Velan has developed a smart device to monitor the state of any quarter-turn valve without adding electrical connections or mechanical interfaces.
By Gianluca Losi, R&D Manager, Velan ABV
The majority of quarter-turn valves installed in a plant are manual valves. In fact, it is estimated that 65% of valves in an offshore or onshore plant are manual, compared to 15% of control valves and 20% of actuated valves. These valves are usually operated using handwheels, gearboxes or levers, and their management is still tied to traditional preventive maintenance techniques, even though they often perform critical functions such as isolating critical parts of the plant during service and maintenance.
Integrating these manual valves into the plant’s distributed control system is not currently planned systematically, even though it would bring significant benefits. These include monitoring their open/closed status and tracking the activities performed on them, primarily reducing the physical presence of operators on the plant both for routine inspections and in case of emergency interventions. Instrumenting all the manual valves in a plant, however, represents a significant investment, both economically and from an operations perspective.
It would involve adding conventional electronic devices, such as limit switches or pneumatic control panels, that meet the installation requirements in potentially explosive environments. There would also be a need to make network infrastructure available for data transmission and power supply for the instrumentation, resulting in increased installation costs and space/weight requirements. Finally, the valves are often difficult to reach, so the above-mentioned wired installation requirements would be further complicated.
Overcoming the challenges
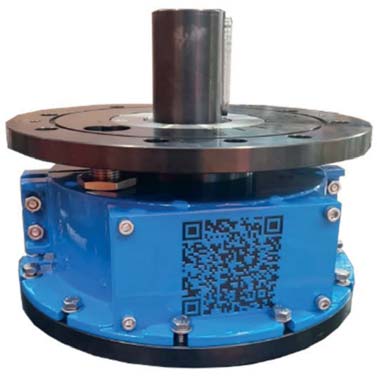
Velan’s V-Flange monitors the state of any quarter-turn valve throughout its life (from shipment to disposal), without the need to add electrical connections and mechanical interfaces, as the entire device is contained in a connection bracket that easily fits between the valve and the operator, and is battery-powered.
The device gives the valve the ability to store the number of operations performed, records and communicates the position of the shutter, monitors the level of vibrations to which the valve is exposed, and interprets the environment in which the valve is located, providing an advanced warning when maintenance is required.
The device integrates electronic components programmed to monitor the current operating condition of the valve but also to automatically determine a possible transition from one operating condition to another throughout the life of the valve. V-Flange is equipped with a wireless connectivity system that allows communication on cellular networks, as well as serial communication with a portable device. The same connectivity system allows the device to be geolocated; a useful feature for tracking its movements during operations and its location in the plant after installation.
Technical features
The design of the V-Flange makes it easy to handle and simple to install and maintain. Indeed, V-Flange features ISO 5211 standard interface flanges, from size F25 to F60, and is already equipped with a connecting joint for easy mounting, even on valves that are already installed in-line.
The device is powered by long-lasting torch-type batteries (primary Li-MnO2 cell) selected to have a minimum lifespan of 5 years (potentially longer if the device is used according to the manufacturer’s instructions), negating the need for a wired electrical connection. The batteries, housed inside the device itself, can be replaced with standard replacements and, using the appropriate access on the protective housing, without having to disassemble the device from the valve, resulting in significant time savings. A series of sensors monitor the operations performed by the valve and the surrounding environment.
All data is stored in an internal memory that can contain up to 36 months of operations. The memory can be periodically emptied, creating a backup of the data acquired up to that moment in a dedicated server and, thus, supporting the data communication module in case of scarce connectivity.
The device is equipped with a sensor system that recognises when it is mounted on the valve and starts intelligent monitoring of the operations. The main sensors are:
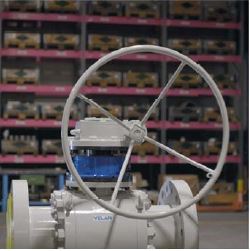
- A position reading and saving system for the shutter, which also counts the number of operations performed. The manoeuvres are automatically classified as openings or closures, and a counter gives feedback on the number of remaining manoeuvres before the next maintenance intervention. The sensor system can uniquely identify the position of the shutter with a resolution of 15° between 0° (valve closed) and 90° (valve open).
- An inertial measurement unit (IMU), capable of measuring the orientation of the valve in space and the accelerations it is subject to, monitors any impacts or excessive vibrations that could compromise the valve’s operating functionalities.
- A temperature and humidity sensor to monitor any deviations from optimal electronic operating conditions. The sensor measures from -20°C to 80°C, also providing information on the suitability of the place where the valve is stored or installed.
- A high-sensitivity omnidirectional microphone, to track environmental noise levels.
V-Flange is equipped with both a wireless connectivity system based on a cellular network and direct communication via serial. The connectivity module utilizes LTE cellular technology for data transmission to the cloud, as well as to geolocate the system during every phase of its life and for recovery in case of loss or theft. In these two cases, it is also possible to delete sensitive data contained in the device to prevent improper use.
The integrated firmware manages the readings from the sensor network and the data transmission according to logic which adapts to the operative situation; optimising energy consumption and the battery’s lifespan.
Advantages
V-Flange enables comprehensive monitoring for the maintenance management of a manual valve. It tracks the number of manoeuvres performed, the time elapsed since the first and last operation, the duration of the valve in the closed and open positions, records impacts, and monitors storage conditions. Integrated software allows the device to classify sensor readings into four different operating conditions: stand-by, transport, service, and maintenance.
It can notify the user in case of events that are anomalous or noteworthy. In addition to these features, V-Flange enables remote monitoring of the valve status, reducing the need for personnel to physically access the valves. This capability is especially useful for valves installed in hard-to-reach areas and during emergency conditions, where users are exposed to a higher level of risk.
In summary, V-Flange is more than just a ‘smart’ device with sensors and connectivity. Its real value lies in the integration of the collected data into an easy-to-use web-based dashboard with configurable functions. For instance, users can generate asset usage reports, conduct historical series analyses, and compare the performance of different valves to develop intelligent management strategies and make data-driven decisions.
About the author
Gianluca Losi holds an MSc in Mechanical Engineering and a PhD in Mechanical and Industrial Engineering. He is currently working as R&D Manager for Velan ABV in Lucca, Italy. His activities revolve around new product development and introduction, with a particular focus on ball valves, actuators, and IIoT systems for asset health management.