Industrial valves are widely used in various critical applications, wherein they are required to handle flammable or environmentally hazardous fluids under extreme operating conditions of pressure and temperature.
By Leire Colomo, Ampo Poyam Valves
Some of the traditionally challenging applications of industrial valves include cryogenic environments, subsea operations, slurry transportation, and petrochemical processes.
In addition to these conventional applications, the ongoing transition towards decarbonisation within the energy sector has resulted in the emergence of new demanding applications and associated challenges. Renewable energy sources, such as wind and solar power, have gained traction in recent years and they are projected to play a crucial role in the forthcoming decades. According to the Energy Transition Outlook by DNV GL (DNV 2022), it is expected that by the year 2050, approximately 70% of the global power system will heavily rely on renewable energy sources (VRES) (see Figure 1).
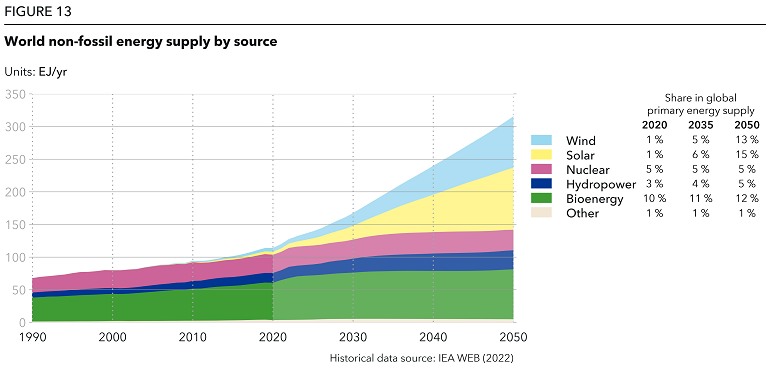
However, one of the primary challenges associated with renewable energy sources is their inability to guarantee on-demand energy generation due to their reliance on the availability of the corresponding energy source. Additionally, the generated energy can’t be stored efficiently for later use. In this context, green hydrogen emerges as a solution for energy storage and transportation. Recent perspectives, as outlined in IDTechEx (IDT 2021), indicate that the demand for hydrogen generation is expected to grow exponentially throughout this decade (see Figure 2). Consequently, the valve industry will assume a significant role, particularly in the development of hydrogen storage and transportation facilities.
Several technologies are being employed for the storage and transportation of hydrogen, including:
- Utilisation of ammonia as a carrier for hydrogen
- Blending hydrogen with natural gas
- Storage of pure hydrogen at room temperature and high pressure (up to 1000 bar).
- Cryogenic liquefaction of hydrogen at temperatures as low as -253°C and pressures up to 65 bar
Within these frameworks, ensuring the integrity and functional reliability of the products is of utmost importance to prevent catastrophic security and environmental disasters. Thus, it is crucial to adequately consider the interplay of various physical phenomena. In this regard, numerical modelling plays a pivotal role in valve design. Traditionally, structural simulations have been employed to verify the integrity of valve components under extreme conditions and to assess internal and external sealing performance. On the other hand, computational fluid dynamics (CFD) codes can be used to examine flow capacity and the impact of fluid dynamics on pressure distribution.
However, conducting independent analyses of the structural and fluid domains may not provide representative results, potentially leading to inadequate designs. As an alternative, fluid-structure interaction (FSI) models, hold high potential for evaluating valve integrity and functionality under severe conditions. These models enable considering the interaction between the fluid, mechanical, and thermal domains. Thus, in the present study, the capabilities of different FSI techniques in valve modelling are analysed for various valve operating scenarios.
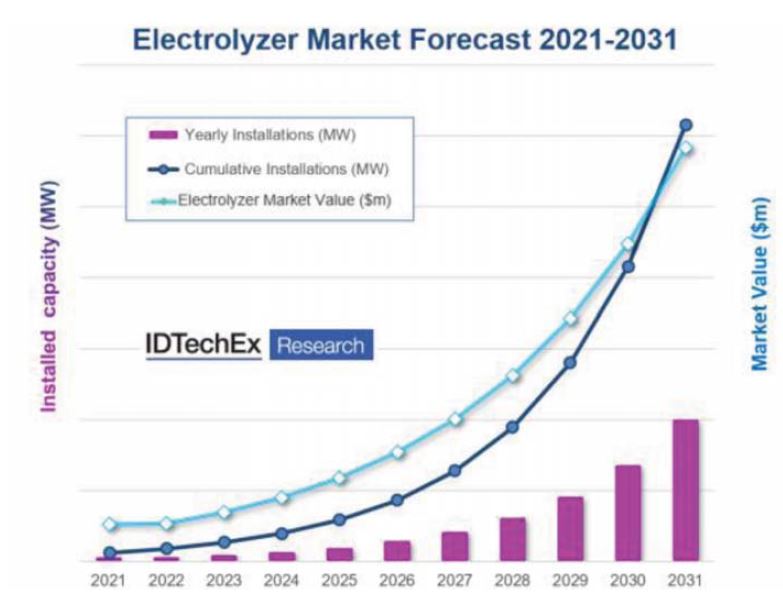
FSI modelling strategies
At Ampo, we distinguish two primary FSI approaches:
i) The monolithic approach, where the entire equation system, encompassing all domains, is solved together in each iteration.
ii) The partitioned approach, where each domain is solved separately, and the results are subsequently transferred between the fluid and structural domains.
Currently, most commercial Multiphysics simulation software adopts the partitioned approach. This choice is driven by the advantage of leveraging powerful mechanical and fluid dynamics solvers that are already available. As a result, the partitioned approach is the most widely used for industrial applications. Figure 3 presents a schematic representation of a typical FSI partitioned modelling structure.
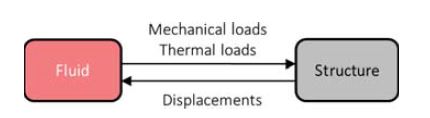
Partitioned FSI simulations can be classified based on the data transfer strategy between the fluid and structural domains:
i) One-way coupled or sequentially coupled (see Figure 4a): In scenarios where the domains’ effects are not reciprocal, data transfer from the affected domain is sufficient, and reciprocal data transfer can be avoided to reduce computational costs. One-way coupling simulations are suitable for modelling valve heating/cooling processes or valve mechanical performance under steady-state conditions. In such cases, the fluid’s behaviour strongly influences the structure’s performance, while changes in the fluid caused by the structure are negligible.
ii) Two-way coupled or fully coupled (see Figure 4b): When both domains have a relevant reciprocal effect, data transfer must be conducted reciprocally. Two-way coupling simulations are valuable for valve design when structural displacements play a critical role in valve operation, such as in time-dependent valve manoeuvring analysis.
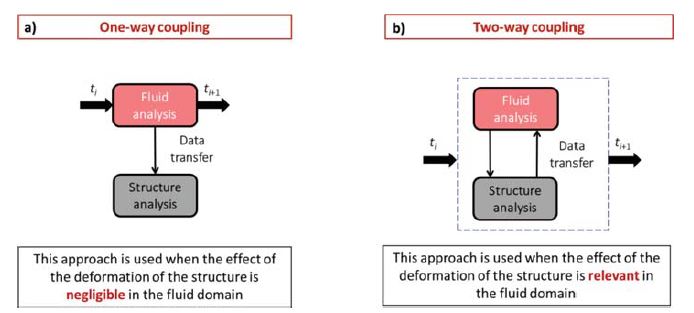
One-way vs. two-way approach comparison in an Ampo Poyam butterfly valve
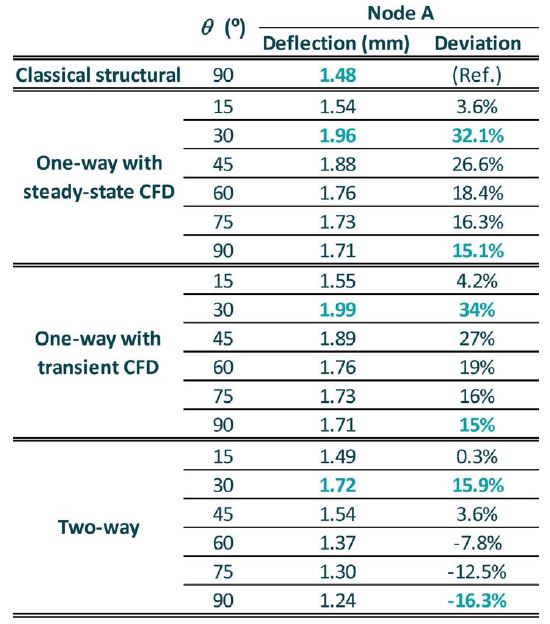
The two-way approach in FSI simulations offers more realistic results compared to the one-way approach. However, it comes with a higher computational cost, making it advisable to use only when necessary for the specific case study. Determining the appropriate approach for design purposes can sometimes be challenging.
In this section, the results obtained using various calculation approaches, ranging from the classical approach to different FSI coupling techniques, are presented for a conceptual butterfly valve case.
- Classical structural analysis: The fluid pressure distribution is calculated assuming a uniform pressure over the disk.
- One-way steady state CFD approach: The fluid pressure distribution is computed for steady state fluid domain scenario at fixed positions (15°, 30°, 45°, 60°, and 90°) sequentially coupled with the structural domain for each position.
- One-way transient CFD approach: Transient simulations of the fluid domain are conducted at the same fixed positions, sequentially coupled with the structural domain for each position.
- Two-way approach: A transient CFD domain is employed to compute the pressure distribution throughout the entire manoeuvring process, accounting for the deflection of the disk due to pressure loads.
Figure 5. Pressure distribution and disk deflection for each simulation approach.
Figure 5 presents the pressure distribution and disk deflection obtained using these four calculation approaches. It is observed that contrary to the assumptions made in the classical approach, all the FSI approaches predict non-uniform pressure distribution over the disk, resulting in asymmetric bending loads. The pressure distribution and magnitude differ among the three FSI cases. The one-way steady-state and one-way transient approaches exhibit similar results since they do not consider the effect of disk deflection in the fluid domain. However, the two-way approach, which accounts for the deflection, predicts lower deflection values but still higher than the classical approach.
Table 1 summarises the disk deflection estimated by each approach. Deviations exceeding 30% are observed in both one-way approaches compared to the classical approach. The critical position for these cases is at 30°, where the combination of dynamic pressure over the disk and suction generated by the depression on the backside of the disk occurs. The two-way approach shows a deviation of 16% compared to the classical approach. In this case, the critical position also corresponds to 30° but exhibits lower deflection values due to the update of the fluid domain with the deformed disk geometry, impacting the pressure and fluid velocity distribution as observed in the CFD plots.
General highlights
In summary, the general highlights drawn from present work are:
- In industrial valves, complex physical phenomena occur simultaneously, and it is mandatory to ensure valve security and proper sealing.
- Traditional calculation present limitations to faithfully model sever valve conditions, as they do not consider in a reliable way the interactions between the fluid domain, the structural domain, and the fluid domain. This lack of precision may lead to inadequate product design and, consequently, costly try and error product fixing.
- FSI can help not only to a better understanding of the complex phenomena that occur inside the valve but also to quantify and determine more realistic values that help to develop more reliable products. Thus, FSI is a valid tool in the product innovation and design process.
About the author
Leire Colomo is the Innovation & Technology Development Director at Ampo Poyam Valves in Spain. She holds degrees in both Industril, Engineering and Production & Operations Management, and an Executive MBA. She has been working as an engineer for over 18 years, and specifically in the oil & gas industry for 16. She moved to the R&D as the Innovation and Technology Director in 2010. She has been involved in new product developments, technology investments and new business models.
References
(BAZ 2013) C. Bazsó, C.J. Ho˝s, “An experimental study on the stability of a direct spring loaded poppet relief valve”, Journal of Fluids and Structures, Volume 42, October 2013, Pages 456-465, https://doi.org/10.1016/j.jfluidstructs.2013.08.008
(DNV 2022) DNV, “The rise of renewables”, Energy Transition Outlook, 13 October 2022, dnv.com/energy-transition-outlook/rise-of-renewables.html
(IDT 2021) IDTechEx , “Electrolyzers are the First Step Toward Green Hydrogen Production, Discusses IDTechEx”, BOSTON, March 31, 2021 /PRNewswire