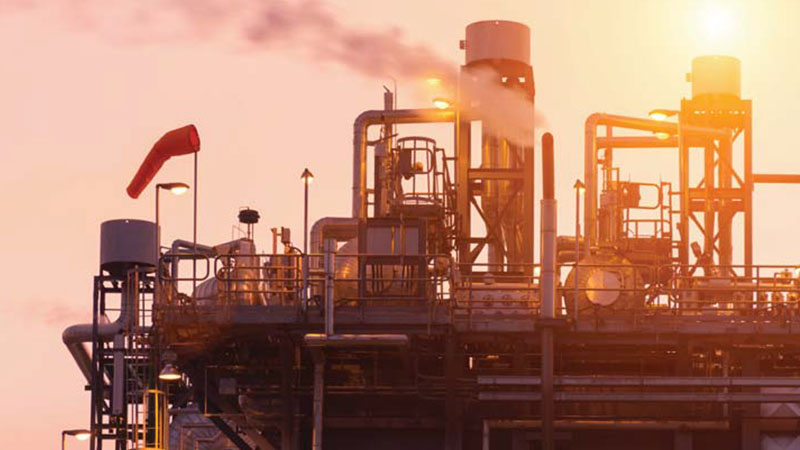
Valve failures in practice
Throughout his career, Bernard Horsfield has witnessed multiple valve failures. Clockwise, starting top left: severe erosion on a ball valve, NJ ball valve with a worn surface, valves should only be disassembled according to a careful disassembly procedure or with an experienced person in attendance to preserve and record evidence of failure, external corrosion on a valve.
About the author
Bernard Horsfield has been in the valve industry since 1990. With extensive work experience in the Middle East and Asia, he is highly skilled in cryogenic design, applications and Gas Phase Polymer Discharge reactors.
Starting out with Neles Jamesbury, career highlights include designing the first LNG valve train assemblies for Shell Brunei and later upgrades for UCC’s gas phase polymer reactors in Europe and the Middle East. He later became Engineering Manager for Metso Automation’s ‘Jamesbury’ Product line, focusing largely on the Middle East and India.
Bernard is currently a Director at Rodefish Ltd, which was initially set up in 2005 to project manage the DBB safety valves for Shell Oil’s Corrib Project. Rodefish provides a suite of services to the broader valve sector, including design, quality, customer support, etc. Based in both the UK and Abu Dhabi, UAE, the company also provides ‘In country’ technical/sales support for UK and US companies not in country.
About this Featured Story
This Featured Story is an article from our Valve World Magazine, September 2023 issue. To read other featured stories and many more articles, subscribe to our print magazine. Available in both print and digital formats. DIGITAL MAGAZINE SUBSCRIPTIONS ARE NOW FREE.
“Every week we share a new Featured Story with our Valve World community. Join us and let’s share your Featured Story on Valve World online and in print.”