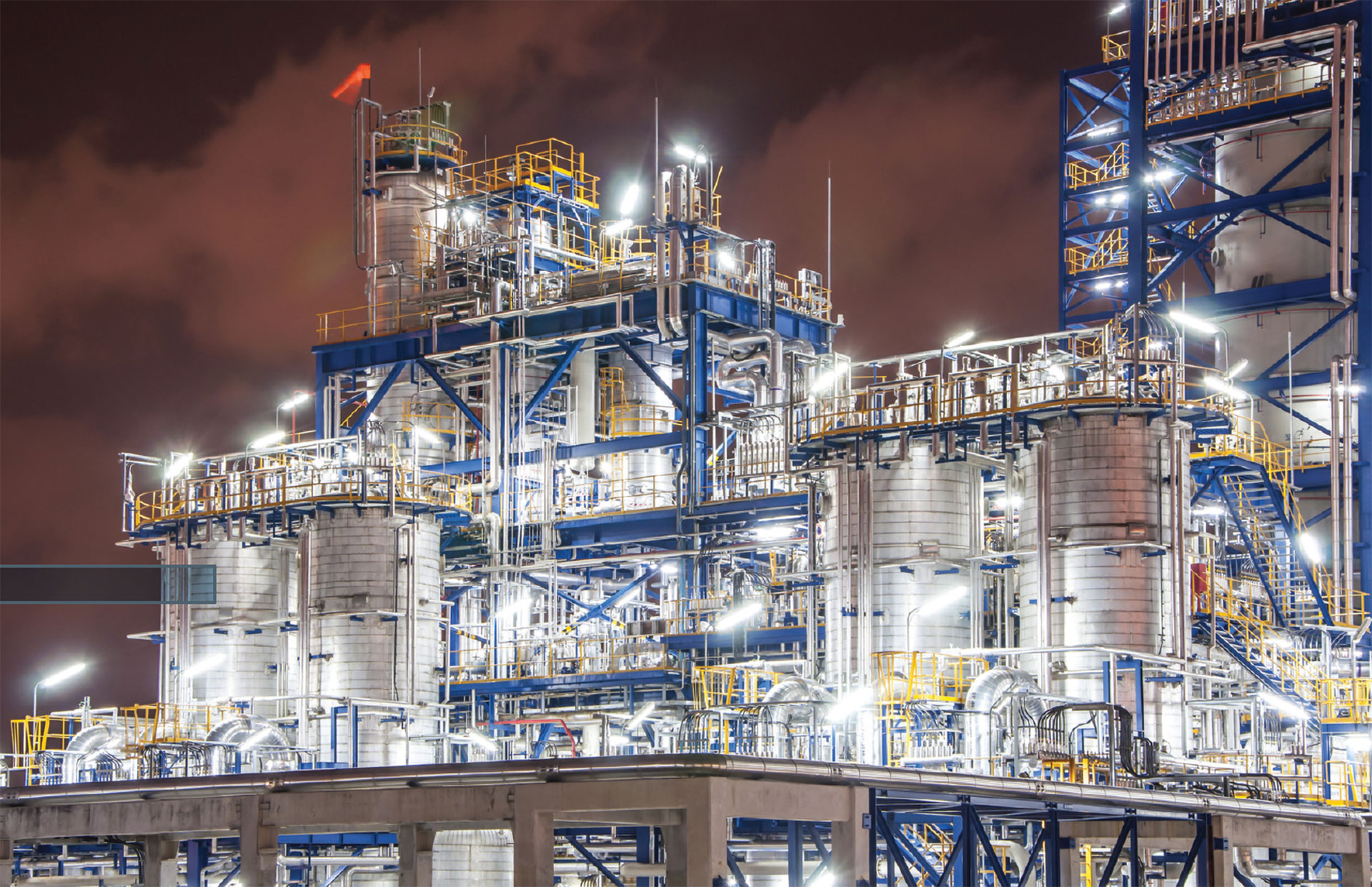
Mr V Murugappan, Instrumentation Engineer at Dow Chemical International Pvt Ltd. discusses the advantages and disadvantages of using a single valve for both throttling and on/off functions.
By V Murugappan, Dow Chemical International Pvt Ltd
Valves are normally the standard selection for final control elements where they perform throttling or on-off function based on application and process demand. However, about forty years ago in process plants, some processes had a single valve which was used to perform both throt-tling and on-off functions using an analog signal from Logic solver. In such instances these valves carried out the regulatory function during normal process operation, while during process upsets or emergency situations either direct 4 or 20mA was used for isolating the process. A single valve used for both throttling and on-off functions has its own advantages and disadvantages as discussed in this paper.
Introduction
Automated valves are important for safe, reliable, efficient operation of plant. The throttling valve plays a major role in plant control and stability. Based on the process requirement, automated valves are classified as control and on-off final control elements. By definition, a control valve is used as a throttling valve in process control. During emergencies like plant trip, system failures require the process to be isolated and control valves are operated as on-off valves in cases where dedicated block valves are not available. Also, to isolate the process for maintenance an emergency block valve function is required.
In olden days, plants were restricted in quantity of IO’s for optimum design due to the limited availability of digital technology and Smart control systems. Even manual control loops were employed to limit the quantity of signals connecting to logic systems. Such plant design constrains were managed using the dual-purpose valves, manual loop valves. A classic example for risk management in those days was a single valve used for both controlling and shutdown functions. Throttling valve used the 4-20 mA varying analog signal to achieve the desired process control and same valve was operated using either of 4 or 20 mA to shut down or drain out the process medium to safety on emergency condition. Since majority of the valve is built of mechanical parts, with proper material selection the valve was ca-pable of meeting the dual-purpose requirements. Nowadays with plant safety and reliability as top priority a lot of emphasis is placed on final control elements design. This coupled with the fact that the DCS and PLC system have become more powerful and capable of handling very large number of IO’s, there is very limited restriction on the quantity of valves. In such cases every part of the process has dedicated control valves and on-off valves respectively as required.
This paper elaborates the usage of a valve in dual purpose case with detailed analysis of the pros and cons of the approach.
Detailed analysis
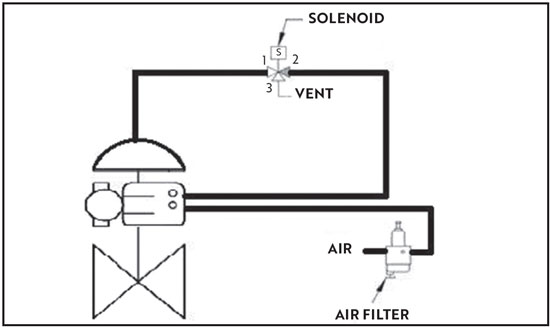
Valves continue to be selected as first choice of final control elements. The valve industry has undergone lot of development and sophistication, far from the first ever valve which was just a pump governor to prevent spillage of a water tank.
Nowadays control valves are operated through positioners for the control func-tion via the 4-20 mA from DCS. When the control valve is also part of shutdown op-eration then a solenoid may be introduced between the positioner and actuator to carry out the trip function. In earlier design control valve without an exclusive trip SOV used same 4-20 mA analog signal from DCS to both throttle as well as either open or close the process depending upon the process requirement.
Such example of introduction of solenoid in valve loop is shown in Figure 1 for reference purpose. In case of double-acting actuator, the configuration is more complex with additional accessories.
New plant is designed considering as throttling and on-off service separately and never considered as single valve for both purposes. Be that as it may, it is interesting to list and compare the pros and cons of using a separate valve for control and on-off function or to use a single valve for both duties. Please see Table 1.
There are of course unique requirements for dedicated control and on-off valves. On-off valve specific requirements can include the need for open channel handling, abrasive service, low pressure drop inverse huge flow, etc. On other hand, control valve has also unique requirements which are high Dp inverse low flow requirement, critical valve problems like cavitation, high noise, flashing, etc. Such specific requirement may opt for dedicated valve instead of a dual-purpose valve. Apart from such general categorizing of valve types, valve selection will also depend on the specific process and plant requirements.
In plants built forty or fifty years ago it is often possible to find valves with tags bearing acronyms such as EFV and ELV. These indicate the valve is normally operated as flow or level control valve and in emergency case can be used as an emergency block valve. Service in such cases would have the requirement of normal operation as throttling requirement and in emergency case to depressurize pressure containing equipment. Provided the valve has been properly manufactured using appropriate materials, has been designed for rugged use, has been fitted with an actuator capable of handling the thrust requirements associated with control and on-off duty, and has been fitted with internals (plug/ball and seat) that can close properly, then such a valve can deliver good value addition such as cost saving, cabling, IO assignment, carbon footprint reduction, etc.
In earlier plant designs use has been made of locally operated control loops having pneumatic controllers and, in such cases when DCS monitoring was not available, operation of such local loops also used a single valve for dual control and on-off application obtaining trip from a nearby instrument which would be the governing parameter.
Today, many existing plants continue to use such dual-purpose valves. Normally, conversion to a situation with two separate valves is only considered if a situa-tion arises such as passing, vibration, etc. And in such cases these changes would cause major field contractor attention, and typically all repair/replacement work would be scheduled for a regular plaint shut-down.
The disadvantage of valve used as dual purpose is that the valve could lose the inherent mechanical characteristics by trim deterioration, could suffer valve seat damage, controllability during normal operation, cannot be added to SIS loops in future, sluggish response over a period of prolonged usage as dual purpose, reliability of process stability etc.
Leakage of such design is again question-able since for a control valve leakage as per IEC 60534-4 is classified as six different classes whereas for on-off valve the leakage mostly complies as per API 598. Hence dual-purpose valve needs to accept the leakage requirement as per inherent design. Also, the bidirectional flow requirements require two separate dedicated valves, as in general dual operation valve would add more complex-ity for bidirectional leakage class requirements.
Air consumption of the valve is again an important factor for dual purpose valves. If the actuator is single acting, then it is more feasible since for double-acting actuator the air consumption would be designed considering the inherent design in general considering seat closure and the stroking time requirements.
For new dual-purpose valve procurement, additional checking parameters are available to measure valve performance with valve signature testing, response test, diagnostic test, hysteresis, friction test, etc. These test reports can be used as reference data. Valves can then be retested following a period of operation to determine whether the valve performance is in accordance with the process requirements or is showing signs of deterioration.
Conclusion
Dual purpose valves are a well-established concept, having been used in process installations since the early days. Speaking gener-ally, assuming the process is low critical then dual-purpose valve can fulfill the process requirement by compensating on certain criteria like leakage and precise control. Moreover, dual-purpose valves can have advantages in retrofit projects due to space constraints, cost reduction, faster turnaround, etc. Also, good performance of an installed dual-purpose valve can promote a ‘like-for-like’ replace-ment strategy. However, if a situation arises requiring these valves to be revalidated, for example, due to model obsolesce, plant revalidation and turn around, performance issues, etc, then there can be compelling reasons to replace the dual-purpose valve with separate valves categorized into control and on-off valves, respectively. For new-build plants it is recommended to have separate valves for dedicated control and on-off use considering reliability and safety.
Disclaimer: The views and opinions expressed in this article are those of the author – Mr Murugappan V and do not necessarily reflect the views and opinion or position of Dow Chemical International Pvt. Ltd. or its affiliates.
Meet the author
V Murugappan is Instrumentation Engineer at Dow Chemical Interna-tional Pvt Ltd.
His career to date spans 15 years. During this time he has acquired diversified experience, including working on water treatment plants as well as power plant erection and commissioning.
As a senior application engineer with Fisher-Emerson he was responsible for sizing almost 6000 valves including control valves, block valves, desuperheater and critical applications.
His professional interests include valve technology, core Instrumentation, Innovation of wireless automation etc.
Mr Murugappan can be reached on Email: muru17@gmail.com