Butterfly valve (MBSD), courtesy of SAMSUN Makina Sanayi
Discover how smart valves are revolutionising the water supply industry by providing real-time monitoring, predictive maintenance and optimised performance for enhanced efficiency and reliability.
By Guenter Oexler
The term “smart valve” has been interpreted in various ways across trade publications, valve magazines and articles, leading to confusion in the industry. With over 40 years of experience working with valves and process engineering, I aim to provide a clear understanding of smart valves, focusing on their applications in the water supply industry and beyond.
In discussions with startup companies developing smart valve solutions, I realised that there is a fundamental need to understand the valves themselves first. It is crucial to consider the application, the valve’s function within the system and the basic problems that need to be solved to create a truly smart valve.
This article primarily focuses on the water supply line, discussing butterfly valves, needle valves and ball valves, which can function as on/off valves, control valves and special devices such as main burst safety devices (MBSD) and pump guard non-return valves (PGNVs), which are essentially controlled check valves.
Understanding smart valves
First and foremost, a manual valve can never be considered a smart valve, even if additional devices like sensors and flow meters are added to it.
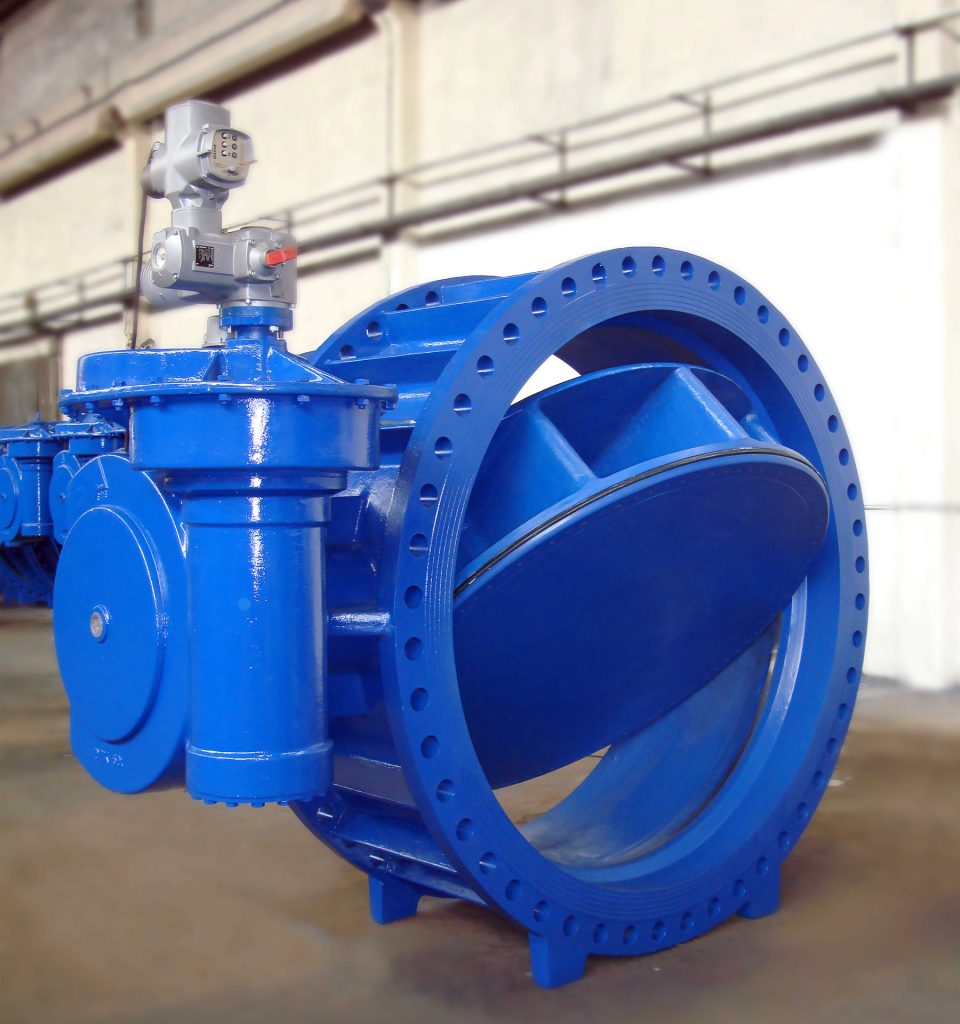
A smart process valve is an intelligent valve used in industrial processes to control the flow of media, such as water. Unlike traditional valves that operate based on manual adjustments or simple automation, smart process valves are equipped with sophisticated technologies that enhance their functionality, performance and monitoring capabilities.
There are multiple reasons to use a smart valve in the water industry. For example, consider a water supply line that feeds water from a reservoir through the countryside into the city network. This line includes safety valves, maintenance valves and at least one control valve.
Most of these valves are installed remotely, where automation requires a power supply, control circuits and communication. Without the addition of smart valve technology, these valves are essentially black boxes to us. Why? These valves, with an expected lifetime of 50 years, are located in remote areas and have a very low operation frequency, often only one cycle every five years or even less for on/off valves.
The situation is different for needle valves, which require permanent condition monitoring as they are essential for maintaining the stability of the water supply.
Key features of smart process valves
Here’s a detailed description of the key features and benefits of smart process valves:
Real-time valve monitoring
At any time, it is essential to know the actual situation of each individual valve and the related piping system. This includes the valve’s position (on/off/intermediate), flow rate, pressure and temperature, which are standard feedback signals from a process valve. What makes a valve smart is the additional data it provides.
Ensuring valve operability
The most important aspect for the user is to know that any specific valve is still in working condition. Imagine a butterfly valve (DN 2000, PN 25) installed for service conditions that stays open for 15 years. In common systems, we know the valve is open, but we never know if it will close when needed. One of the functions of a smart valve system is to periodically operate the valve by a few degrees to ensure it is in working condition.
Predictive maintenance
Smart valves collect additional data such as power consumption, running time and motor temperature. With a mathematical algorithm, deviations from normal operation can be detected within a safe corridor. As soon as the average data runs outside of this corridor, there is a setpoint for predictive maintenance. This eliminates the need for standardised, repeated maintenance and allows for maintenance to be scheduled based on the valve’s actual condition.
Collaboration with SAMSUN Makine Sanayi
In collaboration with SAMSUN Makine Sanayi, a Turkish manufacturer of ductile iron pipes, fittings and valves for the water industry, we had the opportunity to develop smart valves with all the aforementioned functions. We tested these valves at their extensive water testing facility and began collecting data for applicable mathematical modelling.
The benefit of this cooperation is that SAMSUN Makine Sanayi can perform a statistical review of the different types of valves from their production and provide customers with a proper outlook on the lifetime of each valve type. This allows for reliable setpoints for maintenance requirements, repair or replacement to be planned in a controlled manner, avoiding ad-hoc maintenance work and emergency calls that could potentially lead to a shutdown of the water supply. Furthermore, the collected data offers vast possibilities for process optimisation. An additional customer benefit is that as more smart valves are supplied and installed in the field, the reliability of the process control and predictive maintenance prepared and supplied by the valve manufacturer becomes more sophisticated. I extend my special thanks to SAMSUN Makine Sanayi for their courtesy and support in this endeavour.
Field testing setup
For this initial field test, we used SAMSUN Makine Sanayi butterfly valves equipped with AUMA multi-turn actuators and a Modbus interface. The setup also included a Modbus interface flow meter and pressure transducers in a similar configuration. All components were connected via an IO-Link master/GSM network to a cloud-based server, allowing us to test the system under field conditions.
This setup enabled us to have the valve under control and maintain a stabilised process, in this case, water supply stability. In remote areas, we were able to create an independent power supply by using a solar panel with an integrated power pack, as the electric devices used have low power consumption.
The field test demonstrated the feasibility of implementing smart valves in real-world scenarios, highlighting their potential to improve process control, reduce maintenance requirements and optimise water supply systems. The successful integration of various components, such as the valve, actuator, flow meter and pressure transducers, showcased the compatibility and interoperability of the smart valve system.
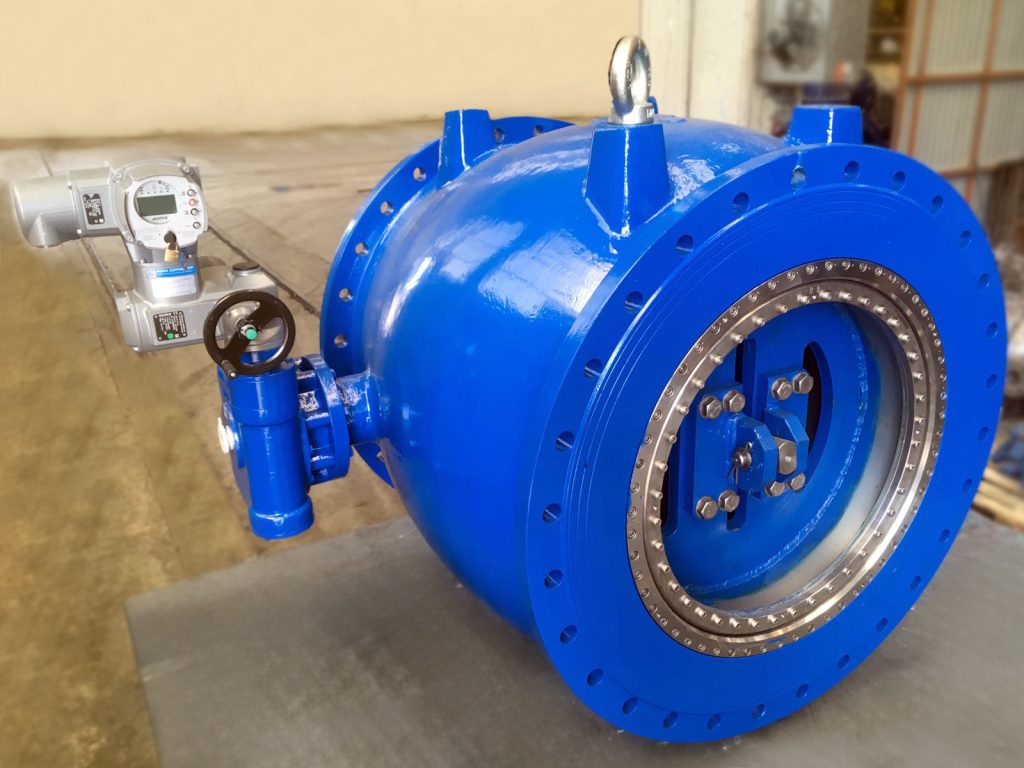
Diagnosing smart valve conditions
The smart valve system enables us to diagnose the condition of various valve types, including on/off valves, control valves, main burst safety devices (MBSDs) and more. By monitoring the condition of the electric actuator or the hydraulically actuated safety system, we can collect data that allows us to identify where wear and tear begins, such as in the media sealing, shaft bearing or sealing.
This advanced diagnostic capability transforms the valve from a black box into a transparent component that communicates its condition. The valve essentially reports its own condition, resulting in precise condition monitoring.
Optimising control valve performance
When monitoring a smart control valve or needle valve used for flow or pressure control, we can now avoid and/or reduce operation within harsh cavitational conditions. With our developed algorithm, we can detect these critical working conditions and adjust the smart control valve to operate within a non-critical range. This optimization of control valve performance offers several benefits:
- Extended valve lifespan by reducing exposure to damaging cavitational conditions.
- Improved process stability and efficiency by maintaining optimal operating parameters.
- Reduced maintenance costs associated with premature valve wear and failure.
- Enhanced system reliability and uptime by proactively addressing potential performance issues.
By leveraging the diagnostic and optimisation capabilities of smart valves, operators can ensure that their control valves are functioning at peak performance while minimizing the risk of cavitation-related damage. This ultimately leads to a more efficient, reliable and cost-effective water supply system.
Conclusion
The implementation of smart valves in water supply systems provides numerous benefits, including improved process performance and predictive maintenance of process valves. These advantages directly contribute to higher water supply output, reduced maintenance costs and minimised process installation downtime.
By leveraging the power of real-time monitoring, advanced diagnostics and performance optimisation, smart valves offer a comprehensive solution for enhancing the efficiency, reliability and cost-effectiveness of water supply systems. As the technology continues to evolve and mature, the adoption of smart valves is expected to become increasingly widespread, setting new standards for water supply management and maintenance practices.
About the author
Guenter Oexler brings decades of experience in valve design, process engineering and customised solutions for process control applications worldwide. His current focus lies in optimising process valves through smart valve solutions, emphasising long-term use and maintenance. Additionally, he works on optimising process applications in the water industry, specifically targeting the reduction of water losses.
Dive Deeper into Valve World
Enjoyed this featured article? There’s much more to discover! Subscribe to Valve World Magazine and gain access to:
- Advanced industry insights
- Expert analysis and case studies
- Exclusive interviews with valve innovators
Available in print and digital formats.
Breaking news: Digital subscriptions now FREE!
Join our thriving community of valve professionals. Have a story to share? Your expertise could be featured next – online and in print.
“Every week we share a new Featured Story with our Valve World community. Join us and let’s share your Featured Story on Valve World online and in print.”