This article explains the new Annex M of API Specification 6D, which establishes the first comprehensive standard for hydrogen valves, introducing four specification levels with increasingly stringent requirements to address the unique challenges of hydrogen service.
By Matthew Doherty, Senior Transition Technologies Engineer, SLB, and Jonathan Geleijns, Energy Transition Technologies Manager, SLB
In September 2024, the American Petroleum Institute (API) published the second addendum to API Specification 6D, which includes the much-anticipated Annex M covering valves for hydrogen gas service. The development of Annex M spanned over a year and a half, starting with initiation of its development by SLB in 2022. This was a logical action in consideration of SLB’s extensive experience and internal testing of valves for hydrogen service and in recognition that the hydrogen economy will expose a much broader audience to the challenges hydrogen presents.
With an effective date of March 5, 2025, Annex M could not have come at a better time. New hydrogen projects continue to be announced while companies continue working toward establishing requirements for valves in hydrogen systems that address hydrogen’s unique challenges, such as material degradation and sealing difficulty. This article provides an overview of the requirements in Annex M and context on how these requirements were derived.
New specifications for hydrogen
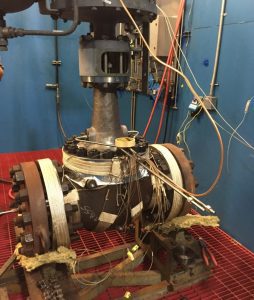
Annex M begins with an introduction of the “specification level for hydrogen” (SLH) concept that drives the requirements for design validation as well as quality and supplemental testing requirements in production. As the SLH progresses from SLH1 through SLH4, the requirements related to these levels in the Annex M sections increase to address the heightened criticality, or risk, of the application, as summarized in Table M.1 in API 6D and reproduced here. The SLH level must be specified for valves conforming to Annex M.
Testing and quality controls
For SLH₁ valves, the design validation requirements include extended-duration gas shell and seat testing and requirements for fire safe certification. The extended-duration pressure testing is done with nitrogen at twice the normal duration. Doubling the test duration enables using nitrogen as a test gas in place of hydrogen, which is dangerous to test with, or helium, which is becoming scarce. The extended duration is based on the theoretical difference in leak rate between hydrogen and nitrogen under laminar flow conditions. The doubled duration of high-pressure gas testing is found throughout all the design validation and supplemental testing in Annex M. For SLH₂ valves, the requirements for SLH₁ apply, as well as added requirements for dynamic gas pressure testing, antistatic testing, and fugitive emissions certification. The dynamic gas pressure testing sequence is taken from API 6D Annex F and is followed by antistatic testing to validate that electrical continuity between components is retained after extensive cycling, thus addressing concerns related to the low ignition energy of hydrogen. SLH₂ is also the first level for which fugitive emissions certification to ISO 15848-1 is required with a minimum tightness class of CH and endurance class of CO₁.
SLH₃ and SLH₄ further increase in requirements from the previous levels by incorporating full API 6D Annex F design validation testing, again with pressure testing conducted with nitrogen and test durations doubled. As for SLH2 valves, SLH₃ and SLH₄ valves have an antistatic test done after Annex F testing is complete and they require fugitive emissions and fire safe certification. For SLH₃, fugitive emissions certification to ISO 15848-1 tightness class BH is required, and for SLH₄ this escalates to tightness class AH, both with a CO₁ endurance class at a minimum.
Annex M does provide the option to apply scaling to design validation at the various SLH levels. For fire safe certification and fugitive emissions certification, scaling rules in the applicable standards are used. For the additional testing, scaling using the rules of API 6D Annex F is allowed. This provides the opportunity to qualify a few different sizes with each test valve, as well as additional pressure classes in some cases, provided there are no changes to the product as outlined in API 6D Section F.2. Annex M also requires revalidation of a design if there are changes to the material, design, or construction of various types of seals such as lip seals, V-packing, or die-formed graphite seals.
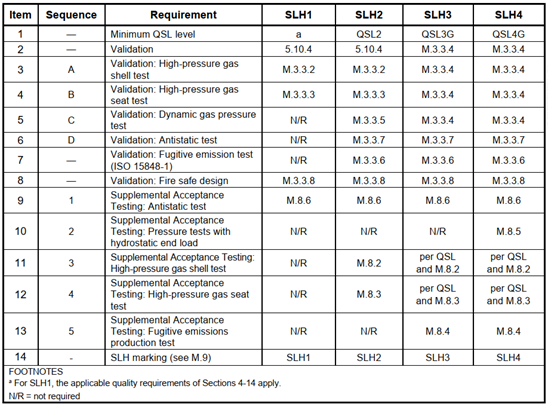
The SLH level also drives quality requirements in the production of valves for hydrogen gas service. The SLH levels link directly with the “quality specification level” (QSL) as a minimum quality requirement. For SLH₁, the quality requirements of the main body of API 6D apply, which are aligned with the recent removal of QSL₁. Increasing to SLH₂ leads to a minimum quality requirement of QSL₂. For SLH3 and SLH₄, the gas version of the QSLs is used, with SLH3 requiring QSL₃G and SLH₄ requiring QSL4G. Supplemental acceptance testing is also influenced by the SLH level, ranging from an antistatic test for SLH₁ to multiple gas tests with extended durations and in alignment with the QSL level for SLH₃ and SLH₄.
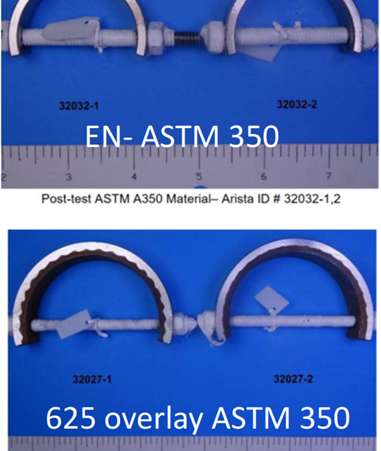
SLH3 and SLH4 valves also require fugitive emissions production testing to ISO 15848-2, with options for the use of helium or forming gas (a mixture of 95% nitrogen and 5% hydrogen) as test gases. The acceptance criteria for forming gas were established based on testing done by a third-party laboratory to provide an equivalent result to tests with helium.
The remainder of the requirements outlined in Annex M are independent of the SLH level and apply to all valves seeking conformance. This includes requirements related to the design, materials, welding, bolting, marking, and documentation. Design requirements are generally unaltered from the main requirements of API 6D other than the need to show suitability of sealant or lubricant used in lubricated plug valves and requirements related to body penetrations. Of note is the ability to block body penetrations to avoid the applicable leak path in hydrogen service. However, if the blocking of that body penetration prevents future venting of the body cavity, then the valve cannot be marked as a double block and bleed (DBB) or double isolation and bleed (DIB-1 or DIB-2) valve, even if this capability normally exists.
Material design considerations
Of particular interest to many are the requirements covering both metallic and nonmetallic materials for valves in hydrogen gas service. The metallic material requirements outlined in Annex M are limited to temperatures below 175 °C, above which the guidance of API Recommended Practice 941 is suggested. This is due to a shift in the primary damage mechanism from hydrogen embrittlement–related damage at lower temperatures to high-temperature hydrogen attack (HTHA) at higher temperatures.
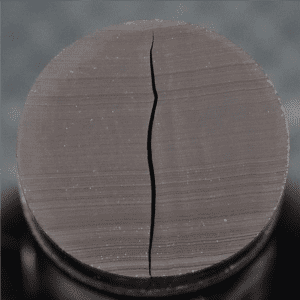
Requirements for metallic materials are split into two sections, one for permitted materials and the other for materials that are permitted with additional testing. Permitted materials are further divided into two categories, the first of which can be used essentially anywhere in the valve and includes carbon steels, low-alloy carbon steels, and austenitic stainless steels that comply with NACE MR0175/ISO 15156. Of these permitted materials, carbon steel has an additional restriction that the chemical composition and carbon equivalent are limited for all pressure-containing parts, primarily to avoid the risk of cracking at pressure-containing welds. The second permitted material category allows use only in pressure-controlling and drive train components and requires compliance with NACE MR0175/ISO 15156. This includes solution annealed or annealed nickel-based alloys or precipitation-hardened nickel-based alloys in conformance with API Standard 6ACRA. These requirements are based on extensive evidence in the literature that although hydrogen-related damage in H2S-containing environments is different than in hydrogen environments, it is more severe for these materials in most cases.
Annex M also allows the use of other materials or nickel-based alloys for other components, provided that additional testing is performed that satisfies both the manufacturer and the purchaser. No specific testing protocol is provided because the specifics will depend on the operating conditions of the application in question, but several test standards are listed for reference. These standards include ASME BPVC VIII Division 3 Section KD-10 for the design of high-pressure hydrogen vessels utilizing a fracture mechanics–based approach. Nonmetallic material requirements include rapid gas decompression (RGD) testing of elastomer materials and aging testing of both elastomer and thermoplastic materials used in valves for hydrogen gas service. In several instances, elastomers previously qualified to NORSOK M710/ISO 23936-2 for RGD resistance have failed RGD testing in 100% hydrogen. For this reason, elastomers used in valves for high-pressure hydrogen gas service must be RGD tested in 100% hydrogen or 100% carbon dioxide, which is seen as the most challenging fluid for RGD. Also, to prove the stability of nonmetallic materials in hydrogen, short-term aging testing at a specified temperature and pressure must be performed roughly in alignment with ISO 23936-1.
Welding and documentation
Welding and documentation Section M.5 covers welding and includes general requirements as well as requirements for overlays, cladding, and nondestructive examination (NDE). The use of nickel-based alloys in pressure-containing welds is prohibited. The section also establishes that the hardness requirements for weld metal and heat-affected zones (HAZs) must be in compliance with NACE MR0175/ISO 15156. Overlays and cladding are permitted provided that, as with surface treatments such as plating and coating, the overlay cannot be used to prevent degradation of the base material due to exposure to hydrogen. For NDE, all pressure-containing welds require both surface NDE and volumetric NDE, which is also the requirement for pup welds in the main body of API 6D. The final sections of Annex M are related to marking and documentation. The nameplate of the valve is required to identify the applicable SLH in addition to the QSL and other marking required by the main body of API 6D. The documentation section includes the requirement to retain documents on the design validation, materials conformance, and supplemental testing results as specified for the applicable SLH.
With the availability of Annex M in the release of the second addendum to API 6D, end users now have an international reference standard to derive requirements for valves for use in upcoming hydrogen projects. In parallel, valve manufacturers have a framework for fully qualifying valves for hydrogen service in preparation of the demand to come. API 6D Annex M will help ensure that as hydrogen infrastructure projects continue to be proposed and evaluated—and eventually built—industry will have valves available that are capable of overcoming the unique challenges of hydrogen gas service.
About the authors
Matthew Doherty is currently a senior Transition Technologies™ engineer for the SLB Valves business line. In this role, Matthew researches the technical challenges for valves in hydrogen, CCUS, and renewable fuels service to enable the selection and development of the ideal valve configurations for these trending and challenging applications. Prior to this role, he spent more than 10 years in various shop, field, and office-based engineering roles supporting the repair and remanufacture of valves. Matthew is a licensed professional engineer in the state of Texas and holds bachelor’s degrees in mathematics and mechanical engineering from the University of Houston and a master’s in engineering from the University of Arkansas.
Jonathan Geleijns has more than 30 years of valve experience, gained in engineering, sales, aftermarket and field services, and technical support in multiple geographical locations. His current position is Energy Transition Technologies™ manager for the Valves business line at SLB. In this role, he focuses on developing markets for hydrogen, CCUS, biofuels, geothermal, emissions control, and other associated applications by investigating and influencing market trends, market needs, product gaps, and industry standards and regulations. Jonathan is also cochair of the API Specification 6D Annex M Valves in Hydrogen Service Task Group and is involved with other committees, such as for Hydrogen Europe and ASME B31.12.
Note: Orbit Low-E and Transition Technologies are marks of SLB.
About this Technical Story
This Technical Story is an article from our Valve World Magazine, November 2024 issue. To read other featured stories and many more articles, subscribe to our print magazine. Available in both print and digital formats. DIGITAL MAGAZINE SUBSCRIPTIONS ARE NOW FREE.
“Every week we share a new Technical Story with our Valve World community. Join us and let’s share your Featured Story on Valve World online and in print.”