This article provides guidelines for developing a comprehensive critical valve integrity management program, including criticality analysis, maintenance strategies, and monitoring.
Text and images by Miguel Gutierrez, Field Consultant Engineer at Saudi Aramco
Valves are essential components that can lead to major process disruptions, equipment damage, environmental incidents, or safety risks if they fail.
A systematic approach is required to identify and properly maintain valves that are critical to operations. This involves conducting a Valve Criticality Assessment (VCA) to designate criticality classes using quantitative scoring methods. Valves considered as “critical” are any MOV, AOV or HOV valves including manual operated valves of any type identified as per Valve Criticality Assessment (VCA) guidelines with a Criticality Class “A”.
Other valves may also be considered ‘Critical’ by their respective facilities if identified as safety critical elements (SCEs) through an Asset Integrity Management System (AIMS) Study, HAZOP, or Safety Integrity Level Assessment (SIL). The main objective of this program is to ensure all critical valves are identified in the computerized maintenance management system (CMMS) with the correct Criticality Class ‘A’ in order to properly select/assign maintenance strategies through task lists. This includes valve cataloging, creation or review of all BOMs, and critical spare parts lists.
Program expectations
To ensure the effective implementation of this program, it is expected that the operating facility identifies and provides a list of all critical valves identified on the VCA Assessment.
After VCA is conducted, each operating facility through Maintenance must review all valves on the computerized maintenance management system (CMMS) as per above list of critical valves (those with VCI within 0 and 3) and ensure they are assigned with a Criticality Class “A”. In parallel, the assigned BOM structure for each valve must be reviewed and created/completed (In case it does not exist) including the segregation of all those spare parts considered obsolete and no longer supplied by the valve OEM.
Once all valves are reviewed and updated in the computerized maintenance management system (CMMS), the proponent facility must proceed to assign applicable maintenance strategies (PdM, PM and Overhauling Task Lists) after performing a FMEA analysis and as recommended by OEM maintenance manuals adjusting task lists frequency along with internal regularity requirements.
Based in all the above, it is expected from each operating facility to establish a critical valve integrity management program by following a systematic approach ensuring all above steps are fulfilled and measuring the program effectiveness through KPIs on a yearly basis after its implementation.
Structured approach
Each number in this section refers to a corresponding number on the program flow chart.
1. Conduct valve criticality assessment and guidelines for assessing
Conduct Valve Criticality Assessment to identify critical valves (Criticality Class A) by following all steps as per quantitative analysis (VCA Guidelines). Valve Criticality Index (VCI) will define the “Valve Criticality Class” as A, B or C as shown in Table 5.
Valve Criticality Assessment guidelines: The main driver behind VCAG is to identify valves with “Criticality Class A” in order to support operating facilities in identifying the appropriate and adequate maintenance strategies and prioritize operations and maintenance efforts to support delivering the required production target in a reliable and safe manner.
- Valve failure consequence: The failure of a critical valve can have undesirable consequences on the operating facility operational objectives. Such failure consequence can be measured using a Risk Matrix (Likelihood –-Severity/Consequence) in terms of its impact on people, environment, economic (i.e., production losses) and company reputation.
- Valve importance: Valve importance characterizes the consequences of a failure in the process unit (i.e., local effect) as well as the whole processing facility it belongs to (i.e., global effect). It will reflect the interdependence of different valves in the production system locally and globally.
- Valve reliability and maintainability: Valve reliability and maintainability will characterize the overall health conditions and repair considerations of the asset.
- Valve utilization: Refers to the extent of utilization of valves, measured in terms of time or capacity, indicating how effectively the main asset achieves production throughput relative to its potential capacity.
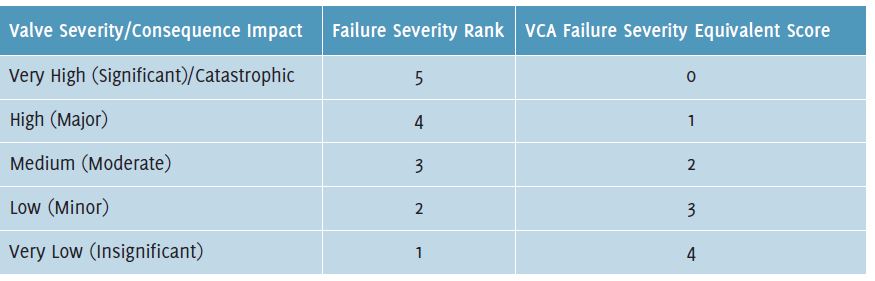
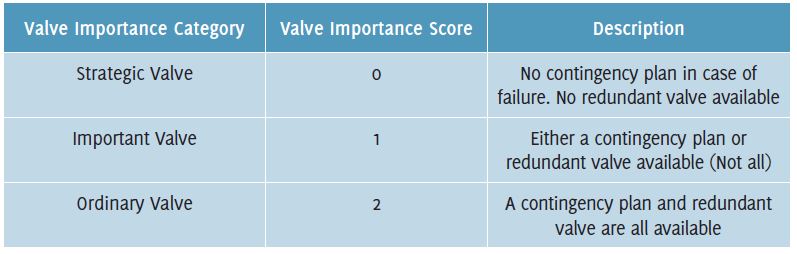
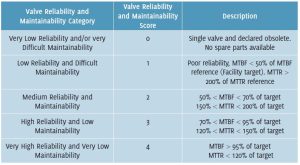
2. Review/update asset BOM structure on CMMS, catalogue materials and create BOM
A material BOM contains a list of components or materials and quantities linked to an equipment. Additionally, the components must be catalogued and the BOM has a valid period and area. With the review and update of the critical valves spare parts assigned on the BOM structure, it is expected to improve spare parts availability and utilization, provide effective material planning, accurate spare parts forecasting and improve material lead time. Additionally, it will be possible to identify spare parts obsolescence and include those in an obsolescence program for future replacement.
The ultimate objective on this step of the process is to ensure that all identified critical valve spare parts are catalogued and stocked in order to reduce equipment downtime and minimize impact on plant reliability and availability.
For the critical valve spare parts cataloguing exercise, the following information is required:
- Spare part approved technical data/specification sheet.
- An official budgetary price quotation from the Original Equipment Manufacturer (OEM) or equipment vendor including vendor official letter, manufacturer part and/or model number, equipment description, budgetary price quoted.
- Valve datasheet showing serial number, model/part/type number and tag number
- Engineering drawings
- Complete bill of materials (BOM)
- Manufacturer’s catalog cuts (manufacturer’s literature) or ordering information
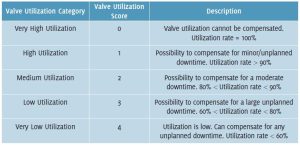
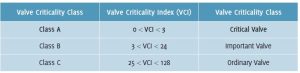
3. Create, review and validate existing maintenance strategies (task lists) on computerized maintenance management system (CMMS) after conducting failure mode and effect analysis (FMEA)
Maintenance strategy is the process of creating and assigning deterministic maintenance tasks to a specific equipment in order to increase its reliability and availability extending its service life.
There are three (3) basic categories associated to valve maintenance strategies as follows:
- Preventive maintenance (PM): This involves the regular and routine maintenance of a valve in order to maintain reliable operation and prevent any costly unplanned downtime from unexpected failure. Typical PM activities include lubrication, cycling, cleaning, stroke testing (partial or full stroke), bolting torqueing, proof testing for EIVs, etc.
- Predictive maintenance (PdM): This technique uses condition monitoring tools to monitor valve performance during operation, enabling the prediction of future failures. This allows permanent fixes or replacements to occur just before failure.
- Overhauling: The repair/refurbishment of an existing valve and/or any of its components by an authorized repair company as per OEM specifications and factory warranty conditions.
The key factors that will enable the successful implementation of a maintenance strategy for critical valves are the following:
- Quality maintenance and failure history data: While most facilities rely on a CMMS to collect and document maintenance history data, there are instances where the quality of the inputted data is insufficient, potentially impacting data analysis negatively. It is crucial to emphasize to operations and maintenance staff the importance of consistently logging critical valve failures and concurrently updating CMMS history to streamline FMEA reviews.
- Utilizing predictive maintenance tools: Such as acoustic emission leak detection, thermal imaging, ultrasonic or eddy current testing, etc. While preventive maintenance (PM) is a good way to keep critical valves from failing prematurely reducing potential downtime, yet the next step is to implement predictive maintenance (PdM) to efficiently gather and analyze the data and proactively take the necessary corrective actions.
- Managing spare parts and inventories: Unavailability of critical spare parts is one of the main reasons of increased downtime and mean time to repair (MTTR) for critical valve failures. Understanding the parts failure modes with their effects and probabilities, will help to identify the spare parts needed minimizing potential downtime.
The implementation of FMEA will lead to the right selection of the asset maintenance strategies by identifying failure modes addressed by each PM task, identifying failure consequences based on hidden or evident failures for each PM task and review PM task for implementation, effectiveness and alignment with business objectives.
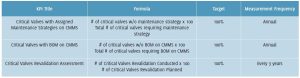
4. Assign maintenance strategies (task lists) on CMMS
Maintenance task lists describe a sequence of individual maintenance activities which must be repeatedly performed within the operating facility.
There are three types of task lists that can be distinguished from one another using indicators:
Equipment task lists have a specific link to a piece of equipment (critical valve). Using equipment task lists, you can define, assign and manage maintenance tasks for critical valves which will help to prepare maintenance plans and issue the required work orders.
Within a task list group, each equipment (critical valve) task list is identified by a group counter, which will facilitate combining several tasks lists in one group. Within the group, the system allocates a sequential number to each individual critical valve task list.
General maintenance task lists are task lists that are used for general maintenance tasks and do not refer to a specific technical object. When using general maintenance task lists, it will be possible to define and manage sequences of maintenance tasks centrally and use them for work scheduling.
Within a group, you can create several individual general maintenance tasks lists and the CMMS system automatically assigns a sequential number and the group counter to each general maintenance task list.
Critical valve integrity management program performance measurement (KPIs)
The implementation of the “Critical Valve Integrity Management Program” must
be aligned with strategic objectives and its effectiveness will be measured by maintaining three (3) basic key performer indicators (KPIs) as follows:
Conclusion
With the implementation of the “Critical Valve Integrity Management Program” by following an established structured approach, it is expected to improve the reliability and maintainability of all critical valves by assigning adequate maintenance strategies and cataloguing of all critical spare parts on the computerized maintenance management system (CMMS), which will ultimately translate in reduced maintenance costs and plant downtime due to unexpected failures.
References available on request.
About the author
Miguel Gutierrez is Field Engineering Consultant at Saudi Aramco with over 30 years of experience in the oil and gas industry, particularly in the downstream business. His focus on piping/pipelines, pressure vessels, heat exchangers, and storage tanks, along with hands-on troubleshooting during plant operations and turnarounds, reflects a comprehensive skill set.
About this Technical Story
This Technical Story is an article from our Valve World Magazine, April 2024 issue. To read other featured stories and many more articles, subscribe to our print magazine. Available in both print and digital formats. DIGITAL MAGAZINE SUBSCRIPTIONS ARE NOW FREE.
“Every week we share a new Technical Story with our Valve World community. Join us and let’s share your Technical Story on Valve World online and in print.”