Linear and rotary actuators rely on well-established engineering principles to operate both throttling and on-off valves. In this article, the author looks at valve and actuator types that he typically encounters in his day-to-day work and also puts forward the advantages that might be delivered by combining both linear and rotary motion into a single actuator.
By Mr V Murugappan, Instrumentation Engineer
Typically, the final control element in a process is a valve, used for either a throttling or on-off function. These two functions each have unique process requirements.
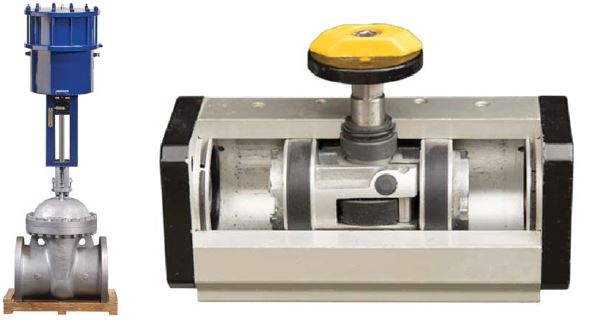
In practice, throttling service is often achieved using a globe valve type. However, in cases where the process media has high viscosity or contains particles then the ball valve design may be preferred. Similarly, if the flow requirement is high then the full pipe flow can be achieved using butterfly valves. On-off service is normally achieved using a butterfly valve which has full pipe flow capability whilst the ball valve may be selected in the case of high viscosity process media or media containing particles. Channel flow requirements call for gate valves. The globe valve is rarely used in on-off service. Whatever the type, all valves require the application of motive force, be that provided by an actuator or via manual operation. This article will consider the type of motion of the plug as it closes against the valve seat. Apart from the type of output motion – rotary and linear – actuators can also be classified by their energy source, such as pneumatic, hydraulic, electric, etc. And in a further classification, actuators can be given labels such as spring and diaphragm, piston with spring, even hybrid actuators with dual mode utilization.
Detailed analysis
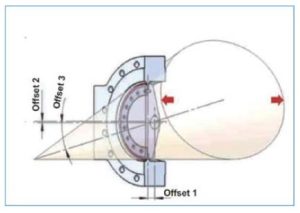
Actuators function by converting the power source into mechanical energy. In the case of a design like the butterfly valve, one or more offsets can be used if enhanced shut-off is required. A maximum of three offsets are possible (Fig. 1).
This means that the contact point deviates from the valve center in all three axes. The benefit is that the transfer of thrust shall be minimal with high seat tightness. In general cases air is used as the energy source for actuator operation. The basic principle of converting linear motion to rotational motion based on compressed air relies on a crank and shaft. See Fig. 2.
Vice versa, a rotational motion can be converted to a linear motion (such as used in car steering) by using a rack and pinion principle. See Fig. 3. In some valves the conversion of motion as well as an offset are used to achieve specific shut off requirements with criticality of the valves being less.
In other cases, such as where the torque requirements might favour the use of an hydraulic or electric actuator, the price of the actuator itself drives up the overall cost of the valve-actuator assembly. In such cases the above principles of motion conversion with offset of the stem and shaft in respective axis can be considered for an effective alternative solution. See Fig. 3.
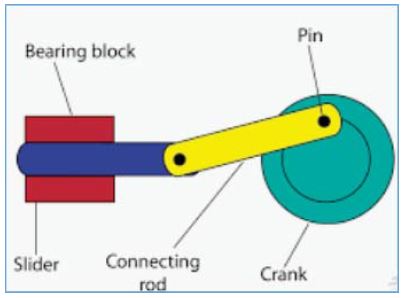
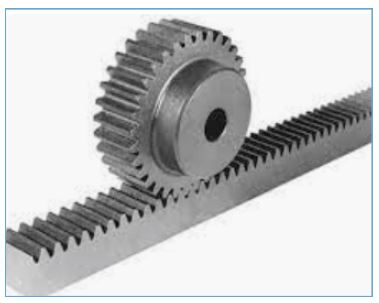
Conclusion
In the author’s experience, linear actuators benefit from ease of mounting, simple operation, accuracy, low maintenance and above all reliability. Rotary actuators offer high thrust delivery, are compatible with multiple valve sizes, and are low maintenance. The author furthermore suggests that the combination/conversion of both linear and rotary motion in an actuator could be especially effective in load transfer and shut-off requirement, require less actuator space, avoid complex actuator designs, and generally be more economical, etc. Hence this article is a futuristic vision in which valves could be easily actuated. It is hoped that these techniques can be established and further developed into more proven solutions for the valve manufacturer and the valve user.
About the author
Mr V Murugappan is an Instrumentation Engineer with a total experience of 16 years. His areas of expertise include valves and power plants. The author can be contacted on: muru17@gmail.com
Disclaimer: This article is fully and solely based on the author’s own experiences and insights and does not necessarily represent the viewpoint of any company and/or other author.
About this Technical Story
This Technical Story is an article from our Valve World Magazine, December 2023 issue. To read other featured stories and many more articles, subscribe to our print magazine. Available in both print and digital formats. DIGITAL MAGAZINE SUBSCRIPTIONS ARE NOW FREE.
“Every week we share a new Technical Story with our Valve World community. Join us and let’s share your Featured Story on Valve World online and in print.”