Yokogawa Electric Corporation and JSR Corporation have conducted a field test in which AI was used to autonomously run a chemical plant for 35 days, a world first. “This test confirmed that reinforcement learning AI can be safely applied in an actual plant and demonstrated that this technology can control operations that have been beyond the capabilities of existing control methods such as PID and/or APC).
Control in the process industries spans a broad range of fields, from oil refining and petrochemicals to high-performance chemicals, fiber, steel, pharmaceuticals, foodstuffs, and water. All of these entail chemical reactions and other ele-ments that require an extremely high level of reliability.
“In this field test, the AI solution successfully dealt with the complex conditions needed to ensure product quality and maintain liquids in the distillation column at an appropriate level while making maximum possible use of waste heat as a heat source. In so doing it stabi-lized quality, achieved high yield*4, and saved energy. While rain, snow, and other weather conditions were significant factors that could disrupt the control state by causing sudden changes in the atmospheric temperature, the products that were produced met rigorous standards and have since been shipped. Fur-thermore, as only good quality products were created, fuel, labor, time, and other losses that occur when off-spec products are produced were all eliminated.”
Conflicting targets
The AI used in this control experiment, the Factorial Kernel Dynamic Policy Programming (FKDPP) protocol, was jointly developed by Yokogawa and the Nara Institute of Science and Technology (NAIST) in 2018, and was recognized at an IEEE International Conference on Automation Science and Engineering as being the first reinforcement learning-based AI in the world that can be utilized in plant management.
Through initiatives including the successful conduct of a control training system experiment in 2019, and an experiment in April 2020 that used a simulator to recreate an entire plant, Yokogawa has confirmed the potential of this autonomous control AI and advanced it from a theory to a technology suitable for practical use. It can be used in areas where automation previously was not possible with conventional control methods (PID control and APC), and its strengths include being able to deal with conflicting targets such as the need for both high quality and energy savings.
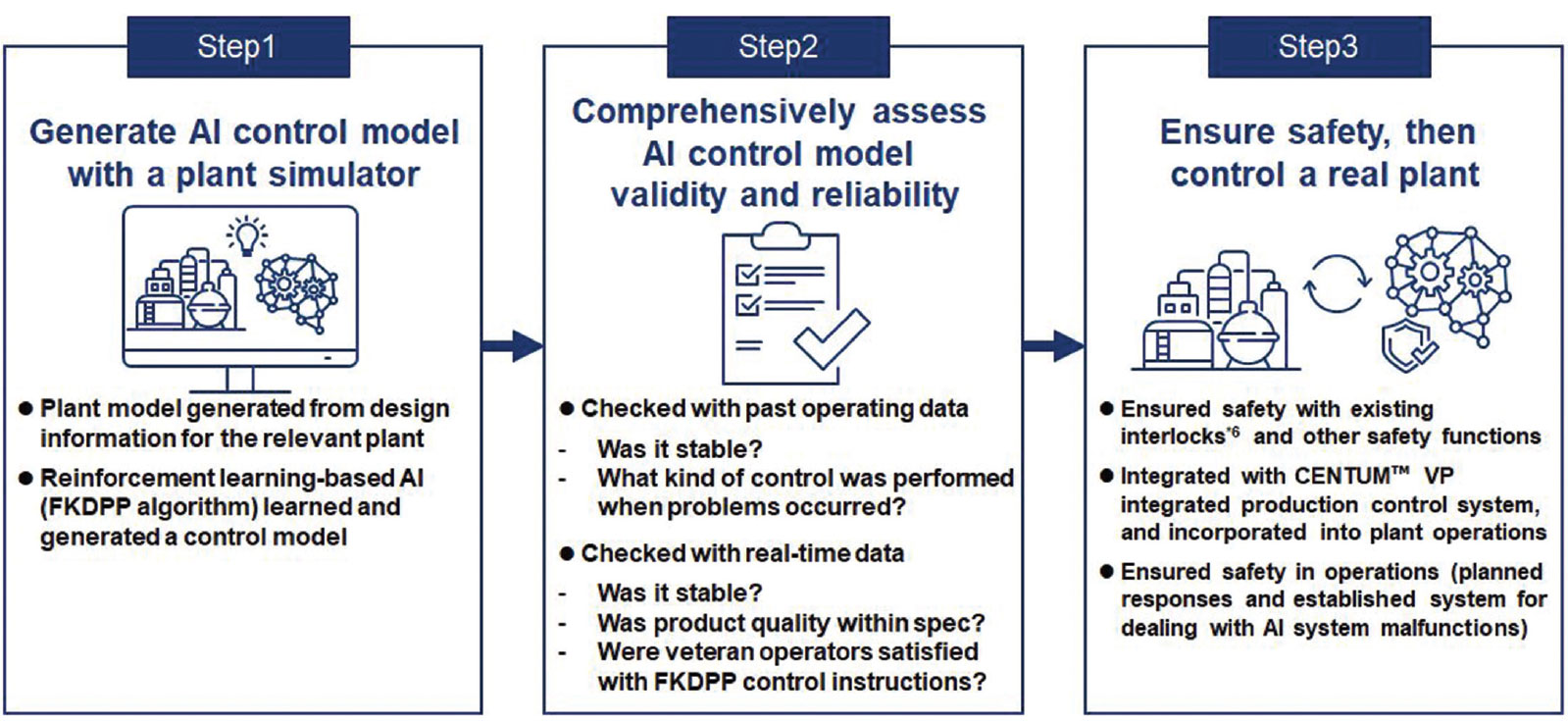
Complex phenomena
Given the numerous complex physical and chemical phenomena that impact operations in actual plants, there are still many situations where veteran operators must step in and exercise control.
“Even when operations are automated using PID control and APC, highly-experienced operators have to halt automated control and change configuration and output values when, for example, a sudden change occurs in atmospheric temperature due to rainfall or some other weather event. This is a common issue at many companies’ plants.”
Regarding the transition to industrial autonomy, a very significant challenge has been instituting autonomous control in situations where until now manual intervention has been essential and doing so with as little effort as possible while also ensuring a high level of safety. The results of this test suggest that this collaboration between Yokogawa and JSR has opened a path forward in resolving this longstanding issue, both companies state.
Under pressure
Yokogawa welcomes customers who are interested in these initiatives globally. The company aims to swiftly provide products and solutions that lead to the realization of industrial autonomy. JSR believes that this demonstration shows AI’s potential for addressing challenges that previously could not be resolved at chemical plants. The company will investigate its application to other processes and plants with the aim of achieving further improvements in productivity. Going forward, the two companies will continue to work together and investigate ways of using AI in plants.
Masataka Masutani, general manager of production technology at JSR: “In an environment that is changing due to factors such as the fully-fledged introduction of 5G and other developments towards a digital society, as well as the aging of the human resources who ensure plant safety and a lack of human resources to replace them, the petrochemical industry is under strong pressure to improve safety and efficiency in its production activities by utilizing new technologies such as IoT and AI. The orientation of JSR is toward making production smart through a proactive incorporation of drones, IoT sensors, cameras, and other new technologies, and in this experiment, we took on the chal-lenge of the automation of plant process control using AI control technology. We verified that AI is able to autonomously control the processes that were previously performed manually on the basis of operators’ experience, and we are firmly convinced of the usefulness and future potential of AI control.”
Robust control
Takamitsu Matsubara, associate professor at NAIST, remarked, “I am very glad to hear that this field test was successful. Data analysis and machine learning are now being applied to chemical plant operations, but technology that can be used in autonomous control and the optimization of operations has not been fully ready until now. The reinforcement learning AI FKDPP algorithm was jointly developed by Yokogawa and NAIST in 2018 to realize autonomous control in chemical plants. Despite having to refer to a large number of sensors and control valves, the AI can generate a robust control policy in a limited number of learning trials. These features helped to improve the efficiency of the development process and led to the achievement of autonomous control for a long period of 840 hours during the field test. I think this very difficult achievement of autonomous control in an actual distillation column and the fact that the level of practical application has been raised to the point where the entire production process and safety are integrated into one system have great significance for the entire industry. I look forward to seeing what happens next with this technology.”
Autonomous operation
Yokogawa Electric vice president and head of Yokogawa Products Headquarters, Kenji Hasegawa, added, “The success of this field test came from bringing together the deep knowledge of the production process and operational aspects that only the customer can provide, and Yokogawa’s strength of leveraging measurement, control, and information to produce value. It suggests that an autonomous control AI (FKDPP) can significantly contribute to the automation of production, maximization of ROI, and environmental sustainability around the world. Yokogawa led the world in the development of distributed control systems that control and monitor the operation of plant production facilities and has supported the growth of a range of industries. With our gaze fixed firmly on a world of autonomous operation that forms the model for the future of industries, we are now promoting the concept of IA2IA – Industrial Automation to Industrial Autonomy. To achieve strong and flexible production that takes into consideration the impact of differences in humans, machines, materials, and methods, the 4Ms, in the energy, materials, pharmaceuticals, and many other industries, we will accelerate the joint development of autonomous control AI with our customers around the world.”