This article examines the validation of compression packing solutions for reliable sealing in supercritical CO2 applications, with focus on testing methods and performance requirements for carbon capture systems.
By Martin Coulthard, Rajib Roy and Jakub Marczyk, James Walker
As the demand for carbon capture, utilisation and storage (CCUS) technology continues to grow, the need for effective and reliable sealing solutions in supercritical CO2 (sCO2) applications has become increasingly important. Among these sealing solutions, compression packing plays a pivotal role, particularly in valve stem sealing applications where the integrity of the seal is paramount for both operational efficiency and environmental safety. sCO2 presents unique challenges, including high pressures, variable temperatures and the potential for chemical interactions with sealing materials. Therefore, selecting appropriate compression packing materials and designs is essential to ensure long-term performance and reliability in these demanding environments.
CCUS is gaining significant popularity due to its crucial role in helping achieve carbon emission reduction targets. To meet the global Net Zero CO2 emissions goal by 2050 and the 1.5°C limit set by the Paris Agreement, investment in CCUS projects is growing rapidly and is expected to continue doing so. This article examines the sealing challenges faced in CCUS and James Walker’s commitment to meeting these as part of its own drive for sustainability and environmental protection.
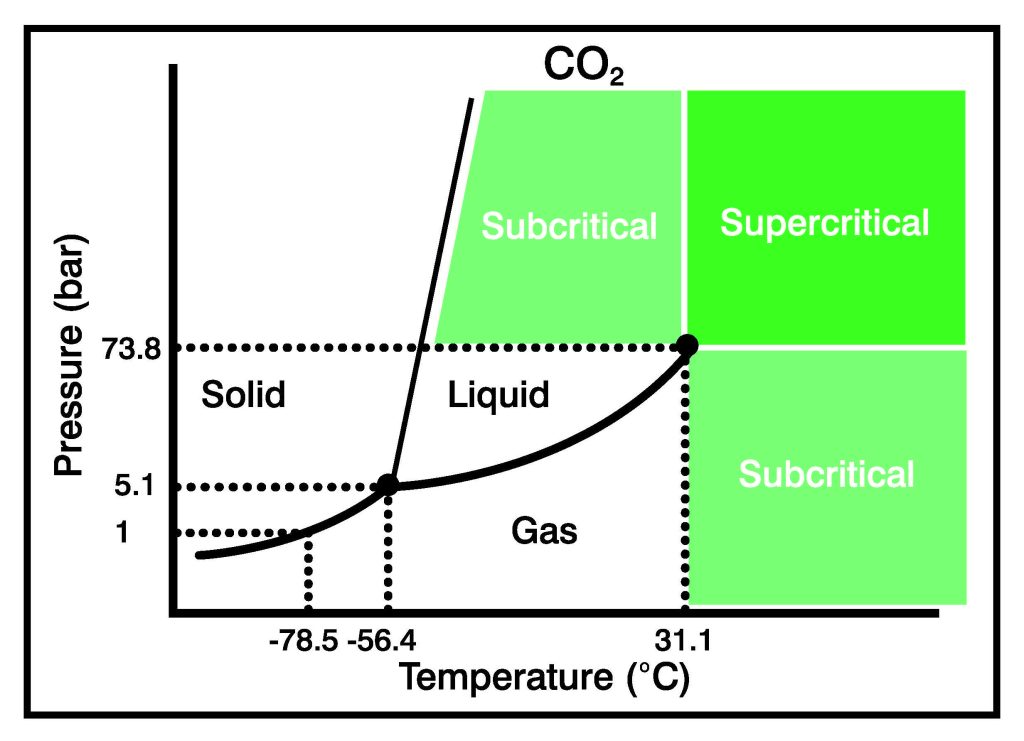
Sealing challenges in supercritical CO2 applications
CO2 exists in multiple phases—gaseous, liquid, and supercritical—depending on the temperature and pressure in application. These phase transitions present unique challenges for the materials used in CCUS systems. CO2 enters a supercritical state at relatively modest conditions (around 31°C and 74 bar, or 1070 PSI), and in this state, it displays characteristics of both a liquid and a gas. This supercritical phase is particularly advantageous for transport and storage of CO2 due to its high density, but it also poses significant challenges for the materials used in pipelines, compressors, and valves. Compression packing serves as a versatile sealing mechanism, providing flexibility and adaptability across various applications.
However, its performance in sCO2 environments requires careful consideration of material compatibility, thermal stability, and mechanical properties. Materials such as PTFE (polytetrafluoroethylene) and other advanced polymers are currently being evaluated for their ability to withstand the specific conditions presented by sCO2, including the effects of pressure and solvent characteristics.
High-performance fugitive emissions control
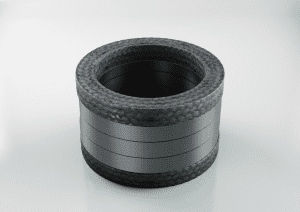
When evaluating packing systems for sealing in supercritical CO2 (sCO2), several critical factors must be considered to ensure effective control of fugitive emissions and maintain long-term system integrity:
Chemical compatibility: The solvent Power of sCO2 can dissolve various substances, potentially degrading lubrication packages not designed for such conditions.
Permeation and phase transitions: The permeation of sCO2 into the packing set and subsequent phase transitions between supercritical, liquid, and gas states can induce physical stress on materials. This can lead to mechanical failure, increased wear, and the formation of additional leakage paths.
External leakage and cooling effects: External leakage can cause rapid cooling around the packing interface, potentially freezing the external part of the system through the Joule-Thomson effect. This can result in mechanical changes within the system, leading to excessive leakage or premature failure.
Selecting a proven & validated fugitive emissions control packing can support long-term system integrity by mitigating the risk of an initial leak path forming.
Retention of low frictional load
The correlation between fugitive emissions and frictional behaviour is significant. Controlling frictional behaviour involves managing the impact of the sCO2 medium, which can degrade lubrication packages due to chemical incompatibility and subject the packing to mechanical stresses through media phase transitions caused by temperature and pressure changes. Rapid cooling effects through leakage can induce additional mechanical and thermal stresses in the system, causing premature material degradation and frictional performance losses. To manage these effects and maximise long-term system performance, careful specification of base materials, lubrication packages, control of fitting procedures and technical assessment of the original equipment design is essential.
Packing integrity and robustness in high-pressure duties
In high-pressure applications, ensuring the integrity and robustness of packing systems is paramount to maintaining operational efficiency and safety.
Mechanical stability: Maintaining mechanical stability is essential, especially with supercritical CO2 (sCO2) under high pressures, which can increase sealing leakage and wear due to elevated hydrostatic unloading effects.
Material selection and housing design: High-pressure sealing challenges require advanced materials that withstand hydrostatic forces, thermal transients, and creep relaxation. Precision manufacturing can ensure seals fit correctly and perform under sCO2 conditions, meeting diverse customer housing design needs.
Phase transitions and material stress: Transitions between supercritical, liquid, and gas states can stress materials, leading to mechanical failure or wear. Cooling during pressure reduction, especially to a gaseous phase, can cause thermal stress and material degradation.
Utilising proven materials: Using tested materials ensures resilience against creep relaxation and thermal expansion variations, maximising product performance and lifecycle under challenging conditions.
The selection of appropriate materials and precise manufacturing processes are critical to developing sealing solutions that can withstand the rigorous demands of high-pressure environments. By focusing on mechanical stability, material resilience, and the ability to handle phase transitions, we can ensure the longevity and reliability of sealing products in supercritical CO2 applications.
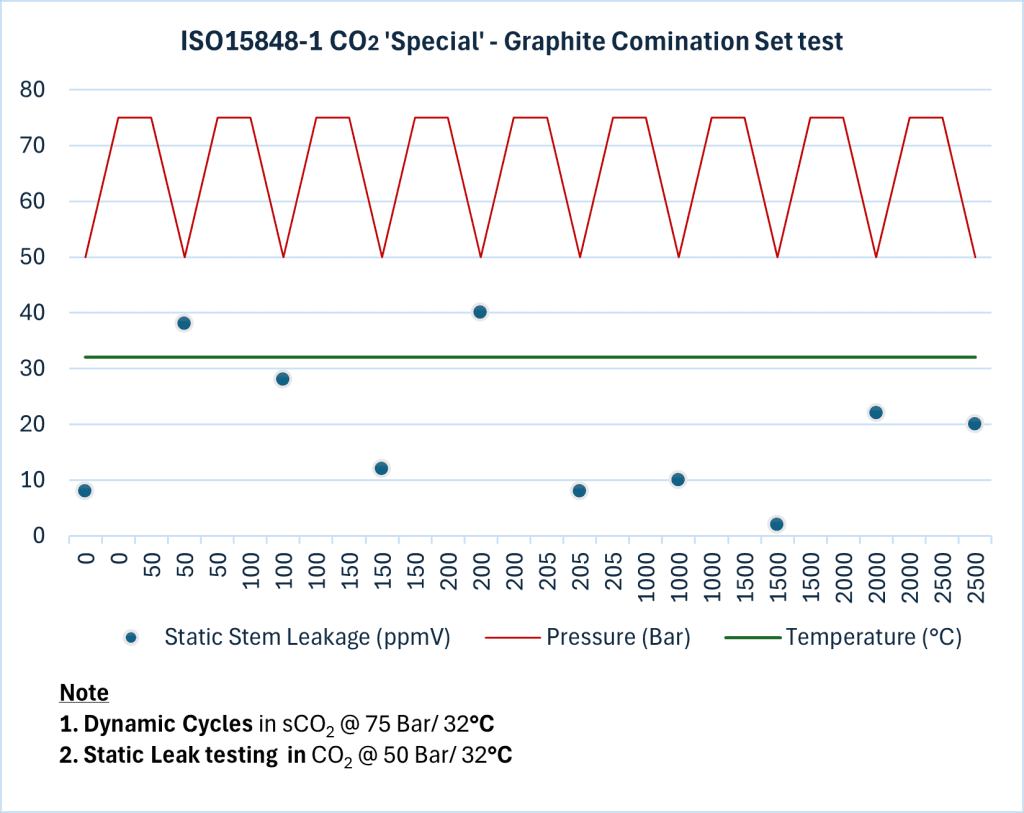
Validation of a packing solution
To tackle these challenges, high-quality, high-purity graphite, fugitive emissions rated combination packing ring sets can present an effective solution. Engineered to endure the harsh conditions of sCO2, these rings are thermally and mechanically stable and help to deliver exceptional fugitive emissions performance while effectively managing frictional behaviour.
Utilising such advanced materials ensures the sealing system maintains its integrity and reliability, guaranteeing long-term operational efficiency and safety. Currently, there are no established industry standards or specifications for evaluating the fugitive emission performance of compression packing in sCO2 applications. To address this gap, James Walker has worked in collaboration with industry-recognised test laboratories following the existing ISO 15848-1 standard and adapting the test media to using CO2 instead of the commonly used helium. By precisely controlling temperature and pressure, the phase transition to sCO2 can be achieved. Subsequently, pressure cycling and mechanical stem cycling are incorporated to execute a test sequence consistent with ISO 15848-1, thereby supporting the validation of packing products for sCO2 applications, with close monitoring of fugitive emissions and frictional behaviour of the packing during an extended testing period in line with a recognised industry format.
Although globally recognised testing standards don’t currently exist for assessing and validating products for the sealing of sCO2, production, handling and storage systems for this media are still subject to environmental regulations. These regulations, which vary by region, often impose limits on greenhouse gas emissions and mandate leak detection and repair (LDAR) programs with the risk of financial penalties or enforced shutdowns for non-compliance. Successful compression packing solutions must therefore not only fulfil operational requirements and comply with such regulations but also enhance product service life and minimise unplanned maintenance. By testing performance, under application specific conditions with the relevant media, we are providing customers with a fully validated product that not only matches the required regulatory performance but also contributes to the long-term reliability and efficiency of the production, handling and storage environment.
Current and future developments
Compression packing has been identified as a product that can be highly effective in preventing leakage in sCO2 valve applications, provided that appropriate materials are selected, proper design and installation practices are followed, and regular maintenance is conducted. It is critical to assess the packing’s performance under operational conditions to confirm its effectiveness in minimising fugitive emissions.
For the CCUS industry to progress and advances in technology to occur, ongoing innovation, research, and development of compression packing materials and packing set design will be essential. These activities will yield deeper insights that refine the design and application of compression packing systems, thereby enhancing the efficiency, reliability, and safety of CCUS technologies. It will be crucial to ensure that sealing solutions keep pace and can perform to the required levels straight out of the box. This will require packing solutions to undergo rigorous testing and validation to confirm their performance, ensuring readiness for future applications.
As part of our commitment to sustainability and environmental protection, James Walker is working at the forefront of developing compression packing sealing solutions suitable for sCO2 applications. Leveraging our product and testing expertise across several industry sectors such as oil and gas, and power, James Walker is validating solutions that tackle the unique challenges associated with sealing equipment processing sCO2 in CCUS systems, particularly gas transmission pipelines and valves.
Authors
Martin Coulthard, Group Manager – Gaskets, Rotabolt & Compression Packing
Rajib Roy, Product Manager Jakub Marczyk, Product Director www.jameswalker.biz
About this Technical Story
This Technical Story is an article from our Valve World Magazine, December 2024 issue. To read other featured stories and many more articles, subscribe to our print magazine. Available in both print and digital formats. DIGITAL MAGAZINE SUBSCRIPTIONS ARE NOW FREE.
“Every week we share a new Technical Story with our Valve World community. Join us and let’s share your Featured Story on Valve World online and in print.”