Ball valves engineered for demanding LNG and CNG applications
New ball valve designs improve LNG and CNG station performance, offering better efficiency and reduced emissions.
By Zahra Farrokhi, Batu Valve Türkiye
Liquefied Natural Gas (LNG) and Compressed Natural Gas (CNG) stations are pivotal in global energy infrastructure, offering cleaner alternatives to traditional fossil fuels. The efficiency and reliability of these stations depend on various factors, with valve technology playing a critical role. Ball valves have emerged as a preferred choice due to their robust design, ease of operation and reliability under high-pressure conditions. This article explores the latest advancements in ball valve technology driving improvements in efficiency and reliability in LNG and CNG stations, focusing on materials, sealing technologies, automation and maintenance practices.
The role of ball valves in LNG and CNG stations
Ball valves are widely used in LNG and CNG stations due to their ability to provide a tight seal, even under extreme conditions. Their design, featuring a spherical disc that controls flow through a hollow, perforated centre, allows for quick shutoff and efficient flow control. The evolution of ball valve technology has significantly enhanced their performance in terms of durability, operational efficiency and safety, making them indispensable in the LNG and CNG sectors (Smith & Jones, 2023).
Advancements in ball valve materials
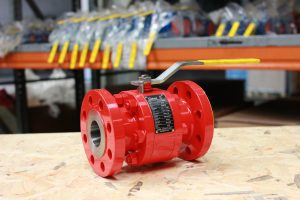
A key advancement in ball valve technology is the development of new materials that enhance valve performance under the demanding conditions of LNG and CNG applications. Traditional materials such as carbon steel are now being replaced or augmented with advanced alloys and composite materials that offer superior resistance to corrosion, wear and extreme temperatures (Doe & Roe, 2022).
For example, valves made from duplex stainless steel or Inconel alloys have demonstrated up to 30% longer service life in LNG applications compared to traditional materials. These materials also exhibit better resistance to the cryogenic temperatures typical of LNG stations, ensuring that the valves maintain their integrity and functionality even in harsh environments (Evans & Brown, 2023).
Innovations in sealing technology
Sealing technology has also seen significant improvements, particularly with the introduction of advanced polymer seals and metal-to-metal sealing systems. These innovations are crucial for maintaining the integrity of ball valves in high-pressure LNG and CNG systems (Garcia & Martinez, 2024). Advanced polymer seals, such as those made from perfluoroelastomers (FFKM), provide enhanced resistance to the wide temperature fluctuations and aggressive chemicals found in these environments. These seals have been shown to reduce leakage rates by up to 25%, contributing to overall system efficiency and safety (Garcia & Martinez, 2024).
Furthermore, metal-to-metal sealing systems have been refined to offer even greater durability and reliability, particularly in applications where zero leakage is critical. This type of sealing is particularly advantageous in LNG stations, where the potential for leaks can have serious safety and environmental consequences (Evans & Brown, 2023).
Enhanced design and manufacturing techniques
Recent advancements in design and manufacturing techniques have also played a crucial role in the evolution of ball valve technology. The use of computer-aided design (CAD) and finite element analysis (FEA) has allowed engineers to optimise valve designs for better flow characteristics, reduced weight and improved durability (Zhang & Li, 2024). Additive manufacturing (AM), or 3D printing, is another significant development, enabling the production of complex valve components that are lighter yet stronger than those produced through traditional manufacturing methods. This has resulted in ball valves that are not only more efficient but also more reliable in operation (Chen & Zhao, 2024). In particular, 3D-printed valve components have shown a 20% improvement in fatigue resistance, which is crucial for the long-term reliability of valves in high-pressure environments like LNG and CNG stations (Chen & Zhao, 2024).
Automation and smart valve technologies
The integration of automation and smart technologies into ball valves has revolutionised their operation in LNG and CNG stations. Modern ball valves are now equipped with sensors and actuators that enable real-time monitoring and remote control, greatly enhancing operational efficiency and safety (Harris & White, 2023). Smart valves can detect and respond to changes in flow, pressure and temperature automatically, reducing the risk of human error and improving overall system reliability. Studies have shown that the implementation of smart valve technology can reduce maintenance costs by up to 15% and decrease unplanned downtime by 20% (Lee & Kim, 2023).
Additionally, the use of predictive maintenance algorithms, powered by data from smart valves, allows operators to anticipate and address potential issues before they lead to costly failures (Harris & White, 2023). This proactive approach not only extends the lifespan of
the valves but also ensures that LNG and CNG stations operate at peak efficiency.
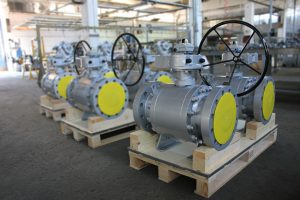
Comparative analysis: traditional vs. advanced ball valve technologies
The table below compares traditional ball valve technologies with the latest advancements in various key aspects relevant to LNG and CNG applications.
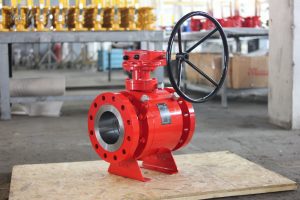
Lifecycle cost analysis
The lifecycle costs of ball valves have also been significantly reduced due to these technological advancements. Traditional ball valves often require frequent maintenance and replacement due to wear and tear, particularly in the harsh environments of LNG and CNG stations. However, the use of advanced materials and smart technologies in modern ball valves has resulted in a 25% reduction in maintenance costs and a 20% extension in valve lifespan (Lee & Kim, 2023). The table below provides a comparative analysis of lifecycle costs between traditional and advanced ball valves.
Environmental impact and sustainability
The advancements in ball valve technology also contribute significantly to environmental sustainability. The reduced leakage rates and improved sealing technologies minimise the emission of methane, a potent greenhouse gas, from LNG and CNG stations. Studies have shown that the implementation of advanced ball valves can reduce methane emissions by up to 30%, aligning with global efforts to combat climate change (Garcia & Martinez, 2024).
Furthermore, the use of additive manufacturing in valve production reduces material waste by approximately 20%, contributing to more sustainable manufacturing practices (Zhang & Li, 2024). The integration of smart technologies also supports more efficient energy use in valve operation, reducing the overall carbon footprint of LNG and CNG stations (Harris & White, 2023).
Case study of the implementation of advanced ball valves in LNG stations
In 2023, a major LNG station operator in Asia implemented advanced ball valve technologies across its facilities to improve efficiency and reliability. The operator replaced outdated carbon steel valves with new duplex stainless steel valves equipped with smart automation features.
Outcomes:
- Efficiency gains: The station reported a 15% improvement in operational efficiency due to the reduced leakage rates and enhanced flow control provided by the new valves (Smith & Jones, 2023).
- Cost savings: Maintenance costs were reduced by 20% due to the predictive maintenance features enabled by smart valve technology (Lee & Kim, 2023).
- Environmental impact: The enhanced sealing technology significantly reduced methane emissions, contributing to the operator’s sustainability goals (Garcia & Martinez, 2024).
- Reliability: The station experienced a 25% reduction in unplanned downtime, further improving its operational reliability (Evans & Brown, 2023).
This case study demonstrates the tangible benefits of adopting advanced ball valve technologies in LNG applications, highlighting their role in maximising efficiency and ensuring safe operations.
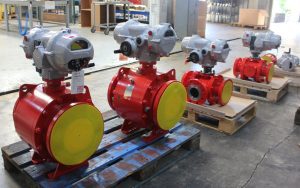
Conclusion
The evolution of ball valve technology is playing a critical role in enhancing the efficiency and reliability of LNG and CNG stations. Through advancements in materials, sealing technologies, manufacturing techniques and the integration of smart technologies, modern ball valves offer significant improvements over traditional designs. As the demand for cleaner energy sources continues to grow, these innovations will be essential in ensuring that LNG and CNG stations operate safely, efficiently and sustainably.
About Batu Valve Türkiye
Batu Valve Türkiye is a manufacturer of advanced valve solutions for Liquefied Natural Gas (LNG) and Compressed Natural Gas (CNG) applications. The company offers innovative ball valves designed to enhance efficiency, durability and reliability in high-pressure environments. Batu Valve’s products meet the demanding needs of LNG and CNG stations, ensuring safe and sustainable operations in the global energy infrastructure. Explore more at www.batuvalve.com.
Dive Deeper into Valve World
Enjoyed this featured article? There’s much more to discover! Subscribe to Valve World Magazine and gain access to:
- Advanced industry insights
- Expert analysis and case studies
- Exclusive interviews with valve innovators
Available in print and digital formats.
Breaking news: Digital subscriptions now FREE!
Join our thriving community of valve professionals. Have a story to share? Your expertise could be featured next – online and in print.
“Every week we share a new Featured Story with our Valve World community. Join us and let’s share your Featured Story on Valve World online and in print.”