Q: Why do parabolic valve plugs have a tendency to slam into the valve seat?
A: Yes, there are certain conditions where this happens, but never when the stem diameter is larger than the seat diameter.
First, such conditions can be avoided when the valve is installed with flow tending to open the valve. Here the fluid force creates a negative feedback.
But then, “flow to open” can create violent eddies from turbulence above the valve plug, which may start resonant stem-plug vibration (and noise). With liquids, there also may be cavitation damage at the lower part of the valve stem.
“Flow to close” avoids the above problems in exchange for possible plug instability due to positive feedback of fluid forces.
Yet, there are conditions where it is unavoidable to use a valve this way. One case may be when the valve handles erosive fluids (such as Bauxite) or is involved in a chemical process (such as Urea let-down). Closing the valve in a system in case of an emergency might also be a reason.
Q: What creates such instability on flow-to-close plugs?
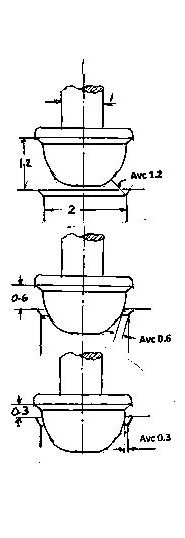
A: Positive forces are created when the force created by the inlet pressure exceeds the force created by the downstream pressure. When closing forces increase in the direction of travel, we have undesirable positive “feedback”. Here is an example explaining how this happens. (Please refer to Figure 1.)
Here is a 2 in globe valve, having a parabolic plug. It is assumed that the P1 inlet pressure is 100 psig. The flow is choked, making P2 = 0.5 P1. Under these conditions, the basic down force (BF) is (22 × 3.14/4 – 12 × 3.14 / 4 ) x 100 = 235 lbs. In this case, there are 3 travel positions: 0.3″, 0.6″ and 1.2″. Next, one has to know the vena contracta area (avc) which is affected by P2. (consult Figure 1). For 1.2” travel, they are: 3.14 in2, for 0.6”travel avc=1.16 in2, and at 0.3” travel, avc = 0.45 in2.
This allows calculation of the net downstream forces (NF). Starting with 1.2″ travel, NF = BF – avc × P2 = 235 –3.14 x 50 = 78.3 lbs. The NF for 0.6″ travel again is BF – avc × 50, or 235 – 1.16 × 50 = 177 lbs.
Finally, for 0.3″inch travel NF = BF – avc × 50, or, 235 – 0.48 × 50 = 211 lbs. From the above, one can expect the most instability between travels 1.2″ and 0.6″. Here the rate of change is (177 – 78) / 0.6 = 168 lb/inch. One way to reduce this danger is to employ an actuator spring with a spring rate in excess of 168 lbs/inch. Note, this only works if the actuator is in the “air to close” mode, (here the rate of spring force increase exceeds the rate of fluid induced force increases).
NF for 0 travel = 235 – 0 psi × 3.14 = 235 lb. Calculating the rate of force change near zero travel = (235 – 212.5) / 0.3 = 80 lbs/inch. This shows that the first 0.6 inch of travel are the most susceptible to “slamming.”
Q: Other than changing the actuator spring rate, are there other ways to improve stability?
A: One other method is: Changing the plug from parabolic to v-port plug, having a more constant vena contracta area around the circumference of the plug.
About the author
Dr. Hans D. Baumann is an internationally renowned consultant with extensive experience in the valve industry. Throughout his career, he held managerial positions in Germany and France, and his innovative spirit led to the creation of 10 novel valve types, including the well-known Camflex valve. Dr. Baumann has authored 8 books, including the acclaimed “Valve Primer,” and has been granted 115 US patents. He also founded his own valve company, which he later sold to Emerson, and served as Vice President at Masoneilan and Fisher Controls Companies.
About this Technical Story
This Technical Story is an article from our Valve World Magazine, December 2024 issue. To read other featured stories and many more articles, subscribe to our print magazine. Available in both print and digital formats. DIGITAL MAGAZINE SUBSCRIPTIONS ARE NOW FREE.
“Every week we share a new Technical Story with our Valve World community. Join us and let’s share your Featured Story on Valve World online and in print.”