Explore the critical role of equipment selection in cryogenic operations, from vacuum-jacketed valves to ISO tanks. Learn how proper choices can overcome challenges in safety, efficiency and cost-effectiveness across industries such as aerospace, medical and industrial manufacturing.
By Chris Herman
The word “cryogenics” has its roots in Ancient Greece, where “kryos” meant “cold” or “frost”. However, it wasn’t until the late 1880s that the term became mainstream in science and technology, with the first cryogenic laboratory constructed in 1882 in The Netherlands.
Today, the widely accepted starting point for cryogenic temperatures is -292°F (-180°C), as the boiling point of many permanent gases like helium, hydrogen, neon, nitrogen and oxygen are below this temperature.
The challenge
Over the centuries, humankind has discovered abundant benefits and uses for low temperatures. In the cryogenic realm, this is best represented by the discovery that the production of lower and lower temperatures through the liquefaction of ambient gases could have many far-reaching positive benefits for countless technologies and industries.
There are seven general benefits attributed to the ability to produce and use cryogenic substances:
-
An outside industrial unit with tanks and vaporizers Preservation of biological food and material
- Reduced thermal noise
- Creation of high fluid densities through gas liquefaction and separation
- Low vapour pressures
- Achieving temporary or permanent property changes
- Creation of superconductive or superfluid substances
- Mandatory tissue destruction
However, cryogenic manufacturers must overcome several challenges:
- Ensuring safety when handling substances at excessively low temperatures
- Maintaining cryogenic liquids in a frigid-liquid state
- Managing heat sources that can cause unwanted “boil off”
- Increased power requirements and associated costs
- Large, complicated and expensive production facilities
- Noise, vibration and electromagnetic interference
- Heat rejection
- Finding suitable materials for construction
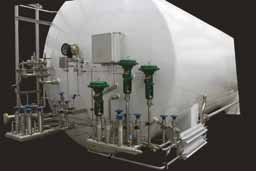
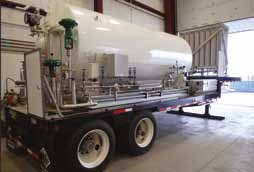
The solution
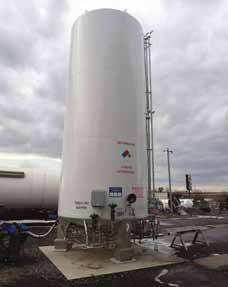
No matter the operational atmosphere, temperature range or cryogenic substance being handled, the systems and equipment used need to be able to satisfy the inherent challenges of handling cryogenic substances.
The roster of equipment and systems that can be incorporated in a cryogenic-manufacturing regime or be required to operate at cryogenic temperatures includes:
- Vacuum-jacketed valves: These valves must conform to stringent regulatory standards to ensure reliable flow control and preservation of cryogenic temperatures. They utilise a vacuumed annular space between the process flow path and the outside wall to make convection to the environment negligible.
- Vacuum-jacketed piping (VJP): VJP systems are engineered to handle a wide spectrum of cryogenic substances. A properly designed VJP system will effectively mitigate convection-heat leaks, enhancing operational efficiency and minimising costs.
-
The installation of a vaporizer on a tank Air separation units (ASU): ASUs separate atmospheric air into its primary components: nitrogen, oxygen and argon. They operate at cryogenic temperatures and high pressures, ensuring a steady supply of high-purity gases essential for a wide range of industrial processes.
- Liquid cylinders: These specialised containers are designed to store and transport cryogenic liquids. They come in various sizes, capacities and pressures to meet diverse needs, providing a convenient and efficient means of delivering cryogenic liquids to various end-users.
- Liquid delivery systems: These systems store industrial gases in their liquid state and are equipped with advanced insulation, safety features, flow-control devices, pressure regulators and monitoring systems to ensure accurate and consistent delivery.
- ISO tanks: ISO tanks are specialised containers used for the transportation of liquefied industrial gases, such as LNG. They conform to stringent safety standards and regulations, ensuring the reliable and safe distribution of these essential resources.
- Liquid cylinder filling stations: These dedicated facilities are equipped with specialised equipment and safety measures to ensure the efficient and safe transfer of cryogenic liquids from bulk storage tanks to individual liquid cylinders.
Conclusion
From its humble beginnings in Ancient Greece to its indispensable use in the construction and deployment of systems and equipment that help send rockets and humans into outer space, it’s hard to argue that “kryos” and its close cousin “cryogenics” has not been one of the spoken word’s greatest contributions. However, cryogenics can only continue to be a contributor to the advancement of humankind if the substances that fall within its definition are produced, handled, transported, stored and dispensed safely, efficiently and reliably. That requires the use of equipment and systems that are able to take the sting out of the characteristics that can make handling cryogenic substances so challenging.
About the author
Chris Herman is the Senior Product Planning & Business Development Manager for OPW Clean Energy Solutions and RegO® Products. He can be reached at chris. herman@regoproducts.com. OPW Clean Energy Solutions, formed in 2021, specialises in cryogenic and industrial gas equipment. For more information on OPW, please visit opwces.com.
Dive Deeper into Valve World
Enjoyed this featured article? There’s much more to discover! Subscribe to Valve World Magazine and gain access to:
- Advanced industry insights
- Expert analysis and case studies
- Exclusive interviews with valve innovators
Available in print and digital formats.
Breaking news: Digital subscriptions now FREE!
Join our thriving community of valve professionals. Have a story to share? Your expertise could be featured next – online and in print.
“Every week we share a new Featured Story with our Valve World community. Join us and let’s share your Featured Story on Valve World online and in print.”