Discover how a comprehensive strategy for valve repair, remanufacturing, and rigorous testing can extend operational lifespan and enhance reliability in oil and gas plant facilities.
By Irawan Josodipuro
In the demanding environment of oil and gas operations, valve performance is crucial for maintaining safety, efficiency, and productivity. This article explores a comprehensive approach to valve management, focusing on repair, testing and maintenance strategies that can significantly extend valve lifespan and reliability.
Valve management strategies
When managing valves in oil and gas operations, operators typically consider three main approaches:
- New valve procurement
- Maintaining valve stock
- Valve repair and maintenance
Each approach has its advantages and challenges. New valve procurement ensures high quality but often involves long waiting times. Keeping a stock of valves eliminates delays but can be expensive and requires careful storage. Valve repair and maintenance, when done correctly, offers a balance of quick solutions, cost-effectiveness and reliability. For many operators, a well-executed valve repair and maintenance program emerges as the most efficient solution to ensure continuous operation and safety in oil and gas facilities.
Common valve issues
In oil and gas operations, valves frequently face four main types of damage:
- External corrosion: This often affects exposed parts such as flanges. It’s a significant concern due to the harsh operating environments and the critical nature of the equipment involved.
- Internal corrosion: This commonly occurs on internal parts, such as the seat ring, in upstream oil and gas operations.
- Valve sealing failure: This can result from various factors including non-compatible operating conditions, rapid decompression, erosion, improper material selection, improper installation and inadequate maintenance.
- Erosion of internal valve parts: This is a common issue in the oil and gas sector due to particulate matter or solid objects in the fluid, as well as high velocity flow.
All these problems can significantly affect valve performance, leading to leaks, reduced efficiency and potential safety hazards.
Methodology and process
The valve repair and maintenance process, from an oil and gas operator’s perspective, consists of six key steps:
- Dismantling, delivery and receiving:
- The valve is dismantled from its operational location, delivered to the maintenance facility and received for further processing.
- Disassembly, cleaning:
- The valve is disassembled into its component parts and each part is thoroughly cleaned to remove contaminants or residues.
- Evaluation:
- Detailed assessment and failure investigation of the valve’s condition to determine the extent of wear and tear, damage, or any other issues that need to be addressed.
- Repair/remanufacture:
Damaged or worn-out parts are either fixed or replaced. This step may include reverse engineering.
What is the difference between remanufacturing and repair?
i. Comprehensive vs. basic: Remanufacturing restores the valve to like-new condition, whereas repair focuses on basic maintenance to restore functionality.
ii. Inclusion of manufacturing operations: Remanufacturing includes machining, welding, heat-treating and other manufacturing operations. Repair does not include these processes.
iii. Extent of part replacement: Both processes exclude valve body replacement, but remanufacturing allows for a broader scope of part restoration and replacement.
iv. Outcome: Remanufacturing results in a valve with an extended lifespan and potentially improved performance, while Outcome: Remanufacturing results in a valve with an extended lifespan and potentially improved performance, while
Reverse engineering: This is a crucial part of the repair/remanufacture step. When parts need to be recreated or improved, reverse engineering techniques are employed to ensure the valve meets or exceeds original specifications. In fact, reverse engineering capability is one of the most important aspects of reliable valve repair and remanufacturing. This engineering process involves deconstructing, evaluating and replicating parts without access to design files or original specifications. It can reproduce another manufacturer’s product or that of an OEM (Original Equipment Manufacturer) following a detailed examination of its construction or composition.
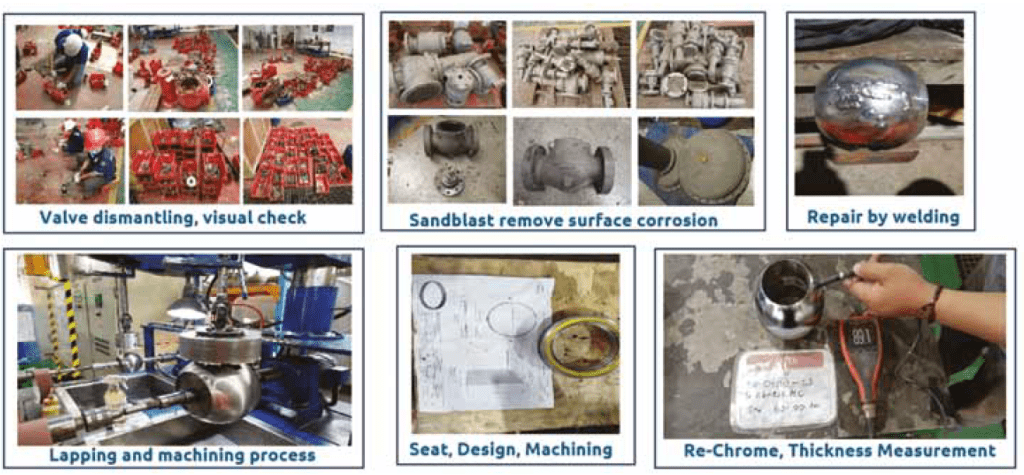
Reverse engineering becomes particularly valuable when:
- Engineered valve parts are out of stock from major manufacturers
- Parts are no longer in production
- Parts are unknown or difficult to find
A single valve failure could result in significant delays and costly downtime. Reverse engineering provides a solution by creating a newly rebuilt system and restoring its functionality.
5. Reassembly, testing, marking, documentation:
- The repaired valve is returned to its operational location, reinstalled and put back into service. Ongoing field maintenance is conducted to ensure continued reliable operation.
- After repairs, the valve is reassembled and undergoes rigorous testing to ensure it meets required specifications. Proper marking and documentation of the maintenance performed are completed.
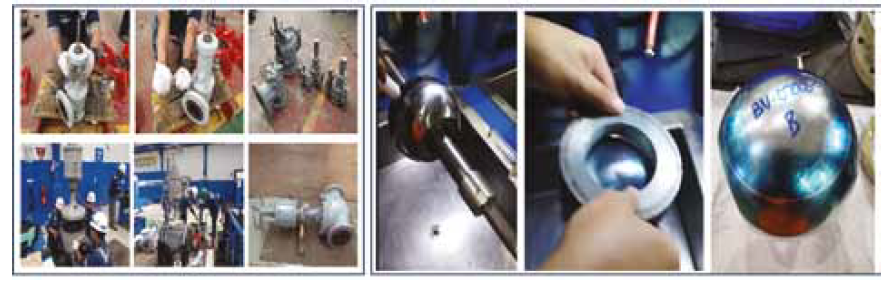
The reassembly of newly refurbished components with the existing valve structure is a critical phase, demanding precision and attention to detail.
To ensure compliance with valve repair and testing requirements, it’s essential to adhere to established standards such as API 598, API 6D and specific end user specifications. The comprehensive testing protocol includes:
- Conventional leak and pressure tests
- Additional performance tests
- Functional tests
- Safety tests
These additional measures are crucial to guaranteeing the integrity of safety features in the repaired valves, ensuring that they not only meet but surpass operational standards.
6. Return delivery, installation and field maintenance:
The repaired valve is returned to its operational location, reinstalled and put back into service. Ongoing field maintenance is conducted to ensure continued reliable operation.
- Field maintenance: Valve maintenance is critical for both repaired and new valves to ensure reliable operation and prevent costly failures in industrial settings. This is especially important in sectors like oil and gas, where valves play a crucial role in controlling fluid flow and maintaining safety.
Key aspects of effective valve maintenance include:
- Regular greasing: Proper lubrication helps prevent friction, wear and corrosion on moving parts of the valve. This extends the valve’s lifespan and ensures smooth operation. Regular greasing intervals should be defined based on operational conditions and manufacturer recommendations.
- Open-close operational checks: Regularly exercising valves through open-close cycles helps verify their functionality and identify any operational issues such as sticking or jamming. This also helps prevent valves from seizing due to prolonged periods of inactivity.
- Continuous improvement of maintenance checklists: Learning from past maintenance experiences and feedback, continuously improve maintenance checklists. Include specific checks based on valve type, application, and criticality. Ensure these checklists are comprehensive and aligned with industry standards and best practices.
- Condition monitoring: Implementing condition monitoring techniques such as vibration analysis, temperature monitoring and leakage detection can help detect early signs of valve degradation or malfunction, allowing for proactive maintenance.
- Training and competence: Ensure maintenance personnel are adequately trained and competent to perform maintenance tasks effectively and safely. Provide ongoing training to keep them updated on new technologies and best practices in valve maintenance.
- Valve condition inspection database: Developing a valve condition inspection database is an excellent approach to systematically tracking maintenance activities, monitoring performance and enhancing future programs based on data-driven insights.
By focusing on these aspects, industries can enhance the reliability, efficiency and safety of valve operations, thereby minimising downtime and maximising productivity.
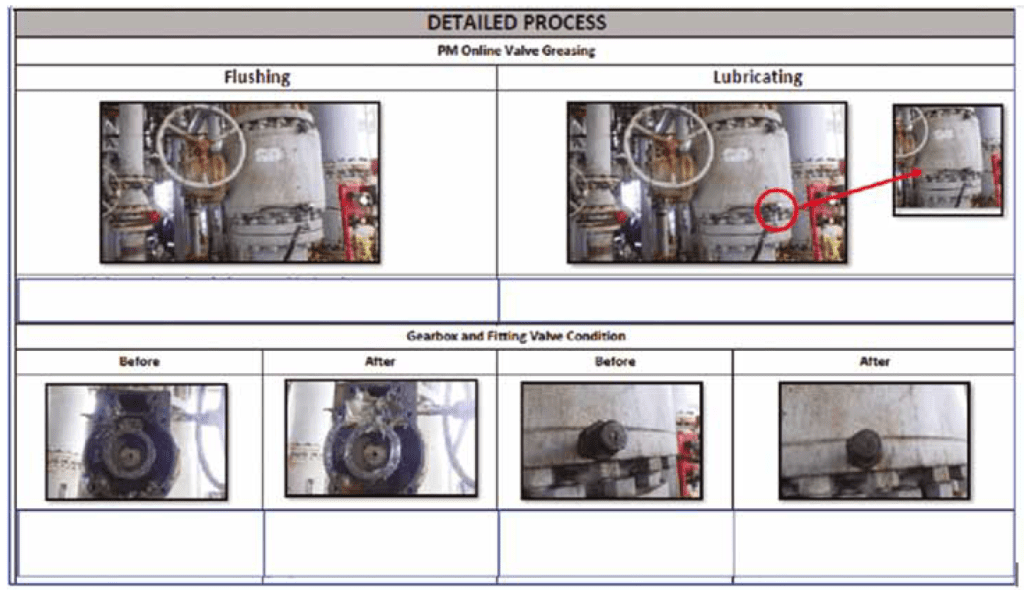
Quality and reliability
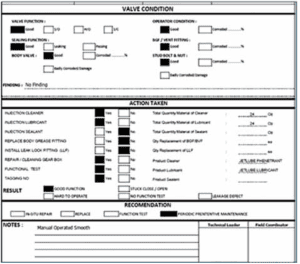
Three important aspects to ensure the quality and reliability of replacement parts are design engineering, material requirements, and inspection and testing. For example, the replacement of metallic seat rings with new inserts requires the minimum design demonstration that the seat ring is manufactured from the material with equivalent performance to the original, including the dimensional tolerances and profiles. The material needs to be backed up with traceability evidence, such as a material certificate, and evidence that the material truly comes from the qualified manufacturer with all properties verified.
The inspection and test should be performed in conjunction with the seat performance test, including after the valves stroke several times under full differential pressure to ensure the stability of the seat ring and its insert. The cavity relief functionality needs to be demonstrated if required. For sealing elastomers, the minimum design of calculations for fill, squeeze and extrusion must be verified including the surface finish of its contact surface. The traceability of the material and the test report must be truly representative and supplied by qualified manufacturers. The inspection and test shall be performed with performance testing.
By adhering to these aspects, the quality of replacement parts can be ensured, maintaining the integrity and safety of the overall system. The know-how of reverse engineering, along with appropriate facilities and thorough inspection, is crucial for ensuring the reliability of repaired valves.
Guidelines and procedures
To ensure the quality of the valve repair process, it’s crucial to develop detailed and robust procedures that supplement standard codes and specifications. In the context of upstream oil and gas operations, key industry guidelines include:
- The American Petroleum Institute (API) 6D 25th edition, which includes specific requirements for valve repair and remanufacture.
- API RP 621, which provides guidance for reconditioning metallic globe, gate and check valves.
These standards offer essential frameworks for maintaining quality and consistency in valve repair and maintenance processes.
Key takeaways to ensure valve reliability
Valve repair demands a comprehensive approach to meet quality requirements, contributing to operational efficiency and safety in industrial operations. This approach begins with selecting capable and trustworthy vendors or workshops, a crucial step in ensuring high-quality repairs and avoiding issues such as conflicts of interest and workmanship problems.
The valve repair process must be qualified, tested and supervised by the client to maintain quality and compliance with industry standards. Integrating these elements enhances confidence in the repaired valves’ reliability, longevity and adherence to regulatory standards, fostering transparency and accountability between service providers and clients.
Attention to best practices, such as the inclusion of grease injection ports, is vital for maintaining valve longevity and performance. These features ensure that lubrication reaches critical areas, preventing wear and ensuring smooth operation over time. Properly integrating and testing these ports can significantly enhance equipment reliability and lifespan.
By embracing these principles and practices, industry professionals can improve the outcomes of valve repair and maintenance efforts, leading to more reliable, efficient and safe operations in demanding industrial environments.
Reference
“Optimizing Valve Performance: A Holistic Approach through Comprehensive Repair and Rigorous Testing for Oil and Gas Plant”, presentation Valve World Asia Conference 2024: Irawan Josodipuro, Richard B. Napitupulu, Kelvin O. Djohan
About the author
Irawan Josodipuro is an accomplished subject matter expert with over three decades of experience in piping, valves, pressure vessels and mechanical static systems. He holds a master’s degree in mechanical engineering from Stanford University and numerous professional certifications. Throughout his career, Irawan has led major international and national oil and gas projects, collaborating with major companies and regulatory authorities. His innovative contributions have earned him prestigious accolades, including the “SatyaLancana Wira Karya” from the President of Republic Indonesia as well as recognition from global institutions. A prolific speaker and author, Irawan is an active member of several international organisations and serves on the steering committee for the Valve World Asia and Valve World Southeast Asia Conferences.
About this Technical Story
This Technical Story is an article from our Valve World Magazine, October 2024 issue. To read other featured stories and many more articles, subscribe to our print magazine. Available in both print and digital formats. DIGITAL MAGAZINE SUBSCRIPTIONS ARE NOW FREE.
“Every week we share a new Technical Story with our Valve World community. Join us and let’s share your Technical Story on Valve World online and in print.”