The market for aromatic compounds takes up 40 per cent of the volume in petrochemicals. Benzene, toluene and xylenes find their way in an array of higher-value consumer products. BTX, being byproducts from petroleum refining, is also plagued by occasional mismatches in supply and demand, leading to price volatility. However, there are technologies for dedicated BTX-production.
By Lucien Joppen
Aromatics are building blocks for an impressive array of half-products (for example polymers) and end products for industrial and consumer products. It would go too far to mention them all but BTX are the starting point for clothing, packaging, solvents, pharmaceuticals, high-end plastics (Lego), coatings, adhesives, fuel additives and so on.
Due to a growing consumer market, especially in emerging economies, the demand for BTX is increasing, roughly 4 per cent per annum. Currently, the global market for BTX is roughly between 100,000 and 120,000 Kt per year, according to industry estima-tions (Mordor Intelligence, other sources). Mordor states in a recent report that BTX is projected to register a CAGR of approximately 3.76 per cent during the forecast period (2021-2026).
Naphtha reforming
Much will depend on the economic climate and subsequent consumer demand. As Mordor states, “the BTX-market was negatively impacted by the COVID-19 pandemic in 2020. Thus, a slowdown or disruption in industrial activity and the economic crisis that broke out due to COVID-19 affected the investments in certain end-user industries, which affected the demand for BTX.” However, over the medium term, as the pandemic’s effect on societies and economies will be increasingly mitigated, BTX will continue its ascent, according to Mordor. These projections are also mirrored by other research agencies and trade industry publications.
As mentioned earlier, BTX are generated as by-products from petroleum refining. Due to the relatively low BTX content in crude oil, BTX is largely created by converting other molecules to BTX molecules.
The most common pathway is naphtha re-forming, which converts non-aromatics from the same carbon numbers to aromatics. Re-formate, the product from naphtha reforming, provides roughly one half of the source for BTX. The pyrolysis gasoline (pygas) from naphtha crackers provides roughly one third of the source for BTX. The remainder comes from coke oven light oil (COLO) and other production methods.
Extraction
There are two types of aromatics extraction in the refining industry: liquid-liquid extraction (LLE) and extractive distillation (ED). Both LLE and ED have been in use for decades and can be employed for all feed-stock types (reformate, pygas and COLO). The choice for either method is motivated by fluctuations in feedstock or half/end product requirements.
LLE has been developed since the 1960s and consists of four major columns: an extractor, stripper, water wash column and recovery column. In the extractor, the solvent dissolves (extracts) the aromatics moving downward, while the undissolved non-aromatics move upward. The liquid moves based on the density difference between the two liquid phases, with the extraction efficiency based on the difference in solubility between aromatics and non-aromatics in the extraction solvent.
Extractive distillation
ED, developed in the 1970s, has a simpler configuration (two columns). As opposed to solubility difference in LLE, ED is based on the relative volatility of non-aromatics over aromatics created by a solvent environment. This relative volatility can be elevated by increasing the solvent volume. However, this increase involves upscaling equipment size and an increase in energy consumption. Substantial gains in yield can be made by solvent selection.
Comparing LLE with ED, the first method requires higher capital investment due to the equipment (columns and related equipment) and solvent use. LLE also has implications for maintenance and start-up time due to its complexity.
This would make ED the “winner”. However, much depends on the feedstock. In certain cases (very low aromatics content), LLE could be the favourable due to relatively less energy use.
BTX
Benzene is extracted from two primary sources: pyrolysis gasoline (pygas), which is a co-product of ethylene manufacture; or reformate, a refinery stream resulting from the catalytic reforming process used in gasoline production. Benzene can also be derived from toluene. Benzene is widely used across many industrial sectors, combined and processed with other basic chemicals (such as ethylene or propylene) to produce countless consumer goods. The largest derivative outlet for benzene is ethylbenzene, an intermediate used in the production of styrene, which is further converted into materials such as polystyrene.
Toluene is extracted from gasoline manufacturing streams in very large quantities to one of three grades of purity: TDI, nitration, and commercial. TDI grade toluene is used to make isocyanates, which are combined with polyols in the manufacture of polyurethanes. In turn, polyurethanes are used in a wide variety of consumer goods. Nitration grade toluene is used as a solvent and also in the production of phenol, particularly in Europe. Both nitration and commercial grades are used as feed in the hydrodealkylation process, which turns the toluene into benzene, and in the disproportionation process, which converts toluene into both benzene and xylene.
Xylenes (para-xylene, ortho-xylene and meta-xylene) are extracted or distilled from gasoline refining. They can also be produced from toluene using the disproportionation process. Xylene is mainly supplied as a mixed stream, although various processes are used to separate the individual isomers for specific destinations. Para-xylene is primarily used as a feedstock for terephthalic acid, a key component in PET. Ortho-xylene is used in plasticizers, medicines, and dyes. Mixed xylenes can be used as solvents and in the printing, rubber, and leather industries.
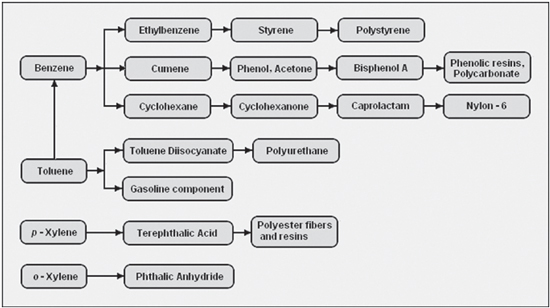
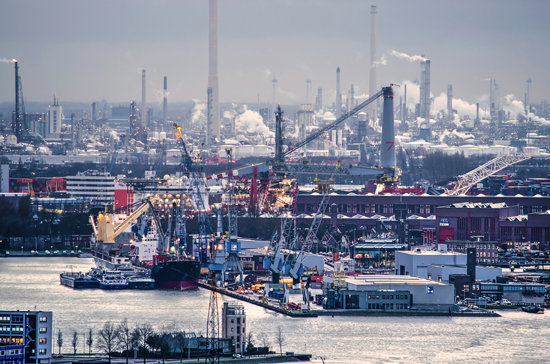
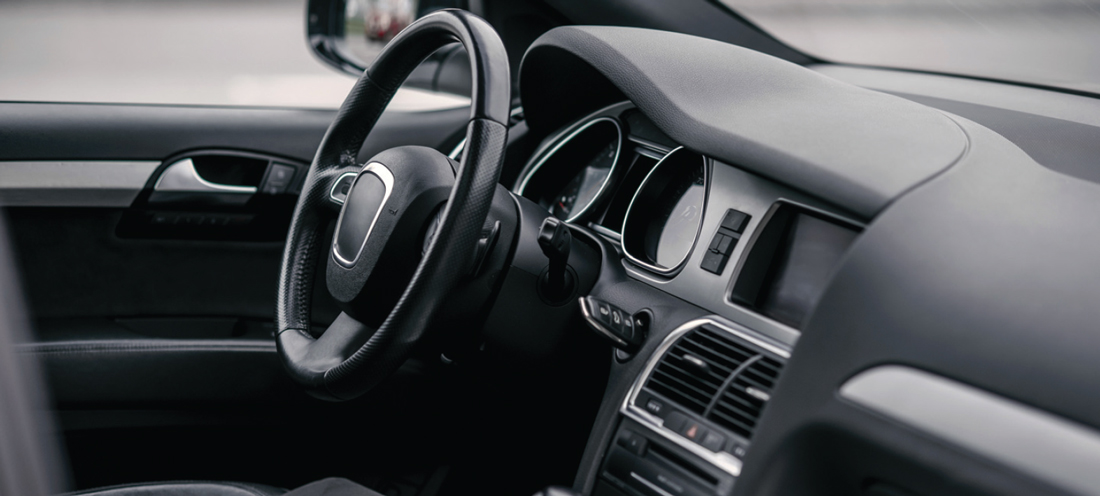
Matching supply and demand
As mentioned earlier, the BTX-market can be very volatile. There are several factors that drive demand, such as economic growth and subsequent demand for consumer products. For example, in 2020 and 2021, the slump in many sectors (such as automotive) caused a downturn in BTX-production. As a result, many refiners did not bother to extract BTX but kept these in their fuels.
The supply side is also of crucial importance. As BTX is a byproduct, the main products – gasoline, kerosine, diesel – impact the production of BTX. If gasoline prices are low, the economics of BTX extraction become more favourable. Reversely, when the gasoline value is high compared to the market price of aromatics, refiners leave a higher proportion of mixed xylenes in the gasoline pool, and toluene conversion to benzene and paraxylene is also reduced. This in turn elevates the price level of BTX for end users. This supply-demand puzzle depends highly on the aromatic compound. For example, toluene is produced in greater amounts than s necessary for the end user market. On the other hand, para-xylene is produced in lower quantities than market demand lower than demand of xylenes. As demonstrated in Figure 2 on page 28, there is a route, via trans-alkylation, to produce mixed xylenes and benzene from toluene. Needless to say, this extra step incurs added cost to the end product.
Valves: Control challenges
Valves in processing aromatic compounds and their mixtures are found to be extremely dry and remove any kind of grease or lubricant from metal or other surfaces. Aromatic compounds create friction to surfaces, like between the control valve plug and seat, which are in continuous movement against each other when controlling the flow. Sometimes, the control valves are also expected to be really tight (ANSI V) to avoid any leakages of these hazardous compounds and to eliminate the installation of an additional shut-off valve to the piping. Pipeline purging in these kinds of conditions with heavy solvency should be taken seriously to avoid any impurities or debris in the piping. Combining the challenges of frequent movement with many reversals, seating tightness and possible piping debris makes the application highly critical and demanding, and literally pushes it to the edge of optimum conditions for a control valve. There is a real risk that control valves can get stuck, and the wearing and scratching of seating surfaces may occur. This then leads to many kinds of control problems, such as hunting and poor control performance, as well as leaking. These control problems can be prevented by proper valve selection, material selection and control valve diagnostics.
Source: Hydrocarbon Engineering, 2013. Article by Sari Aronen (Neles)
Crude to chemicals
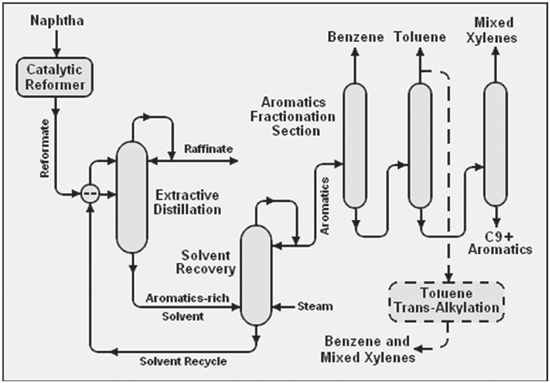
Looking at the near future, it seems that crude oil refineries will adapt their processes to produce relatively more naphtha (and petrochemicals) at the expense of fuels. This has been driven by the relatively slower growth rate in global demand for refinery fuels such as diesel, jet, and gasoline relative to petrochemicals.
This move is also expected to lift refinery margins that have been heavily tied to highly volatile gasoline price levels. On the other hand, margins of integrated complexes (fuels and petrochemicals) are expected to be higher and more predictable in the coming decades. Several complexes have made this transition, using a mix of medium and heavy crude oils and employing various process technologies to increase feedstock conversion to light olefins and naphtha range products. A good example is the Jamnagar COTC (crude oil to chemicals) project (Reliance), intending to double the conversion rate from crude to chemicals (ethylene, propylene, butadiene, BTX).
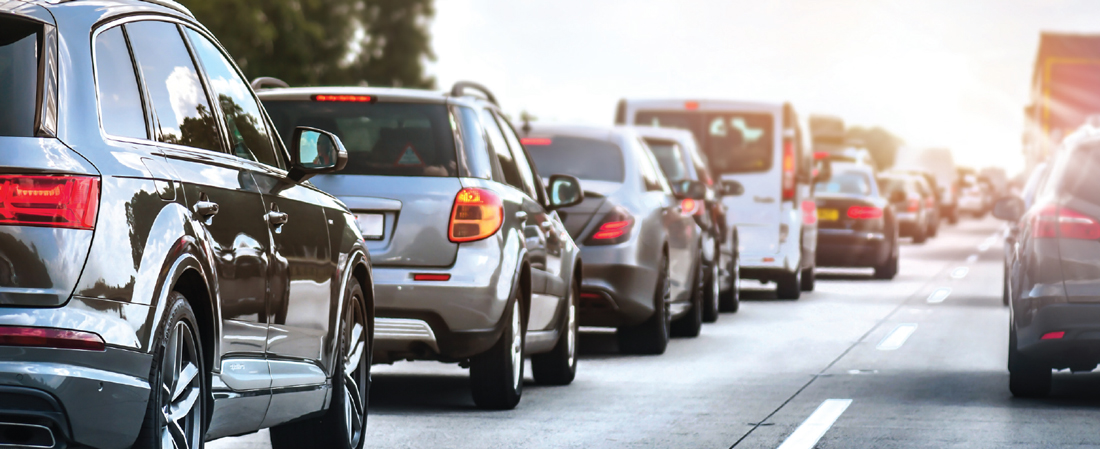
Spectacular yields
There are three routes that COTC-operators employ: (1) direct processing of crude oil in steam cracking, (2) integrated hydro-processing/de-asphalting and steam cracking and (3) processing of middle distillates and residues using hydrocracking technology (Source: JEP.com).
Apparently, COTC is gaining momentum. However, there is only a selective group of global players active in this domain.
Apart from India’s Reliance, there are Saudi Aramco, Sinopec, Hengli Petrochemical, Shell, ExxonMobil and Total. To highlight the efforts of one of the aforementioned companies, Saudi Aramco is developing two catalytic technologies (thermocracking and catalytic conversion) that promise yields of around 70 per cent of chemicals from the barrel.
As for the contractors/technology providers, the usual suspects have emerged, such as Honeywell UOP, Axens, Chevron Lummus Global, Siluria Technologies and McDermott, the latter having implemented more than 100 hydroprocessing plant designs globally through its joint-venture with Chevron Lummus.
Bio-aromatics
Besides more focused BTX-production based upon conventional feedstocks, there is also the option to use other types of organic feedstocks. There are two companies, Anellotech and BioBTX, that produce drop-ins for BTX and who are in various stages of the TRL-timeline.
The first company uses non-food biomass to produce aromatics such as bio-para-xylene via thermal catalytic conversion. The company has partnered with Japanese drinks producer Suntory to incorporate this compound in a 100 per cent biobased bottle.
BioBTX (the Netherlands) has devised a two-step process – Integrated Cascading Catalytic Pyrolysis – to convert mixed waste plastics into a vapour. This vapour is being led past a catalyst to produce a BTX mix. “We can rely on a variety of feedstocks such as waste plastics or municipal waste”, says Niels Schenk, CTO at BioBTX. “As long as this mix contains carbon, we are good.”
Drop-ins
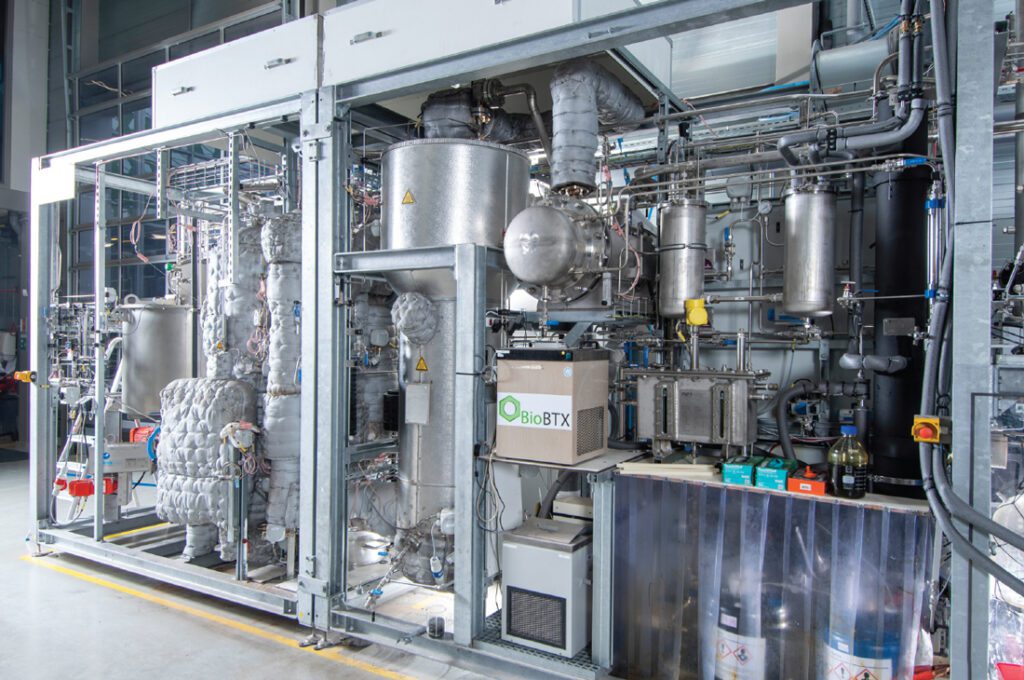
Schenk’s colleague Tijmen de Vries pyrolysis is a relatively new method to produce aromatic compounds from bio-mass. However, this pathway has a disadvantage: the performance of the catalyst (zeolite) is affected by metals and miner als in biomass which in turn impacts the quality of the end product. By keeping these materials out, BioBTX is able to produce aromatics that are identical to their fossil-based counterparts. In case of oxygen (via biomass), this element is removed in the catalytic process.
“We produce drop-in aromatics that are identical to fossil-based aromatic compounds. The main difference is that our product is manufactured based on renewable carbon and as such has a significantly lower CO2-footprint. Ultimately, the industry will gradually shift to these lower-carbon options, partly because of supply-demand constraints (high demand-low supply, ed.), partly because industries also strive to reduce their CO2-footprint. Given the crucial role of BTX in a broad range of applications and industries, we can make a difference as a company.”
Ramping up production
To make a difference, BioBTX is planning to scale up its production to industrial proportions. The company started its pilot production in 2018 to validate the production process.
Currently the investment process for the industrial scale facility is ongoing. The new factory should be operational in 2024, with full capacity realised in 2027, taking in 50,000 tons of plastic waste and transforming this stream into an undisclosed output of BTX.
“The volume we need in terms of input is around 10 per cent of the plastic waste that could be used for chemical recycling in the Netherlands. Apart from this feedstock, we can also rely on 3rd generation biobased feedstocks that are abundant in the region where we are located. This is important as cost reduction is a crucial factor. We need to compete with a mature sector that produces BTX on a massive scale. In the end, we are convinced that we are able to compete on price.
References
Benzene-toluene-xylene (BTX) market. Growth, trends, COVID-19 impact, and forecasts
(2022-2027). Mordor Intelligence, 2020
Identifying breakthrough technologies for the production of basic chemicals. A long-term view on the sustainable production of ammonia, olefins and aromatics in the European region. (CE Delft, 2012)
Reliance Industries to invest billions in Indian COTC Complex, (Processworldwide.com 2019)
Find the best aromatics extraction system for industrial applications (Hydrocarbonprocessing.com, 2018)
How Crude Oil-to-Chemicals (COTC) Technologies are Reshaping the Global Oil Market | GEP(GEP.COM, 2021)
Oil and petroleum products explained: Refining crude oil Peak Fuel Demand Will Occur Within 10 Years (Oilprice.com, 2020)
About this Featured Story
This Featured Story is an article from our Valve World Magazine March 2022 issue. To read other featured stories and many more articles, subscribe to our print magazine.
“Every week we share a new Featured Story with our Valve World community. Join us and let’s share your Featured Story on Valve World online and in print.”