Why version 2.0 of the Control Valve App by UReason focuses on providing recommendations on next best actions.
By Nicolas Spiegl and Moutusi De, UReason
Predictive maintenance using process data and algorithms is no longer a mere concept; it is a strategy to detect changes in an asset’s condition before these changes compromise performance. By identifying potential future issues, necessary actions can be taken in advance to prevent these. However, when applied to numerous assets—say, hundreds of control valves in one plant—sifting through the influx of information and determining the right course of action can be a real challenge. How this challenge is addressed can make the difference between success and failure when scaling up a predictive maintenance solution.
Predictive maintenance app
With the Control Valve App, UReason has developed a predictive maintenance tool capable of analysing the current asset health condition of control valves. This includes detecting failures before they become a problem, benchmarking the control performance of the valve, and accurately calculating the remaining useful lifetime of valve and actuator. The Control Valve App is now used by asset owners in the chemical-, pharmaceutical- and energy industry.
But as the adoption of the Control Valve App in individual plants grew from tens of valves to hundreds, so did the challenge of managing an ever-increasing volume of asset health data. To address this, the Control Valve App’s original algorithm was enhanced. Now, it not only diagnoses the valve’s condition but also converts this data into actionable insights—essentially, recommendations for next steps in the form of notifications or workorders in the maintenance management system. See Figure 1.
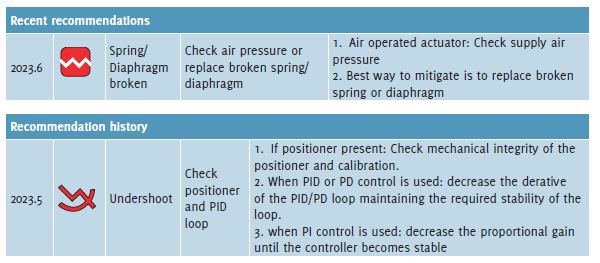
Version 2.0
The initial version of the Control Valve App employed a combination of expert and AI-driven algorithms to assess the valve’s condition using its setpoint and position. Version 2.0 goes a step further. It not only monitors the health of the valve and actuator but also automatically matches the observed conditions and changes with a robust set of recommendations. When crafting an algorithm that autonomously generates such advice, two pivotal aspects must be considered:
Precision in recommendations
Recommendations should be specific enough to be integrated directly into maintenance management systems. Given the detailed analyses the Control Valve App offers, it’s equipped to provide granular suggestions. These consider both the current state and the historical trends of the valve. For instance, a manual inspection might be mandated only if a particular failure is detected, and its severity escalates over a three-month period. To enhance visualisation and the usability, a novel asset health timeline has been introduced, tracking the evolution of asset health issues over time. See Figure 2.
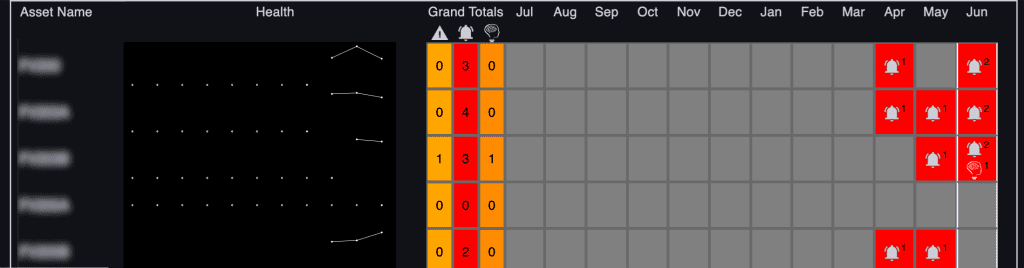
Customisability
It’s vital to customise recommendations to individual valves, specific process units, or entire plants. The advice should align with the unique asset management and maintenance strategies, which can vary based on the industry, location, process type, and other factors. For example, a recurring overshoot in a control valve could lead to substantial product loss in a specialty chemicals plant. In contrast, the same overshoot might be inconsequential in a bulk chemical production facility. The Control Valve App, by default, produces a set of industry-standard recommendations. However, domain experts have the flexibility to refine these suggestions to better align with a plant’s overarching asset management strategy.
A platform to tailor the PM process
In conclusion, as predictive maintenance tools evolve and are deployed at larger scales, they must not only detect failures before they affect operation, but they also must enable to use the new information and insight as part of the existing work processes. The Control Valve App’s Version 2.0, with its auto-generated recommendations based on valve conditions, exemplifies this integration. It offers a platform where domain experts can further tailor the recommendations, based on the health diagnostics of the app, their own know-how and expertise, and the asset management strategy of the individual process plant.
About the author
Dr Nicolas Spiegl is a chemical engineer who leverages his knowledge of technology and work processes to develop pragmatic digital solutions. He works with partners and clients in the process industry to reduce costs, increase efficiency, and innovate new business models. He can be reached at nspiegl.@ureason.com. For more information, please visit www.ureason.com.
Moutusi De currently serves as Marketing Lead at UReason. Her responsibilities involve crafting and executing innovative marketing strategies that drive sales growth and user acquisition. Her dedication to staying at the forefront AI and digital transformation fuels her drive to explore cutting-edge strategies that can propel UReason to new heights.
About this Featured Story
This Featured Story is an article from our Valve World Magazine, October 2023 issue. To read other featured stories and many more articles, subscribe to our print magazine. Available in both print and digital formats. DIGITAL MAGAZINE SUBSCRIPTIONS ARE NOW FREE.
“Every week we share a new Featured Story with our Valve World community. Join us and let’s share your Featured Story on Valve World online and in print.”