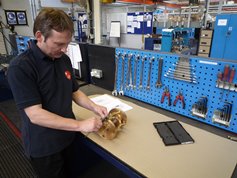
Leader in the Assembly Department.
How tidy is your personal work-space right now? Perhaps there’s a pile of papers that needs sorting or a half-finished project waiting on a spare part. Surely you would be more efficient if work processes were streamlined, recurring problems resolved and all tools immediately at hand? Well, that’s exactly how they feel at valve-maker Truflo Marine, as I discovered on visiting their very organized premises in Birmingham, England.
To be absolutely clear: my visit to Truflo Marine was quite impromptu. Passing by, I simply knocked on the door, asked for a look-see and they kindly showed me around. There was, therefore, no time for anyone to tidy up.
Nevertheless, the offices and factory areas were remarkably neat and tidy.
That’s the result of various initiatives the company has been implementing of late. Initiatives such as Lean Management, the BIT Program, 5S, the suggestions box and the wonderfully named TEA Team (short for Truflo Excellence Academy Team).
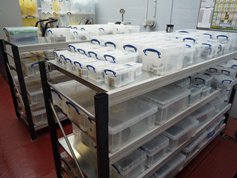
to properly store equipment.
During my walk through the plant, HR Manager Chris Anson pointed out some of the wall charts generated by the TEA Team. “The TEA Team facilitates and guides teams looking to identify problems, quantify them and find solutions. We work closely with all departments – machining, assembly, documentation, production – and encourage interaction between them.”
Recalling a recent case history, Chris notes how some older engineering drawings had become partly illegible. That meant workers having to down tools to decipher texts. As a solution, the TEA Team initiated a process whereby the older drawings are scanned into the computer, analyzed and properly annotated. This is an on-going task but has already resulted in fewer delays on the work-floor, comments Chris.
Asked for advice on how to implement change, Chris says that it is important to get everyone on board: directors, managers and co-workers alike. “Ensure time is made available for internal training and plan implementation days so that whole teams are freed up to make improvements. Afterwards, conduct regular audits to maintain benefits and prevent backsliding into old practices,” she says.
(Development Department).
Continuing the tour, it is also immediately obvious how much effort has been taken to properly label and store tools and other equipment. “Basically we are looking to promote efficient and safe working practices,” notes Ron Turner, Lean Champion and Team Leader in the Assembly Department. “For example, the test flanges used to go walkabout and could never be found when needed. Now they are kept in a central location in labelled containers. We will soon be going a step further, recording the precise locations on computer.”
Plastic containers are also used to store any quarantined jobs. Comments Ron: “valves which cannot be finished are not left lying around. All the parts are properly documented, dated and stored in one location. That gives an instant overview of the jobs waiting completion, facilitating a more efficient follow-up.”
All these improvements on the shop floor have not gone unnoticed. Ron says that visiting customers have been very complementary and that the company’s audit rating has skyrocketed.
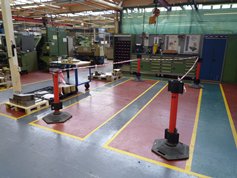
valuable floor space.
In the machine shop I noticed an empty, roped-off space and casually asked Alan Bradley (Lean Champion, Development Department) if he was expecting some new machinery. My assumption was, however, way off the mark.
Alan: “what we have done is re-think how parts are sent to the work stations. They used to be routed through a central location but are now dispatched direct from the stores area. This makes the whole production system more efficient and has freed up considerable floor space into the bargain. That area has been roped off to demonstrate the tangible benefits of the new system – and to prevent anyone from simply putting more parts here!”
Alan has also found a way to turn rubbish into cash. “We now have dedicated bins for various waste items. It is surprising how much valuable waste material, such as costly alloys, was left lying around.
With 25 years’ experience in engineering, Alan knows a thing or two about running an efficient machine shop. His parting thought on implementing improvements is both sage and simple: “have a place for everything and keep everything in its place”.