New technologies, such as additive manufacturing, are an essential element in the development of new, innovative products and product parts.
AM offers a wide variety of new opportunities that exceed those of the traditional subtractive manufacturing methods. In this progress report, we will use SAMSON as an example and shine a light on the challenges that companies face while implementing additive procedures in R&D and manufacturing as well as the opportunities that such technologies involve.
By Holger Eckholz (SAMSON AG), Domagoj Vnucec (SAMSON AG), Martin Boche (TÜV SÜD Industrie Service GmbH)
SAMSON operates wherever there is controlled flow of oils, gases, vapors or chemical substances. This means that control valves are used in different applications and fields of industry, such as chemicals and petrochemicals, oil and gas or industrial gases. The control valves need to stay capable of meeting the requirements that apply in these applications also in the long term. As a result, the company’s first-rate process automation products are continually upgraded by integrating innovative developments in digitalization, flow simulations, design and control engineering. Even though some restrictions still apply, the freedom of part design granted by additive manufacturing makes it possible to create highly complex geometries that would be impossible to implement using traditional machining methods. Design opportunities are unprecedented. This applies in particular to valve parts exposed to high levels of wear and tear or parts that help reduce noise emissions (see Figs. 1 and 2).
Bonus
The same is true for valve sections to be heated up or cooled down as well as for areas where flows are mixed or distributed. Once an additive manufacturing process has been established, new ideas and approaches are developed, which results in entirely new products or upgrades of existing products being created.
Control equipment for special, complex applications is often ordered in small quantities. As a result, having in place special additive manufacturing procedures is a bonus since they complement the series manufacturing processes, which cater for large order quantities. This also includes the additive manufacturing of spare parts that have gone out of stock and would otherwise take much longer to be delivered.
Thanks to optimized part topologies, the weights of some parts can be reduced considerably (see Figs. 3 and 4). Product weight is becoming an increasingly important aspect in many sectors of industry. Currently, there is no other method than additive manufacturing to create such complex geometries with optimized topologies.
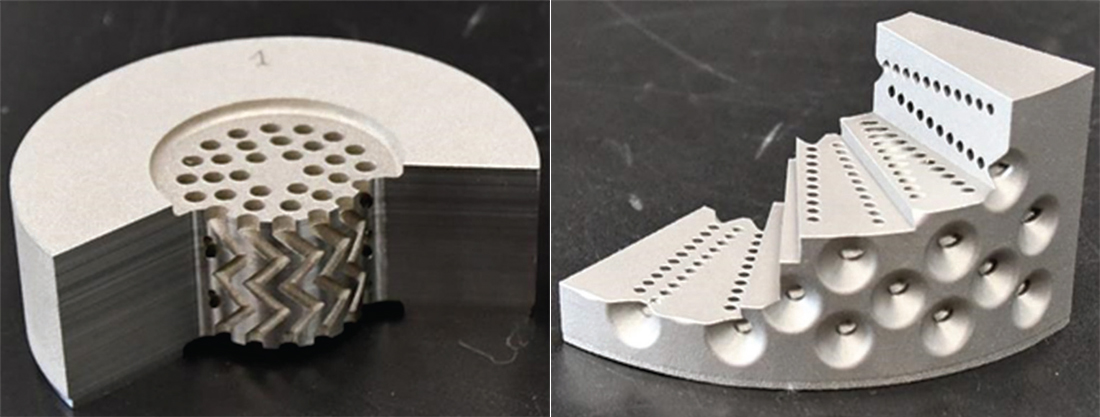
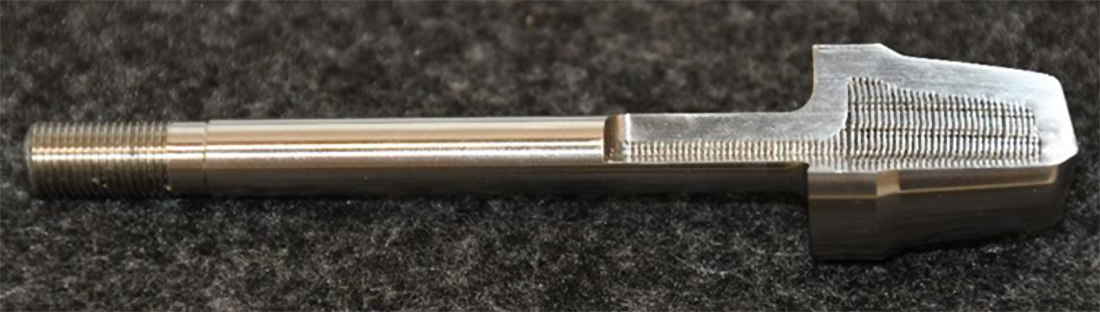
AM: from design to reality
In addition, supplementing additive manufacturing with subtractive manufacturing methods is favorable or even required regarding the necessary post-processes to machine-finish the manufactured part. Another benefit is the decade-long experience accumulated in the design departments, which makes it possible to rapidly draft optimized CAD models to meet additive manufacturing requirements.
The term ‘additive manufacturing’ not only refers to a new manufacturing procedure as in subtractive manufacturing, it also covers the entire process: starting with manufacture-optimized machining of a digital 3D model, to the actual printing process of the real-life part, the post-printing process and part qualification. The additive manufacturing methods currently available on the market all have their very own benefits and drawbacks in terms of material purity, mechanical and technological properties, manufacturing accuracy and suitability for the finished products and future applications.
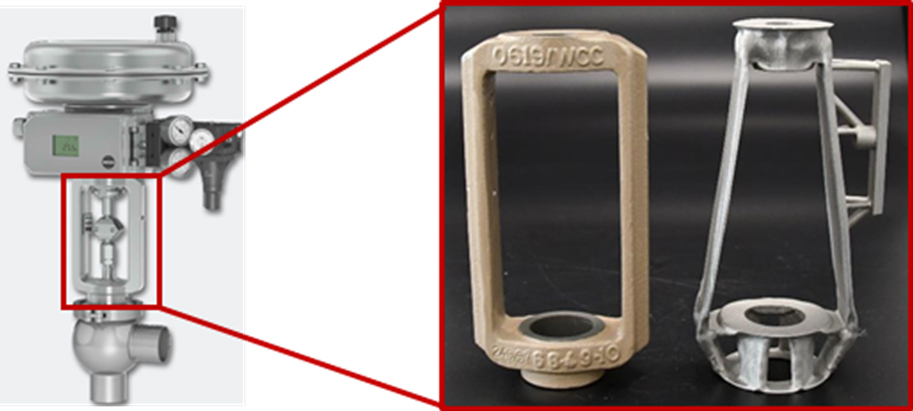
Laser-based powder bed fusion
In valve engineering, the laser-based powder bed fusion method for metals (LB-PBF-M) is the most favorable since it enables manufacturers to comply with the material property and purity requirements according to the European Pressure Equipment Directive (PED) and additionally provides full flexibility relating to the implementable geometries.
Powder bed fusion is a procedure where parts are built by fusing together metal powder particles layer by layer. A laser beam moves along certain paths to create the desired geometry by melting together layer after layer of powder in an inert gas atmosphere. No binders are used in the procedure and very high densities of over 99 % can be achieved.
The same quality requirements as for traditional semi-finished products must be complied with when using additive manufacturing of semi-finished products. This applies in particular to the mechanical and technological quality criteria compared to cast, forged or rod materials and their reproducibility, for example. On top, the specifications stipulated in the PED must be observed.
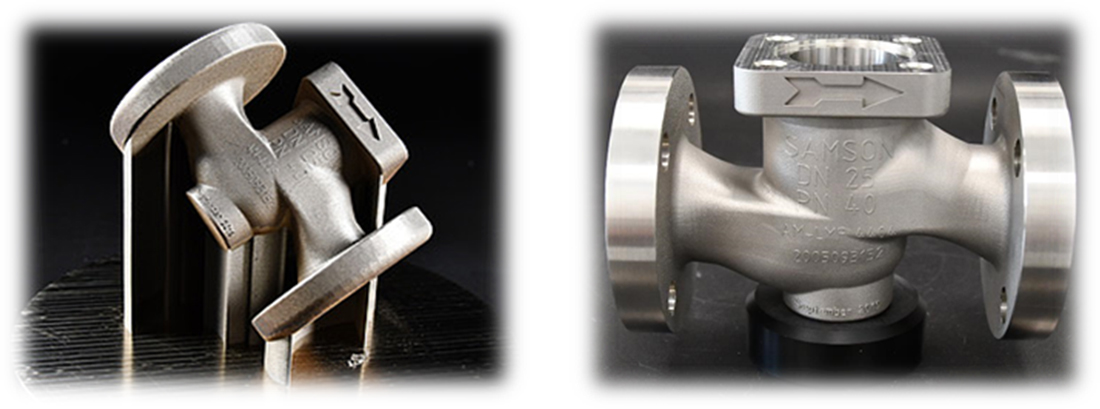
No standards
To guarantee an adequate safety level for pressure equipment, the PED prescribes that appropriate design calculations must be performed to establish the strength of the pressure equipment concerned. Relating to material properties, these calculations must be based on verifiable data. Normally, harmonized European material standards for pressure equipment serve as the basis in this case.
For additively manufactured materials, however, such standards do not exist unfortunately. This is because the material itself does not exist until it is created from the powder feedstock in the print job that is run on the machine with the mechanical and technological properties that are characteristic of the machine and its set of parameters. As a result, there is a requirement to verify the properties of the additively manufactured material by performing destructive and non-destructive tests on it and to record and statistically analyze the results in a continuously expanding database.
PMA
The measured minimum material properties (including a safety factor) of the material that was additively manufactured by SAMSON are ultimately recorded in detail in a material specification sheet. Compliance with the specified minimum values is continuously demonstrated by destructive testing on specimens printed along with the actual material as well as by non-destructive testing on the parts themselves.
This opens up an alternative path specified in the PED, which involves a particular material appraisal (PMA) for pressure equipment. Regardless of this path, pressure equipment manufacturers must always create a PMA. The major benefit of a PMA is that pressure equipment manufacturers can directly reference the material specifications of the additively manufactured material as the basis for its mechanical and technological properties. Additionally, who makes the additively manufactured semi-finished product can document the material properties in a 3.1 certificate or, in cooperation with a notified body, a 3.2 certificate.
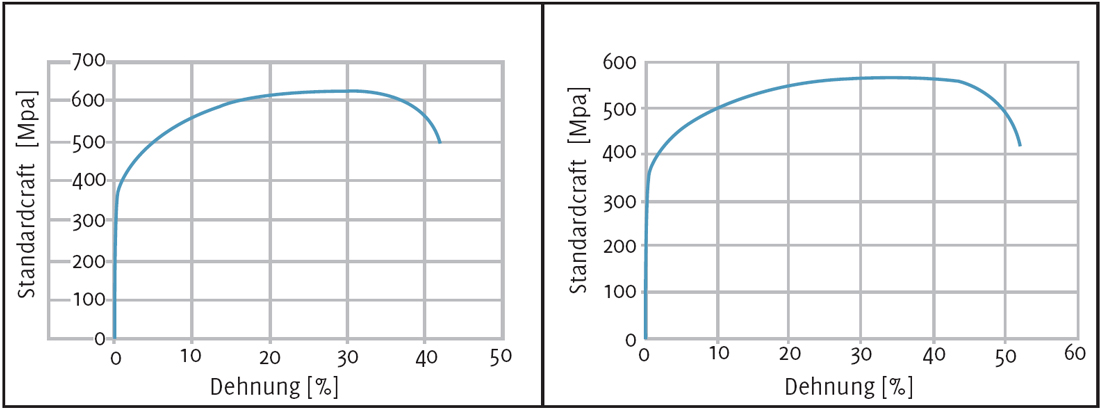
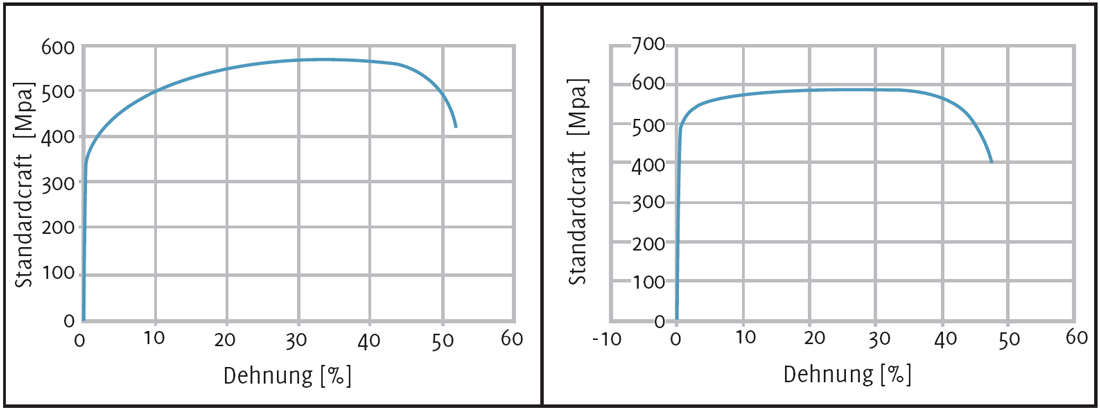
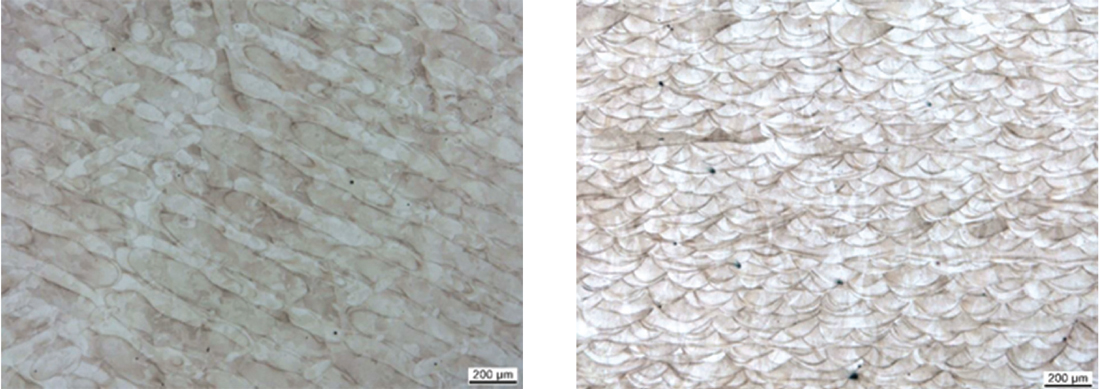
Comprehensive quality assurance
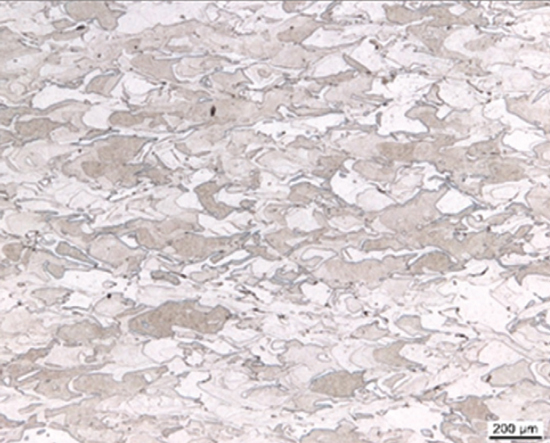
XY layer. Recrystallized molecular structure with dissolved layer structure. No melt lines visible.
The fundamental requirements to be complied with in this context include putting in place comprehensive quality assurance systems for the powder feedstock, incoming goods inspections, qualification of the material used for the additive manufacturing method, qualification of the manufacturing parameters, staff qualification and lab testing.
Any variations in the technological properties that may occur across the machine’s building chamber as well as anisotropies depending on the build-up direction must be recorded, analyzed and taken into account.
Subsequent heat treatment also leads to different material properties than in the pure as-built condition of the material (see Figs. 6 to 9). The well-established internal processes to handle quality assurance and quality control are to be applied to the new manufacturing method as widely as possible. And they also need to be expanded to ensure that the order fulfilment processes run smoothly. Accordingly, cross-departmental design guidelines, company standards, testing instructions, quality assurance documents and work plans need to be created; responsibilities must be defined and the processes are to be implemented in the corporate ERP system.
Challenging
During the associated qualification and certification processes, TÜV SÜD Industrie Service supported SAMSON as the notified body. Up until now, additively manufactured parts have mostly been subjected to visual inspections. The PED, however, places prime importance on the materials’ mechanical properties as well as on the absence of faults on the inner and outer surfaces of the semi-finished products. Documenting compliance of the additively manufactured products with the applicable European laws and regulations can be challenging at times. For example, there are often no sound statistics on the variations in the mechanical and technological properties that occur during manufacturing. Particularly when it comes to safety-related parts, the influence of these variations in the mechanical and technological properties across the building chamber that affect the parts must be clarified. This means that the mechanical strength of the parts depends on their position within the building chamber. Consequently, the properties’ variation range must be taken into account when preparing for a print job.
New qualification and certification program
A new qualification and certification program by TÜV SÜD Industrie Service takes into account the general safety requirements of the PED as well as the application within the meaning of EN 13445-4 (Unfired pressure vessels – Part 4: Fabrication). Additionally, the know-how and experience of material scientists and welding experts were taken into account to reveal frequently encountered problems and develop best practice scenarios. As a result, the the program creates a reliable basis for assessing and certifying the quality of the additive manufacturing processes.
At the end of February 2021, SAMSON was audited and certified as an additive manufacturer for semi-finished parts in accordance with Annex I (4.3) of the PED 2014/68/EU. As a result, SAMSON has a certified quality management system for the additive manufacturing of semi-finished products (materials). This enables SAMSON to manufacture pressurized equipment from 1.4401/316 and 1.4404/316L austenitic stainless steels also using the additive LB-PBF-M laser-based powder bead fusion for metals method.
About this Featured Story
This Featured Story is an article from our Valve World Magazine March 2022 issue. To read other featured stories and many more articles, subscribe to our print magazine.
“Every week we share a new Featured Story with our Valve World community. Join us and let’s share your Featured Story on Valve World online and in print.”