Mike Parrott is a mechanical engineer with extensive experience in valve engineering and nuclear power. He currently works as a senior manager for commodity equipment at Rolls-Royce SMR, where he develops valve solutions for Small Modular Reactors (SMRs). We spoke with Mike to learn about the challenges and progress in valve engineering for this new nuclear technology.
By Valve World Editor
The nuclear power industry is seeing renewed interest, with Small Modular Reactors (SMRs) leading this renewed focus. These compact, scalable nuclear reactors aim to be deployed faster and at lower costs compared to traditional large-scale plants. Rolls-Royce SMR is making notable progress in SMR development.
Mike Parrott has been involved in Rolls-Royce SMR’s valve engineering efforts for nearly four years. His extensive experience in mechanical engineering and valve design provides valuable knowledge to this field.
Mike’s path to Rolls-Royce SMR
Mike’s career began with a ball valve manufacturer in the UK, where he worked on mechanical engineering design, calculations and drafting. He later joined Rolls-Royce’s Submarines business. “I spent nine years in the Submarines business, supporting the UK nuclear submarines. Design, manufacturing, safety case and in-service support,” Mike explains. This work gave him insights into nuclear engineering in confined spaces.
Rolls-Royce SMR’s progress
Rolls-Royce SMR has made significant progress in the UK market. Mike explains, “We’ve just completed the generic design assessment step two.”
The Generic Design Assessment process, overseen by the UK nuclear industry’s independent regulators, is a key milestone for Rolls-Royce SMR. Mike elaborates on the GDA process: “It provides independent review of our safety, security, safeguards, waste management and environmental protection. We provide information to the regulators to provide confidence in our design, safety case, principles and processes.”
Focusing on consistent design
A main goal in SMR development is consistency in design, which can improve efficiency and reduce costs. Mike emphasises this point: “We need to ensure consistency. This means using the same terminology across the industry, communicating clearly with suppliers and using consistent products within the plant.”
This approach extends beyond terminology to the entire process of valve selection and design. “We’re trying to reduce spare parts and improve maintenance procedures,” Mike adds. “We’re looking at how we can use one product in multiple areas of the plant.”
The benefits of this consistency are significant. It simplifies maintenance, reduces inventory costs and streamlines manufacturing. Mike provides an example: “We’ve designed a valve body that can be used in multiple manufacturing processes and in different areas of the plant. This allows for flexibility and consistency.”
Working together for new ideas
Working together for new ideas Mike emphasises the importance of working with suppliers in the valve industry. “That’s where a lot of the knowledge is,” he says. “I know a lot about valves, but the suppliers are the real experts on their products.”
This collaborative approach involves looking at valves from a new perspective. Rather than focusing only on where a valve has been used before, Mike encourages suppliers to consider what the valve can do. “It’s about understanding what the product can do, rather than just where it’s been used before,” he explains.
Mike describes their approach: “Instead of saying ‘Here’s what we need, give us a valve,’ we explain the situation and ask, ‘How would you address this? What options do we have?’” This open approach encourages new ideas and problem-solving.
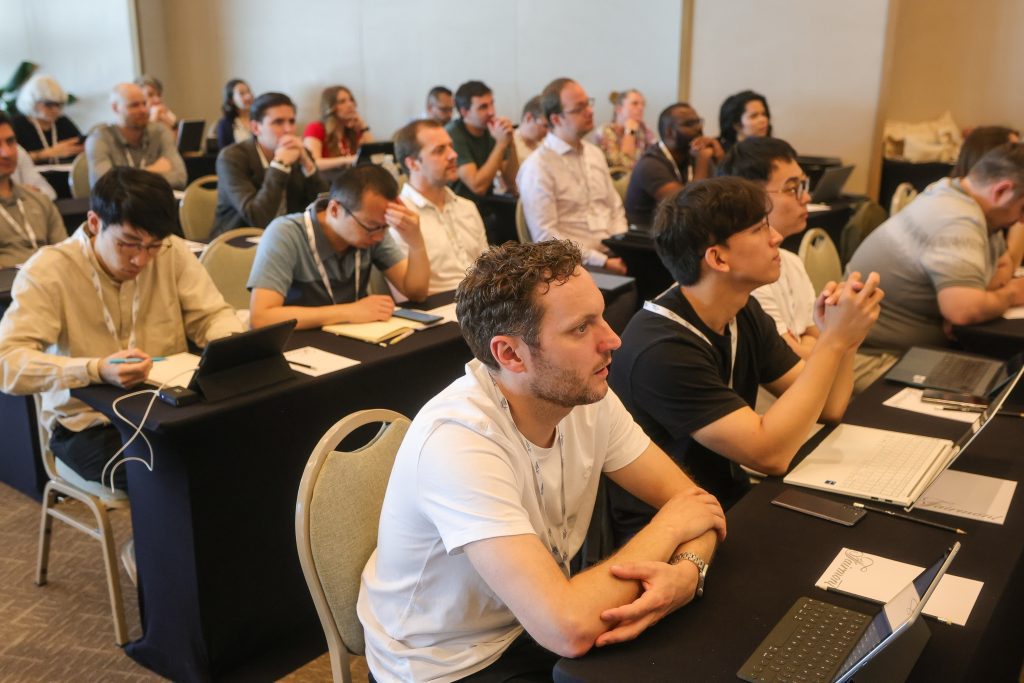
Balancing new ideas with proven technology
While new ideas are important, the nuclear industry also needs to use proven technologies for safety and reliability.
Mike notes, “We’re trying to use as much technology that’s already been used in the nuclear industry as possible. That’s important for an SMR.”
However, this doesn’t mean new ideas are off-limits. Rolls-Royce SMR is developing new valve designs. Mike reveals, “We are developing a new valve with several patents pending. We hope this will help the entire nuclear industry, not just Rolls-Royce SMR.” The balance between new ideas and proven technology is delicate. Mike explains, “When we decide who to work with and why, we try to use as much information and products that have already been proven. We have to balance what’s new and good with what has always worked well.”
3D printing: A new approach to valve production
One area that Mike finds particularly interesting is 3D printing, also known as additive manufacturing. “I think 3D printing will be very useful for our industry,” he says. “With 3D printing, we can address problems we’ve had with control valves, like instabilities or manufacturing defects.” This technology could change how valves are produced, allowing for more complex designs and potentially reducing costs. Mike explains, “We can use advanced analysis to determine what we need, then print a part that fits in the same space as the old one. This can improve how the system works.” The potential uses of 3D printing in the nuclear industry are extensive. Mike adds, “3D printing could help the industry in many ways. We could use it to make valve bodies, valve cages and other parts.”
Following regulations and working internationally
The nuclear industry operates under strict regulations, and for good reason. Mike highlights their importance: “Regulatory compliance is essential not just for safety, but also for public trust. Nuclear power has faced scepticism in the past, but ultimately, it’s a well-controlled process for generating electricity.”
Rolls-Royce SMR is not only following UK regulations but also looking at international standards. Mike mentions their work with the International Atomic Energy Agency (IAEA): “We’re working with them to see how different regulators can work together. This is an important aspect of what’s happening in the nuclear industry.”
This international cooperation could make the approval process for SMRs easier worldwide. Mike explains, “If we go to another country, we go through their regulatory process. We want them to use as much of our existing work as possible. The IAEA is supporting this transition and journey or collaboration between regulatory bodies. in another country.”
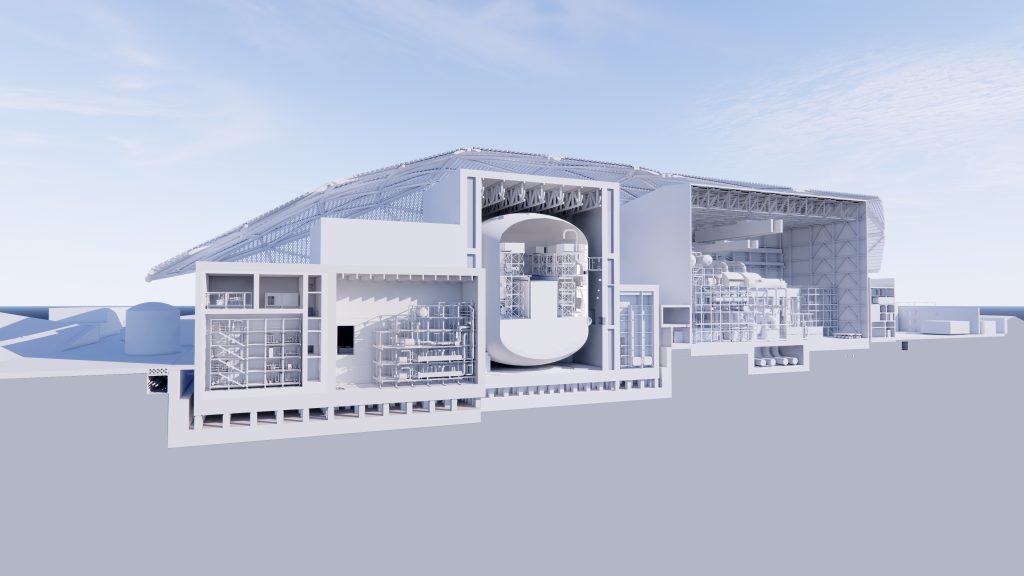
Nuclear safety first
Throughout our conversation, Mike consistently emphasised the importance of safety in nuclear engineering. “Safety is the top priority in any industry. But in nuclear, the layers of safety we have in our products and processes are absolutely essential,” he states. This focus on safety is reflected in the strict standards and processes Rolls-Royce SMR follows, including the concept of ALARP (As Low As Reasonably Practicable) in risk assessment and safety design. Mike explains, “We use the ALARP principle. We always have to balance different factors, but safety is always at the top.”
The interconnected nature of the nuclear industry makes safety even more important. Mike notes, “What one company does in the nuclear industry affects everyone. If we made a mistake, it would impact the entire industry.”
The future of SMRs and valve engineering
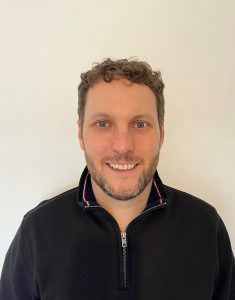
Looking ahead, Mike is positive about the future of SMRs and their role in global energy production. “SMRs will grow quickly because they can be connected to the grid faster than traditional large power stations,” he predicts. “Getting connected to the grid faster means a quicker return on investment.”
However, he’s quick to add that SMRs are not the only solution to all energy needs. “SMRs won’t solve all our energy problems by 2050. They’re part of a mix of energy sources,” Mike clarifies. “The World Nuclear Association has done a lot of work predicting future energy needs. SMRs will help meet that demand, but they’re not the full solution.”
For valve engineering in this new era of nuclear power, Mike advises professionals to broaden their thinking. “Use your experience, but also try to expand it. Don’t just think about what a valve does, but what it could do. Think about its function, where it could be used, and what challenges the industry faces.”
Mike also encourages valve manufacturers to adapt to the needs of the nuclear industry. “Look at your products from a different angle. Consider how they fit with nuclear standards and what that means for your business.”
Conclusion
The development of SMRs represents a new direction in nuclear power, with valve engineering playing a crucial role. Companies like Rolls-Royce SMR are working towards safer, more efficient nuclear reactors through consistent design, collaboration and balancing innovation with proven technology.
While challenges remain, including maintaining strict safety standards and working across international borders, the industry is well-positioned to overcome these hurdles. SMRs offer a promising option for clean, reliable energy, but their success depends on continued progress in valve engineering and other critical components. The valve industry has a unique opportunity to contribute to this emerging field by adapting existing technologies and developing new solutions for SMRs.
Dive Deeper into Valve World
Enjoyed this featured article? There’s much more to discover! Subscribe to Valve World Magazine and gain access to:
- Advanced industry insights
- Expert analysis and case studies
- Exclusive interviews with valve innovators
Available in print and digital formats.
Breaking news: Digital subscriptions now FREE!
Join our thriving community of valve professionals. Have a story to share? Your expertise could be featured next – online and in print.
“Every week we share a new Featured Story with our Valve World community. Join us and let’s share your Featured Story on Valve World online and in print.”