Advanced valve disc and seat designs allow some high-performance butterfly valves to maintain superior sealing over a significantly extended service life.
Karin Pharr, Emerson
High-performance butterfly valves are common across a wide range of chemical and petrochemical processes. They may be manual or and significantly reduced footprint make them an excellent solution for equipment isolation applications.
While there are many types of butterfly valves available, there are significant differences in their internal design, which directly impact their sealing performance and long-term reliability. This article focuses on the key design features to help users evaluate the best alternative for their critical on/off valve applications.
Applications suited for butterfly valves
While a high-performance butterfly valve may be used in a variety of situations, they are best suited for equipment isolation and on/off applications requiring bubble-tight, zero-leakage shutoff.
These valves are generally less expensive than plug or ball valves, especially as line sizes get larger. They also take up far less space when installed, allowing them to fit in tight piping configurations, where space may be limited. While butterfly valves can be utilized for flow control, their control range is somewhat narrow, so the requirements of the application must be carefully evaluated before using these valves in throttling service.
There are a multitude of high-performance butterfly valve body and sealing designs, but the overall performance and long-term reliability varies significantly among models. When choosing a valve, it is important to understand the differences to select the right valve for a particular application and budget.
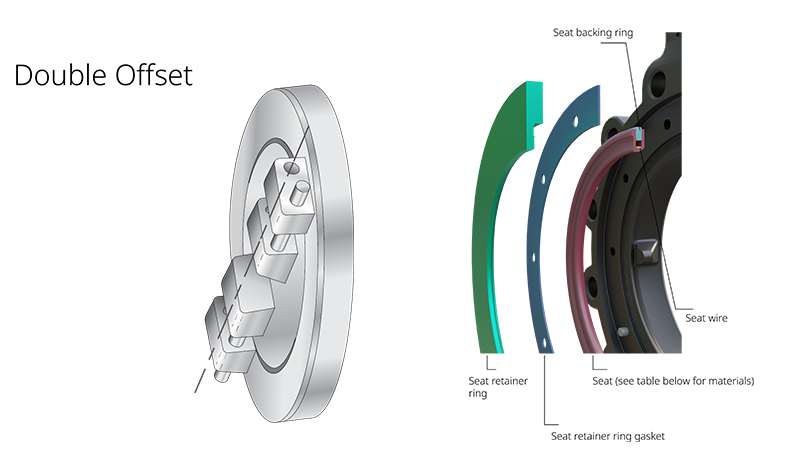
Valve sealing and packing design alternatives
When evaluating a high-performance butterfly valve, users should start with the disc and seat design. Some butterfly valves wedge the disc into a soft seat and rely on process pressure to provide reliable shutoff. Such valve designs only work with pressure on a particular side of the valve and will perform poorly in bi-directional applications. Other valves utilize seat designs that continuously wear as the valve moves, creating leakage after a short time in service, and eventually causing premature failure of the seat.
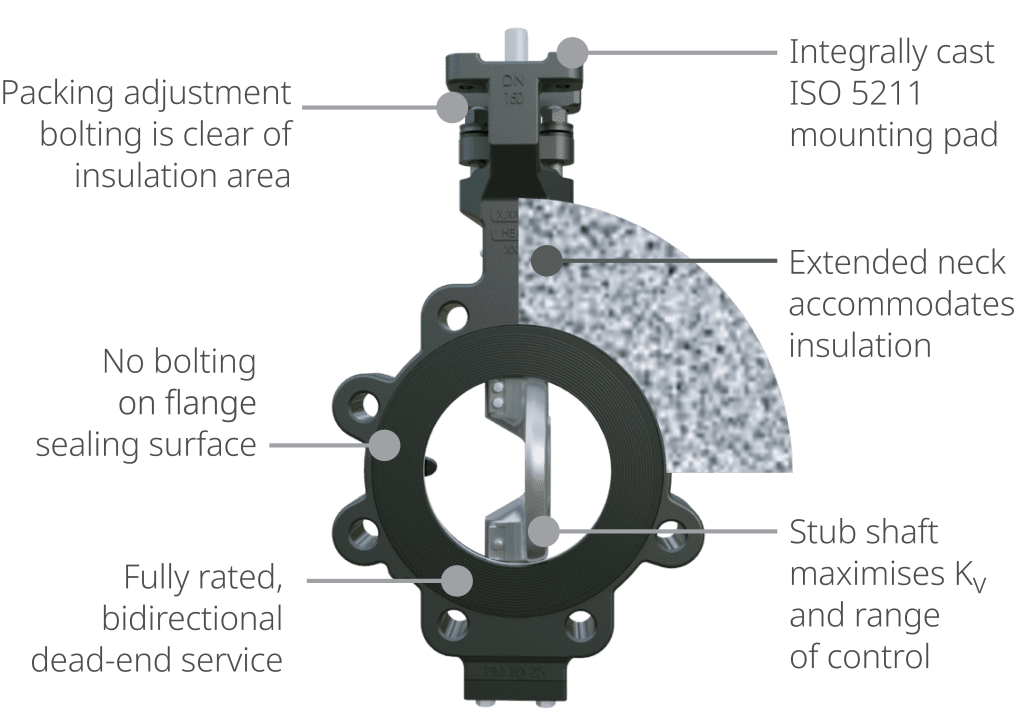
Better valve designs utilize a double offset design that allows the disc to wedge tightly into the seat at the end of travel, yet lift quickly off the seat after only a few degrees of travel to limit wear (see Figure 1). Such designs offer zero-leakage, bubble-tight sealing due to the double offset camming motion, and they can maintain that level of performance over an extended life since the seat is only engaged in the final degree of movement. The double cam design also operates independent of system pressure, so the valve provides zero leakage regardless of system pressure.
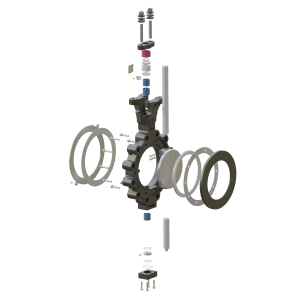
It can also operate with pressure on either side of the disc, and it can even seal when installed on the end of a pipe with one side exposed to atmosphere. A double offset design does offer advantages, but the valve life is significantly increased when that design is combined with a self-adjusting seal composed of very long wear materials, backing rings for support, and specially designed seal rings that incorporates engineered wires and gaps to allow the seal to self-adjust with each stroke. Such a design enables the valve to maintain zero-leakage performance over many more valve cycles, and it greatly extends valve life to reduce lifecycle cost Another key feature of these types of valves is the packing arrangement. The latest environmental standards require many valves to achieve and maintain very low levels of packing emissions. Historically, this level of packing performance required a highly compressed packing, which accelerates wear of both the packing and stem, while hampering valve movement. This limitation can be overcome by utilizing live-loaded packing washers and advanced sealing ring material combinations suited for a broad range of pressures and temperatures. The self-lubricating nature of these rings, along with a high-hardness valve stem, provide ease of movement. The live-loaded, high-compression packing maintains extremely low levels of packing emissions over many valve cycles, and the packing compression can be adjusted to further extend valve life.
Valve body design
While the valve seat and packing designs are critical, a design with installation and maintenance in mind is also important. The valve should come with standard face-to -face valve dimensions, provide an extended stem to allow the packing to be adjusted even when the valve is insulated, and provide an integral, standard actuator mounting base that accepts most actuators without requiring coupling or additional brackets (see Figure 2). Another key feature is a stem/disc design that maximizes flow capacity. Many high-performance butterfly valves have a thick shaft that passes through the flow path, obstructing flow and increasing pressure drop. Better designs reduce the profile of the disc/shaft combination, allowing a valve of equal size to pass more flow with less pressure drop.
Maintenance friendly
While a top-tier high performance butterfly valve will last for years, at some point seat and packing wear are inevitable, so it is important that the valve be designed to easily replace and repair these components. Therefore, the valve should be specifically engineered to allow replacement of both the seat and packing materials without disassembling the valve stem and disc (see Figure 3). Though repairs should be infrequent and maintenance costs low, lifecycle costs will be further reduced if the packing and seats can be easily and quickly replaced.
Key take aways
The small form factor, low cost, and superior sealing capability of high-performance butterfly valves make them an excellent solution for equipment isolation and on/off applications. However, a wise user will carefully evaluate the details of high-performance valve designs.
Features such as double offset sealing, advanced disc seat designs, and low emission packing can extend valve life significantly. Advanced sealing techniques operate independent of process pressure and maintain zero leakage in bidirectional and even dead-end pipe applications. When maintenance is eventually required, top tier valves are designed to facilitate easy and quick repairs with minimum disassembly. If a project requires reliable and zero leakage isolation, consider the advantages of well-designed high-performance butterfly valves. The initial savings can be significant when compared to plug or ball valve equivalents, and the extended life and ease of maintenance provide long-term lifecycle cost savings as well.
About the author
Karin Pharr is the global product manager for high performance butterfly valves at Emerson. She is responsible for portfolio management, pricing, marketing, and strategic program execution across the Keystone™ High Performance Butterfly Valve portfolio. Before product management, Pharr held multiple positions across engineering, information technology, and business process. She holds a Bachelor of Science degree in Nuclear Engineering from Texas A&M University.
About this Technical Story
This Technical Story is an article from our Valve World Magazine, November 2024 issue. To read other featured stories and many more articles, subscribe to our print magazine. Available in both print and digital formats. DIGITAL MAGAZINE SUBSCRIPTIONS ARE NOW FREE.
“Every week we share a new Technical Story with our Valve World community. Join us and let’s share your Technical Story on Valve World online and in print.”