What is RGD and why is resistance to this phenomenon so critical to many sealing applications in the oil and gas industry?
By Patrick Stephen, Product Manager, James Walker
Rapid Gas decompression (RGD) resistance, also referred to as Explosive Decompression (ED) resistance or Anti Explosive Decompression (AED), is a vitally important property of elastomers in the Oil & Gas industry. RGD resistance is a required property for seals operating in the challenging environments found in many in valves, wellheads, trees, manifolds, tubing hangers and other offshore, subsea, surface and flow line equipment.
What is RGD?
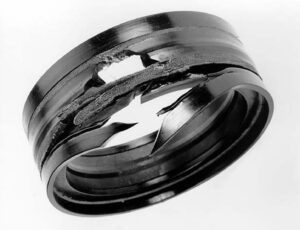
The media in upstream oil and gas applications can be under very high pressures and can be present in liquid and gas phases. Even if the medium is nominally liquid, there may be dissolved gases that can cause RGD damage. These gases are absorbed into the elastomer seals over time, until the gases inside the elastomer are at the same pressure as the system. Some swell will result in this absorption but while the system pressure remains high, no damage to the elastomer will occur. If the system pressure is quickly released, for example as a result of a blowdown event or the opening of a valve, a pressure difference occurs between the gas trapped in the elastomer seal and the surrounding environment. The gases within the elastomer will expand which can inflate the material causing blistering and cracking.
RGD induced damage has the potential to cause catastrophic seal failure.
Note: RGD damage is a physical phenomenon and not due to chemical attack. However, some gases, for example H2S, will also chemically attack susceptible elastomers, and must be considered separately and in addition to the potential for RGD damage.
Factors affecting RGD damage
- Effect of seal cross section size
The likelihood of RGD damage increases with cross section. Larger cross section seals are at substantially higher risk of RGD damage occurring. - Type of gas
All types of gas can cause RGD damage, however H2S and CO2 have high permeation rates and therefore the effects of RGD can be especially problematic. These gases can also undergo phase changes from supercritical to gaseous phases during depressurisation, generating large increases in gas volume escaping the seal. When sour gas or carbon dioxide gas is present in the system media, careful elastomer selection and sealing system design is advised. - Elastomer Selection
Elastomer materials are tested and scored based on their level of RGD resistance.
A perfect rating is 0000, meaning the elastomer suffered no damage when exposed to the arduous test conditions. The result of any testing should always be reviewed before selecting an elastomer seal for use where RGD is a risk. - Elevated temperatures
The risk of RGD damage increases substantially with temperature as all elastomers lose strength at elevated temperatures. - Effect of pressure
RGD testing at James Walker’s elastomer centre of excellence. Image courtesy of James Walker. The risk of RGD damage becomes substantial above 50 bar (725 psi) and increases as the pressure increases. Higher pressures can cause a greater pressure differential between the gas trapped in the elastomer and the surrounding environment.
- Groove fill and interference
Experience has shown that through effective design of the housing geometry, the risk of RGD damage occurring can be reduced. This is done by optimising the levels of groove fill and interference applied to the seal. Specialist sealing engineers can advise on the options available. - Effect of decompression rates (blow down, depressurisation)
With a depressurisation rate of 1 bar/minute (14.5 psi/minute), the likelihood of RGD damage is low but increases substantially above 10 bar/minute
(145 psi/minute). Trapped gas needs time to escape the elastomer, and a slower decompression rate allows more time at a lower pressure differential. - Repeated decompressions
Repeatedly pressurising and then rapidly depressurising a system has the potential to amplify the effects of RGD. As system pressure fluctuates, for example as a valve is opened or closed, RGD events have the opportunity to compound their effects; with each cycle, causing an increasing amount of damage to the elastomer and eventually leading to failure.
RGD Resistant elastomers
Specialist HNBR, FKM, FFKM and Aflas compounds can be optimised for RGD resistance. In order to achieve RGD resistance the elastomer will typically be a harder grade and have high modulus, but developing elastomers with these properties will not ensure RGD resistance has been achieved. Compounds are carefully designed and processed specifically to achieve RGD resistance, and are then tested to assess and demonstrate they possess the desired RGD resistant characteristics.
About this Featured Story
This Featured Story is an article from our Valve World Magazine, March 2023 issue. To read other featured stories and many more articles, subscribe to our print magazine. Available in both print and digital formats. DIGITAL MAGAZINE SUBSCRIPTIONS ARE NOW FREE.
“Every week we share a new Featured Story with our Valve World community. Join us and let’s share your Featured Story on Valve World online and in print.”