This article explores new valve designs that improve how molten salt is managed in solar power plants. It shows how these innovations are making solar energy more efficient and reliable.
By Krishnakumar Viswanathan, Global Engineering Leader and Vignesh Murugan, Engineer, Flowserve
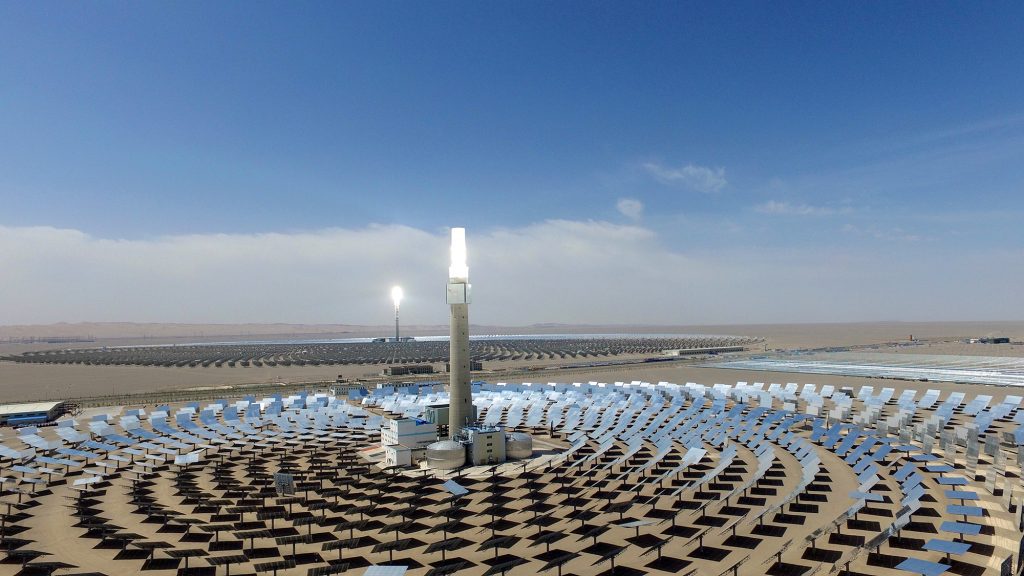
Concentrated Solar Power (CSP) plants have become a pivotal technology in the renewable energy sector, leveraging the sun’s energy to produce electricity. One of the critical components enabling the efficiency and reliability of CSP plants is the advanced valve technology used to manage molten salts, which act as both heat transfer fluids (HTF) and thermal energy storage (TES) materials. This white paper delves into the design considerations, challenges and innovations in valve technology specifically tailored for molten salt applications in CSP plants.
Thermal energy storage and molten salt applications
Thermal energy storage is a pivotal component of CSP plants, enabling them to store excess thermal energy during peak sunlight hours for use during periods when sunlight is unavailable. This capability allows CSP plants to generate electricity even at night or on cloudy days, enhancing their reliability and efficiency. Molten salts serve as both a heat transfer fluid (HTF) and a thermal energy storage material here. Their ability to store and transfer heat efficiently makes them ideal for this dual role. In addition, molten salts are used as coolants and, in some cases, as fuel in nuclear power plants, as well as electrolytes in high-temperature molten salt batteries.
Why use salt mixtures
Simple salts require substantial energy to melt and degrade faster than mixtures. To optimise their thermal properties, salts like nitrates, carbonates, fluorides and chlorides are combined in specific ratios. These mixtures achieve lower melting points, high boiling points, low vapour pressure and high thermal stability.
Few of the combination of salt mixtures and their properties are below:
Parabolic and tower-based CSP plants
CSP plants typically employ two primary designs: parabolic troughs and solar towers. Most second-generation CSP plants use nitrate salt mixtures, usually comprising 60% sodium nitrate and 40% potassium nitrate. This mixture melts at 221°C and begins to crystallise at 238°C. In the operational cycle of a CSP plant, hot salt (>400°C) is heated by solar towers or troughs and stored in hot tanks, maintaining temperatures above 500°C. Cold salt (<400°C) is preheated to remain above its freezing point and is pumped to the tower, where it is further heated and cycled back, ensuring continuous energy generation.
Advantages and challenges
- The use of molten salts in CSP plants offers numerous advantages, including high thermal stability, high density, non-flammability and low vapour pressure, making them both efficient and safe.
- However, challenges such as salt crystallisation can pose significant risks to handle the equipment’s like pumps and valves, potentially leading to higher operational costs.
- CSP has higher costs compared to other energy sources due to technological limitations, with TES efficiency at 90% but electricity transformation is only at 50%.
Valves that can be used in CSP plants
Several types of valves can be employed in CSP plants for handling steam and air, but for molten salt applications, globe control valves and triple offset butterfly valves are preferred due to their unique design construction, ensuring efficient operation and control of the molten salt flow. Here are some common types of valves used in CSP Plants:
- Gate valves: Allow unrestricted flow of molten salt in large pipelines, minimising resistance.
- Butterfly valves: Compact design suitable for controlling flow in
large pipelines, especially in space-constrained areas. - Globe valves: Enable precise regulation of molten salt flow rate, essential for optimising heat transfer.
- Check valves: Prevent backflow, ensuring molten salt moves in the intended direction only.
- Control valves: Actuator-equipped for precise control overflow, pressure and temperature.
- Pressure relief valves: Automatically release excess pressure to prevent over-pressurisation, ensuring safety.
- Thermal expansion valves: Maintain system integrity by accommodating thermal expansion and contraction of molten salt.
General requirements for valves
For valves handling molten salts, specific requirements must be met:
- Valves must have metal seating, and insulated graphite is recommended for wetted parts.
- Compliance with standards like ISO 5208/API 598/EN 13344-1 Rate-A for On-Off valves and FCI 70-2 Class V for Control valves is essential.
- Butt-weld end connections are preferred for secure sealing.
- Packing leak rates should meet ISO 15848 Rate-A standards.
- Valves should allow inline maintenance and packing replacement without actuator removal.
- Heat tracing systems are necessary for proper operation.
- Valves should withstand thermal cycles inherent in CSP operations.
- Packing and gasket materials should be selected based on valve type.
Valves must also meet plant-specific requirements, such as:
- Valves must withstand seismic loads.
- Noise and vibration should be within acceptable limits.
- Electrical equipment should be suitable for site conditions.
- Minimum design life of valves should comply to project and site-based requirements.
- Valves should endure thermal cycles of 20,000 to 25,000 cycles.
- Packing and gasket decisions should align with principal’s specifications.
- Compatibility with designated pipe schedules is necessary.
- Valves should function across a range of cold and hot salt temperatures.
- Compatibility with salt mixtures and chosen materials of construction is crucial.
- Adequate insulation thickness should be maintained.
Triple offset butterfly valve (TOBV) - Optimisation of energy consumption and compliance with EHT requirements are essential.
- Valves should undergo rigorous testing and operators should receive comprehensive training.
- Spares and special maintenance tools should be readily available.
Design considerations
Triple offset butterfly valve (TOBV)
- TOBV designs must adhere to standards like ASME B16.34, API 609 and ASME Sec VIII Div.1.
- They should feature butt-weld end connections as per ASME B16.25, metal-to-metal sealing and efficient integration with heating systems to prevent salt freezing.
- Internal fasteners must be secured against thermal turbulence, and body necks/guides designed to accommodate effective EHT systems.
- Joint sealing, stem packing and seal rings must be designed to prevent salt from contacting graphite.
- Temperature sensors should be placed in the most adverse heat locations, such as the packing, bottom gasket and body flow region.
- The body stuffing box extension should be designed based on thermal FEA, site conditions, insulation accommodation and heat supply.
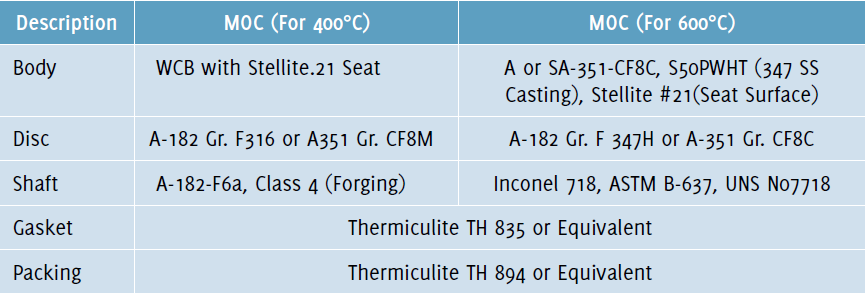
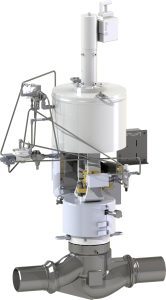
Globe control valve (GCV)
- GCV designs also follow standards such as ASME B16.34, API 623, ASME Sec VIII Div.1 etc.
- The design should prioritise preventing exposure of the packing area to hot flow to maintain the temperature within the admissible range in the stuffing box region.
- An essential consideration is the incorporation of a special packing system with an HT extended bonnet: i. For temperatures up to 400°C, materials like Garlock 1200 PBI, Garlock ThermaPUR 4122 and Zinc rings must be utilised. ii. For temperatures up to 600°C, the utilisation of Garlock Quickset 9001 1303 FEP packing materials is necessary.
Verification and validation
Thermal finite element analysis (FEA) Thermal FEA is essential for verifying valve designs. For cold salt valves, it helps identify and mitigate cold regions, while for hot salt valves, it assesses packing degradation and thermal loads. Transient thermo-structural analysis can determine thermal shock, fatigue life and creep life of valves, ensuring their reliability under CSP plant conditions.
Field validation
Testing valves under simulated CSP conditions, including thermal cycles and seal performance, provides critical insights into their real-world performance. Collaborating with industry partners and conducting on-site validation ensures design integrity and operational efficiency.
Energy saving and thermal loss in CSP plants:
Efficient heating and thermal management are vital in CSP plants. Key points include:
- Selecting heaters like tubular or ceramic-based ones optimises energy and geometry.
- Valves in cold salt lines are heated above salt’s melting point to prevent freezing, with external surfaces designed for insulation.
- Shaped heaters and precise sensor placement mitigate heat loss.
- Balancing power consumption and geometry maximizes efficiency, reducing costs and improving sustainability.
Developments and future outlook
Advancements in molten salt technologies are driving significant innovation in the valve industry, especially for Concentrated Solar Power (CSP) applications. These advancements demand valves capable of withstanding extreme temperatures, corrosive environments, and rigorous operational conditions.
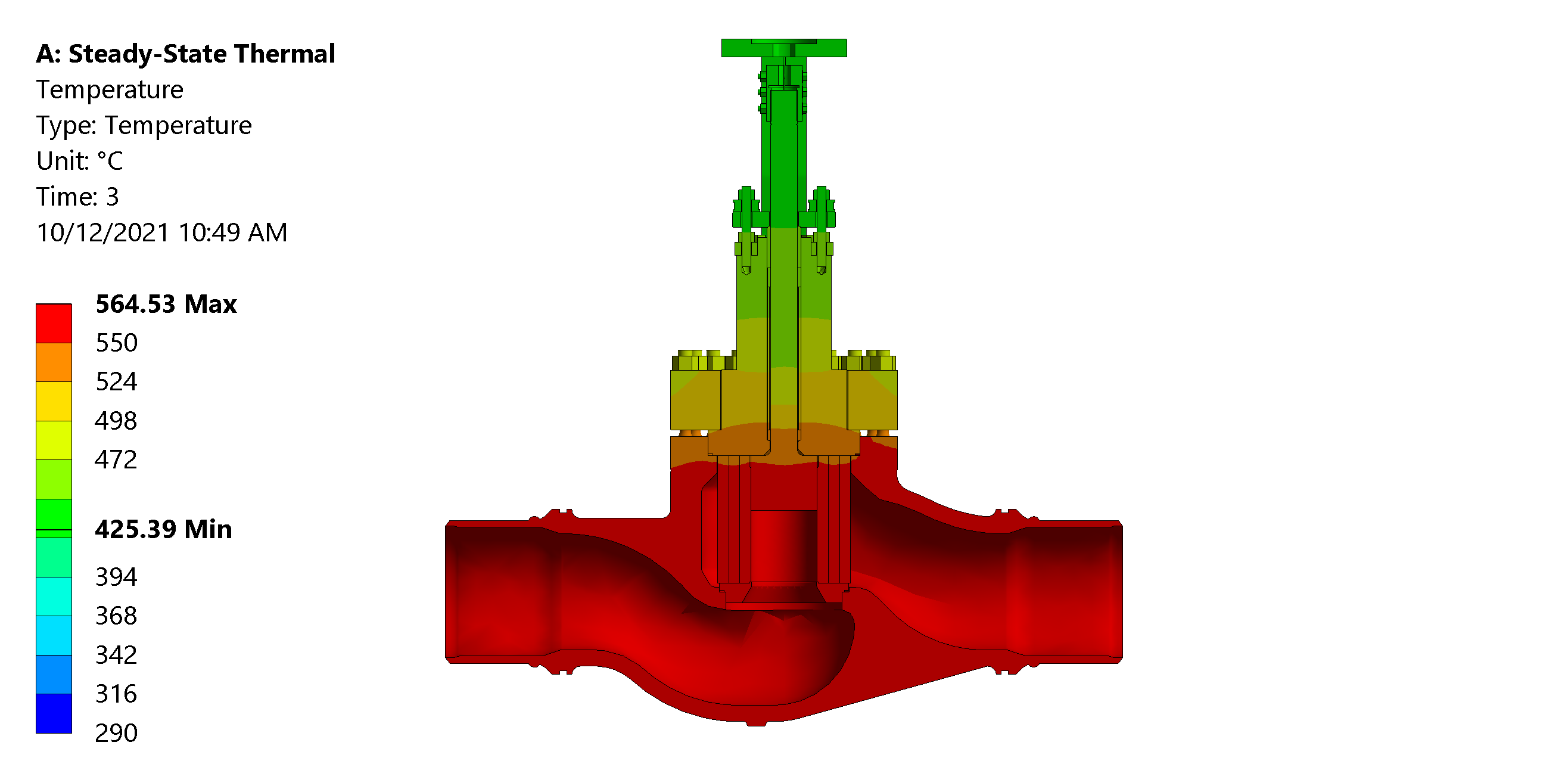
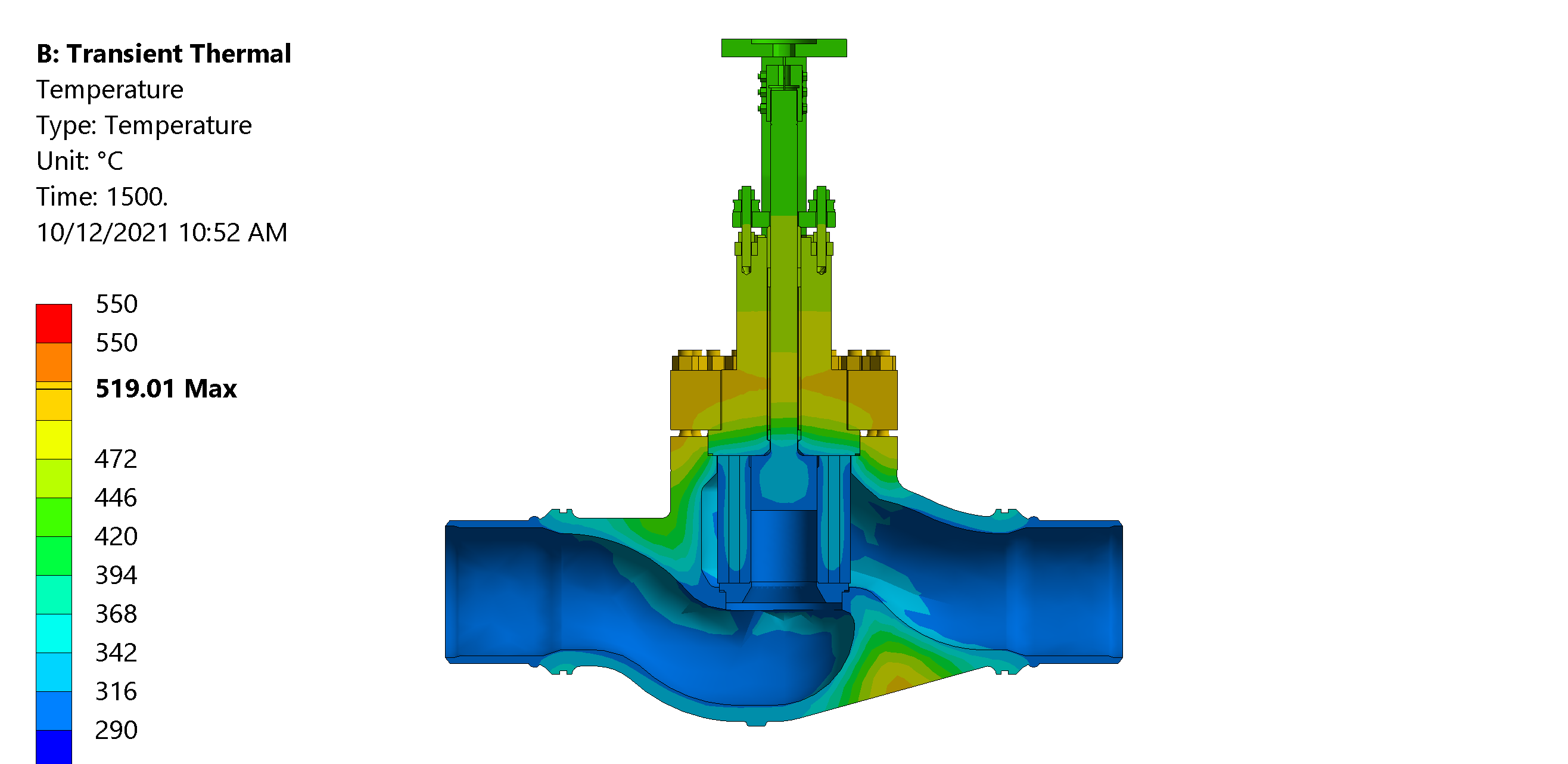
Key technologies include:
- Molten Salt Fast Reactors (MSFR)
- Fluoride Salt-Cooled High-Temperature Reactors (FHR)
- Liquid Fluoride Thorium Reactors (LFTR)
- Hybrid Sulfur Process in Integral Molten Salt Reactors (HyS IMSR)
- Generation-3 CSP (Gen-3 CSP)
- Methane pyrolysis
- Reforming
- Desalination
Each requires specialized valves designed for durability in high-temperature and corrosive environments, ensuring safety and efficiency.
The CSP market is poised for substantial growth, with its valuation expected to skyrocket from USD 28.3 billion in 2023 to USD 552.3 billion by 2034, advancing at a compound annual growth rate (CAGR) of 34.6%. The power capacity, valued at 6602 MW in 2022, is anticipated to grow at a CAGR of 5.6% from 2023 to 2030. This growth is fuelled by government incentives promoting renewable energy and increasing global investments in solar power infrastructure.
The rapidly expanding Concentrated Solar Power market offers a wealth of opportunities for valve technology innovation. As we’ve explored, the unique challenges posed by molten salt systems demand cutting- edge solutions in valve design, materials and smart technologies. By rising to these challenges, the valve industry is not merely adapting to new requirements but actively shaping the future of sustainable energy generation.
The advancements discussed – from novel materials resistant to extreme temperatures and corrosion, to sophisticated designs that ensure reliable operation in harsh conditions – underscore the critical role of valve technology in CSP efficiency and reliability. As the industry continues to evolve, these innovations will be key to unlocking the full potential of solar thermal energy, contributing significantly to a more sustainable and resilient global energy landscape.
About the authors
Krishnakumar Viswanathan is the Global Engineering Leader for butterfly valves at Flowserve. With 15 years of experience, he specialises in new product development, valve design, actuation system design and testing and evaluation of isolation and control valves. His expertise covers both rotary and linear control valves, including triple and double offset butterfly valves, globe control valves and actuators. Krishnakumar holds a Bachelor of Engineering (B.E.) degree in Mechanical Engineering.
Vignesh Murugan is an Engineer for butterfly valves at Flowserve valve division. He has 5 years of experience in valve design, specialising in the design of triple offset valves, gate, globe & check valves. Vignesh holds a Bachelor of Engineering (B.E.) degree in Mechanical Engineering.
About this Technical Story
This Technical Story is an article from our Valve World Magazine, October 2024 issue. To read other featured stories and many more articles, subscribe to our print magazine. Available in both print and digital formats. DIGITAL MAGAZINE SUBSCRIPTIONS ARE NOW FREE.
“Every week we share a new Technical Story with our Valve World community. Join us and let’s share your Technical Story on Valve World online and in print.”