Hubei Taihe is considered an expert in the LNG valve industry, a sector with a very high technical threshold. The company is endorsed by both its sound track record involving almost every large-scale LNG terminal in China and its outstanding performance in the overseas market. Besides a full range of LNG cryogenic valves, Taihe has built up a unique “cryogenic valve digital full lifecycle management system” and several service centers around the globe.
By Laura Wang, Valve World, Shanghai
From LNG to a full range of cryogenic valves
As the company has grown to be a leading brand, it has gained a remarkable track record and sound reputation. Yet Mr Zhang Wenzhong, the founder of Hubei Taihe Petrochemical Equipment Co., Ltd. (Taihe) believes that LNG valves are never an easy arena for manufacturers. With over thirty years of experience in LNG cryogenic product R&D and marketing, Mr Zhang emphasises that the technical threshold for this sector is very high. Neither simple imitation nor short-term developments can create true value in this field.
Located in Zigui County, Hubei Province – known for its proximity to the famous Three Gorges Dam – Taihe was established in 2007. However, its research of cryogenic valves dates back to the early 1990s when Mr Zhang worked as technical director of a renowned European valve company. He gained a deep knowledge and understanding of manufacturing processes and technical solutions and, most importantly, created a pioneering design idea and service principle. This dictated that Taihe would have LNG cryogenic valves as its core product and would eventually be viewed as an LNG valve expert.
Impressive track record
Taihe has built up a full range of cryogenic valve products. Impressively, 80% of all 46” LNG terminal valves installed in China were made by Taihe. From the perspective of product type, Taihe butterfly valves for LNG applications account for 90%, and Taihe ball valves account for 60-70%. Other special types, such as the 46” class 150 top-side mounted triple offset cryogenic butterfly valve are used by PipeChina Longkou LNG Co., Ltd. In total, the Longkou project uses 5053 quality Taihe valves, including ½” – 46” Class150 – 1500 cryogenic ball, butterfly, globe, check and control valves. These statistics make Taihe the valve manufacturer who has supplied the most valves in quantity, the largest valve in size and the highest Class for the Longkou project, accounting for 85% of the total.
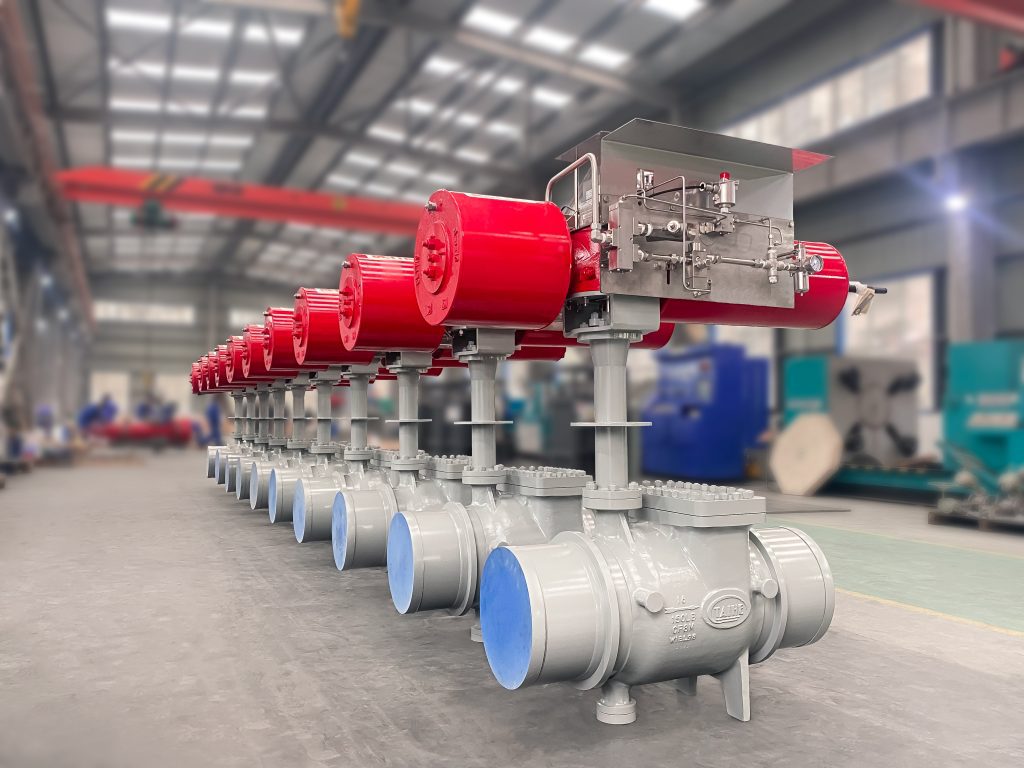
The 42” Class 150 pneumatic cryogenic control valve is used by Sinopec Qingdao LNG Co., Ltd, specifically in the 270,000 m³ Qingdao LNG tank farm project, the largest LNG tank farm in China. The 36” cryogenic butterfly control valve is used in the PipeChina Tianjing LNG tank farm. These valves outperformed the corresponding products of other manufacturers. Thanks to its product performance and high level of technical service, Taihe has become highly recognised and has won many orders for 42” cryogenic butterfly valves from customers including PipeChina Tianjing LNG, PipeChina Shandong Longkou LNG, Sinopec Longkou LNG, Sinopec Qingdao LNG, CNOOC Jiangsu Binhai LNG, Ningbo LNG, Zhuhai LNG, China Suntien Tangshan LNG, and ENN Group Zhoushan LNG.
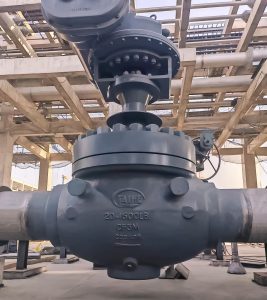
The company’s 24” Class 1500 cryogenic ball valve is operating smoothly in the PipeChina Tianjin LNG project. Its sound performance has attracted orders for massive amounts of various valves from Dalian LNG, Tangshan LNG, Tianjin LNG, Longkou LNG, Nanshan LNG, Binhai LNG, Rudong LNG, Qidong LNG, Pinhu LNG, Ninbo LNG, Zhoushan LNG, Wenzhou LNG, Zhangzhou LNG, Chaozhou LNG, Jieyang LNG, Yangjiang LNG, Beihai LNG, Hainan LNG, etc. Products involved include 1216 items of 6” – 24” Class 1500 cryogenic top-mounted trunnion/floating ball valves; and 28,652 items of ½” – 4” Class 150 – 1500 cryogenic top mounted ball valves. The sound track-records of other Taihe valve products, such as the 42” pneumatic cryogenic control valve and 36” roof breather valve, are also recognised.
Overseas markets
In the overseas market, Taihe has successfully won bids for a medium-scale LNG terminal project in Algeria and a super-large LNG project in Nigeria in 2023. Nearly 1200 valves were supplied to these two projects, including high-pressure cryogenic ball and butterfly valves of various sizes. Nigeria is currently the third largest LNG exporter in the world with the largest natural gas reserves in Africa; its proven natural gas reserves account for 37% of total reserves in Africa and are ranked ninth in the world. Taihe is working with the largest ongoing project in Nigeria, which will see 16 gas liquefaction production lines built with a designed capacity of 4.56 MMTPA, eventually increasing to 17 MMTPA.
Investments in development
Whether in the domestic market or overseas, Taihe’s competitors are all internationally recognised brands. In 2015, Taihe mastered the core technology regarding large-size cryogenic valves and developed over twenty new products and flow control techniques. This broke the multilateral monopoly of several other brands in this specific field.
Taihe has consistently invested in technical innovation and R&D, with around RMB 87 million being invested by 2023. It also established an R&D centre in Frankfurt, Germany, with a team of professionals from all over the globe who continue to develop advanced flow control technology.
Taihe is the first manufacturer in China to be approved as a ‘National Cryogenic Valve Technology Research Center’ by the China Petroleum and Petrochemical Engineering Institute. In cooperation with domestic and foreign firms, Taihe has developed dozens of new items, including cryogenic (-196 to -256°C) control valves for LNG, ships, liquid hydrogen and below 3000+ meters (deep- sea) applications.
Clearly, Taihe’s cryogenic valve manufacturing techniques and skills have risen to an advanced level which is now widely recognised by customers worldwide.
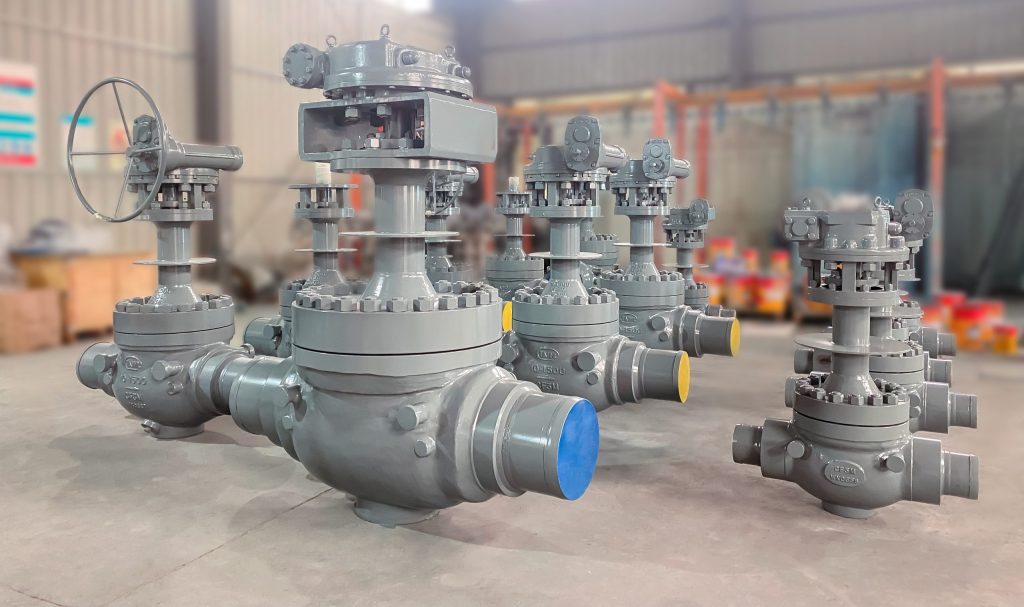
Life cycle management powered by digitisation
As a specialist focused on LNG cryogenic valves, Mr Zhang and his team place LNG applications at the heart of the company’s managerial strategy and operating model. Accordingly, Taihe has used digital technology to build a unique cryogenic valve full lifecycle management system. The system covers the entire manufacturing process – from raw material inspection, admission and secondary inspection to processing, inspection, flaw detection, intensive pressurising, assembling, cryogenic testing, room temperature testing, and coating – through to installation, operating and maintenance. All information involved is digitised and entered into the management system. Customers have access to all data relating to the valve products they use.
Mr Zhang also attaches great value to the quality control of the supply chain for LNG valve materials and parts, with resources invested in production and supply. The goal is to reduce or even eliminate any possible quality issues by ensuring a sound supply chain.
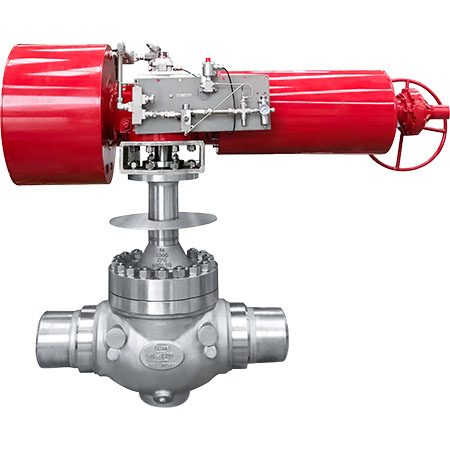
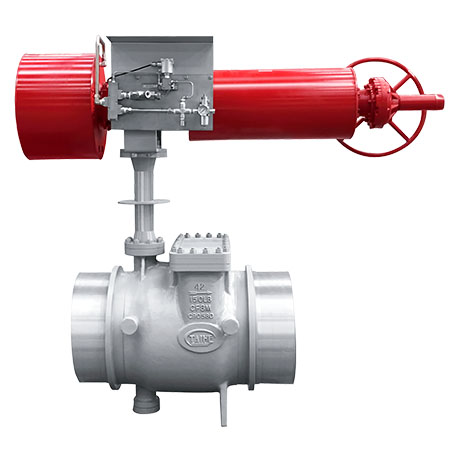
Outstanding quality
As Taihe has grown to a globally recognised brand in the field of LNG valve products, a commitment to outstanding quality remains the major driving factor, according to Mr Zhang. In the early years, before the company had an established brand and track record, Taihe kept a proactive attitidue and accumulated experience in LNG valve maintenance and repair.
Occasionally, their valves were used in LNG projects as substitutes or transitional products. These opportunities allowed the then-unknown brand to exhibit remarkable competitive power due to outstanding quality. While competitor valves experienced issues, Taihes’ LNG cryogenic valves operated smoothly as expected, even though they were considered temporary replacements. This proved to be a decisive advantage in demonstrating Taihe quality, allowing it to gain trust and a prominent reputation from worldwide customers.
The newly built Cryogenic Valve Smart plant consists of six flexible production lines. It features a comprehensive smart inspection system that completely excludes any chance of human intervention and manipulation through computer-generated inspection reports. The powerful manufacturing capability and abundant professional experience perfectly match future customer needs. Taihe took advantage of these strengths and gradually built a differentiated “customised + mass-produced LNG cryogenic valve solution”. This combination is set to differentiate the Taihe brand with a unique advantage; from the product performance perspective, Taihe satisfies both the general and challenging requirements of various LNG applications; from the business perspective, Taihe creates additional value for customers with good quality, optimised performance, delivery cycle and cost.
Global technical service centers
With the ongoing development of its international business, Taihe has established a sales office and five technical service centres globally. The sales office in Singapore oversees the total overseas market, while technical service centres located in Naples, Vancouver, Dubai, Sydney and Sao Paulo cover the world’s major energy and chemical markets: Europe, North America, Middle East, South East Asia and South America.
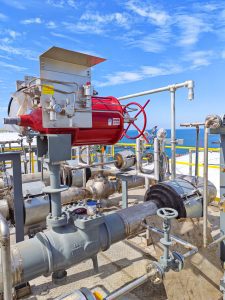
Besides the advantages offered by its premium quality and competitive delivery cycle, Taihe’s service is second to none. With years of experience in the field of LNG valve products, Mr Zhang and his team have gained deep knowledge about any possible issues that may arise in various conditions and applications. This knowledge enables them to optimise LNG cryogenic valves at the R&D stage. Additionally, abundant experience also facilitates the provision of professional and efficient after-sales service.
The five service centres around the globe demonstrate Taihe’s determination to develop its overseas market and to provide quality after-sales service, including prompt on-site maintenance, inspection, replacement of parts, etc. Indeed, the company’s after-sales and maintenance service is a well-established, steady source of revenue, further optimising its business structure and profit composition. It enables Taihe to generate more profit to fund new product development and iteration. The goal is to provide one-stop LNG cryogenic valve solutions featuring “Taihe quality” and “service-from-China” to worldwide customers.
Because of the full range of products, outstanding quality, reduced delivery cycle and professional technical service, Taihe’s brand influence in LNG valves is going from strength to strength. Every time we speak with Mr Zhang – the founder of Taihe and an old acquaintance of Valve World – we learn more about Taihe’s strength and development principles and the future of LNG valve products from a rational perspective.
As Mr Zhang concluded: “In the future, Taihe will input more resources to the fields of FLNG, LNG tanks, and ship applications. We aim to become one of the world’s leading cryogenic valve manufacturers.”
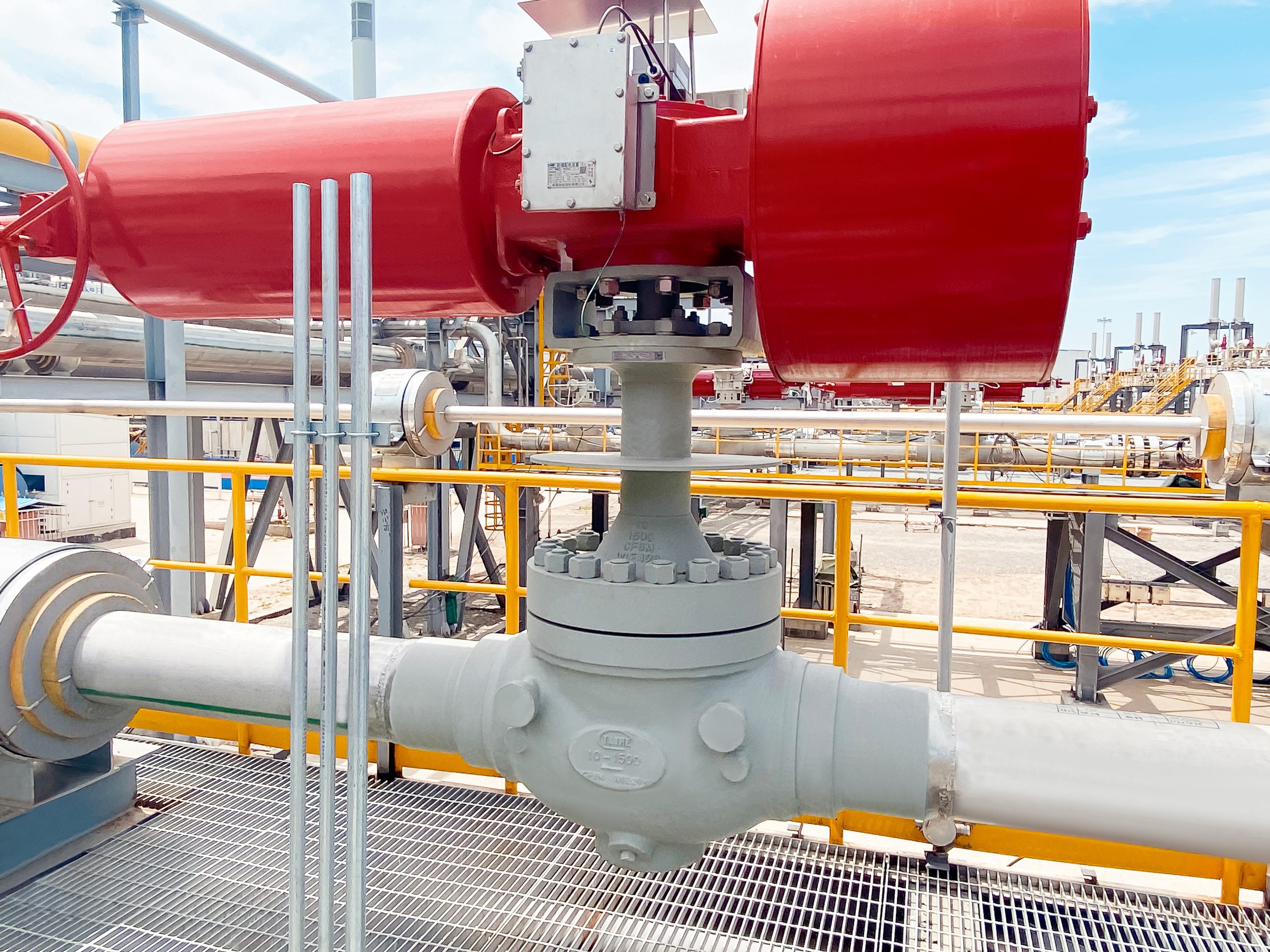
Cryogenic Valve Smart Manufacturing Project
Taihe’s Cryogenic Valve Smart Manufacturing Project, representing an investment of RMB 286 million, will soon be complete, with equipment installation and commissioning underway. The new plant occupies 60,200 m2 with a total floor area of 34,842 m2. It houses over 500 items of equipment, such as high-performance inspection instruments, a CNC centre, numerical control machine tools, welding robots, etc. The smart plant combines digitisation, informatisation, integration and eco-friendly principles under one roof.
On completion, production capacity will increase by a factor of five while significantly reducing the production time. Annual output is expected to soar to RMB 800 million. In addition to satisfying the increasing needs of domestic customers, Taihe will supply the international market. Advanced digital equipment and unmanned production lines reduce human intervention during manufacturing, leading to improved product standardisation. Combined with precise full-process quality inspection, this will significantly contribute to the outstanding quality and performance of Taihe valve products. The new plant will also serve as a platform for product upgrading and R&D.
About this Featured Story
This Featured Story is an article from our Valve World Magazine, March 2024 issue. To read other featured stories and many more articles, subscribe to our print magazine. Available in both print and digital formats. DIGITAL MAGAZINE SUBSCRIPTIONS ARE NOW FREE.
“Every week we share a new Featured Story with our Valve World community. Join us and let’s share your Featured Story on Valve World online and in print.”