For over three decades, Bernard Horsfield has been advising plant owners on how to improve valve performance in PE facilities throughout Europe and the Middle East. For Valve World, he kindly gave a personal outline of many of the ‘lessons learned’ as regards valves in critical service in polymer discharge systems (PDS).
By Bernard Horsfield
In this article I will discuss the valves used in polymer discharge systems (PDS) found in gas phase fluidised-bed polymerization plants. Gas phase polymerization is a flexible way to manufacture high quality grades of polyethylene (PE).
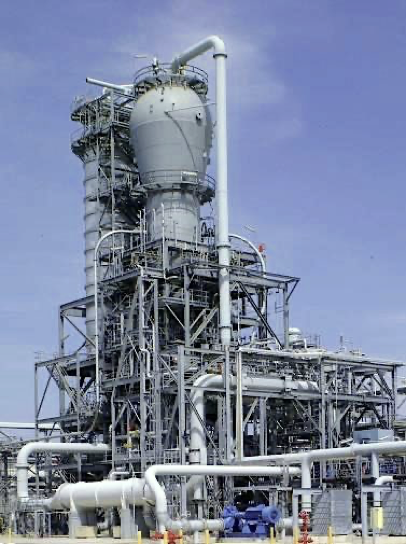
In fact, gas phase process technologies represent the largest PE footprint in the world. PE is used to produce a wide array of commodity and premium resins that are used in everyday products including food packaging, plastic bottles, recreational equipment, pipe, and larger commercial goods.
An advantage of the gas-phase processes is the relative ease with which the reacted polymer can be separated from the unreacted monomer. This process also enables the production of different types and grades of polymers from a single reactor. In a reactor, gaseous monomer, comonomers and proprietary catalysts combine to produce a dry, polymer resin. This resin – along with hydrocarbon vapour, unspent catalyst, and possibly polymer sheets and chunks – flows from the reactor to the PDS where unreacted gas is separated from the product and returned to the reactor. The resin product is then fed downstream where it is purged with nitrogen to neutralise any remaining absorbed hydrocarbons. Finally, the granular polymer is pelletized.
The PDS usually consists of a number of vessels, as well as a range of valves and piping. Valves provide control for the PDS, isolation, gas venting and recycling. All these valves are classified as critical control elements.
Valve design problems
with gas phase polymer reactors in my role as technical support for a leading valve manufacturer. End user companies were making significant investments at the time, so I travelled widely to visit plants throughout Europe and also the Middle East. These were exciting times for equipment suppliers, thanks to technology developments, the introduction of new catalysts and increases in production capacity. However, such changes were putting larger loads on equipment like valves, causing problems. I therefore worked with our factory to address issues of erosion and impaction.
It was the valves installed in the PDS that quickly had our particular attention. Looking to identify unexpected failures, we realised that the polymer powder was getting under the soft seated ball valve being used at the time. This led to a dramatic increase in the torque required to cycle the valve. If not addressed, the valve would seize up.
I have to explain at this point that the main problem of impaction is not just the powder, which for want of a better description resembles washing powder. As this powder leaves the reactor it may still be in the process of changing from a monomer into a polymer thanks to the presence of catalyst. It is the growth of this media once it gets into a cavity that causes the real problem. If trapped polymer continues to ‘grow,’ it can exert huge loads on components. In my early years, I personally witnessed multiple instances where polymer discharge valves had seriously eroded internals as well as cavities which were completely filled with catalyst.
At the time the seats were made of carbon-filled PTFE, which in hindsight were always going to be a problem. Fortunately, a solution from the USA was found that would hold the seats more firmly in place during valve operation.
Later, industry moved to the use of trunnion-mounted, metal-seated ball valves with PEEK inserts for bubble tightness. Equipped with high-cycle actuators, these constitute the valve of choice for many polymer producers. The polymer-proof metal seat prevents valve seizure and the anti-abrasive feature that withstands the hard polymers and abrasive catalysts found in polymer production plants today.
Back to the 90’s, Tungsten carbide coatings were another step forward. The technology was still in its infancy back then, with many coated balls having to be rejected immediately after production due to cracking, glazing or peeling. With perseverance we managed to eliminate all the problems, but this took quite some time working closely with suppliers.
Stem leakage
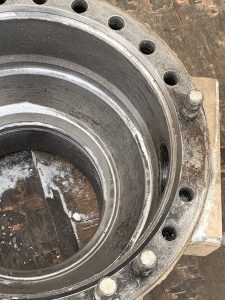
Like most engineered equipment, once you modify and improve one part you move the load to the next weakest point. In this case it was the packing and stem leakage. We had achieved a higher cycle capacity and the packing couldn’t cope.
Die-formed graphite packing rings formed the company standard at the time. However, when these proved ineffective in polymer discharge valves, a PTFE chevron packing set was adopted. At the time we were using both floating and semi-floating balls, the latter being trunnion-mounted. Both designs had independent stem/packing cartridge.
Why am I telling you this? Because it is important to explain how fire safety was achieved even though we used a complete set of PTFE chevron packing.
The principle of our design was that as the packing degraded or became ineffective in a fire, the stem would move up slightly under pressure (for reference, the movement would only be a few millimeters even on a product as large as a 10” floating ball valve). The stem would then create a metal-to-metal contact with the valve body, effectively stopping the potential escape of media.
When I was working with a plant in Europe, I personally witnessed numerous packing sets that had become solid PTFE blocks due to cold flow under compression.
To understand how this happened, we need to consider the static and dynamic loading experienced by packings used in valves with rotating stems. The outer diameter seals against a static valve body whilst the inner diameter is expected to seal against a rotating surface. Needless to say, the chevrons wore out very quickly on the inner diameter in this application. The continual tightening of the gland ring together with the process temperature meant that ‘cold flow’ of the virgin PTFE also played a factor in producing a solid block of PTFE.
By now, the customer was under a great deal of pressure to eliminate ethylene leakage into the environment by the local authority in France. So, we needed to find a solution quickly. As both a design engineer and technical support for a key end user, I was able to set up my own test cell and trial a number of designs I had put together.
As the stem and packing on the PDS valve was a cartridge design I did not have to use a complete valve for the tests. Valve pressure did not play a role in this failure which was purely due to packing load, temperature and duty cycle.
My background in other industries paid off and a solution was developed using seals specifically designed for static/dynamic loads in combination with a standard packing set. I personally delivered the first stem cartridge, which weighed in at 12 kilograms. Incidentally, I took it on a plane as hand luggage; something I very much doubt would be allowed today. Fortunately, the assembly was extremely successful, and the facility hit a high in production output.
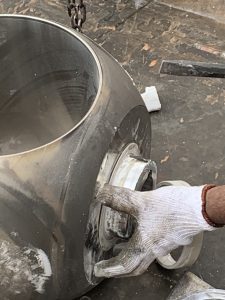
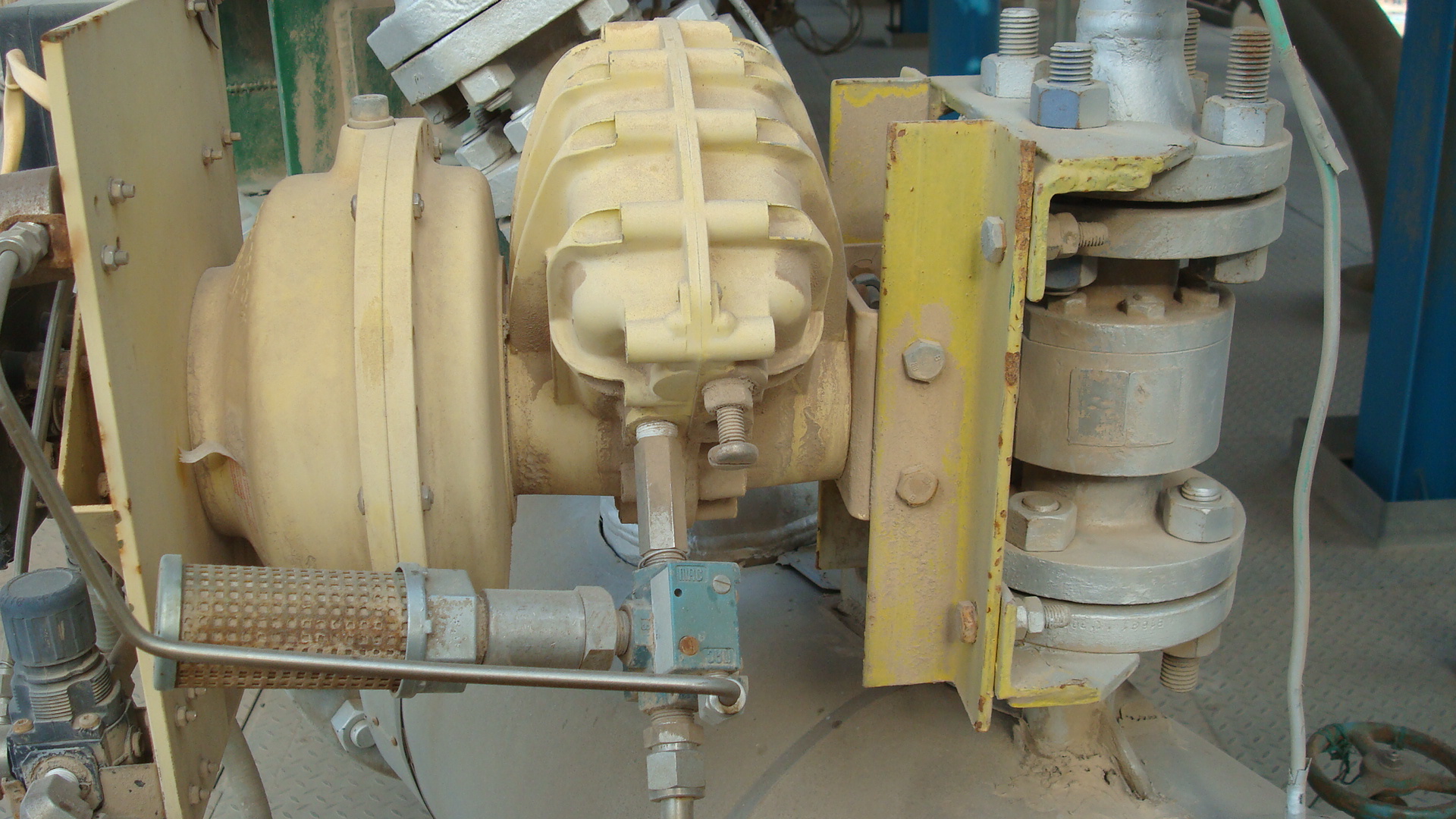
Extending service intervals
As technical support, I worked closely with a client that had five separate plants in Saudi Arabia. In those days there was very little security, with both movement and entry almost unimpeded. I was therefore a frequent visitor, moving regularly from site to site.
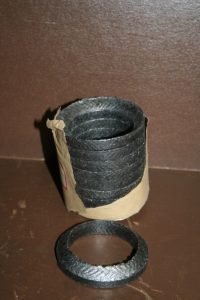
I recall supervising the valve outage from a facility that wanted to benefit from the various valve upgrades we had designed. The valves were then moved to a local sub-contract service workshop for stripping and cleaning, followed by insertion of the new seat supports. Of course, all the necessary checks were in place, such as an on-site inspector to check the welding procedure specifications.
That particular refit took up two whole weeks. Nowadays, the same work is often accomplished in just three days.
The experiences gained during these early years were most helpful in my further career, which saw me work with industry-leading companies and products. For example, when providing both commercial and technical support for plants in Saudi Arabia and Kuwait, I supervised both service and replacement of actuators and switchboxes. At the time, customers in these countries were replacing scotch yoke designs with vane actuators, to try and extend outages from two years to three years.
The vane actuator more than met the customers’ expectations in performance but the weak link continued to be the valves. In my honest opinion, valves that are properly specified and manufactured can achieve longer service intervals even in demanding applications like polymer discharge systems. The crux, however, is whether the customer is willing to invest in the technology that is required.
Requirements for PDS valves
Based on his decades of experience, Mr Horsfield recommends that the following list should be considered when selecting valves for use in PDS applications:
- Full-bore ball valves
- Tungsten carbide clad balls
- Metal seats with Class VI shutoff
- 316 stainless steel bodies
- Stems typically made from high-strength steel to resist torque inertia
- Splined stems eliminate backlash
- High cycling rate: 300,000 to 500,000 cycles per year
- Fast cycle times: 2 to 3 seconds
- Withstand abrasive media
- Prevent growth/impaction of polymer in cavities and grooves
- Withstand physical forces
- Withstand vibration (extra support sometimes required to standards ASME bodies)
- Live-loaded packings limits hydrocarbon emissions
- Firesafe design (and not ‘fire-tested design’)
- Canopies for actuators exposed to direct sunshine
About the author
Bernard Horsfield has been in the valve industry since 1990. With extensive work experience in the Middle East and Asia, he is highly skilled in cryogenic design, applications and Gas Phase Polymer Discharge reactors. Starting out with Neles Jamesbury, career highlights include designing the first LNG valve train assemblies for Shell Brunei and later upgrades for UCC’s gas phase polymer reactors in Europe and the Middle East. He later became Engineering Manager for Metso Automation’s ‘Jamesbury’ Product line, focusing largely on the Middle East and India. Bernard is currently a Director at Rodefish Ltd, which was initially set up in 2005 to project manage the DBB safety valves for Shell Oil’s Corrib Project. Rodefish provides a suite of services to the broader valve sector, including design, quality, customer support, etc. Based in both the UK and Abu Dhabi, UAE, the company also provides ‘In country’ technical/sales support for UK and US companies not in country.
About this Technical Story
This Technical Story is an article from our Valve World Magazine, December 2023 issue. To read other featured stories and many more articles, subscribe to our print magazine. Available in both print and digital formats. DIGITAL MAGAZINE SUBSCRIPTIONS ARE NOW FREE.
“Every week we share a new Technical Story with our Valve World community. Join us and let’s share your Featured Story on Valve World online and in print.”