High pressures and temperatures and/or highly corrosive media pose higher demands on control valves. For example, the use of supercritical steam in power plants requires specific alloys to withstand rapid increases in temperature and pressure. In this article, several severe service applications are discussed. One lesson: the most elaborate designs are not always the most cost-effective solution.
By Hans D. Baumann
As for supercritical steam, pressures and temperatures typically rise above 220 bar (3,200 psia) and above 374 °C (706 °F). Despite the many technical difficulties, super-critical steam is used because the higher temperatures on one side and the condenser temperatures on the other end offer higher effective thermal energy levels. As a result, these systems have higher operating efficiencies than power plants operating with lower steam temperatures.
Specifically for control valve design, valve manufacturers need to find the right metal alloy for mitigating the effects of thermal shock. Ignoring the latter can lead to thermal stress problems able to cause severe failures. This happened with first generation valves that were machined from a solid, four-sided block of steel. Some of these valves failed due to stress crack penetrating
30 mm thick walls.
Aerodynamic sound
During my experiences in the late 1950s, I used blocks of cone-shaped forged metal, base upon a modified chrome-nickel alloy. The exterior was countered by machining to follow the shape of the interior cavities using the minimum possible wall thickness using a 0.2 per cent yield limit at the given temperature as a criterium.
Separate inlet pipe nipples were welded on both sides of the housing for stress balance. Since these power plants used once-though boilers, there was no pre-heating, subjecting the valve to the full-service temperature. To soften the impact, I lined the inlet nipples with a thin-walled tube. This tube was welded to the nipple wall on one end in order to allow longitudinal expansion of the liner and so absorb the initial thermal shock from the pressure carrying walls.
While dealing with high-pressure reducing steam valves, I got my first experience with aerodynamic sound. We tried to alleviate the noise by welding a multi-holed plate inside the large outlet port of a turbine by-pass valves. These proved somewhat effective (now a standard practice). In those days (1957), Siemens, then my employer’s customer, contacted universities to learn about the theory of sound.
Urea
Urea let-down is another severe service application that puts high demands on control valves. Urea is an organic compound used primarily to produce fertilizer. It is highly corrosive and the choice of valve body material is limited to either 316L or specialty grades, such as duplex stainless.
The high-pressure let-down occurs at the end of the production cycle. A special angle valve is employed with a long, curved inlet port in order to avoid unnecessary turbulence in the valve body. There is a gradually tapered extension downstream of the valve’s orifice, allowing for a smooth outlet jet and to avoid crystallization. The valve body typically is forged to provide homogeneous material throughout. This design, understandably, drives up the cost.
Natural gas
In the upstream of the natural gas value chain, the challenge is to reduce high well pressure, which rises typically above 3000 psi. This reduction, ultimately down to 1050 psi, is necessary to allow dehydration to prepare for pipeline shipment. Problems encountered are high sound levels and erosion due to entailed sand and water droplets. Here again, angle valves are proven to be effective. Low noise trims are problematic, since small passages tend to plug up while large passages tend to wear out due to erosion.
The attached photo shows a valve that has been fitted with a long multi-step trim. This trim was effective in terms of noise reduction but the plug had to be replaced periodically due to erosion. Conventional control valves encountered up to 111 dBA sound levels with pipe celebration levels above 14 times the acceleration of gravity. Special valves, such as the one in the image, could reduce sound to below 80 dBA.
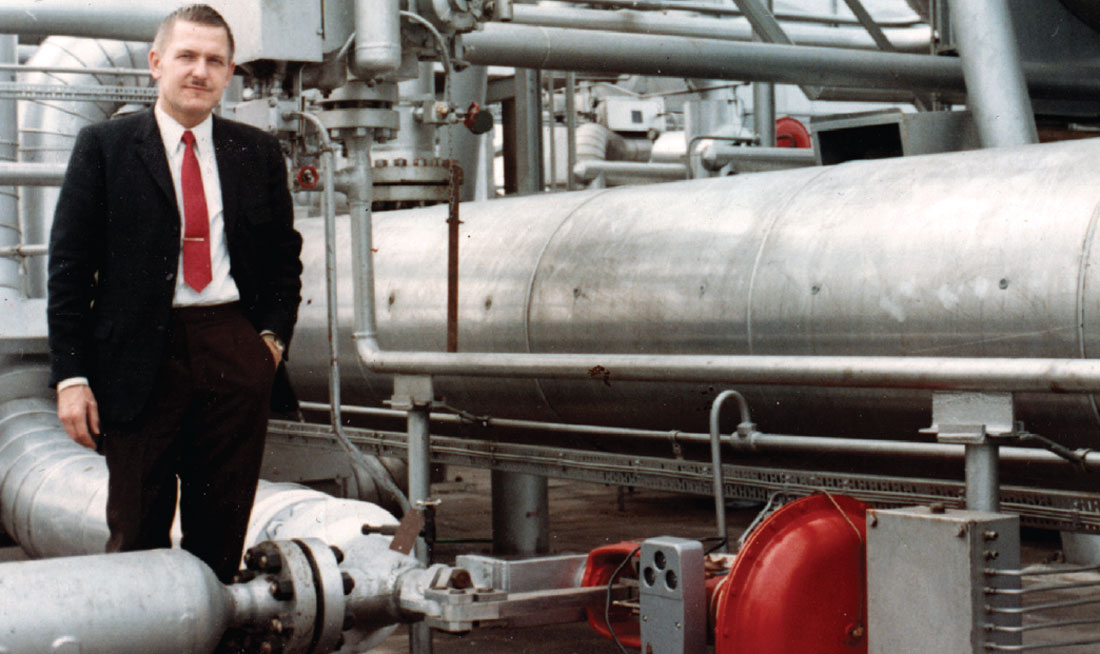
Flow control challenges
The control of flow of slurries, in particular in the mining industry, has proven to be a huge challenge. For these applications, pinch valves or Saunders-type valves are employed. The problems are cavitation, erosion, and the fact that these valves make poor control valves due to the absence of an acceptable flow characteristic.
Rubber-lined butterfly valves would be acceptable for flow control but suffer from similar problems of cavitation and erosion. Here is one way to reduce such ill effects. Try to keep the pressure drop below 15 psi, the resultant turbulence velocity is low enough to make the solid slurry particles bounce-off the elastic rubber, instead of tearing into it.
Cheap solutions
One typical case of slurry application is bauxite mining. One of my customers periodically ordered the same cheap cast iron butterfly valve. On inquiry, I found that they installed such a valve to control bauxite slurry till it was worn out in a couple of weeks, at which time it simply was replaced with a new one. I agreed that this was a very cost-effective solution and good for our business!
This reminds me of a story. The German rocket designer Werner von Braun was asked why the burner chambers of his rockets were made of cast iron, since they would last only for a short period. His reply was: “That is correct, but they last long enough to reach the target.”
About the author
Dr. Baumann, a former VP of Masoneilan and Fisher Controls, is now an international consultant. He is credited with 106 US patents and has authored 140 publications and seven books, including the Control Valve Primer now in the fourth edition. Dr. Baumann is an Honorary Member of ISA and a Fellow Member of ASME. He can be reached at hdbaumann@phbinc.net