Offshore platform
William Braule, an Application Engineer for DuPont’s Kalrez® business, Meyrin, Switzerland, discusses the company’s approach to creating sealing solutions for hydrogen and carbon dioxide applications in the valve industry.
By Valve World Editor
As industries worldwide shift toward sustainable practices and clean energy solutions, the need for specialised sealing technologies has grown significantly. At the forefront of this transition is William Braule, an Application Engineer for DuPont’s Kalrez® business.
In his role, Braule provides technical services for customers in energy and oil & gas applications across Europe, the Middle East and Africa (EMEA), focusing on selecting and designing elastomer valve seals and packings for challenging applications. He also coordinates The DuPont Center of Excellence for Oil & Gas and Energies.
With DuPont’s extensive background in materials science, Braule and his colleagues are addressing the unique challenges presented by hydrogen and carbon dioxide applications in the valve industry. Their work is crucial in developing sealing solutions that can withstand the demanding conditions of these emerging energy sectors.
“Our company strategy incorporates sustainability at every level as we work towards the 2050 net zero CO2 emissions goal,” Braule explains. This commitment to sustainability drives DuPont’s innovation in sealing technologies, particularly for clean energy applications.
Understanding the challenges of H2 and CO2
The move towards clean energy sources introduces a set of complex technical issues, particularly in sealing applications. Braule elaborates on the distinct nature of these challenges: “Carbon dioxide and hydrogen each present a different problem. Carbon dioxide can cause elastomer seals to swell, while hydrogen is difficult to contain due to its small molecular size and high diffusion rate.”
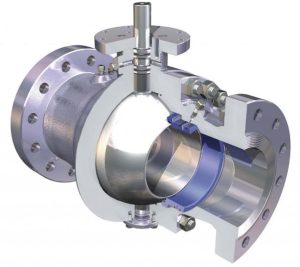
This dichotomy necessitates a careful approach to perfluoroelastomer sealing development. For CO2 applications, the main concern is the ability to withstand rapid gas decompression, which can lead to seal damage. In contrast, hydrogen applications require materials that can prevent gas escape and leaks due to the gas’ small molecules and high diffusivity.
DuPont’s solution for advanced sealing
DuPont’s Kalrez® perfluoroelastomer components are central to addressing these challenges. Braule explains, “Kalrez® perfluoroelastomer parts are uniquely positioned to meet the demands of new clean energy applications and CO2 capture across various industries.”
The distinguishing factor of Kalrez® parts is DuPont’s control over the production process, from creating the base polymer to manufacturing the finished seal. This comprehensive approach allows for exceptional quality control, traceability and performance optimisation.
Braule highlights the chemical structure that gives Kalrez® parts its advantage: “The carbon-fluorine bond provides excellent chemical and thermal resistance.” This robust chemical composition makes Kalrez® parts particularly suitable for the demanding conditions found in H2 and CO2 applications, which can also include impurities.
Comprehensive testing for assured performance
So that Kalrez® seals perform reliably in these challenging applications, DuPont conducts thorough testing. Braule outlines their methodology: “Our testing processes for H2 and CO2 environments are comparable to other gas or fluid tests for Oil and Gas services, with additional safety measures for hydrogen testing.”
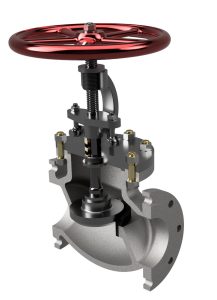
The testing parameters are extensive, covering, for example, pressure, temperature, gas concentration, exposure time and rapid gas decompression resistance. Recent Rapid Gas Decompression (RGD) testing for hydrogen applications involved several steps:
- Using a specialised test fixture with multiple O-rings
- Compressing O-rings evenly while exposing them to gas
- Placing the test fixture in a pressure vessel
- Heating and pressurising the vessel
- Performing decompression cycles
The specific conditions for the study included pure H2 gas, 13% seal compression, 200 bar pressure, 150°C temperature, a 72-hour hold time, and a 120 bar/min decompression rate.
Customised solutions for various applications
Recognising the diverse requirements across industries, DuPont offers several grades of Kalrez® parts for different applications. Braule details some of these offerings:
- Kalrez® Spectrum™ 6375 and 6380 for specific chemical environments
- Kalrez® Spectrum™ 7075 and 7090 for extreme heat resistance above 300 °C / 320 °C in air.
- Kalrez® OG193 and 0090 for superior Rapid Gas Decompression (RGD) resistance and gap extrusion resistance
- Kalrez® Spectrum™ 7375 and 7390 for steam resistance and high heat resistance up to 300 °C.
Additionally, Kalrez® Valve Stem Packing (KVSP™) is designed specifically to reduce unwanted emissions in control valve glands.
“Kalrez® Valve Stem Packing addresses the issue of fugitive emissions in petrochemical plants,” Braule notes.
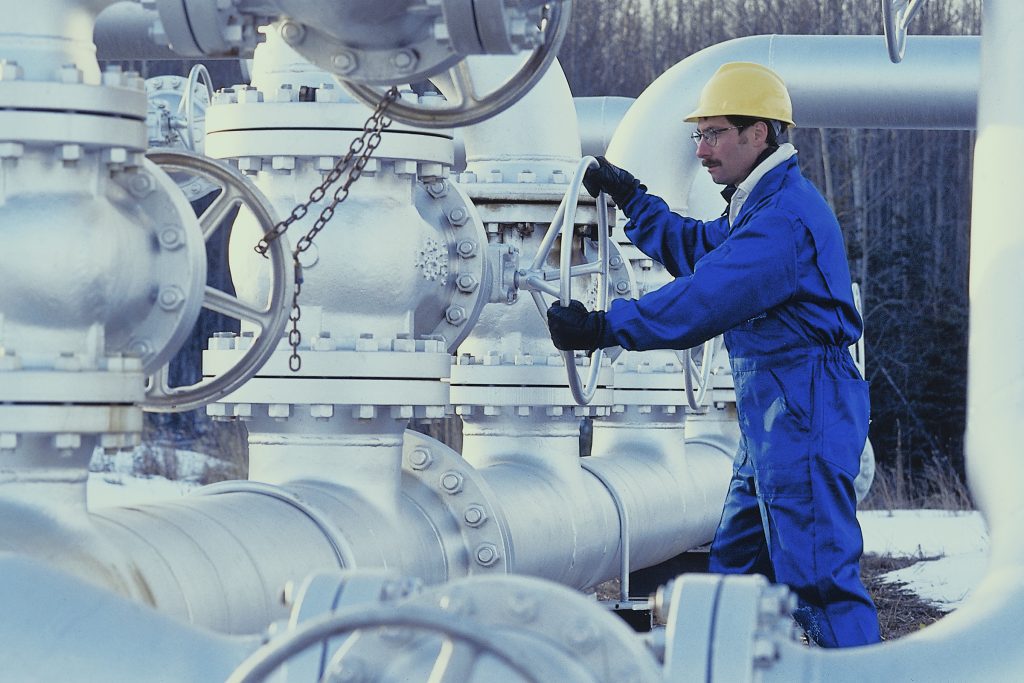
Practical applications and case studies
The effectiveness of Kalrez® seals is best demonstrated through real-world applications. Braule shares two notable examples:
- Kalrez® Valve Stem Packing (KVSP™) in a petrochemical plant:
Applied in control valve glands handling a mixture of pentane, butane, hexane, acetone and acidic water at -30°C and ~4.5 MPa, KVSP™ performed better than competitive PTFE packings. The outcome was an absence of detectable gland leaks and yearly savings of £54,000 per reactor unit. - Kalrez® 0090 O-Rings in sour gas application:
Used in ball valves in the Oil & Gas industry, these O-rings managed sour feed gas with 5-15% H2S and 2-5% CO2 at temperatures from -7 to 121°C and pressures of 71 to 85 bar. Braule states, “Due to their exceptional chemical resistance and outstanding RGD performance, Kalrez® 0090 O-rings perform better than competitive FFKM seals and show minimal or no degradation.” The seals surpassed performance requirements of 24 months, compared to 6-12 months for competitive solutions, resulting in substantial cost savings and improved reliability.
The importance of collaboration in sealing technology
As the need for H2 and CO2-resistant seals grows, Braule emphasises the significance of collaboration. “At DuPont, we maintain close contact with both valve manufacturers and end users to understand their needs and goals. This approach creates an environment where all parties can learn from each other.”
This collaborative approach is crucial, especially given the current lack of widely accepted industry standards for selecting seals in H2 and CO2 applications. Braule notes that DuPont is working on compliance with new standards, such as API 6D Annex M for hydrogen service in pipelines and pipe valves.
Sealing technology in clean energy transition
The transition to clean energy sources presents both challenges and opportunities for sealing technology. Braule explains that as industries move towards more sustainable practices, the demands on sealing materials are evolving.
“In the context of hydrogen applications, we’re dealing with a gas that has a very small molecular size,” Braule elaborates.
“This means that traditional sealing materials may not be sufficient to prevent leakage. Our work with Kalrez® parts focuses on developing materials that can effectively contain hydrogen under various pressure and temperature conditions.”
For carbon dioxide applications, particularly in carbon capture, utilisation and storage
(CCS) technologies, the challenges are different. “CO2 can cause significant swelling in many elastomers, which can lead to seal failure,” Braule says. “Additionally, in CCS applications, we often deal with rapid gas decompression scenarios, which can cause severe damage to seals if they’re not properly designed.”
These challenges highlight the need for continued innovation in sealing technology. Braule believes that advancements in this field will play a crucial role in enabling
the widespread adoption of clean energy technologies.
Future trends in sealing technology
Looking ahead, Braule anticipates several trends that will shape the future of sealing technology:
- Increased focus on sustainability: “We expect to see growing demand for sealing materials that are not only high-performing but also environmentally friendly,” Braule predicts. “This includes considerations of the material’s lifecycle, from production to disposal.”
- Material science advancements: “Ongoing research in polymer science may lead to new materials with even better performance characteristics,” Braule says. “We’re particularly interested in materials that can withstand extreme temperatures and pressures while maintaining their sealing properties.”
- Customisation and specialisation: “As industrial processes become more complex, we anticipate a growing need for highly specialised sealing solutions tailored to specific applications,” Braule notes..
Sustainability
DuPont has placed sustainability at the core of its business strategy and innovation pipeline. As stated by former CEO Ed Breen, “At DuPont, sustainability is integral to our strategy, embedded in every aspect of our business.” The company’s approach is built on three pillars: Innovate, Protect, and Empower. A key sustainability goal for DuPont is “Delivering solutions for global challenges” through product innovation. More than 80% of DuPont’s innovation portfolio is expected to deliver sustainability value for customers or advance solutions to global challenges. This includes a new enterprise-wide initiative focused on developing products for the emerging hydrogen value chain, including green and blue hydrogen technologies.
DuPont has observed increasing customer demand for product carbon footprint data and carbon reduction strategies, with over 60% of their strategic customers having set climate targets. As Chief Technology and Sustainability Officer Alexa Dembek notes, “The number one way that we can lead sustainably is through innovation that addresses global challenges.”
The economic impact of advanced sealing solutions
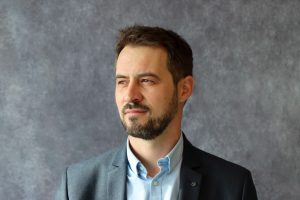
While the technical aspects of sealing technology are crucial, Braule also emphasises the economic benefits of advanced sealing solutions. “When we consider the total cost of ownership, investing in high-quality seals, in the shape of O-rings, T-Seals or customer parts, often results in significant long-term savings,” he explains. This is particularly true in critical applications where seal failure can lead to costly downtime or safety issues.
“In applications where unplanned maintenance or seal failure can result in significant economic losses or damage to a company’s reputation, the initial cost of the sealing element becomes a secondary consideration,” Braule states.
He illustrates this point with an example from the Oil & Gas industry: “Offshore operations face significant financial risks from unplanned downtime. By using high-performance seals that can extend maintenance intervals from 6 to 24 months, companies can achieve substantial cost savings and operational benefits.” Industries face increasing pressure to reduce emissions, and high-performance seals can play a role in meeting regulatory requirements. “Fugitive emissions from valves and other equipment are a significant concern in many industries,” Braule notes. “Advanced sealing solutions can help companies comply with stringent environmental regulations while also improving their operational efficiency.”
Collaboration and innovation
As the sealing industry continues to evolve, Braule sees collaboration as key to driving innovation. “No single company has all the answers,” he admits. “It’s crucial that seal manufacturers, valve producers, end users and research institutions work together to address the challenges we face.”
This collaborative approach extends beyond technical development. Braule emphasises the need for knowledge sharing and education within the industry. “As new technologies emerge, it’s important that we educate engineers and technicians
on proper seal selection, installation and maintenance,” he says. “This knowledge transfer is crucial so that the benefits of advanced sealing technologies are fully realised in real-world applications.” DuPont is actively engaged in these educational efforts, offering training programs and technical support to its customers and partners. “We see our role not just as a product supplier, but as a knowledge partner,” Braule explains.
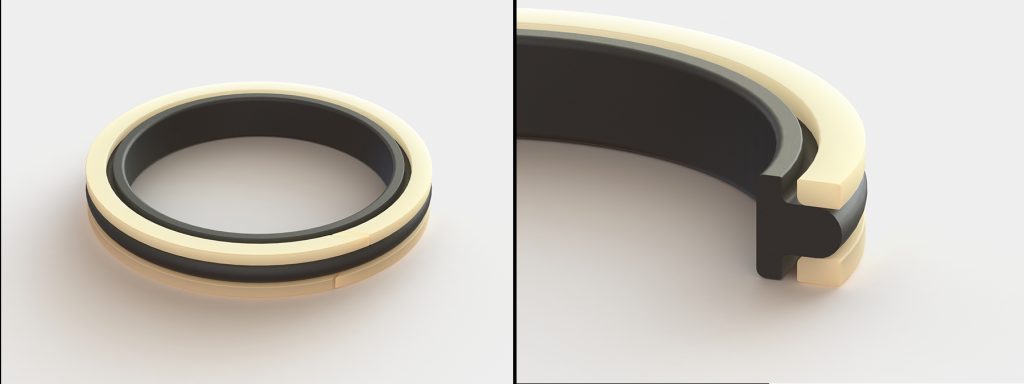
Sealing the clean energy future
As industries worldwide continue their transition towards cleaner, more sustainable energy sources, the role of advanced sealing technologies becomes increasingly critical. From containing hydrogen in fuel cells to managing CO2 in carbon capture systems, these often-overlooked components play a vital role in enabling the clean energy technologies of the future.
As William Braule concludes, “The challenges we face in the transition to clean energy are significant, but they also present tremendous opportunities for innovation. At DuPont, we’re excited to be part of this journey, developing the sealing solutions that will help make a more sustainable future possible.”
Rapid growth in low-emission hydrogen and CCUS capacities
The hydrogen sector is poised for significant expansion in the coming years, particularly in low-emission production methods. According to the International Energy AgencyGlobal Hydrogen Review 2023:
- Electrolyser manufacturing capacity could increase from about 8 GW/year in 2022 to around 80 GW/year by 2030 if all announced projects are realised. This represents a tenfold increase in capacity for green hydrogen production.
- The production of low-emission hydrogen from fossil fuels with carbon capture, utilisation and storage (CCUS) is projected to grow from about 0.6 Mt in 2022 to approximately 6 Mt by 2030 if all announced projects come to fruition. This also represents roughly a tenfold increase in blue hydrogen production capacity.
These projections highlight the rapid scaling expected in both green and blue hydrogen technologies, presenting significant opportunities and challenges for industry players in the coming years.
Dive Deeper into Valve World
Enjoyed this featured article? There’s much more to discover! Subscribe to Valve World Magazine and gain access to:
- Advanced industry insights
- Expert analysis and case studies
- Exclusive interviews with valve innovators
Available in print and digital formats.
Breaking news: Digital subscriptions now FREE!
Join our thriving community of valve professionals. Have a story to share? Your expertise could be featured next – online and in print.
“Every week we share a new Featured Story with our Valve World community. Join us and let’s share your Featured Story on Valve World online and in print.”