Whilst oxygen is not flammable, it does support combustion of other materials. Essentially, nearly all substances are combustible in oxygen-rich environments. Therefore the cleanliness of gaskets, packings and other seals in contact with oxygen is essential so that they are not contaminated with substances that could cause ignition.
By Francesca Torriani
Several national and international stan-dards are available which describe the cleaning practices and their corresponding control methods, but unfortunately a clear and unambiguous approach regarding sealing components is still missing. The aim of this article is to give a general overview of the steps and factors to consider when assessing a cleaning strategy.
Before selecting an effective cleaning and control method, several aspects have to be considered and in particular the following:
1. What is the required final cleanliness level?
2. What are the typical contaminants that affect the selected component/seal?
3. What is the condition of the component/seal before cleaning?
4. Is there an environmental and safety impact related to the cleaning method and in par-ticular the cleaning agents?
5. What is the availability and cost of cleaning agents and cleaning process?
6. Does the cleaning process have an effect on component/seal performance?
Acceptable contamination level
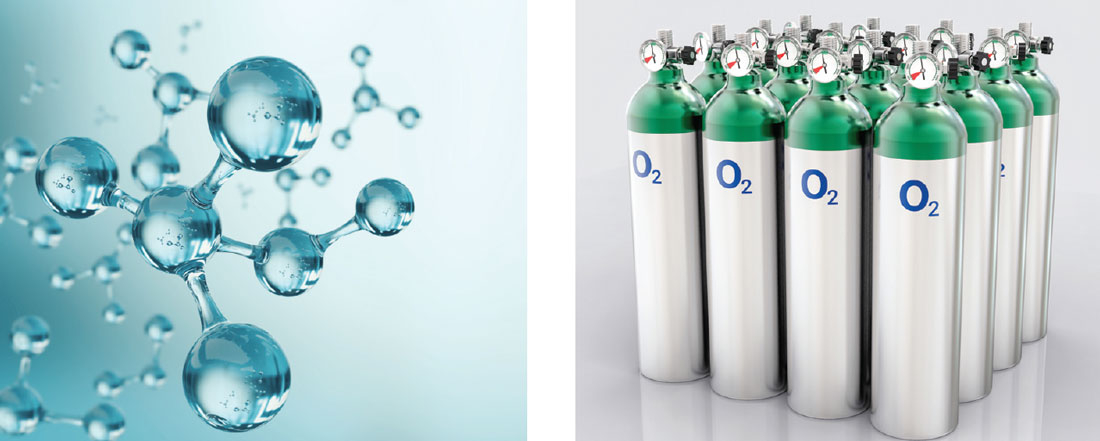
First, what is the required final cleanliness level(1)? To establish the detail of the cleaning regime it is necessary to decide what level of impurity is allowable. The determination of the acceptable contamination level depends on various factors including oxygen purity, pressure, temperature and type of impurity involved. Two main catego-ries of typical contaminants of industrial products exist: fluid/greases and solids/particulates, and for each category and sub-category suggested limits are defined in standards, important examples being ASTM G93, EIGA Doc. 33/18 and ASTM STP 812.
Second, there are several different types of contaminants(2) that can be found on gaskets and seals, including both organic and inorganic material such as oils, greases, cleaning agents, dirt, fibers etc.
An evaluation of the initial condition of the component(3) has to be performed in order to determine whether a single operation will be sufficient to obtain the required degree of cleanliness. It may be possible that a number of cleaning opera-tions will be required such as a preclean-ing stage, an intermediate phase and a final one.
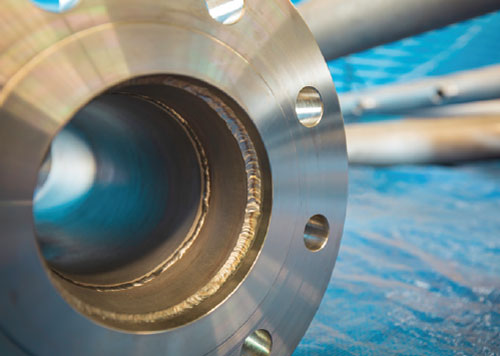
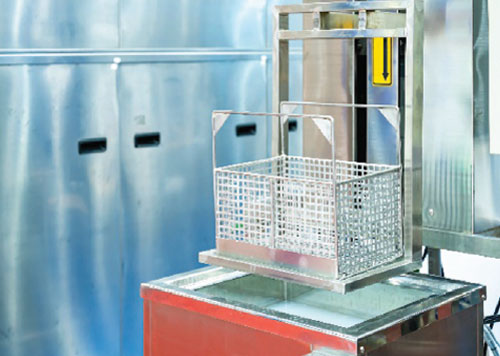
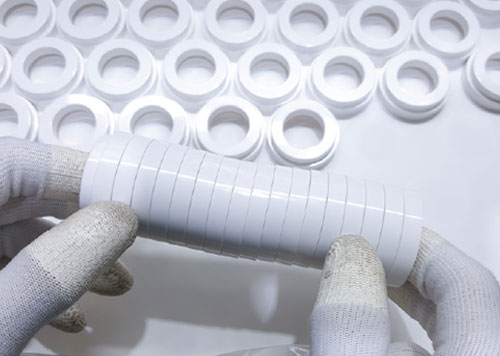
Potential risk
The fourth aspect is the impact on environmental and safety impact related to the cleaning method and in particular cleaning agents. Certain substances that were traditionally used to clean components for oxygen service are no longer permitted because of their effect on the environment. This could be due to ozone depletion, one such example being 1,1,1-trichloroethane.
Other compounds were found to be responsible for photochemical smog and ground level ozone resulting in a potential risk not only for the environment but also for human health. Attention should be given to pollution of surface water and groundwater caused by improper waste disposal or accidental spillage of solvents. Furthermore, cleaning operations can also be a hazard for human safety, in particular for operational personnel, who could be exposed to toxic, carcinogenic, potentially carcinogenic or mutagenic agents. For all these reasons an appropriate safety, health, and environmental risk assessment for a correct use of cleaning agents must be performed before their use.
Intuitive point
Before selecting the cleaning method, the availability and cost of cleaning agents and cleaning process(5) should be taken into consideration. Several points are relevant in this analysis: if a cleaning agent is used, is it suitable for a re-use? If so, how many times could this chemical product be used? Which is the most cost-effective cleaning agent for a determined material? Is it possible to limit the number of cleaning phases thanks to a particular cleaning product?
Also, does the cleaning process have an effect on component/seal performance(6)? This is a very intuitive point that shouldn’t be neglected when selecting a cleaning strategy which shall not jeopardize product function. It has to be checked if the sealing material could be affected by solvents in the cleaning agent. Some materials might absorb the cleaning agent with a consequent loss/reduction of sealability.
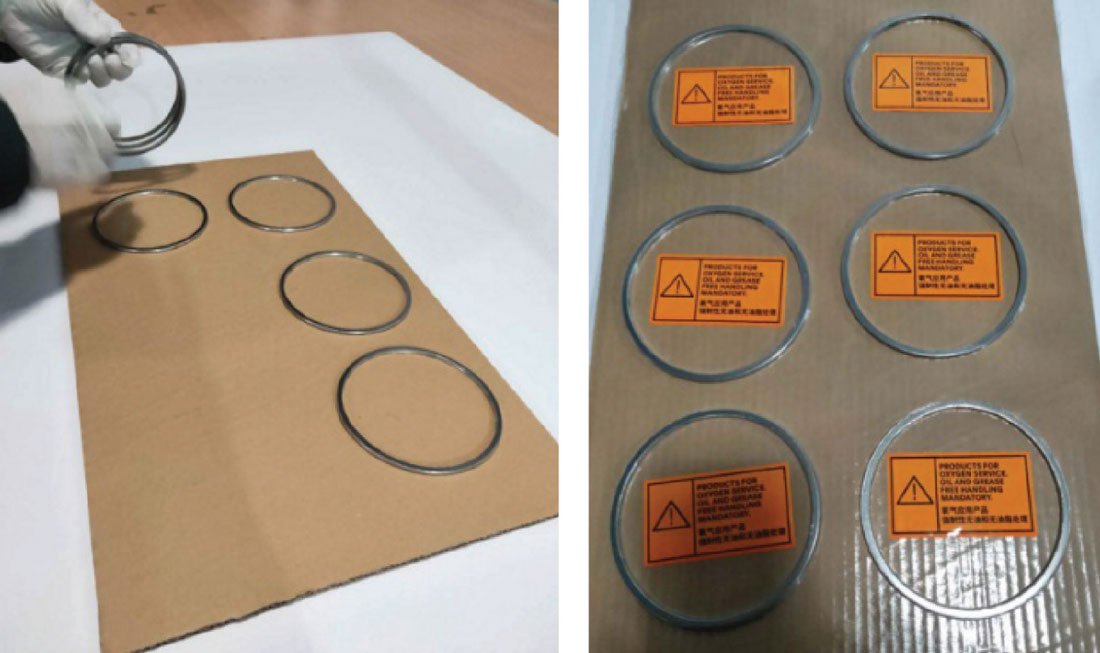
Cleaning methods
Cleaning methods can be categorized as mechanical, chemical, or a combination of the two. In mechanical cleaning, forces which are generated mechanically remove impurities from the selected component. Typically such processes include: abrasive blast cleaning, wire brush/grinding cleaning, tumbling, vacuuming/blowing, “pig” cleaning and ultrasonic cleaning.
For chemical and mechanical combined cleaning methods two main groups can be identified: aqueous cleaning and vapour degreasing. In aqueous cleaning a solution interacts with the surface of the component and its impurities, thus facilitating their removal. The final contaminant elimination is obtained in a second phase with a mechanical method. Typical sys-tems based on this method are: hot-water cleaning, steam cleaning, caustic and detergent cleaning, acid cleaning and solvent cleaning. Vapour degreasing is a process for the removal of soluble organic materials from the surfaces by the continuous condensation of solvent vapours and their subsequent washing action.
Inspection strategies
There is a wide range of control and mea-surement methods that can be selected, varying from simple to complex ones depending on how rigorous the cleaning has to be. Obviously simple inspection techniques have low sensitivity in detecting contaminants but complex examinations are frequently impractical for a general use. Inspection methods can be divided in two main classes: qualitative and quantitative tests. Qualitative analyses usually consist of pass or fail type tests and include direct visual inspection with white light, direct visual inspection with ultraviolet light, wipe test, water break test and gas extraction. Quantitative examinations such as solvent extraction are capable of high sensitivity to quantify even low levels of impurities. For particular applications other type of controls can be utilised, including spectrometric and chromatographic analysis.
Packaging
Once the component has been successfully cleaned and verified as meeting the established cleanliness criteria, it has to be packaged to avoid possible recontamination. Normally gaskets are packaged using new, clean plastic bags and tagged with a label indicating that the component has been cleaned for Oxygen service. However, since plastic waste is one of the biggest sustainability issues that the world is facing nowadays, in the future companies will strive to replace plastic bags with alternative and sustainable materials.
To conclude, organic and inorganic particles have to be removed when dealing with components, such as gaskets, packing, valves and other equipment intended to be used in enriched oxygen environments. To ensure an adequate level of cleanliness, a specific cleaning program has to be implemented during the manufacturing process. Whilst existing standards can help in assessing this process, an unambiguous indication of the strategies to be adopted for gasket cleaning has not been yet defined. Hence, major efforts still need to be undertaken to remedy this and to define a common strategic action.
About the Author
Francesca Torriani is an application engineer for General Packing Italy SpA and ESA Flange Gaskets and Packings Division member. She has a degree in Energy Engineering from Polytechnic University Turin.
References
(1) EIGA Doc. 33/18 – Cleaning of Equipment for Oxygen Service.
(2) ASTM G93/G93M – 19 – Standard Guide for Cleanliness Levels and Cleaning Methods for Materials and Equipment Used in Oxygen-Enriched Environments.
(3) M 034e – DGUV Information 213-074 Edition 9/2018.
(4) Stefan Schulz and Oliver Zach – Oxygen – Component of the air that we breathe and a dangerous substance! – Valve World March 2017
(5) Photos : 1-2-3-4-5-6: Shutterstock
(6) Photos : 6-7-8: Burgmann Packings Group GmbH