The oxygen scrubber at Fuchswinkel biogas feed-in plant removes oxygen before the biogas enters the natural gas network. Federal rules set a maximum oxygen concentration of 10 ppm.
Gas network operator GASCADE uses SIL-capable AUMA actuators in its Fuchswinkel biogas feed-in plant in order to avoid dangerous shunts between two compressor trains.
By Dr. Jörg Isenberg, AUMA
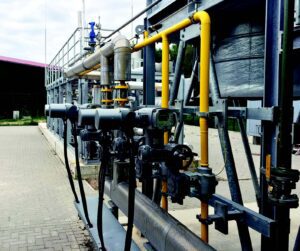
Biogas feed-in plants are used to inject biomethane produced by biogas plants into the natural gas network. Due to the way it is produced, biogas typically contains up to 2% oxygen at the transfer point between the producer and the network operator. If biogas is to be fed into high-pressure gas pipelines, however, current regulations in Germany require that the daily average oxygen content does not exceed 10 ppm (0.001%). This means that oxygen needs to be removed before biogas can enter the natural gas network.
To meet this limit, German gas network operator GASCADE has installed an oxygen scrubber at its biogas feed-in plant in Fuchswinkel, located south of Hamburg in Germany. From here, biogas feeds into the Rehden Hamburg natural gas pipeline (RHG).
Objective: avoiding shunts
To ensure high availability, the Fuchswinkel plant has two compressor trains in a redundant arrangement. Biogas from both compressor trains goes through the same oxygen scrubber, which is located between the second and third compressor stages. With this setup, there is a risk that a control malfunction could create a “shunt”, with one of the compressors pushing gas through the oxygen scrubber and into the other compressor train – in the worst case, even reversing the direction of flow. This could cause considerable damage to the plant and reduce plant availability. The company, therefore, specified a safety instrumented system (SIS) meeting SIL 2 requirements
to interlock the valves connecting the two compressor trains.
Safe AUMA solution
There are two places where a shunt between the two compressor trains might happen: at the inlet to the oxygen scrubber from the second stages of the compressors and at the outlet from the oxygen scrubber to the third compressor stages. At both points, two valves – one for each compressor – control the gas flow. In normal operation, with one compressor active and the other on standby, one of these valves is open and the other is closed. A shunt would happen if both valves were open simultaneously.
To prevent this situation, a safety instrumented system meeting SIL 2 requirements was installed according to IEC 61508. Four AUMA SAEx 07.2 actuators equipped with ACExC 01.2 actuator controls in their SIL version are used to control the valves in question (actuators A to D in the illustration below). These actuators and actuator controls are TÜV certified for safety-related applications up to SIL 3 (when a redundant system setup is used).
Interlock function achieves SIL 2
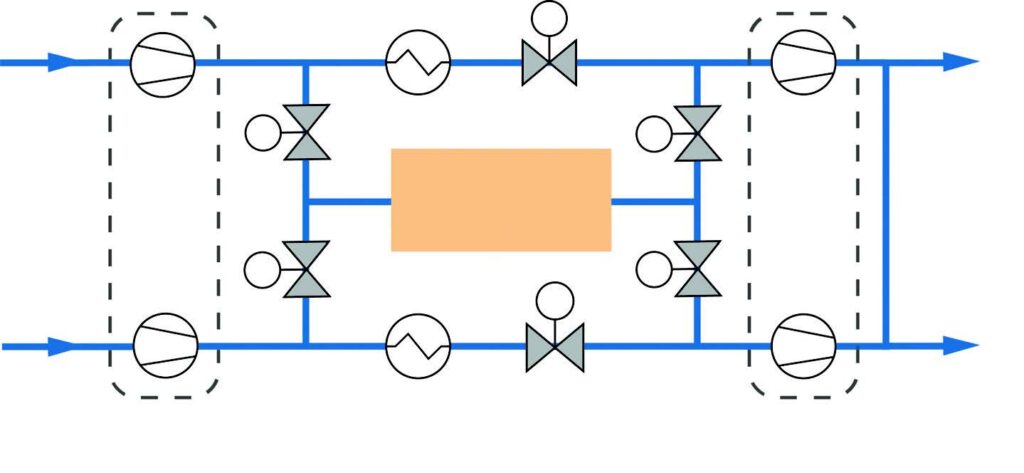
In this SIS the actuators carry out the safety function (SIF) “Safe STOP”. In addition, the actuators are equipped with end position switches that carry out the safety function “Safe end position feedback”. The end position switches are purely mechanical and are suitable for safety-related systems up to SIL 2.
The “Safe STOP” safety function is used to interlock the two compressor trains against each other and avoid a shunt. The “Safe end position feedback” safety function provides the release signal to unlock the “Safe STOP” and allow the associated valve to be opened. It signals if the actuator is entirely in the end position CLOSED. This signal is processed by a safety PLC.
Only if actuator A is completely closed (safe end position feedback CLOSED) will the safety PLC send an additional release signal to actuator B, and vice versa. The same is true for actuators C and D. In the ACExC 01.2 SIL actuator controls, the release signal is hardwired to the input for the safety function “Safe STOP OPEN”. As long as there is no release signal, the SIF “Safe STOP” is active and the actuator cannot open the valve, even if the actuator receives an operation command. Only when a safe end position feedback CLOSED signal is available can the actuator process an operation command to open the valve.
Conclusion
AUMA actuators certified for safety-related applications up to SIL 2 (or SIL 3 with redundant system setup), combined with the SIL 2-capable safety function “Safe end position feedback”, allowed the Fuchswinkel biogas feed-in plant to successfully implement a safe interlock between two compressor trains. This enabled operator GASCADE to reduce the risk of a dangerous shunt by a factor of at least 100 according to SIL 2, and to achieve this with a simple and compact design for the safety instrumented system.
This application is an example of many other similar interlock functions, covering other industries besides oil and gas, that can easily be implemented following the same simple and compact design.
About the author
Dr Jörg Isenberg studied physics in Karlsruhe, Germany and Eugene, USA. He received his Ph.D. in physics from the University of Constance, Germany. As a Product Specialist based at AUMA, he is responsible for all products used in functional safety applications.
About this Featured Story
This Featured Story is an article from our Valve World Magazine December 2022 issue. To read other featured stories and many more articles, subscribe to our print magazine. Available in both print and digital formats. DIGITAL MAGAZINE SUBSCRIPTIONS ARE NOW FREE.
“Every week we share a new Featured Story with our Valve World community. Join us and let’s share your Featured Story on Valve World online and in print.”