As valves operators, end users develop their own standards and regulations to ensure their valves are complying with international best practices as well as raise the bar for the required minimum of optimum design versus product quality to ensure they are ready to operate and function.
By Mohanned Waleed Tarabzouni, Saudi Aramco
Valves are significant components of an operating facility where isolation is required. They require to be carefully selected and specified to be suitable for its intended function and purpose. This includes complying at least with the listed international standards and best practices in addition to developing internal codes or specifications to suit each organization’s application and systems.
Design specifications
As a major energy company, Aramco has a structured internal set of standards, procedures and forms to serve as minimum requirements for specifying valves.
These codes regulate specifications that addresses many aspects including but not limited to:
- Design
- Service
- Material selection
- Testing
- Inspection
The requirements of which these developed codes vary for the service, application and facility function. Several factors dictate case by case requirements that evaluate pressure, temperature, fluid type and other risk factors.
Service Requirements
Service specific requirements mandated in Aramco’s codes include application such as sour hydrocarbons, high temperatures, corrosive brine products and so forth. To give a brief about these requirements, these include the following:
-
Regular wellheads examination is important work toward the low emission arrival of crude oil to the surface. Image courtesy of Saudi Aramco. Subsea or underwater valves shall be of ball design and of class 300 as minimum with ring joint connection.
- Clean dry gases can be equipped with soft seated valves with double block and bleed features.
- Gas flare systems shall have only gate, ball or triple offset butterfly valves only.
- Isolation valves shall be fire tested and design verified.
- Any drain or vent shall be capped with a plug or blind.
- Pig trap main valves shall be of DIB-2 seat configuration and of through-conduit gate or ball valves only.
- Additionally, trim material for pig trap valves shall be duplex stainless steel with seat pockets overlaid with Inconel 625.
- Blowdown or kicker applications shall have lubricated plug valves.
- Instrument isolation valves shall be of API 602 gate valves.
The above listed shows a small number of several guidelines and requirements for service specifications listed as internal company standards. These are being revised, updated and upgraded based on lessons learned and projects experiences to ensure all valves are properly specified, selected and designed.
Design requirements
Additionally, some design requirements are specified to ensure the proper selection of the valve type, design, material and configuration. This includes the following:
- Installation of gate valves with horizontal or below orientation needs to be in clean service or utility applications to prevent blockage of the flow line.
- All threaded connections of valve bodies such as drain and vent shall be seal welded.
- Self-locked handles shall be provided for lever operated valves.
- Non-slam check valves shall be selected for rotating equipment discharge lines.
- Wafer type check valves are not permitted in hydrocarbon services.
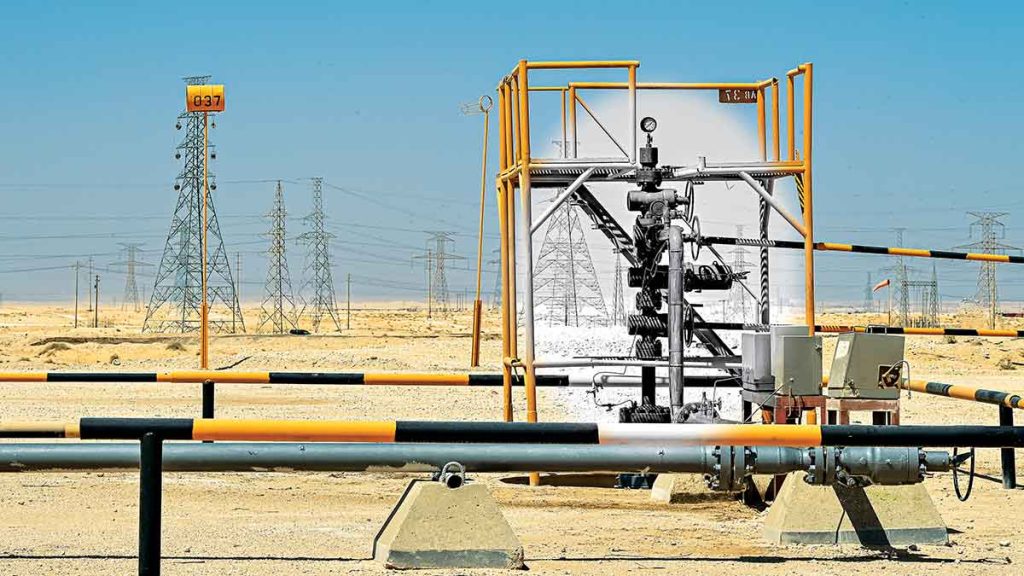
Design requirements are typically specified for each facility during project planning and design review to ensure a full understanding of the process and flow parameters as well as any additional requirements. Operations and maintenance best practices are always introduced to ensure past experiences have been addressed and logged.
To wrap up, end users require and build their specifications in alignment with international bodies and groups such as ASME, API, BS, IOGP and more. These combined maintain the minimum required specs are met to ensure safe and smooth operations of the facility and its assets. Aramco continues to ensure excellence in hydrocarbon transportation, shipping and handling through adopting these best practices and ensuring up-to-date specifications.
About the author
Mohanned Tarabzouni is a valve engineer with 10 years of experience in the oil/gas industry. He holds a master’s degree in pipeline engineer and Bsc in mechanical engineering. Mohanned’s roles include project design reviews, operations/maintenance supports as well as troubleshooting/conducting failure assessments.
About this Featured Story
This Featured Story is an article from our Valve World Magazine, March 2024 issue. To read other featured stories and many more articles, subscribe to our print magazine. Available in both print and digital formats. DIGITAL MAGAZINE SUBSCRIPTIONS ARE NOW FREE.
“Every week we share a new Featured Story with our Valve World community. Join us and let’s share your Featured Story on Valve World online and in print.”