The valve trifecta consists of the highest quality, best delivery, and lowest price. When looking to purchase a valve, these three aspects, in this specific order, should be taken into consideration, and together become the ideal standard in valve selection. Part one was featured our September issue.
By Charlie Evans and Angelica Pajkovic, Valve World
Valve World had the pleasure of speaking about the valve trifecta with Matt Hartfiel, Vice President of Downstream, Industrial & Energy Transition – Valves, Automation, Instrumentation and Measurement, and Charles Metrailer, Executive Director of Downstream Valves & Automation from MRC Global. In Part Two of this article, they discuss the importance of price and total cost of ownership and offer key strategies for valve procurement.
When choosing a valve, there are numerous factors to consider. While it is ideal to strive for the best in all three categories, namely quality, delivery, and price, compromises must inevitably be made to select the correct valve for the application. “Relying upon decades of industry experience, we continuously analyze each aspect within the trifecta and attempt to understand the importance of each in relation to the overall value for the customer,” said Hartfiel. “End users are becoming increasingly dependent upon knowledgeable suppliers to assist them in their decision-making processes.”
The application
Understanding the service conditions is the first place to start when selecting a valve, with a specific approach taken for each installation. As an example, is the valve for a non-critical, utility service or for a severe service application where safety is paramount?
In non-critical applications, the valve with the lowest price based on the customer’s approved manufacturers list should be sufficient. There are numerous areas within a plant that do not require highly engineered valves, including applications such as utilities, vents and drains. These ‘utility’ valves are typically non-alloy in nature (e.g., bronze, iron, and carbon steel), with ample availability in the market through local distribution and sufficient manufacturing capacity. “Price and volume will likely be the dominant drivers in these cases,” said Hartfiel.
However, for critical or hazardous applications, special considerations should be taken to incorporate reliability and fit-for-service. Even within the procurement process, non-commercial factors such as non-destructive examination (NDE), casting quality and adherence to specific standards should be examined. “In addition, costly implications of leak detection and repair (LDAR) need to be considered to understand the complete picture and not just the initial price,” said Metrailer. Examples of hazardous applications include chlorine, phosgene, isocyanates, and hydrofluoric acid.
Synergizing capital projects and MRO
Often seen as the most price driven, capital projects are highly budget oriented, while also requiring strict schedules to be met. One of the areas that can be overlooked is the future state once the project has been completed and the site or unit is fully operational. Did the project team consider the future maintenance strategy in the decision-making process, or was the initial cost of the material the predominate focus? It is not uncommon for the maintenance team to completely replace the original equipment installed due to misalignment on the longer-term reliability and maintenance strategy. Additionally, the fabrication and skid manufacturing can also be a piece of the project heavily driven by price, while intentionally or unintentionally not taking into consideration the end user’s approved manufacturers list. This can also create a disconnect with the future maintenance strategy, leading to unnecessary spend by the end user during a future turnaround event.
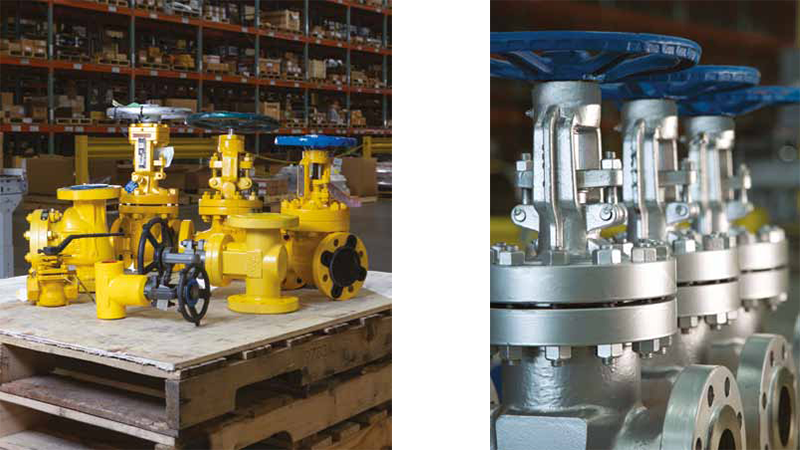
Planning and delivery
Whether project or MRO, proper planning has become increasingly necessary to ensure cost control and on-time delivery of material, especially considering the global supply chain challenges experienced during the COVID and post-COVID eras. “Generally speaking, manufacturers will offer their lowest cost option based upon full factory deliveries to maximize efficiencies and productivity. This can be an effective procurement advantage if ample lead-time is available. Otherwise, the lowest cost options may present an increased risk to the job if lead-times exceed schedules or promised deliveries are missed,” Hartfiel added.
Total cost of ownership
End users expect the industry (distributors, manufacturers, etc.) to be able to quantify the value of each valve in reference to the design, quality, and reliability during their commercial evaluation. When looking beyond the initial cost of a valve and ahead to the future maintenance needs, new realities can start to unfold. Poorly functioning or misapplied valves can lead to premature failures, excess emissions, significant downtime, unplanned outages and worse, human injuries. In the end, the initial cost of the valve can represent a fraction of the overall cost of the valve at the end of its lifespan. “Most of the time people only think about the first or upfront costs – especially when the next valve in line costs 50% more,” said Metrailer. “If one valve lasts three years, and the other lasts five years, it may be worth thinking differently and holding quality in higher regard than price.” If the lower-cost valve must be replaced more frequently, there exists a growing associated cost.
“Thinking about the whole picture is something that is very important for end users to remember,” continued Metrailer. “We give customers access to resources and provide them with the education that will aid them in making the best possible choice for their company, especially as the industry continues to lose subject matter experts due to retirement.”
Cost analysis example
Valve type: 3⁄4” 800# A105 gate valve:
- Initial cost ~$50
- Average cost to change out: ~$4,000.
- Based upon the above, it is easy to see that understanding the importance of how valves can and will operate in service is critical to cost control and total cost of ownership.
Deeper data analytics
As the industry has evolved, customers have expanded their data driven approach to valve selection and purchasing. In addition to traditional procurement and category management teams, end users have begun adding third party consultants to help them evaluate procurement best practices and cost savings initiatives. This can lead to innovative solutions and valuable cost savings but can also risk further commoditizing the valve industry based upon a one-size-fits-all approach. Valves can quickly become random numbers in an electronic catalog and lose their uniqueness and application-centric capabilities. Conversely, many licensors have strategies in place based upon the valve type considered ‘Most Effective Technology’ (M.E.T.). There remains an opportunity in the industry to expand this approach and truly understand how valve designs and product solutions increase safety, reliability and total cost of ownership. Valve manufacturers offer solutions within their portfolios based upon problems that have been solved in the past. In many cases the design itself originated not by chance but because of an unresolved problem that required additional innovation and creativity. “Our industry stands at a critical juncture in history to professionally articulate our overall value proposition using experience, data, and success stories,” stated Hartfiel.
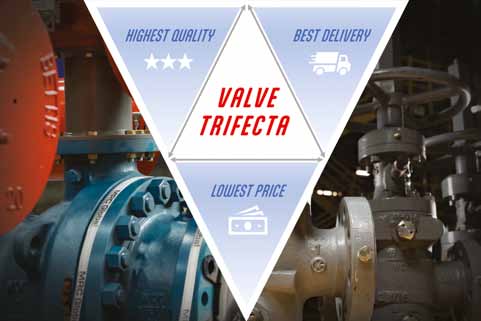
Final thoughts
While the valve trifecta – highest quality, best delivery and lowest price – is ideal, each factor must be carefully considered from every angle to determine what can be compromised and what is required. When asked their thoughts about the valve trifecta, Hartfiel and Metrailer came to the consensus that quality remains the most important factor to be considered, as it relates to both price and delivery.
“Overall, it comes down to knowledge and collaboration with experts to determine the best valve for minimizing the total cost of ownership,” concluded Metrailer.
About this Featured Story
This Featured Story is an article from our Valve World Magazine, November 2023 issue. To read other featured stories and many more articles, subscribe to our print magazine. Available in both print and digital formats. DIGITAL MAGAZINE SUBSCRIPTIONS ARE NOW FREE.
“Every week we share a new Featured Story with our Valve World community. Join us and let’s share your Featured Story on Valve World online and in print.”