Hydrogen’s potential to revolutionise our energy landscape is undeniable. Its clean nature, versatility, and ability to store renewable energy make it a compelling option for a sustainable future. From powering vehicles to storing renewable energy, hydrogen is making waves as a potential significant change in the energy landscape.
By Ralf Vogel, ESA
Hydrogen and helium are both gases and can leak if not properly contained. However, there are some differences between the two in terms of their properties and behaviour when it comes to leakage.
Hydrogen is the lightest and most abundant element in the universe. It is highly flammable and can form explosive mixtures with air. Hydrogen gas is colourless, odourless, and tasteless, making it difficult to detect leaks without specialised equipment. Hydrogen molecules are small and can easily escape through tiny openings or leaks in containers or pipelines.
Helium, on the other hand, is an inert gas and is non-flammable. It is also colourless, odourless, and tasteless. Helium is lighter than air and can quickly disperse into the atmosphere if released. While helium is not as prone to explosion or combustion as hydrogen, it can still pose safety risks if it displaces oxygen in enclosed spaces. In terms of leakage detection, hydrogen leaks can be detected using various methods such as hydrogen sensors, gas detectors, or by using soapy water to check for bubbles at potential leak points. Helium leaks are measured using similar methods, but helium is often used as a tracer gas in leak testing due to its low concentration in the atmosphere. It is important to handle both hydrogen and helium with care and follow proper safety protocols to prevent leaks and ensure the safety of personnel and equipment.
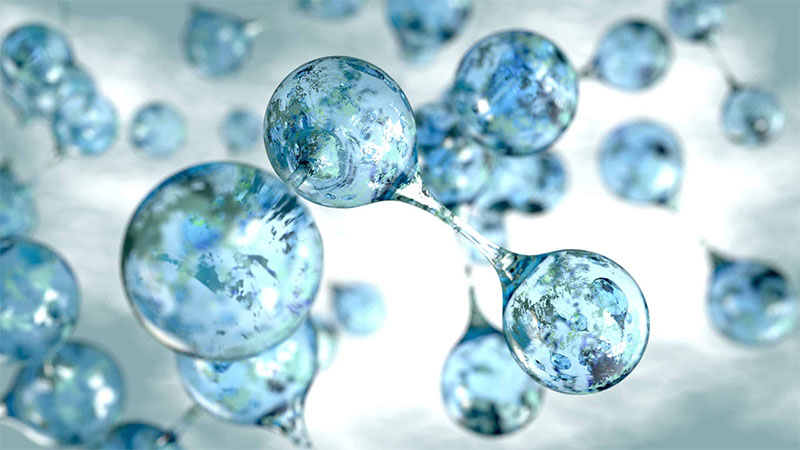
Gaskets
Gasket testing for hydrogen involves evaluating the performance and integrity of gaskets used in hydrogen systems. Since hydrogen is a highly flammable and reactive gas, it is crucial to ensure that gaskets can effectively contain and prevent leaks of hydrogen gas. Here are key aspects of gasket testing for hydrogen:
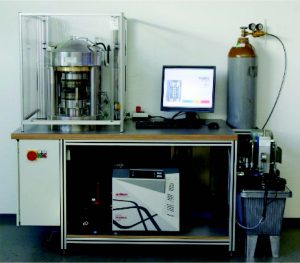
- Material compatibility: gaskets must be made from materials that are compatible with hydrogen gas. Common materials used for hydrogen gaskets include stainless steel, graphite, and certain elastomers. The selected material should have low permeability to hydrogen and be resistant to embrittlement or degradation caused by hydrogen exposure.
- Leak testing: gaskets are subjected to various leak testing methods to verify their effectiveness in preventing hydrogen leaks. These tests may include visual inspection, pressure decay testing, bubble testing, or helium leak testing. The goal is to ensure that the gasket forms a reliable seal and does not allow any hydrogen gas to escape.
- Compression and recovery testing: gaskets are often subjected to compression and recovery testing to assess their ability to maintain a proper seal under different operating conditions. This involves applying and releasing pressure repeatedly to simulate real-world scenarios and evaluate the gasket’s resilience and sealing performance.
- High-pressure testing: gaskets used in high-pressure hydrogen systems may undergo specific high-pressure testing to determine their ability to withstand the extreme conditions. This testing involves subjecting the gasket to elevated pressures to ensure it can handle the intended operating pressure without failure or leakage.
- Temperature testing: gaskets may also undergo temperature testing to evaluate their performance across a range of temperatures. Hydrogen systems can experience temperature variations, and gaskets must maintain their sealing properties under these conditions. Thermal cycling and exposure to extreme temperatures are common methods used for temperature testing. It is important to note that gasket testing for hydrogen should be performed in accordance with relevant industry standards and guidelines, such as those provided
by organisations like the American Society of Mechanical Engineers (ASME) or the International Organization for Standardization (ISO). These standards provide specific requirements and procedures for gasket testing in hydrogen systems to ensure safety and reliability.
Flanges
The EN 1591 standard refers to the European standard for the design and calculation of flanges. It provides guidelines and requirements for the design, dimensions, materials, and testing of flanges used in various industries, including oil and gas, chemical, and power generation. The standard covers several types of flanges, such as weld neck, slip-on, blind, and threaded flanges, and ensures their compatibility and safety in different operating conditions. Compliance with the EN 1591 standard helps ensure the integrity and reliability of flanged connections in industrial applications.
EN 13555 specifies the gasket parameters required by EN 1591-1 and provides the test procedures for establishing the values of these parameters.
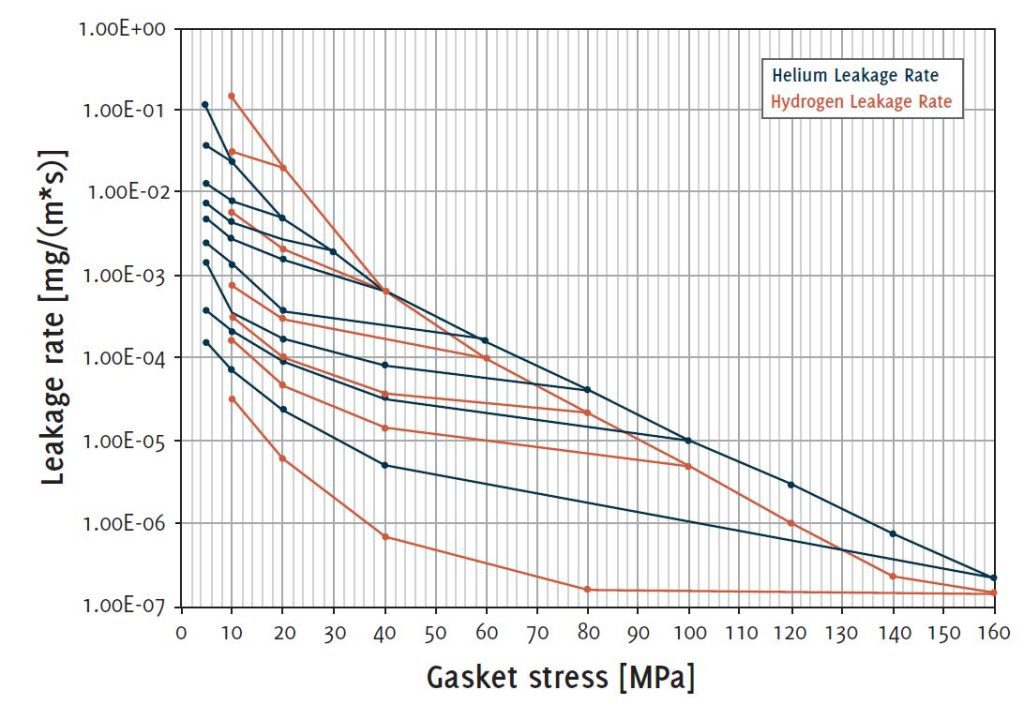
Graphite is a versatile material that can be used especially at elevated temperatures. Several standard graphite gaskets made from sheet material were evaluated at a test laboratory, which is an ESA associated member, and one of these gaskets shall be looked at in this article as an example. The test set-up is shown in Figure 1. Both tests with helium and hydrogen were performed using the same mass spectrometer equipment. Depending on the test gas the mass spectrometer is calibrated with a reference gas sample.
The tests were done according to EN 13555 with 2 mm thick graphite gaskets at room temperature. Standard DN40 PN40 gaskets according to EN 1514-1 were used and the test pressure was 4 MPa. The applied gasket stresses ranged from 10 to 160 MPa. The leakage rates for helium and hydrogen including the loading and unloading curves, are shown in Figure 2. At low stresses up to 30 MPa, hydrogen showed slightly higher leakage rates compared to helium. For higher flange stresses this reversed. All measured leak rates were below the L0.01 limit of the German TA-Luft regulations except for those measured at a very low gasket stress.
To truly comprehend the leakage characteristics of graphite gaskets, rigorous testing is essential. Until now most tests with helium and hydrogen have shown leak rates in the same ballpark range. Unlike hydrogen though, helium, is very unreactive. It will not burn or oxidise and doesn’t form compounds, all of which make it safe and easy to handle. Because of this, researchers prefer helium as the main test gas due to the reduced safety risks.
About the author
Ralf Vogel is a mechanical engineer and has been working in the sealing industry for 28 years. Currently, he is the Technical Director of the European Sealing Association.
About this Technical Story
This Technical Story is an article from our Valve World Magazine, February 2024 issue. To read other featured stories and many more articles, subscribe to our print magazine. Available in both print and digital formats. DIGITAL MAGAZINE SUBSCRIPTIONS ARE NOW FREE.
“Every week we share a new Technical Story with our Valve World community. Join us and let’s share your Featured Story on Valve World online and in print.”