Design and casting methodology are of significant importance for valve quality and lifespan. In the development and production of valves used in the oil and gas industry, such as API6D Ball Valves, these methodologies positively influence the process of developing applications including static, flow and casting analysis whilst ensuring the validation and reliability of the products.
By Burak Bozkara, Gedik
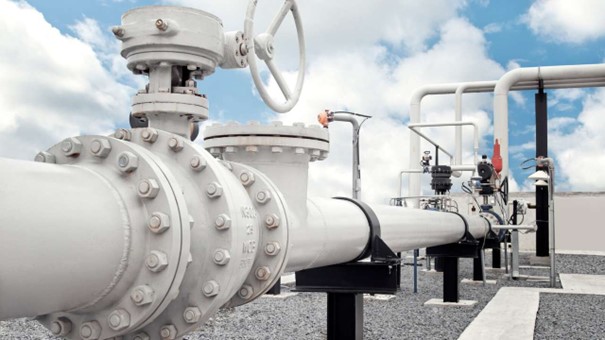
Valves are used across various industries, including oil, natural gas, chemicals, marine and others, to ensure safe flow control. Different types of valves have been developed based on the pipelines they are used in, the properties of the fluids and environmental conditions.
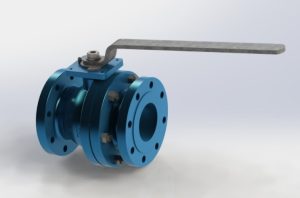
Producing and validating these valves in accordance with international standards and regulations is crucial for meeting both production and environmental requirements, as well as ensuring user safety. The API6D standard, established by the American Petroleum Institute, specifies the requirements for pipelines and the valves used in them. Valves used in oil and natural gas pipelines must be manufactured to meet all requirements, considering both the chemical properties of the fluids and their economic values.
This article aims to describe the advanced engineering work involved in the design and production development stages of API6D compliant ball valves, which are designed, produced and tested within our company. It also explains the casting defects encountered during the production phase and the improvements made in the casting methodology.
Valve design process
Valves, depending on the sector in which they are used, may be exposed to conditions such as high pressure, corrosive environments, high temperatures and more. Therefore, valves must be designed and manufactured considering these conditions. Due to the challenging operating conditions and complex geometries, some valves are produced using casting methods. The difficulties and limitations inherent to the casting process, as well as international standards, customer requirements and operating conditions, must be taken into account during the design phase.
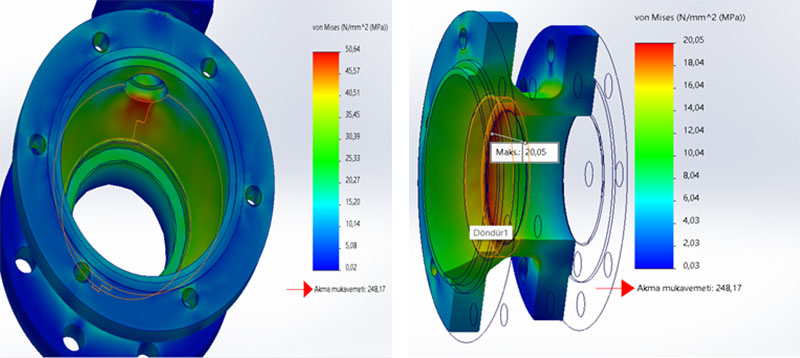
The ball valves developed in this study have been designed to meet the requirements of the API6D design standard and other referenced standards such as ASME B16.10, ASME B16.5 and ASME B16.34.
During the design process, the mechanical properties of ASTM A216 Gr. WCB quality cast carbon steel, which was chosen as the body material, were tested through tensile and hardness tests. Design calculations and analysis work were carried out based on these data. Static analyses were performed on components exposed to pressure, such as the body, sphere and bonnet part, to examine the loads and deformations experienced by these parts. Based on the results obtained, it was determined that the loads applied to the components are below the material’s yield strength, indicating that the design is highly suitable in terms of pressure. Static analysis simulations were set to 1.5 times the valve’s working pressure (19.6 Bar), which corresponds to 29.4~30 Bar, as specified in the standards. Design calculations have been performed in accordance with the requirements specified in API6D and ASME B16.34 standards. The data obtained from these calculations align with the results of static analysis simulations conducted on the computer. As a result of these efforts, the design has been theoretically validated and a valve design has been developed that ensures maximum efficiency under operational conditions. All work performed at this stage was documented, resulting in the creation of a design package.
After completing the final design work, the model production process for the body and bonnet parts to be manufactured using the casting method was initiated. In this process, model data was created with machining and shrinkage allowances provided according to the EN 8062-3 standard requirements. To maintain maximum production efficiency during the design phase, the amount of machined surfaces was kept to a minimum. However, this process was carried out in a manner that did not adversely affect product quality in accordance with the standard requirements.
Casting method development studies
Casting simulations have been conducted to prevent defects such as shrinkage and gas porosity, as well as negative effects like internal stresses, in the body and bonnet parts to be produced using sand casting methods. In addition to these simulations, feeder and feeder distance calculations were completed to maintain a productive Net/Brute ratio and ensure high-quality casting. Solidification gradients and molten steel filling simulations were performed using Novacast. Feeder and runner designs were optimised based on these simulations, leading to the development of an optimal casting method.
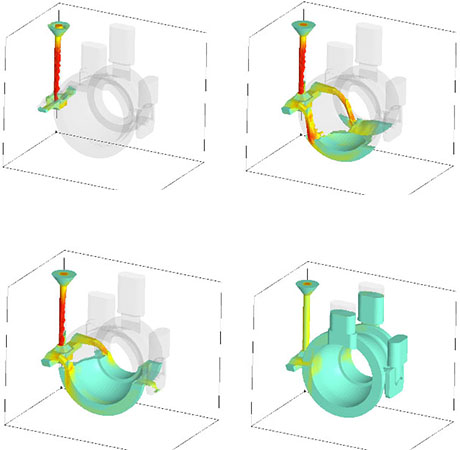
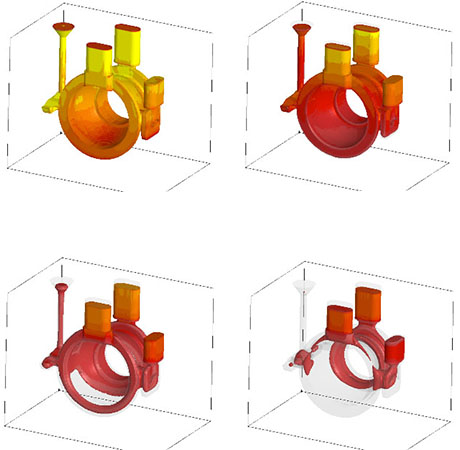
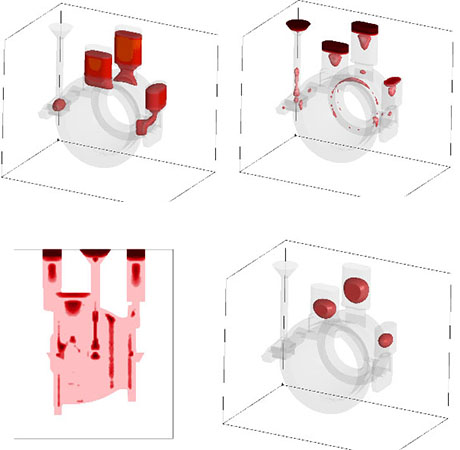
Improvements were made to the design based on casting simulations to ensure directional solidification and minimise the likelihood of hot spots. All simulation work was meticulously documented and included in the design package.
Additionally, casting method forms were created and documented to define feeders, sand mixtures and cooling systems, aiming to prevent confusion during the production phase.
The goal of these efforts is to achieve high-quality production with low scrap rates using the developed model and casting method. Prior to the casting simulation and calculation studies, hot spots and shrinkage cavities were observed in the regions indicated in the visuals of the cast parts. Non-Destructive Testing (NDT) was performed on the cast parts before the simulation, and the discrepancies identified in the simulation were concretely detected. Shrinkage cavities occurred in areas distant from feeders and where the module height was high. Additionally, due to turbulence during the filling of the mould, gas cavities were observed at various points on the parts. All these discontinuities were detected through liquid penetrant tests and radiographic inspections performed as part of the NDT work. The relevant areas of the parts were sectioned to confirm these discrepancies. Below, images of the parts, which were examined using carbon-electron microscopy after the NDT tests, are shared.
As a result of the NDT and simulation studies, new model data were generated, addressing issues such as directional solidification that could create defects. Following the creation of the new data, errors such as shrinkage and gas cavities in the cast parts were resolved.
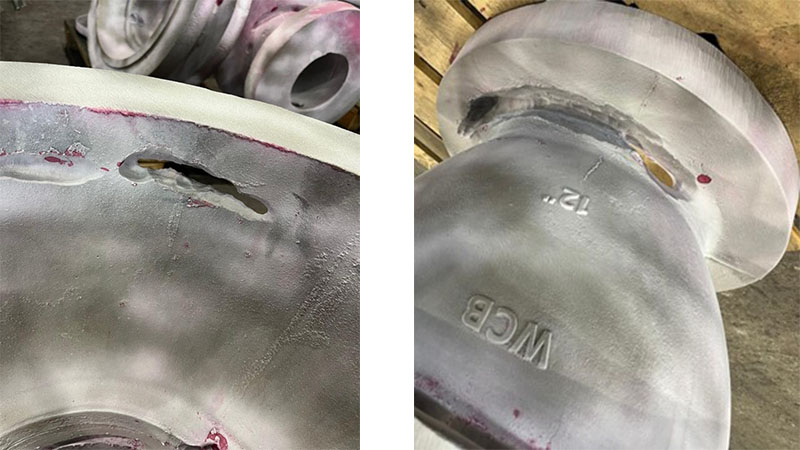
Testing and validation process
After completing the casting, machining and assembly phases, the valves must be tested to ensure they meet the relevant standard requirements. According to the API6D design standard requirements, valves must undergo pressure and leak tests. The prototype valves developed successfully passed pressure and leak tests conducted at 1.5 times the working pressure (19.6 Bar), which is approximately 29.4~30 Bar. The theoretically calculated opening and closing torque values were also measured and verified during the design calculation phase. In addition to the tests performed on the valve itself, tensile tests, chemical analyses, hardness tests and other tests were conducted on the subcomponents used in the valve assembly to ensure that all standard requirements were met.

Conclusion
This study aimed to explain the contributions of advanced computer-aided engineering applications and the positive effects of modern product development processes, in addition to traditional product development techniques. Design and casting method calculations were validated using simulation programs to create the most suitable design and production method. Data obtained from calculations and simulations were concretely tested and validated after prototype production. As a result of these efforts, high-quality and long-lasting API6D ball valves have been developed, fully meeting standards, market and customer requirements.
Developments and future outlook
Advancements in molten salt technologies are driving significant innovation in the valve industry, especially for Concentrated Solar Power (CSP) applications. These advancements demand valves capable of withstanding extreme temperatures, corrosive environments, and rigorous operational conditions.
About the author
Burak Bozkara is an R&D Engineer at Gedik Termo Valve, where he applies his expertise in the valve and casting industry. With a background in Mechatronics Engineering, Burak has been actively involved in critical processes such as the Production Part Approval Process (PPAP), Design Failure Mode Effect Analysis (D-FMEA), valve design, and the simulation of designs.
About this Technical Story
This Technical Story is an article from our Valve World Magazine, October 2024 issue. To read other featured stories and many more articles, subscribe to our print magazine. Available in both print and digital formats. DIGITAL MAGAZINE SUBSCRIPTIONS ARE NOW FREE.
“Every week we share a new Technical Story with our Valve World community. Join us and let’s share your Technical Story on Valve World online and in print.”