Valve sealants are essential to ensure the valve functionality and reliability through the intended service life. Depending on the formulation, sealants can be used for prevention, protection or as a solution for practical failure such as seized valves, passing or external leakage. Therefore, it is important to understand how to select the right sealant to achieve the required task and avoid causing additional failures and complications in the valve as a result of using the incorrect product.
By Bader M. Jarallah and Abdullah B. Samman, Saudi Aramco
Currently, there is a lack of standard guidelines in the industry to guide users on how to select the proper product for different types of valves and applications. This article aims to provide general tips and methods that users can follow to guide them in the right direction, with more focus on some lab tests that can help understand more about the sealant.
Valve sealants
Valve sealant is a term generally used in the industry for the products used to repair valves online. This includes preventive maintenance as well as emergency repair. Products are usually injected through the designated injection ‘fittings’ to perform a specific task.
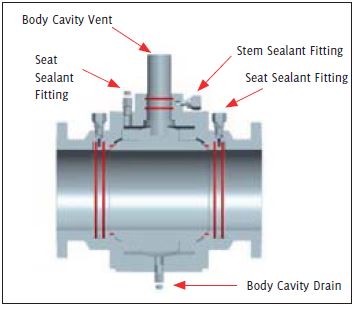
Based on the required task products can be classified as follows:
- Valve Lubricants
- Valve Sealants
- Cleaners and Flush
- Packing Compounds
Generally, all valve repair products can be categorized as greases. Grease is defined as a semi-solid material consisting of base oil, additives and a thickener. When used for the purpose of sealing, solid particles (fillers) such as PTFE are sometimes added to the grease to enhance its ability in bridging and sealing deep scratches. Below is the breakdown of sealant composition:
- Base Oil: This can either be mineral based or synthetic. The choice depends on the service type where synthetic based products can be used with services that are not compatible with mineral based oils.
- Thickener: Thickener is the term describing the ingredients added to a base oil in order to thicken it to a grease structure; typically, a metal or non-metal soap. Adding thickener to the base oil converts it from fluid form (oil) to semi-fluid form (grease).
- Additives: Chemical and metallic additives added to grease in order to enhance their performance, choice of additive package is important. For example, applications involving high contact loads will require extreme pressure (EP) additives. Another example is corrosion-inhibiting agents added to the grease for corrosion prevention.
- Filler: These are solids that are added to the sealant for the purpose of providing additional sealing capability. Valves that require sealing deep scratches can utilize sealants with fillers to ensure those scratches are properly sealed. In addition, solid lubricants are sometimes added to different sealants.
Figure 2. Valve sealant composition.
Classification of valve sealant
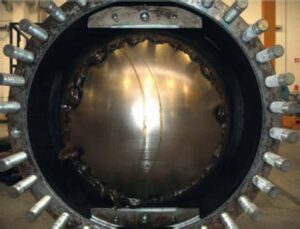
Depending upon the formulation, valve sealant can be classified into the following main categories:
- Cleaner: A semi-fluid combination of solvent and semi-synthetic lubrication oils with inorganic thickener. Valve cleaner is recommended to be used as a corrective and preventive action to clean important seal faces and sealant passages. Valve cleaner also penetrates and loosens rust and corrosion deposits. It is essential to ensure that the valve cleaner is compatible with the valve material and does not contain ingredients, acid, caustic, or any solvent, that could have negative effects to the valve internals.
- Lubricant: This is formulated from synthetic grease with corrosion inhibitors and an inorganic thickener free of fillers and sealant additives. Valve lubricant is recommended to be used as a seat lubrication for on-service valves during PM activities for lubrication purposes.
Figure 4. Samples of valve failures that could have been prevented/rectified using valve sealant: (a) Corrosion in the seat pocket area due to accumulation of corrosive products. (b) Accumulation of sludge and debris in the valve cavity. (c) Damage to the valve seating area. - Sealant: formulated from synthetic grease with corrosion inhibitors and an inorganic thickener and sealant additives to enhance the sealing characteristics. Valve sealant is recommended to be used as a corrective action for worn valves with minor leakage problems due to minor scratches to sealing surfaces and shallow corrosion pits. In case of heavy leaks, which usually occur due to deep scratches, heavier sealants with solid fillers such as PTFE particles and flakes are recommended. Figure 4 demonstrates typical valve issues that can be rectified using valve sealants.
Importance of selecting the correct sealant
Using sealants for maintenance and repair of valves is important for the reliability and functionality of the valve in the long term. If the wrong type of sealant is used, major failures and further complications are expected. Figure 5 is an example of failed sealants because of wrong selection. Some of the failure mechanisms that can result from wrong sealant selection include solidification of the sealant, turning the sealant into powder, sealant washout with process fluid and many other forms of failures.
Characteristics of a good sealant
Before injecting any valve repair products, several questions should be considered: will this sealant do the intended job? Is this product compatible with the service? Will it damage my valve? Thus, it is important to evaluate the proposed valve repair product prior to commencing the maintenance activity. The following are the main criteria that should be considered when selecting a sealant:
- Safe and environmentally friendly
- Injectability of the product (ability to be pumped)
- Service compatibility
- Sealant capability
- Sealant stability
Figure 5. Solidified sealant in the valve cavity causes restriction of valve movement.
Qualification of a valve sealants
Currently, there are no international standards or procedures that focus on how to select the right sealant. Sealant composition belongs to the manufacturers’ critical know-how which is not usually shared with end users. However, there are several ASTM standards available to classify/qualify grease by understanding its properties. Below are the main ASTM tests for grease.
Lubricating greases consistency – ASTM D217
This measures the consistency of the mixture via a penetrating cone test. Consistency is categorized by different codes referred to as NLGI numbers. The higher the number, the higher the consistency and the more solid the mixture is. See Table 1. This is an important parameter to consider for the injectability of the sealant. However, a compromise must be taken to ensure the sealant is consistent enough to perform the required task.
Dropping point – ASTM D566
The dropping point of a grease can be defined as the temperature at which the material transforms from a semi-solid state to a liquid state, i.e., the temperature at which the first drop of material occurs. This is an important parameter to consider when selecting an appropriate sealant as it gives an idea of how well the sealant will withstand high temperatures. The dropping point of the sealant should always be higher than the highest temperature expected in the application.
Sealant stability with water and hydrocarbon (non-ASTM)
Since the sealant will be in contact with the service product, it has to be stable and resist disintegration when they are in contract. Therefore, the sealant must be tested with the product material: either hydrocarbon or water.
This can be done by placing a specific amount of water or hydrocarbon in a container and placing a globule of the sealant in the fluid. The sealant should remain in the fluid for a specific number of days (typically one week) and the mixture is visually inspected for any disintegration of the sealant in the fluid.
Figure 6 shows how a product with good stability in water would react where there were hardly any physical changes to its composition. Figure 7, however, showcases a product with poor stability in water as it was dissolved.
Finally, Figure 8 showcases an example of a product that was tested for hydrocarbon stability where it was mixed with pentane solution for 120 hours at 25°C.
Temperature stability (non-ASTM)
Depending on the expected operating temperature of the application, it is essential that the lubricant sealant will be able to operate properly at this temperature. Hence, it must be ensured that the sealant will be thermally stable both chemically and physically.
Typically, the temperature range is provided by the product manufacturer. Measuring the temperature limits can be quite troublesome as it must consider several factors such as the dropping point of the sealant and the flash point of the base oil used.
However, when the temperature range of the sealant is not provided, it can be tested in the lab by subjecting a globule of sealant to continuous high temperature for an extended period. The tested subject is then observed for any physical changes that occur.
An example of this can be seen in Figure 9 and Figure 10 where the sealant was heated to 60°C for 120 hours. As can be seen, the product in Figure 9 was not affected by the high temperature while Figure 10 product failed by drying up and hardening.
Conclusion
To summarize, proper selection of valve sealants and lubricants is important for all industrial plants to ensure reliability and safe operation of valves. It is highly important to understand how to qualify sealants for certain applications as there are currently no international guidelines for sealant selection.
Several tests are explained in this report which are of high importance to valve sealants such as consistency, dropping point, water/hydrocarbon stability and temperature stability. The tests mentioned in this report can be utilized and customized to aid in developing a qualification process suitable for the targeted application.
It is also worth noting that some of the performance aspects of sealants cannot be confirmed without conducting a field trial. This is an additional step that can be taken towards extra measures, especially when trying new products for special applications. The application can be monitored for a specific period of time while the product is applied to ensure it is not causing any problems.
About the author
Abdullah Samman is a Lubrication Engineer working with Saudi Aramco Central Engineering. He has a B.S. in Mechanical Engineering from the University of Leeds. Since joining Aramco in 2015, he has worked on several issues in the field of rotating equipment and lubrication. He has dealt with troubleshooting of rotating equipment, lubrication failures, corporate lubricant condition monitoring program as well as providing consultations to operating facilities and projects.
Bader Al-Jarallah is a Valve Engineering Consultant at Saudi Aramco Central Engineering. He served as the Chairman of Valve Engineering Standards Committee as well as committee member of several engineering standards. Bader has a B.S. in Mechanical Engineering and M.S. in Material Engineering. Bader joined Saudi Aramco in 2000. Since then, he has dealt with various design, commissioning, operations, troubleshooting & maintenance issues.