ASME gasket factors have been deployed in the design of flanges for over 80 years. Despite this, little is known about the evolution of their development. All the more reason to travel back in time and gain insight in their early use and subsequent development over the years.
By Randy Wacker
The source of this information is extracted principally from a book titled Pressure Vessel and Piping Design published by ASME. It includes a series of technical articles from the period 1927 to 1959. This article also includes information of a more current nature. It should in no way be interpreted as a disparagement of this present practice. It is intended though to draw some contrast between the deployment of ASME factors and more modern design techniques.
In 19341, M and Y values do not yet exist. Attempts to seal bolted flanges recognize the need for a minimum load to ‘seat’ the gasket, and the load to retain the seal at the internal working pressure.
Elusive concept
It is believed that for a given working pressure, the unit gasket stress needed to seal it, is some ratio of the working pressure. The concept of contact-pressure ratio is recognized as a potential defining factor to be used in flange design.
The authors of the ASME publication caution that this concept is an elusive one but acknowledge this as being in common usage. For a given gasket type, these concepts are later introduced into flange design as Y for the initial seating stress (originally called the yield factor) and M as the contact ratio. Specifically, they are later introduced as nonmandatory suggestions to derive the two required bolt loads for flange design.
Shortcomings
The authors of Gasket-Loading Constants (published in 19432) note the general success of the new rules governing flange design. However, critics of the method, and most particularly regarding the use of M and Y values note some shortcomings.
The mechanics of the action of gaskets is not well understood and the method does not take into account the effect of temperature on the gaskets. The authors concede that “the present gasket rules constitute an extreme simplification of the rather complex problem in which only some of the most elementary effects have received consideration.”
Other comments at the time reveal that experiments indicate that M and Y values are in fact not constants. Also, ASME is encouraged to reveal the methods used for determining M and Y values. No such validation appears.
Disconcerting
In the publication Gaskets and Bolted Joints (19503), the author points out that “it is disconcerting to find, in a survey of American literature, not a single paper which gives either the analytical or an experimental study of the gasket conditions which make for tightness of a bolted joint.”
It is hoped that a formal testing program will allow for a better definition of the concept of tightness. He points out the tightness of a joint is best defined based on some maximum allowable rate of leakage, and some criteria should be in place for a particular medium.
Years later, this gives rise to the concept of tightness class. In the case of EN 13555 testing, values L1.o, L0.1, L0.01, etc. For the Pressure Vessel Gasket Testing Group, they are identified as Class 1, Class 2, Class 3, etc. Markl contests that the original intent of design committee in incorporating M and Y values into the Code focused on flange strength.
Gasket tightness
At present, formalized gasket testing protocols have addressed the need for a scientifically based understanding of gasket properties and how they interact with the conditions to which they are exposed. Tightness takes on a mathematically substantiated meaning. In the case of Europe, gasket tightness is central to the design of flanged connections and has been adopted into the basis (EN 1591-1) of flange design since 2001.
Regretfully, this is not so much the case in America. Even though a formal gasket tightness testing protocol was established well over 25 years ago. In America, the Pressure Vessel Research Council (PVRC) method is available, to those who are aware of it, to identify tightness-based bolt loads for gasketed flanged connections. Figure 1 shows the generalized plot for EN13555 Testing. The required gasket stress associated with a particular value tightness is revealed.
Figure 2 shows the general PVRC testing relationships. Again, tightness is associated with a particular value of gasket stress. The values a, GB and GS are used to evaluate the particular value/class of tightness. In both instances, helium is the test medium. Adjustments for molecular weight and viscosity can be made for other mediums.
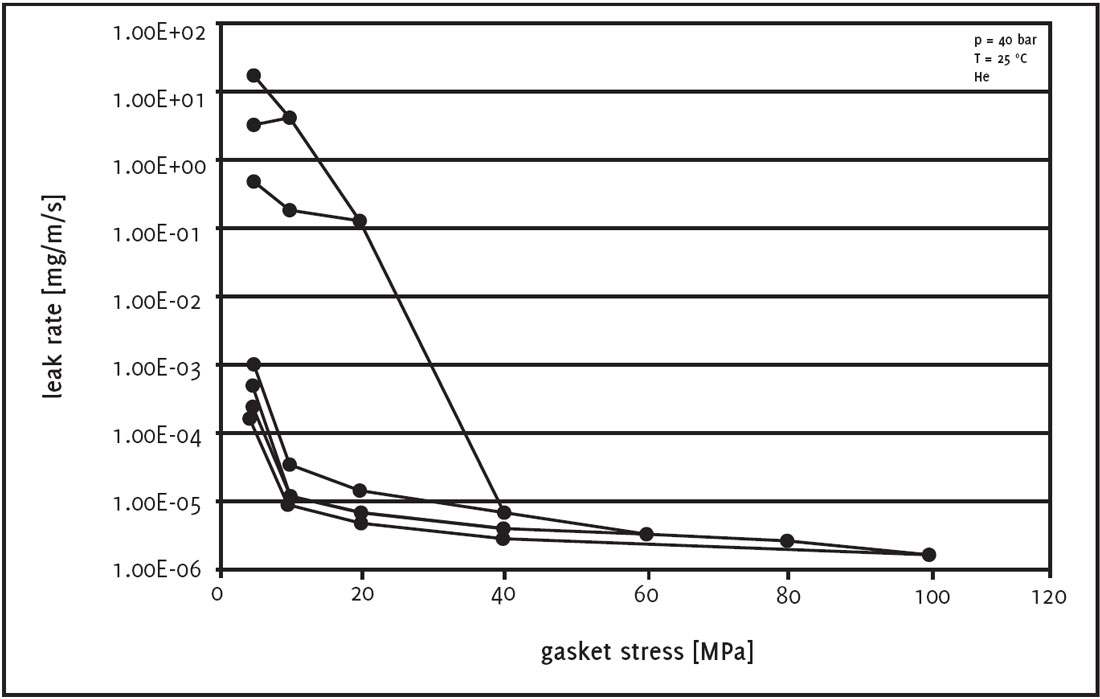
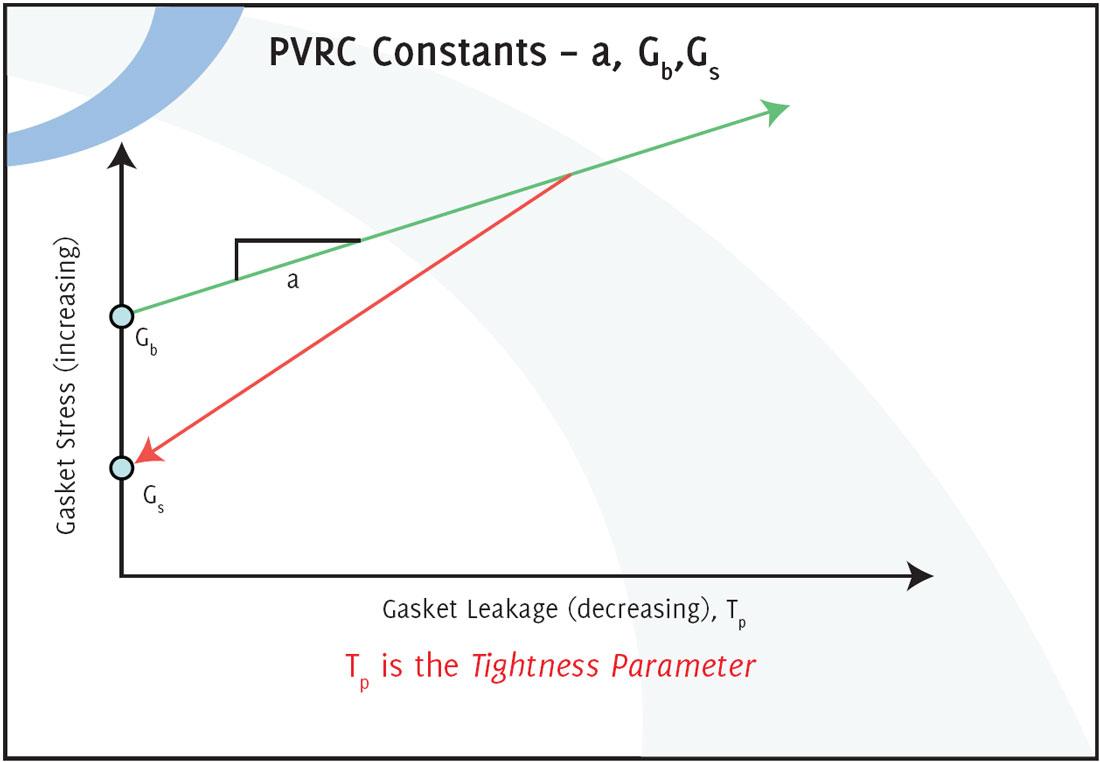
Conflict with ASME code
A Special Working Group was tasked with incorporating tightness-based bolt loads into the ASME pressure vessel code. In the book entitled, An Introduction to the Design and Behavior of Bolted Joints, 3rd edition, copyright 1995, it is suggested that the PVRC method may be adopted into ASME code by 1995.
Surprisingly, here in 2022 this is still not the case, though those familiar with the method have successfully deployed it for decades; over 20 years in the case of this writer and longer for others.
Just one of the reasons for the deployment of the PVRC method is because engineers recognize that bolt loads specified by M and Y values do not always result in satisfactory results. Higher than M and Y derived values are sometimes needed.
How is this not in conflict with the current ASME code? This condition has been recognized by the ASME and has been addressed in Section VIII, Division 1, Non mandatory Appendix S, Design Considerations for Bolted Flange Joints. With regards to tightness/leakage, it’s acknowledged that M and Y derived bolt loads may be inadequate for the task. Extracted from this appendix verbatim is the following: “… it is evident that initial bolt stress higher than the design load may and, in some cases, must be developed in the tightening operation … ”.
No resolve yet
In summary, the use of M and Y factors to seal bolted flange connections has been a success over many years. However, contemporary engineers who are using the ASME code and are familiar with the value/reliability of evoking tightness-based bolt loads will find themselves left to their own resources to deploy them.
There have been numerous technical attempts4 to study flange leakage and/or associate tightness with a given M and Y factor. Regrettably, the information developed by these efforts, or the efforts of the ASME Special Working Group have yet to be formally adopted into the pressure vessel code.
Tightness-based bolt loads remain elusive to the current ASME flange designer. Consequently, the modern ASME flange designers still lack a formal sense of what tightness class is best suited to their medium.
Reconciliation
Equally elusive is that they are left to their own resources to judge to what extent higher-than-design loads are within a safe margin of their particular circumstance. Hope continues that a reconciliation of these short comings will not be too far in the future.
The evaluation and mitigating of fugitive emissions can and should be within the grasp of current scientific method. M and Y factors and the associated calculation method, as can also be found in the main bodies of EN 13480-3 or EN 13445-3, are completely unsuitable for proof of tightness or for reducing fugitive emissions through the design of a flange connection. For this purpose, only the calculation algorithm of EN 1591-1 in conjunction with gasket characteristics according to EN 13555 can be used.
References
1. Design of Bolted Flange Connections by E.O. Waters, D.B. Wesstrom and Frank S.G. Williams.
2. Gasket-Loading Constants by D.B.Rossheim and A.R.C. Markl.
3. Gaskets and Bolted Joints by Irving Roberts.
4. Welding Research Council Bulletin (WRCB) 468 Leak Testing of Raised Face Welding Neck Flanges, WRCB 484 Gasketed Joint Leakage and Emissions. WRCB 233 Report on Gasket Factor Tests, WRCB 442 Polytetrafluoroethylene Gasket Qualification, WRCB 461 Experimental Leak Testing of 16-inch Class 300 RFWN with and without External Bending Moments, WRCB 271 Gasket Leakage Behavior ASTM F3149 Determining the Maintenance Factor M and the yield factor Y Loading Constants Applicable to Gasketed Materials and Designs.
About the author:
Randy Wacker, P.E., graduate of California Polytechnic University has over 40 years of experience in the design, specification, maintenance and troubleshooting of process equipment. He is currently a Senior Consultant for Inertech, Inc. and member of the ESA Flange Gaskets Division.