Velan high performance ANSI-2500 isolation valves for residue hydrocracking
Explore how new valve technologies are improving residue hydrocracking processes, enhancing safety, efficiency and reactor performance in refinery operations.
By Duke Tran, P.Eng MBA and Luc Vernhes, P.Eng., Ph.D, Velan
Recent advancements in valve design and materials have led to substantial improvements in residue hydrocracking reactors (RHRs) operations. These innovations address key issues such as thermal shock, corrosion and the need for precise control in these critical processes. For example, thermal sleeves utilizing advanced materials and manufacturing techniques, like ceramic coatings and 3D printing, have emerged as effective solutions for protecting valves from rapid temperature fluctuations. These designs minimize heat transfer through conduction, convection and radiation, significantly extending valve lifespan and reducing maintenance requirements.
Gasket technology has also evolved to meet the demands of RHR environments. High-performance gaskets, including those employing noble metal plating, offer enhanced corrosion resistance, thermal stability and durability. These advancements ensure better sealing performance and reduced risk of leakage, which is crucial for both safety and efficiency in hydrocracking operations. Furthermore, the integration of automation systems, such as Programmable Logic Controllers (PLCs) and advanced control panels, has revolutionized valve management in RHRs. These systems enable precise control, efficient purging, optimal heating cycles and enhanced safety protocols. The combination of robust hardware and sophisticated software allows for real-time monitoring and adjustment, minimizing human error and maximizing process efficiency.
Thermal shock protection in valve design
Thermal shock poses a significant challenge in residue hydrocracking operations, where valves undergo rapid temperature fluctuations. During a typical process cycle, catalyst valves may experience numerous thermal cycles ranging from ambient temperature to over 800°F (427°C). These sudden changes cause different parts of the valve body to expand or contract at varying rates, potentially leading to severe mechanical stresses, cracking or complete valve failure.
To address this critical issue, valve manufacturers like Velan have developed advanced thermal protection solutions. One notable innovation in this field is the implementation of Hexashield™ ceramic-coated, 3D-printed thermal sleeves. These sleeves provide a robust thermal barrier that effectively absorbs and dissipates rapid temperature changes, thereby protecting the integrity of the valve body.
The effectiveness of these thermal sleeves lies in their ability to mitigate all three mechanisms of heat transfer:
- Conduction: Traditional solid metal sleeves readily conduct heat. In contrast, modern 3D-printed double-walled thermal sleeves create an insulating space between the walls, significantly reducing heat conduction. This design principle is similar to that used in vacuum-insulated containers.
- Convection: The double-wall design also minimizes convective heat transfer. By preventing direct contact between the high-temperature process fluid and critical areas inside the valve body, these sleeves effectively eliminate a major pathway for heat movement.
- Radiation: Advanced thermal sleeves often incorporate ceramic coatings on their inner surface. These coatings are designed to reflect radiant heat back towards the process fluid, further minimizing heat transfer to the valve body.
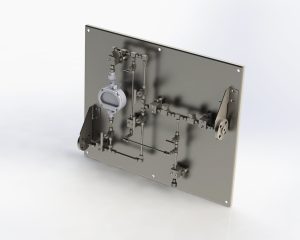
The combination of 3D printing technology and ceramic coating in thermal sleeve design offers several advantages:
- Precision manufacturing: 3D printing allows for the creation of complex, double-walled structures with precise specifications, optimizing thermal protection.
- Enhanced thermal resistance: Ceramic coatings provide an additional layer of thermal insulation, improving overall heat management.
- Corrosion and fouling resistance: Many ceramic coatings also offer excellent resistance to corrosion and fouling, enhancing the durability and longevity of the sleeve in harsh process environments.
These innovations in thermal protection technology enable valves to withstand the extreme conditions typical in residue hydrocracking processes, significantly improving reliability and reducing maintenance requirements.
Advanced gasket technology in severe service applications
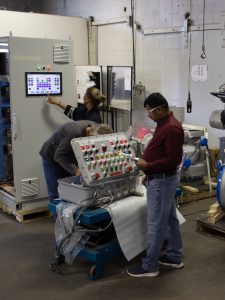
In residue hydrocracking processes, where extreme temperatures, high pressures, corrosive substances and significant mechanical stress are commonplace, the reliability and durability of gaskets are paramount. Recent advancements in gasket technology, such as Velan’s Securaring™ gold-plated gaskets, have emerged as critical components in these demanding environments, offering exceptional performance and longevity.
Gold-plated gaskets represent a significant leap forward in sealing technology for severe service applications. Their unique properties address several key challenges in hydrocracking processes:
- Corrosion resistance: Gold’s inherent resistance to corrosion, even when exposed to aggressive chemicals and gases, makes these gaskets ideal for environments where standard materials rapidly degrade. This resistance ensures long-term seal integrity in the presence of corrosive process fluids.
- Thermal stability: Gold maintains its properties across a wide temperature range, from cryogenic conditions to extreme heat. This stability is crucial in hydrocracking processes, where temperatures can fluctuate dramatically, ensuring consistent sealing performance under varying thermal conditions.
- Chemical inertness: The non-reactive nature of gold provides a robust barrier against chemical attacks that could compromise the seal. This inertness
is particularly valuable in processes involving complex hydrocarbon mixtures and catalysts. - Electrical conductivity: In highly combustible environments, the electrical conductivity of gold offers an additional safety benefit. By facilitating the dissipation of static electricity, these gaskets help prevent spark generation, reducing the risk of fires or explosions.
- Durability: Gold-plated gaskets exhibit excellent wear resistance, crucial for maintaining seal integrity in high-pressure and high-stress environments. This durability translates to extended service life and reduced maintenance frequency.
Velan’s Securaring™ gold-plated gasket incorporates these advantages while also addressing a common issue in gasket design. Its unique rib profile, securely positioned between the valve body and bonnet, prevents gasket rocking. This feature is critical as it ensures even distribution of sealing forces across the gasket surface. Uneven loading, a common problem with conventional gaskets, can lead to valve body leakage, compromising both safety and efficiency.
The implementation of such advanced gasket technologies goes beyond mere component improvement. It represents a systemic approach to enhancing the overall reliability and safety of hydrocracking units. By minimizing the risk of leaks and extending maintenance intervals, these gaskets contribute to increased operational uptime and reduced lifecycle costs.
Automation in residue hydrocracking units
Residue hydrocracking units in oil refining involve many interacting components: valves, purge systems, heat tracing systems and reactors. Managing these operations by hand is difficult, error-prone, and can put workers at risk. For these reasons, refineries use Programmable Logic Controllers (PLCs) and control panels to automate these processes. Automation in hydrocracking units offers several benefits:
- Precision and accuracy: Automated systems control valves, purging and heating cycles more accurately than manual operation. This reduces errors that could affect product quality or safety.
- Safety: PLCs can detect unusual conditions quickly and trigger alarms or shutdowns to prevent accidents.
- Efficiency: Automated control adjusts operational settings to reduce downtime and improve unit efficiency.
- Data logging and analysis: PLCs record operational data, which helps with monitoring, analysis, maintenance planning and process improvements.
These automation systems play a crucial role in enhancing the safety, efficiency and reliability of residue hydrocracking units.
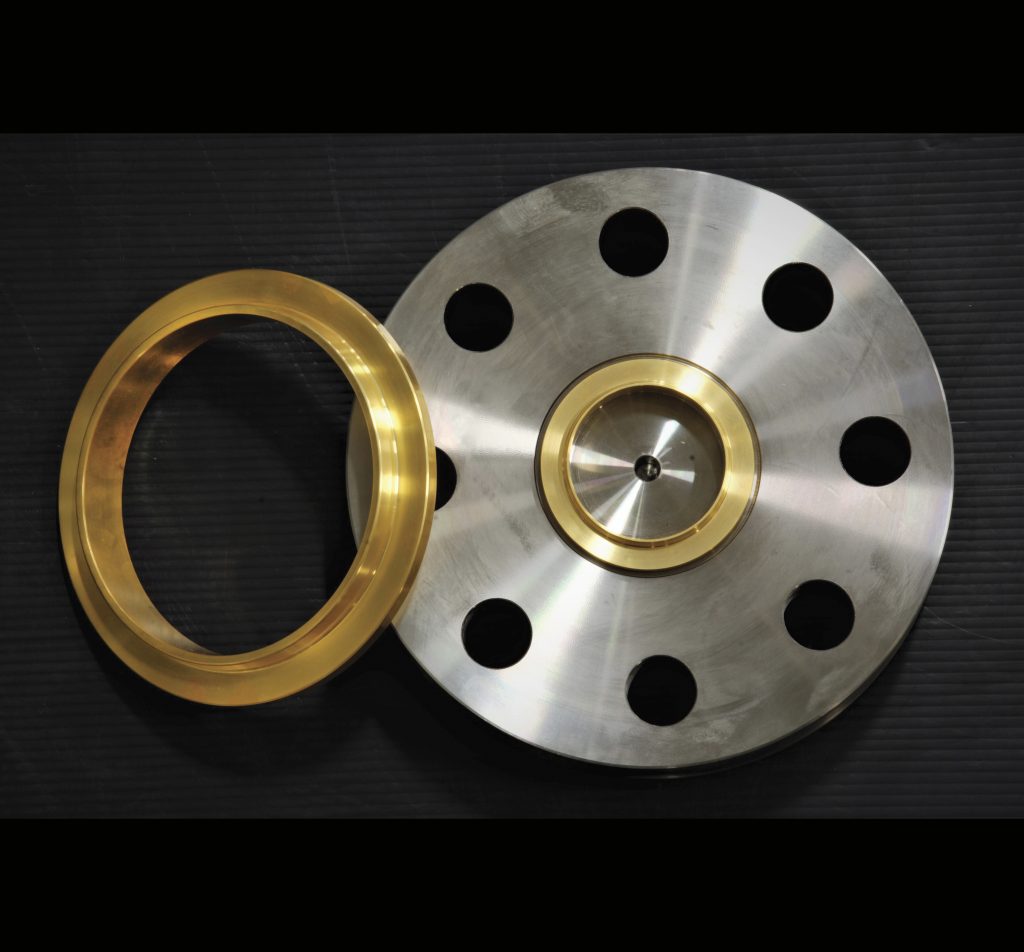
PLC-controlled systems in residue hydrocracking
Programmable Logic Controllers (PLCs) are essential in managing the complex operations of residue hydrocracking units. These systems offer precise control, enhanced safety and improved efficiency. Here’s an overview of key applications:
1. Valve control
- Sequential operation: PLCs manage valve sequences, ensuring correct material flow throughout the process. This includes precise valve timing and maintaining proper pressure and flow rates.
- Safety interlocks: These systems prevent valves from operating under unsafe conditions, avoiding hazards like over-pressurization or improper chemical mixing.
- Real-time monitoring: Continuous tracking of valve positions helps quickly identify and address any issues.
2. Purge system management
- Automated purging: PLCs control purging cycles, ensuring thorough removal of unwanted gases or liquids from the system.
- Feedback-based adjustments: Sensors provide real-time data on purging effectiveness, allowing for necessary adjustments.
- Safety integration: Purge systems connect with overall safety protocols, automatically triggering purges during anomalies or emergency shutdowns.
3. Heating cycle control
- Temperature regulation: PLCs monitor and adjust heating elements to maintain optimal temperatures for efficient reactions.
- Energy management: Automated control helps optimize energy use, balancing operational costs with process efficiency.
- Thermal safety measures: Temperature sensors and feedback systems prevent overheating, protecting equipment and personnel.
4. Control panel features
- Operator interfaces: Control panels typically feature user-friendly interfaces for easy monitoring and control.
- Performance analytics: Many systems include tools for analyzing performance data, helping identify trends and potential issues.
- Remote access capabilities: Some setups allow for remote system access, enabling quick responses to operational changes.
- Data management: Continuous data logging supports detailed analysis, reporting and regulatory compliance.
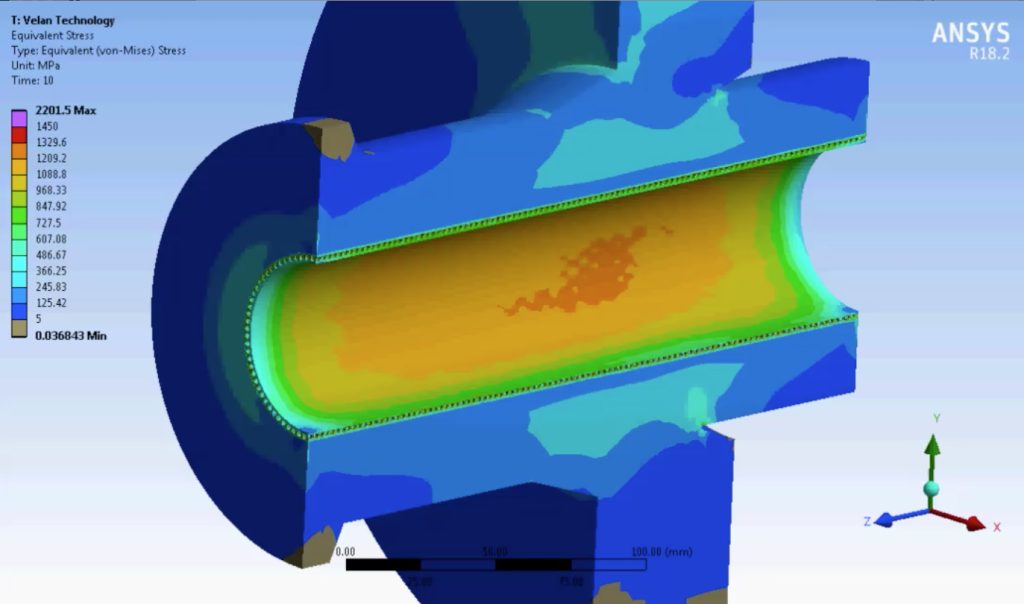
Conclusion
Advancements in valve technology are playing a crucial role in enhancing the reliability, efficiency and safety of residue hydrocracking reactors. These complex systems operate under extreme conditions, necessitating continuous innovation in materials, design and control systems.
Key developments in the field include:
- Thermal protection solutions that mitigate the effects of rapid temperature changes on valve components.
- High-performance gaskets utilizing noble metal plating to improve corrosion resistance and sealing capabilities.
- Advanced automation systems that provide precise control, real-time monitoring and predictive maintenance capabilities
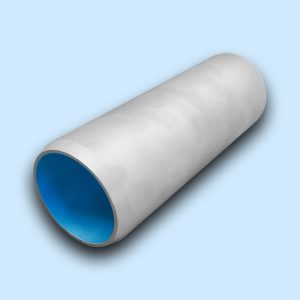
Velan has contributed to these advancements with innovations such as the Hexashield™ thermal sleeve and Securaring™ gold-plated body seal gaskets. Such technologies, coupled with digital solutions for real-time monitoring and predictive maintenance, provide a robust framework for optimizing reactor performance.
These innovations collectively contribute to:
- Improved reactor performance and product quality
- Extended equipment lifespan and reduced maintenance requirements
- Enhanced safety protocols and risk mitigation
- Increased operational efficiency and reduced downtime
As the refining industry faces growing challenges, including processing heavier crude oils and meeting stricter environmental regulations, these technological advancements will be essential.
The ongoing collaboration between valve manufacturers like Velan, refineries and research institutions will be crucial in driving further innovations to address the complex needs of residue hydrocracking processes.
About the authors
Duke Tran, P.Eng MBA, is the Executive Vice-President of Product Innovation and Technology at Velan. With 35 years in the valve industry, Duke has led engineering teams at major global manufacturers and held executive roles in sales, marketing, and business development. He holds 37 US patents in flow control technologies, reflecting his commitment to advancing fluid handling systems.
Luc Vernhes, Ph.D, P.Eng., is the Director of Business Development at Velan, which he joined in 2003. He previously led Velan’s Innovation, R&D, and Technology team and the metal-seated ball valve design team. Luc chairs the Canadian Mirror Committee ISO/TC 153, holds a PhD in Engineering Physics and a Master’s in Mechanical Engineering, and is a licensed Mechanical Engineer in Québec. He has six US patents and has published approximately 15 peer-reviewed papers.
Dive Deeper into Valve World
Enjoyed this featured article? There’s much more to discover! Subscribe to Valve World Magazine and gain access to:
- Advanced industry insights
- Expert analysis and case studies
- Exclusive interviews with valve innovators
Available in print and digital formats.
Breaking news: Digital subscriptions now FREE!
Join our thriving community of valve professionals. Have a story to share? Your expertise could be featured next – online and in print.
“Every week we share a new Featured Story with our Valve World community. Join us and let’s share your Featured Story on Valve World online and in print.”