^ The Crane FK-TrieX
Article By Sarah Bradley (KCI Publishing), Mark Shorback and Jörg Massow – Crane ChemPharma & Energy, A business of Crane Co.
___
Article By Sarah Bradley (KCI Publishing), Mark Shorback and Jörg Massow – Crane ChemPharma & Energy, A business of Crane Co.
___
In severe service industries, safety, reliability and efficient operation are paramount. The performance requirements and demands on valves are often extreme, and unusually, a single valve will not match all of the criteria.In the push to maximize industrial capacity and efficiency, valve selection has always been a challenging exercise. Many times, design guides will select a valve that meets all specifications of the process, yet it may be cost-prohibitive.
This is where a compromise often becomes necessary. Specific valve attributes need to be prioritized, while economics might take Crane ChemPharma & Energy carries forward the illustrious 165+ year history of Crane innovations, with their new full port metal seated Triple Offset Valves that build on improvements of previous offerings, to represent the best of all their designs wrapped into one powerful, versatile valve, the company states. By Sarah Bradley (KCI Publishing), Mark Shorback and Jörg Massow – Crane ChemPharma & Energy, A business of Crane Co.precedence over other attributes. The quandary of what features can be sacrificed to fit the system into the allotted budget.
The challenge of severe service
With this in mind, the Crane engineers and development team conceived the idea for the new FK-TrieX. The Crane FK-TrieX design engineers studied the rigorous performance requirements of severe service applications like LNG, molecular sieve packages, EDC/VCM, PVC Production, refinery reforming, ethylene production, highly reactive fluids, bulk storage, terminals, pipelines, among others. All of these applications require economical, highperformance valve solutions with a wide range of performance capabilities.
These severe service applications require valves to meet a wide range of demanding criteria including absolute tight shut-off or bi-directional zero leakage; the ability to withstand high temperatures, often exceeding 1,000 degrees F; a low weight; complete fire safety; low-torque requirements for operation and ease of automation; maximum throughput and efficiency at high flow rates, and the ability to handle a high ratio of solids, often up to 50 per cent.
Until the Crane design team set out to build the Crane FK-TrieX, there was no one single valve type that would address as many of the above criteria, the company states.
Powerful hybrid
At Crane, the design group applied their vast experience and history of valve design expertise to enhance the typical metal-seated valve performance, offering a fresh perspective in valve selection.
This latest Crane FK-TrieX valve design takes the best features of the severe service ball valve portfolio and “harnesses the economy and reliability of a triple offset valve platform to develop a powerful, versatile hybrid. This innovation could be defined as a full port triple offset ball valve”, the company states.
The Crane FK-TrieX is an authentic triple offset design employing all of the geometrical advantages of a triple offset sealing element to achieve bi-directional zero leakage, certified to API 6D and API 598 specifications. Crane says this level of zero leakage specifications is rarely if ever seen in authentic full port design fully pigable fire-safe designs.
High valve flow coefficient
This new Crane valve also allows for line size reduction, thanks to the high valve flow coefficient that this full port design enables the FK-TrieX to deliver, surpassing the conventional TOV Cv by a factor of 4x to 8x +.The high Cv makes the FK-TrieX an extremely important innovation for existing environments where limited flow causes contamination and clogging, necessitating frequent valve replacements. “This feature also makes this valve an excellent candidate for application in the construction of new pipelines, where structural support and the weight of the valve and line are a constraint. With its high Cv, a lighter, smaller line size can be used, reducing the weight and thus, the structural support needed for the system”, he company states.
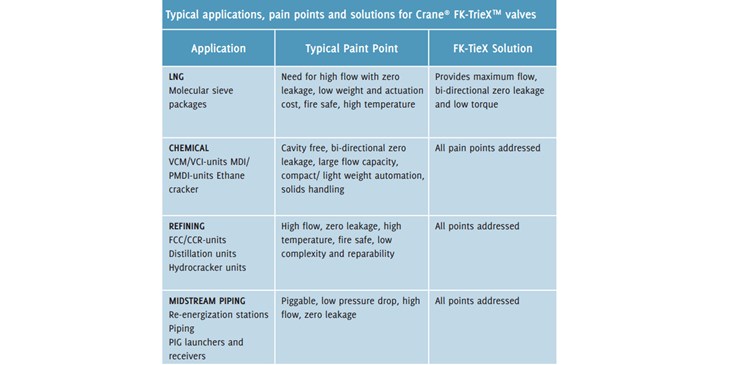
Ease of inspection, repair, and replacement
The Crane proprietary end-entry securing and sealing configuration “guarantees suitability for dead-end service, while still providing for the safe removal of the body seat for inspection and replacement. This body seat is the first-ever single-seat bidirectional valve design that meets API 6D specifications.”
The hard facing options for the TrieX seating surface are vast, including materials beyond the typical selection, greatly boosting the versatility of the valve. This seating can be easily resurfaced if the need arises and the body seat itself can be replaced, another first in the triple offset valve category.
The Crane FK-TrieX design is engineered to also address as many aspects of the valve selection matrix as possible, offering a wide range of materials, high flow, bidirectional zero leakage, low torque, light weight, low emissions, fire-safe high-temperature resistance in a one-piece body configuration. These versatile attributes of this valve offer design professionals the opportunity to decrease the need for compromise on valve selection, while still achieving process outcome and budget compliance, Crane states.
Unmatched safety
Crane states its FK-TrieX severe service isolation valves are designed for safety on all fronts, safeguarding personnel, operations, and assets from fire and explosions, leakages, and environmental damage. The triple offset sealing mechanism provides repeatable bi-directional bubbletight shutoff at full differential and low pressures. The torque seating evenly distributes compression of the seal along the entire sealing area, enhancing the tightness of the seal.
Fugitive emissions are not only a safety risk but are considered a significant contributor to global greenhouse gas emissions, with estimates putting the share of fugitive emissions between 5 and 12 percent of the total global output.
“In today’s environmental-conscious climate, emissions control has become a significant consideration while specifying valves, and the Crane FK-TrieX meets the highest standards, with certifications to API 641 and ISO 15848 BH C03 at 750 degrees F. The stem seal technology is built on the same innovative platform as the Crane FKX9000, providing critical performance in an uncompressing design.”
The Crane FK-TrieX also meets the rigorous standards of the API 607 fire test for quarter-turn valves confirming its pressure-containing capability during and after the test.
Reliable operations
The innovative design of the Crane FKTrieX also maximizes durability, reduces unplanned shutdowns from valve failures, and reduces planned valve maintenance time too, by more than 50 per cent, the company claims. “On the rare occasion where repair is required, the ease of serviceability and the ability to field repair the hard-faced seats ensures the lowest possible downtime for the operation.”
This reliability originates from a few significant characteristics of the Crane FK-TrieX. “The frictionless sealing mechanism minimizes wear that is typically seen in other technologies. The wear typically attributable to spring force and other impinging forces on the seat of the valve is absent in the FK-TrieX.”
The replaceable stellite-welded seat with an RC hardness rating of 40 and flexible laminate seals of this valve provides excellent shutoff and approximately double the life of regular stainless-steel seats.
The cavity-less self-cleaning design ensures solids are not trapped in valve crevices, significantly reducing the likelihood of premature failure. Additionally, the API 6D standard full-bore design means that Pipeline Inspection Gauges (PIGs) and cleaning scrapers can pass through the valve in fully open condition, allowing for cleaning of the system without the need for valve removal. This standard full-bore architecture affords an optimal flow profile with high Cv and low-pressure drop across the valve.
Lower overall operating costs
Relative to existing technologies, the Crane®FK-TrieX enables systems to realize upfront and long-term cost savings by virtue of its high Cv value that allows for a reduction in line size throughout the system. The savings from smaller actuators, 20 per cent lower structural support cost and a reduced cost of planned maintenance of more than 50 per cent, all add up.
The modular seat design of the FK-TrieX means the seat and laminate seals can be replaced individually, without having to replace the entire valve, further reducing maintenance costs. Moreover, these replacements can be carried out in the field, eliminating the need to ship the valve to service centers.
The quarter-turn design ensured that the valve can be actuated and operated without complex and oversized actuators, further reducing set-up and operation costs. The single-piece body architecture of the valve reduces its weight by up to 20 per cent, decreasing structural support costs. The single body design also means a reduction in possible leak paths.
Engineered with the same face-to-face dimensions as other technologies and complying with the standard ASME B16.1 Long Pattern, means the FK-TrieX can be readily swapped with other standard valves, without creating modifications to the system.
Built on tradition
Muta in Slovenia is home to the stateof-the-art assembly center that manufactures the Crane FK-TrieX line of valves. Steeped in the blacksmith tradition of Muta in particular and the rich metalworking and steel production and processing heritage of Slovenia in general, the assembly center is once again an example of Crane innovation, building on a rich legacy.
Located in the foothills of the Austrian Alps, this center of excellence has been producing the Crane FKX9000 triple offset valve line for the last four years with “impeccable quality control, and the FK-TrieX will utilize many of the same processes and equipment.”
As the chemical and energy sectors continue to evolve, greater demands are being placed on system components, as customers seek ways to maximize effectiveness and balance costs, without compromising on application requirements for the most difficult sealing and flow control needs.
“Crane FK-TrieX “full port triple offset ball valve” offers an effective solution for severe service applications with the ability to perform under demanding conditions while offering unmatched safety, reliability of operations, and a greatly reduced startup and lifetime cost, thanks to its innovative engineering.”
About Crane
Crane Co. is a diversified manufacturer of highly engineered industrial products. Founded in 1855, Crane provides products and solutions to customers in the hydrocarbon processing, petrochemical, chemical, power generation, unattended payment, automated merchandising, aerospace, electronics, transportation and other markets. The Company has four business segments: Fluid Handling, Payment & Merchandising Technologies, Aerospace & Electronics and Engineered Materials. Crane has approximately 11,000 employees in the Americas, Europe, the Middle East, Asia and Australia. Crane Co. is traded on the New York Stock Exchange (NYSE:CR). For more information, visit www.craneco.com.
Crane ChemPharma & Energy
Crane ChemPharma & Energy (within Crane’s Fluid Handling segment) designs and manufactures a variety of high-performance products including: highly engineered check valves, sleeved plug valves, lined valves, process ball valves, high performance butterfly valves, bellows sealed globe valves, aseptic and industrial diaphragm valves, multi/quarter-turn valves, actuation, sight glasses, lined pipe, fittings and hoses, and air operated diaphragm and peristaltic pumps.
Its trusted brands (in alphabetical order) ALOYCO®, CENTER LINE®, COMPACNOZ®, CRANE®, DEPA®, DUO-CHEK®, ELRO®, FLOWSEAL®, JENKINS®, KROMBACH®, NOZCHEK®, PACIFIC VALVES®, RESISTOFLEX®, REVO®, SAUNDERS®, STOCKHAM®, TRIANGLE®, UNI-CHEK®, VALVES®, WTA®, and XOMOX®offer customers complete and innovative product portfolio designed for the most demanding corrosive, erosive, and high purity applications. Among the industries served are the chemical processing, biotechnology, pharmaceutical, oil & gas, refining, and power generation.
Crane Co. is traded on the New York Stock Exchange (NYSE:CR).
For more information, visit