Interview with Mr Mrinal Das, Senior Vice President, Projects & Engineering Purchase of Dorf Ketal Chemical Ltd.
By Laura Wang, Valve World
Mr Das has extensive experience with valves and their applications, especially in the refinery, petrochemical and chemical industries. He is currently employed at an end-user company and has previously worked for EPCm and EPC company with a valve manufacturing set up. With his vast experience with adopting various perspectives in this field, both upstream and downstream, Mr Das has a profound understanding of the challenges and opportunities of the current and future valve market. Throughout all of this, he wholeheartedly believes that effective communication between end user, consultants and manufacturer is the best solution for all possible problems.

What is your approach to valves?
“I am currently working as the head of the project department and engineering procurement in my company; Dorf Ketal Chemical. During my tenure of over 30 years, I have worked in areas such as plant operation, project management and commissioning of plants. I have had the opportunity to interact with various valve manufacturers. Also, I have used different kinds of valves in all sorts of chemical, petrochemical and refinery industries in India, the US, Europe, and the Gulf countries. For example, I have worked on the Petronas Malaysia project through Larsen and Toubro Ltd. This has helped me to accumulate vast, diversified, and practical experience. I am thus fully aware of the importance of valves, and how to deal with challenges and obstacles at different stages.”
What would you say is your biggest challenge at work?
“To make sure we are very focused on safety and reliability. I think this is of topmost priority in the chemical industry because we have to comply with lots of safety and statutory rules. We also have a big responsibility towards the employees and community. For me, the first challenge is always to make absolutely sure that my colleagues are working safely in the plant.” “Over the last two decades, the limited number of suppliers meant we didn’t have a great deal of choice. Now, the market has become very open and competitive. Compared with before, the number of options is increasing, which also leads to new challenges. For example, it’s harder to judge who delivers the best quality and timely deliveries, and who can best meet the requirements and specifications.
As the number of options increases, the costs, in both time and effort, to gather the information needed to make a good choice also increases. This brings about another major challenge.”
“Valves should be treated as priority equipment.”
“We have seen more problems with manual valves than with control valves. Control or on/off valves are generally supplied by reputable manufacturers. Because of the large number of manufacturers, quality issues also come up. Furthermore, it’s important for the suppliers to understand the users’ requirements and the circumstances and process conditions under which these valves will be operating at plants. That should all be considered. So far, this has not yet been fully achieved.” “I personally think it would help to have ‘consolidated valve manufacturers,’ rather than having too many players. With this term I mean that manufacturers should also focus on understanding the market, the specifications, and should be technically skilled. Moreover, they should offer quality products and good service.”
How do you deal with those challenges?
“Most of the challenge is that the valves are supplied by manufacturers who don’t exactly know where those valves are going to be used in plants. This is a shared responsibility between the supplier and the user. Users should give clear requirements to the valve manufacturer, and go through the specifications, codes and standards with them.”
“Take the chemical industry as an example. It’s a fast-growing industry, especially in India, Southeast Asia, and China. It’s a huge market. As there is a big demand, the industry will have to face some big challenges because of hazardous chemicals. Users don’t always disclose what kind of chemicals will be in contact with the valves. However, in the case of mechanical processes, seating, leakage, and packing are three things that are very important for valve manufacturers in the chemical industry to know before they offer their valves. Manufacturers have to find out where and how their valves will be installed. Then, it’s important for users to help valve manufacturers understand what they’re exactly supplying for.
Valves should be seen as critical equipment. Leaking valves may cause multiple problems, safety issues, or even a plant shutdown, so they should be treated as priority equipment. They take up a critical role in any process, so users and suppliers should communicate extensively before, during and after operation.”
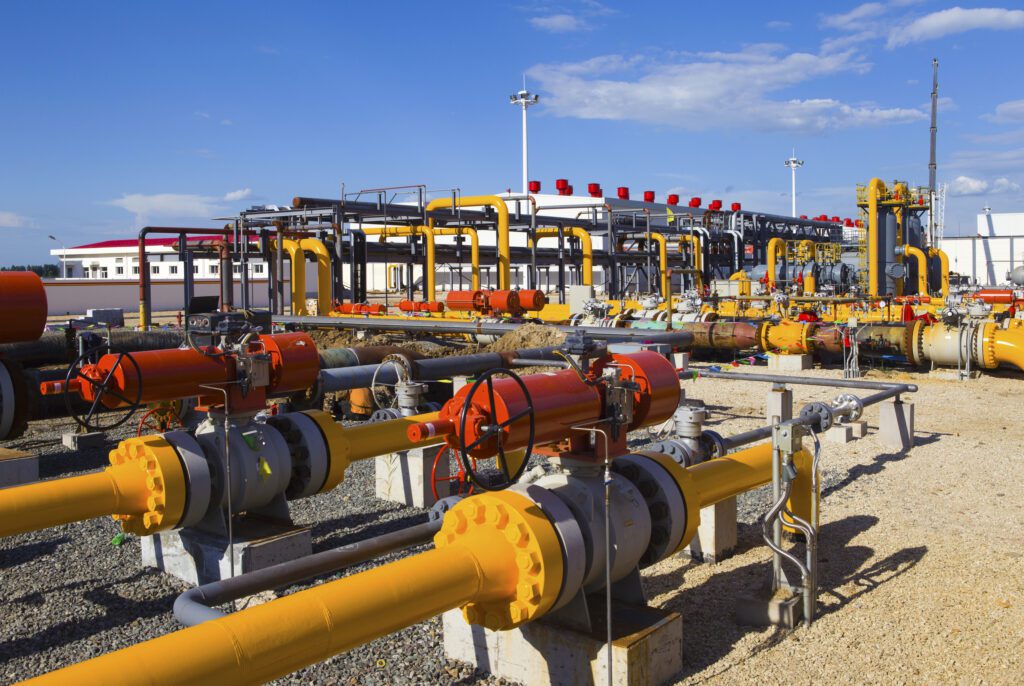
Can you name some highlights or major success stories?
“I started my career at a chemical manufacturing company, and then I spent most of my career at Larsen and Toubro, Jacobs Engineering, Laxmi Organic, and Deepak Fertilisers & Petrochemiclals before joining Dorf Ketal. I have been working on many different projects and plants in the fields of refineries, petrochemicals and chemicals, such as hydrogen plants, ethylene oxide and ethylene glycol plants. Honestly, the fact that these plants have performed very successfully, and without any problems or safety issues, is a highlight in itself. Lots of equipment, valves, instrumentation, and more were involved in this. The satisfying part is that we haven’t compromised on anything we’ve specified, purchased, or what vendors we’ve selected. Safety and efficiency always come first.”
How do you evaluate potential suppliers?
“Suppliers are evaluated based on their reputation, quality, delivery, and past track record. We have a list of valve vendors we issue enquiries to based on their past services and performance in plants. When we need valves for special services, such as hydrogen, chlorine, fluorine, oxygen, cryogenics, to name a few, we search and approach new vendors in this field.
For standard valves, we usually choose suppliers that we’ve already worked with.” “We evaluate possible new vendors. We do a shop visit and check their manufacturing facilities and technical and financial capabilities. We take feedback from clients they’ve previously supplied to. Then, we check their manufacturing process, their casting and forging performance, their skills, and their references. After all of this, we shortlist the suppliers.”
As a member of the 2023 Valve World Southeast Asia Conference Steering Committee, and the Moderator of the Fugitive Emissions panel discussion, what are your expectations of the coming event?
“I am very honoured to have the opportunity to moderate the Fugitive Emissions session, because I think fugitive emissions are becoming a very big issue. Especially for chemical industry, valves are a critical class of equipment that operating facilities rely upon to control the flow of process fluids. A valve has to function correctly and be in compliance with the relevant standards and specifications.
The overall quality and emission control have a big influence on the reliability of the whole plant and site. Both flange and valve leakage could not only cause great financial loss, but more importantly, cause safety hazards. Besides, nowadays, climate change has become a global issue. Climate change negatively affects all living beings. Now is the time to take action to reduce the issues caused by exploiting natural resources. The responsibilities lie with large companies and industries. We invest in ESG (Environmental, Social, & Governance) to achieve a sustainable approach in the corporate world, and to decrease the negative impact of industries on the planet. The proposal for carbon neutrality has led the world into an era of climate economy and set off a green change with both opportunities and challenges. In order to achieve these goals, we should focus on combatting fugitive emissions more.
Valve World Southeast Asia is an important platform for communicating with end users, EPCms, EPCs and manufacturers. Specifically, regarding procurement, the event also enables us to face challenges in the manufacturing sector and learn about future developments.
About Dorf Ketal Chemical
Dorf Ketal Chemicals is a specialty chemicals manufacturer and services provider with a global presence. It offers its customers innovative chemical solutions and quick, decisive response to solve the most difficult problems in the development, commercialisation, marketing and application of specialty engineered chemistries for the refining and petrochemical industries. Founded in 1992, Dorf Ketal has demonstrated product and service expertise in the largest refineries and petrochemical plants in the world. Dorf Ketal Chemical believes that sustainability creates economic value, and contributes to healthy ecosystems and strong communities.
About this Featured Story
This Featured Story is an article from our Valve World Magazine, September 2023 issue. To read other featured stories and many more articles, subscribe to our print magazine. Available in both print and digital formats. DIGITAL MAGAZINE SUBSCRIPTIONS ARE NOW FREE.
“Every week we share a new Featured Story with our Valve World community. Join us and let’s share your Featured Story on Valve World online and in print.”