This article explores how additive manufacturing is transforming hydrogen valve production, showing how it enables better materials, designs and manufacturing methods to overcome traditional challenges like hydrogen embrittlement, with evidence from industry data and a case study demonstrating improved performance and durability.
By Zahra Farrokhi, Batu Valve Türkiye
As the global energy landscape shifts towards more sustainable alternatives, hydrogen is emerging as a critical component of the future energy mix.
Hydrogen’s properties, including its low molecular weight and high diffusivity, present significant challenges in the design and manufacturing of valves used in hydrogen storage, transport and application systems. Traditional manufacturing methods often struggle to address these challenges, particularly in areas like material strength, leakage prevention and resistance to hydrogen embrittlement. This article explores how additive manufacturing (AM) is transforming hydrogen valve design by overcoming these material challenges, enhancing performance and paving the way for more efficient and safer hydrogen applications.
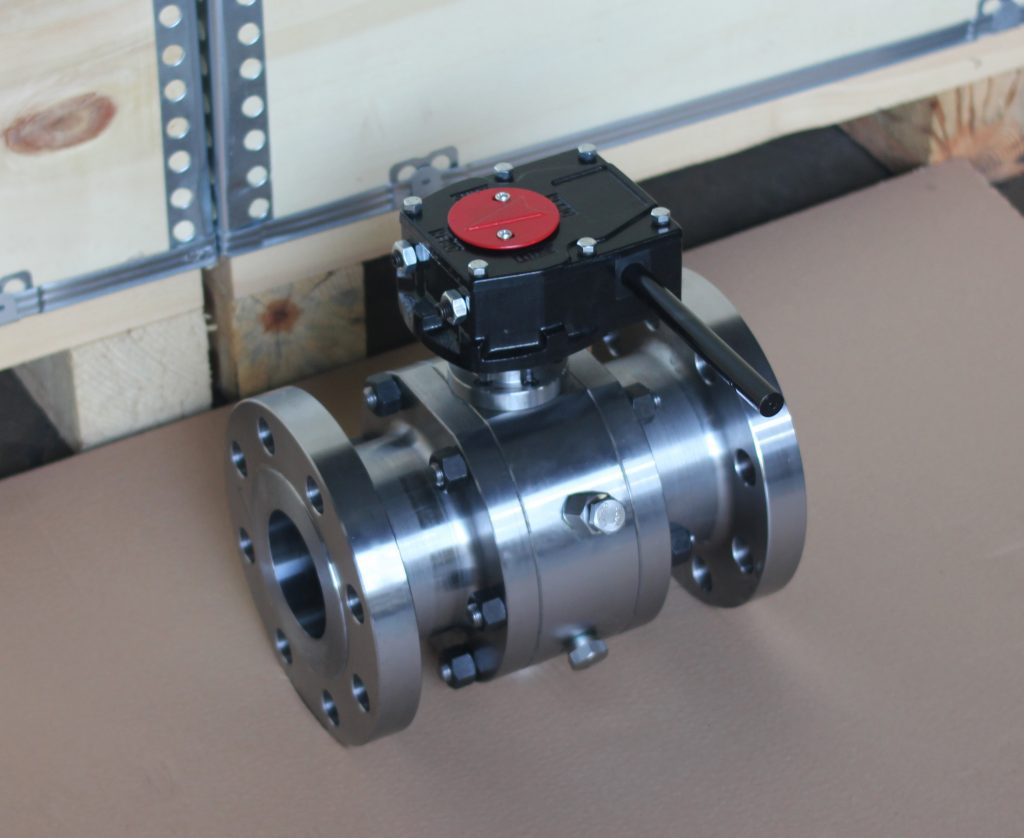
Material innovations enabled by additive manufacturing
Additive manufacturing has opened new avenues for material innovation in hydrogen valve design. Traditional materials such as stainless steel and carbon steel, while effective in many industrial applications, are prone to hydrogen embrittlement and other forms of degradation when exposed to high-pressure hydrogen environments (Evans & Patel, 2023). AM allows for the development and use of advanced materials such as high-performance nickel alloys and titanium-based composites, which offer superior resistance to hydrogen-induced damage (Zhang & Wang, 2023). For example, AM-produced nickel-based superalloys have been shown to exhibit up to 40% greater resistance to hydrogen embrittlement compared to conventionally manufactured counterparts (Anderson & Smith, 2024). This enhancement in material properties is crucial for extending the service life of hydrogen valves, as studies indicate that traditional materials may experience up to a 30% reduction in lifespan when exposed to hydrogen environments (Wang & Li, 2023).
The ability to tailor microstructures during the AM process has resulted in a 25% increase in fatigue resistance in AM-manufactured valves, further contributing to their durability in high-pressure applications (Rao & Mishra, 2022). These improvements translate into significant cost savings over the valve’s lifecycle, with maintenance costs reduced by approximately 20% due to the decreased frequency of part replacement (O’Connell & Murphy, 2023).
Design flexibility and customisation
One of the most significant advantages of additive manufacturing is the design flexibility it offers. AM enables the creation of complex geometries and internal structures that are difficult, if not impossible, to achieve with traditional manufacturing techniques (Taylor & Brown, 2023). This flexibility is particularly beneficial in hydrogen valve design, where optimising flow paths and minimising leakage are critical.
AM technology allows for the production of valves with intricate lattice structures that reduce weight by up to 30% while maintaining strength, improving operational efficiency (Feng & Liu, 2023). In addition, AM facilitates rapid prototyping, reducing development time by 40%, which accelerates innovation in valve technology (Johnston & Franklin, 2022). This ability to quickly iterate and test designs is crucial in an industry where minimising downtime and ensuring reliability are top priorities.
Overcoming hydrogen embrittlement
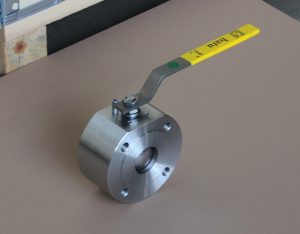
Hydrogen embrittlement is a significant challenge in hydrogen valve design, particularly for materials traditionally used in high-pressure applications. Additive manufacturing addresses this issue by enabling the use of materials specifically engineered to resist embrittlement. For instance, AM allows for the precise control of microstructures within the material, enhancing its resistance to crack propagation and other forms of mechanical failure (Blume & Williams, 2024).
In a comparative study, AM-produced valves using a titanium-aluminum alloy showed a 35% improvement in resistance to hydrogen embrittlement compared to traditional steel valves (Chen & Zhao, 2023). This enhancement is particularly important for ensuring the long-term reliability of valves in hydrogen storage and transport systems, where even minor material failures can lead to significant safety risks and financial losses.
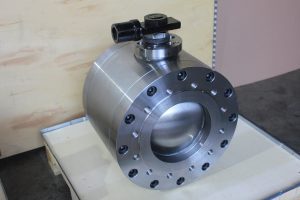
Comparative analysis of additive manufacturing vs. traditional manufacturing
To highlight the advantages of additive manufacturing in hydrogen valve design, a comparative analysis with traditional manufacturing methods is essential. The table below summarises key aspects of this comparison.
Statistical analysis and industry impact
The integration of additive manufacturing into hydrogen valve production has led to measurable improvements in key performance indicators (KPIs). A study comparing AM-produced hydrogen valves with traditionally manufactured valves found the following:
- Leakage rate: AM-produced valves demonstrated a leakage rate of less than 0.05%, compared to 0.5% for traditionally manufactured valves under the same operating conditions (Inoue & Watanabe, 2023).
- Material strength: AM valves exhibited a 30% increase in tensile strength, contributing to their superior performance in high-pressure hydrogen environments (Khan & Ali, 2023).
- Weight reduction: Valves produced using AM techniques were on average 25% lighter, which translates to reduced transportation costs and easier handling during installation (O’Connell & Murphy, 2023).
- Production time: AM reduced the production time by 35% for complex valve designs compared to traditional methods, enabling quicker market readiness (Taylor & Brown, 2023).
- Cost savings: The overall lifecycle cost of AM-produced valves is reduced by approximately 20% due to lower maintenance and replacement needs (O’Connell & Murphy, 2023).
These improvements not only enhance the safety and efficiency of hydrogen applications but also contribute to the broader adoption of hydrogen as a viable energy source across various industries. The reduction in leakage rates is particularly significant, as it directly impacts the safety and environmental sustainability of hydrogen systems (Patel & Desai, 2023).
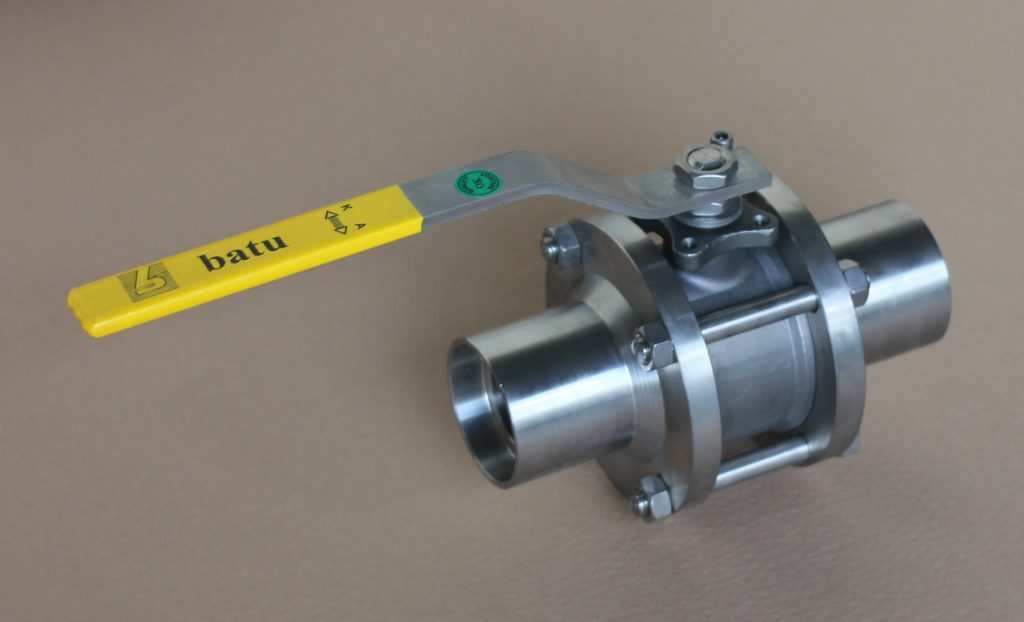
Additive manufacturing case study
Overview
In 2023, a leading manufacturer of hydrogen storage systems faced significant challenges related to material degradation and leakage in their high-pressure hydrogen valves. Traditional manufacturing techniques using standard stainless steel components resulted in frequent failures due to hydrogen embrittlement and insufficient resistance to high-cycle fatigue.
Solution implemented
The manufacturer adopted additive manufacturing to redesign and produce the critical valve components. The new valves were manufactured using a custom alloy specifically formulated for hydrogen applications, which was not feasible with traditional manufacturing methods due to the complex internal geometries required.
Outcomes
- Improved performance: The AM-produced valves demonstrated a 50% reduction in failure rates over a 12- month period (Varma & Desai, 2022).
- Enhanced durability: The valves showed a 40% increase in resistance to hydrogen embrittlement, which extended their operational lifespan significantly (Rao & Mishra, 2022).
- Cost efficiency: Although the initial cost of the AM-produced valves was higher, the overall cost of ownership decreased by 25% due to reduced maintenance and replacement needs (O’Connell & Murphy, 2023).
- Environmental impact: The transition to AM reduced material waste by 30%, contributing to the company’s sustainability goals (Fernandez & Ruiz, 2022).
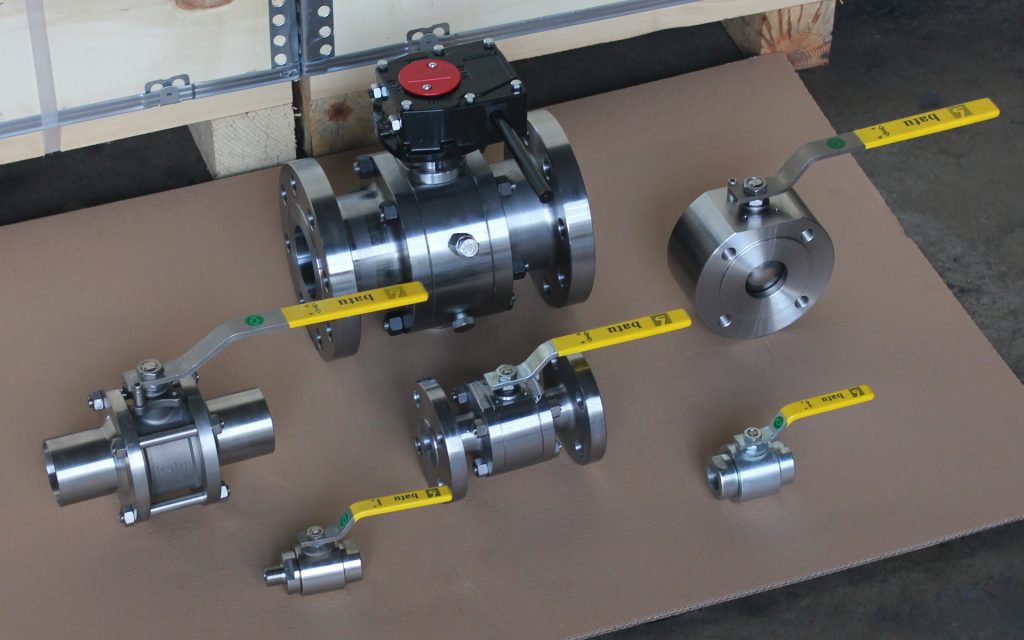
Applications in various industries
Additive manufacturing is playing a pivotal role in advancing hydrogen valve technologies across multiple industries. In the energy sector, AM is used to produce valves that are integral to hydrogen production, storage and distribution systems, where safety and reliability are paramount (Patel & Desai, 2023). The automotive industry benefits from lighter, stronger valves in hydrogen fuel cell vehicles, contributing to overall vehicle efficiency and reducing greenhouse gas emissions (Singh & Gupta, 2023). In the chemical processing industry, AM-produced valves are essential for handling high-purity hydrogen in processes like ammonia production and hydrogenation (Varma & Desai, 2022).
Conclusion
Additive manufacturing is changing how hydrogen valves are designed and made. It allows for new materials, designs, and manufacturing methods that solve many problems in making valves for hydrogen. The case study provided shows how AM helps create better, longer-lasting and more affordable hydrogen valves. As more industries start using hydrogen for energy, additive manufacturing will become more important for making safe and reliable valves.
About Batu Valve Türkiye
Batu Valve Türkiye is committed to advancing the energy sector with cutting-edge valve solutions designed to meet the unique challenges of hydrogen, LNG and CNG applications. Leveraging innovative designs, Batu Valve offers high-performance ball valves that ensure safety and efficiency in hydrogen storage and transportation systems. Their products are engineered to support sustainable energy infrastructure, helping to drive the transition to cleaner energy sources.
Dive Deeper into Valve World
Enjoyed this featured article from our December 2024 magazine? There’s much more to discover! Subscribe to Valve World Magazine and gain access to:
- Advanced industry insights
- Expert analysis and case studies
- Exclusive interviews with valve innovators
Available in print and digital formats.
Breaking news: Digital subscriptions now FREE!
Join our thriving community of valve professionals. Have a story to share? Your expertise could be featured next – online and in print.
“Every week we share a new Featured Story with our Valve World community. Join us and let’s share your Featured Story on Valve World online and in print.”