In this article, JGC addresses the challenges surrounding valve interlocking devices, highlighting discrepancies between components and the need for collaborative solutions. In addition, the burgeoning demand for 3D printing in construction is explored, offering a solution to labor shortages and quality concerns.
By Tatsuya Tobe, JGC Corporation
In the realm of valve engineering, precision and reliability are paramount. However, the landscape is not without its challenges. From mismatched components to complex procurement processes, the industry faces hurdles that demand creative solutions. In this exploration, we delve into the intricacies of valve operations, the transformative potential of 3D printing in construction, and the quest for standardization within the framework of JIP33.
Findings: pain points of valves with interlocking devices
Valves with interlock devices are important to perform valve open and close sequence properly. We faced that valve stem nuts and adapters were not matched at the construction site. Adapters were made by interlocking device vendors to match with the valve stem nuts as per the valve vendor drawings. However, the drawings and actual stem nut dimensions were different (see Fig.1). Now new improvement is expected from EPC side. For example, valve stem nut dimension check for all valves at valve vendor factory regardless of whether some valves are actually used for interlock devices or not, this is traditional method and may not be practical for valve vendors.
For future improvement, 3D scanner will be used to measure the actual valve stem nut dimensions, and the adapters will be made by 3D printing to match with the actual valve stem nuts at the construction site by EPCs. There are several improvement chances to prevent from same pain points. EPCs, valve vendors, and interlock device vendors collaboration is important for the new improvement.
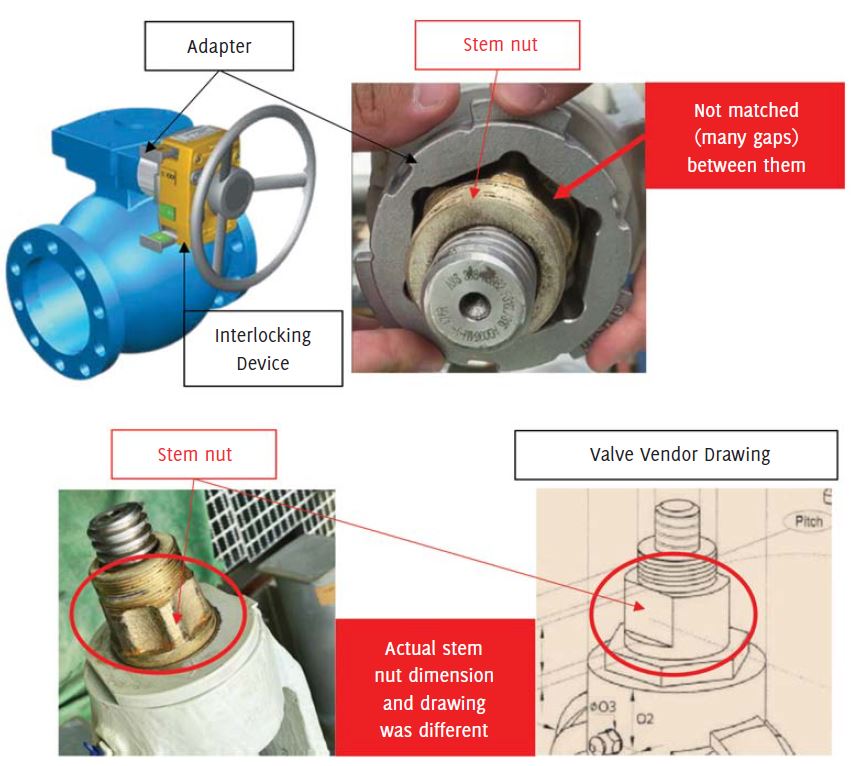
New demand: 3D printing
So why do we view 3D printing as a new demand? Because there are several challenges posed at the construction stage. There are many workers on the construction site, however, skilled workers are limited and there is a shortage of them. Furthermore, workers make things by hand manually. Each worker’s skill and the quality of their work may not be the same. So, there is a risk in the quality of manual work. Therefore, we are accelerating the use of 3D printing in construction as our new demand. Initially, we are applying 3D printing for concrete foundation work (see Fig.2).
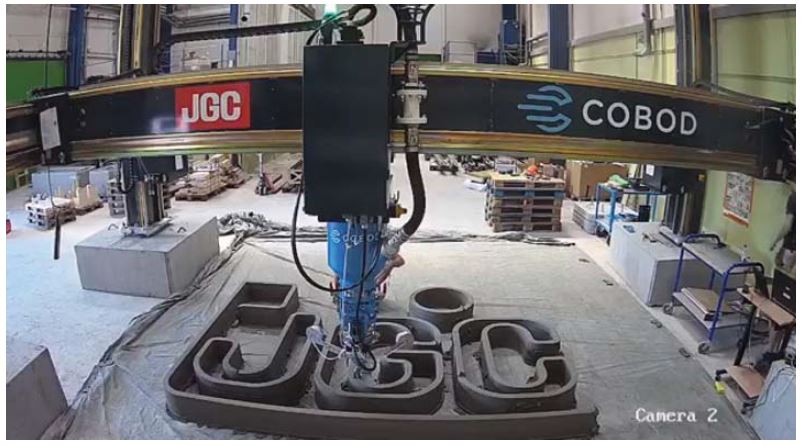
Also, we are applying 3D printing for metal piping components using WAAM (Wire and Arc-based Additive Manufacturing) technology (see Fig.3). Generally, 3D printing has several potential merits in terms of reducing lead time, ensuring consistent quality, allowing for flexible design and saving workers.
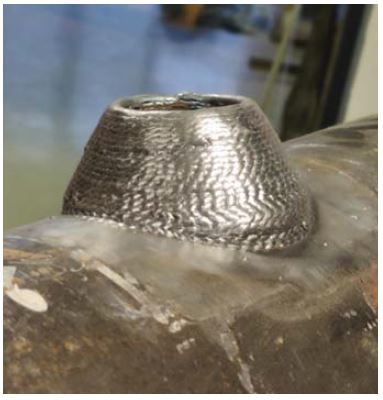
For example, piping spools require many construction steps such as cutting and welding. When 3D printing is used, these steps could be drastically reduced. When we use the large-scale 3D printing to make equipment and structures, we can achieve involving less workers. From vendors’ point of view, vendors manufacture products at their factories. After the manufacturing is completed, these products are shipped for a 1 or 2-month period. This manufacturing process, including shipment, is repeated.
So, we need to consider the shipping period in the EPC schedule. In the future, when the products are manufactured by 3D printing, the 3D data could be sent directly to the construction site. The shipping period may not be necessary with 3D data. We do not think that all manufacturing methods will be completely changed to 3D printing. We expect that the best combination of vendor manufacturing and vendor 3D data sent to the construction site will be a key point in the future to reduce the lead time of products for the construction site.
From the end-users’ point of view, they have started using 3D printing for several parts in timely maintenance due to supply chain considerations, and end-users also have a need for pressure vessels manufactured by 3D printing. So, we need to respond to end-user needs from the EPC side.
New challenges: standardizing identification codes in JIP33
Before JIP33, we had many different specifications project by project, and we repeated vendor technical bid evaluations using the different specifications. This proved to be an inefficient approach for end-users, EPCs and vendors. After JIP33, we have the standardizing procurement specifications regardless of project. There are no more different specifications project by project and end-user by end-user.
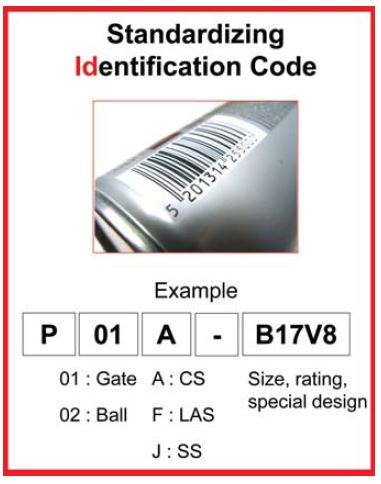
This could be efficient approach for all parties. For manual valves, we have the standardizing procurement specifications for gate and ball valves in JIP33 now. Such as gate and ball valves, we basically call bulk valves as a common word. Bulk valves mean same designed valves, but not one by one design such as pressure vessels. Imagine how many bulk valves will be purchased in one PJ? Normally around total 10,000 bulk, which are not all the same. Depending on valve type, size and rating, the number of bulk valves is different. And they’re not purchased all at once, the purchasing will be done step by step such as 1st purchase order and 2nd purchaser order depend on the EPC detailed schedule. So, bulk valve purchasing is very complicated and difficult to manage for EPCs and vendors. To improve this situation and for more effective use of JIP33, we need one more function for real procurement and management with JIP33. This could be Standardizing Identification Code (Standard ID) (see Fig.4).
Now the purchasing specifications are standardizing but IDs are not standardizing. This may be inefficient for real procurement with JIP33. So, the solution could be to propose standard ID for bulk valves in JIP33 as a new function. Standard ID will be a uniform code for all projects with each valve having a designated standard ID. Same valve will have same standard ID always.
Now the purchasing specifications are standardizing but IDs are not standardizing. This may be inefficient for real procurement with JIP33. So, the solution could be to propose standard ID for bulk valves in JIP33 as a new function. Standard ID will be a uniform code for all projects with each valve having a designated standard ID. Same valve will have same standard ID always.
Then, we could manage each bulk valve simply by standard ID. We expect that all bulk valves as per JIP33 standardizing procurement specifications could be linked by standard ID. Standard ID will be marked on the actual bulk valves, and we can see real JIP33 valves by standard ID. While this is still just a general concept, this may prove to be a tremendous challenge in the future. But the efficiencies through standardizations will be a demand in oil and gas industry in general.
Therefore, standard ID could be on trend. And standard ID has a potential to apply to other bulk materials such as pipes, fittings and flanges. To achieve them, communication with end-users, EPCs, and vendors is an important key point.
About the author
Tatsuya Tobe graduated with a bachelor’s degree of aerospace engineering and is a piping material engineering group manager at JGC Corporation, the largest process plant EPC contractor in Japan. For the last 23 years, his career has been working at piping engineering, especially for material engineering. The experience covers various categories thru basic engineering phase to construction phase, such as material selection based on fluid service, specifying project requirements, manufacturer selection, surveillance, and audit, mainly at natural gas and petrochemical plant projects.
About this Featured Story
This Featured Story is an article from our Valve World Magazine, March 2024 issue. To read other featured stories and many more articles, subscribe to our print magazine. Available in both print and digital formats. DIGITAL MAGAZINE SUBSCRIPTIONS ARE NOW FREE.
“Every week we share a new Featured Story with our Valve World community. Join us and let’s share your Featured Story on Valve World online and in print.”