EMICO’s headquarters in Taiwan, where the company was the first ball valve manufacturer to implement the ISO 9001, API-6D Quality Assurance System.
When it comes to manufacturing ball valves for applications in the oil and gas industry, EMICO (Eayuan Metal Industrial Co., Ltd.) is certainly no novice. For more than three decades, EMICO has been offering customised valve solutions for the upstream, midstream and downstream oil, gas and chemical industries. Its expertise is focused on floating ball valves and trunnion ball valves.
By Jude Jiang, Valve World, Shanghai
Raised in a family environment rich with hand-crafting traditions, EMICO president Mr Jason Lin infuses his passions into traditional manufacturing with modern approaches. As one of the few lumber craft masters in Taiwan, his father and EMICO founder Mr K.C. Lin, had to abandon his beloved vocation in the face of endangered wood species but transformed his industry experience, craftsmanship and entrepreneurial spirit into valve manufacturing. Mr Jason Lin has carried on that mission.
Because of ongoing COVID-19 travel restrictions, the Valve World Asia team conducted an intensive video interview with Mr Jason Lin, covering diverse topics from Lin’s personal story and the entrepreneurship that forged the company to its recent product developments. As Emico has expanded its international business, it has gained worldwide recognition for its brand name, which has become synonymous with valve reliability. As the first ball valve manufacturer in Taiwan
to implement the ISO 9002 Quality Assurance System, EMICO is one of the few local manufacturers with its products extensively used in various challenging oil and gas applications worldwide. Its ball valves are exported to North and South America, Europe (mainly Germany, France and the Netherlands), Japan, Singapore, Australia and the UAE. From local to global, EMICO’s story embodies what forges an excellent valve maker, embedded with a Taiwanese touch – bringing traditional values, pioneering spirit and progressive thought to navigating changes across the eras.
Integrated production system providing casting quality control
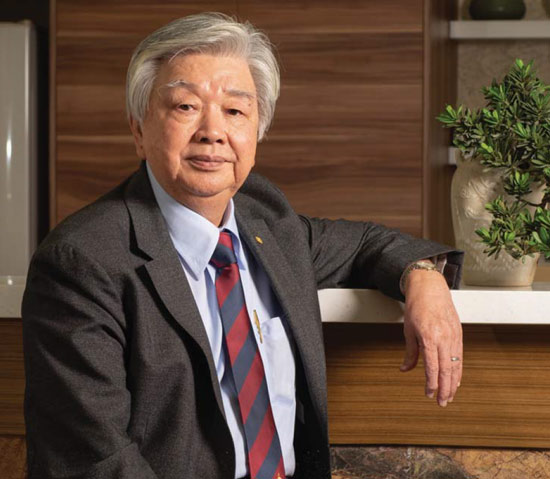
Mr Lin explained that to ensure high-quality product consistency in valve manufacturing, it’s essential for manufacturers to establish an integrated production system; an in-house valve casting foundry, especially for complex casting techniques. EMICO has developed state-of-the-art investment casting processes, and while it is not a straightforward process, Mr Lin added that a little research can go a long way.
EMICO set up its in-house investment casting foundry adjacent to its main valve manufacturing facility back in 2012, but during the first four years, the company dedicated itself to investing in casting technique improvements.
“The most challenging part of investment casting is quality control,” Mr Lin explained. “Even with the same location and climate conditions, the eventual outcomes of molten iron can vary from day to day. In the initial R&D stage, even our very experienced casting experts couldn’t guarantee stable quality.”
Investment casting – also called lost wax casting – is a complex precision casting technique replicating wax patterns to produce complex and intricate valve components. Known for its capability to produce clear net shape, high-dimensional accuracy and intricate design, investment casting has more specific process parameters than other metal casting processes such as sand casting and expandable mould casting. Although it’s a popular technique and widely applied with numerous advantages, the most notable disadvantage is occasional defects which add to the overall cost of the process.
One major defect caused is fine bubbles
in the molten iron that can lower the quality of the product. With numerous trials, the team integrated the casting process with Mould-flow, a wax injection and compression moulding simulation to address manufacturing challenges ahead of time. For instance, how best to pour
the molten iron into the mould to avoid fine bubbles for high-quality casting? This problem can be solved with the aid of prototyping techniques. With such research and planning, manufacturing defects can be reduced before the actual investment casting.
Furthermore, to meet or exceed the required mechanical materials properties of castings, EMICO runs an in-house heat treatment facility for controlled heating, soaking and cooling of the various castings. Through precise heat treatment processes, the hardness of steels can be increased or decreased, internal stresses can be relieved, and tensile strengths can be improved. EMICO has not only mastered the investment casting of the most common valve materials such as carbon steel and stainless steel 304 and 316; the foundry also manufactures high-quality Inconel (Ni-Alloy), Duplex and Alloy 20 (CN7M) castings. These nickel-based alloys are corrosion-resistant, have high strength and are well-suited for service in extreme environments subjected to high pressure and kinetic energy.
Unlocking the power of ball valves
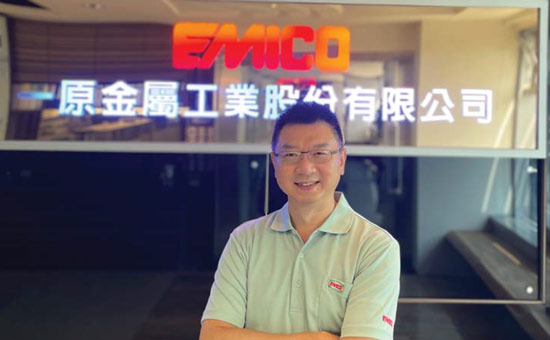
Since the advent of the industrial revolution, oil and gas activities have remained the primary sources of fugitive emissions, leading to significant consequences in economic loss, environmental damage and health risks. Statistics show that approximately 60% of fugitive emissions come from valves, and as much as 80% of the leakage per valve originates from its stem-seal interface.
“Early on, we observed the international market demand for low emissions and were one of the pioneers in exploring low-emission valve production,” Mr Lin said.
To achieve a high standard of valve stem and body seal leakages, ten years ago Mr Lin led his team to obtain the ISO 15848-1 fugitive emission certification for EMICO’s ball valves. The test results were successful, with EMICO gaining the highest class level, for instance, Endurance Class CO3, which requires enduring 2500 mechanical cycles and four thermal cycles. On top of that, EMICO low emission product design covers every critical valve part, including stem seals, soft seals and hard metal seals for both floating ball valves and trunnion ball valves.
In the specific case of EMICO’s design for trunnion ball valves, it incorporates a solid forged ball with top and bottom trunnions fitted with self-lubricated PTFE-impregnated stainless steel bearings. This provides high cycle life and minimal operation torque for pressures up to ASME Class 1500. In the closed position, thrust generated by pressure is supported by the trunnions to reduce seat wear from unexpected surge pressures.
Produced through the company’s own investment casting, EMICO ball valves offer various configurations, including 1-piece, 2-piece and 3-piece with threaded, socket weld, butt weld or flanged ends in Class 150, Class 300, Class 800, Class 900, Class 1500 and Class 2500 ratings. Most EMICO ball valves have low-torque and provide longlasting service.
Product portfolio expansion
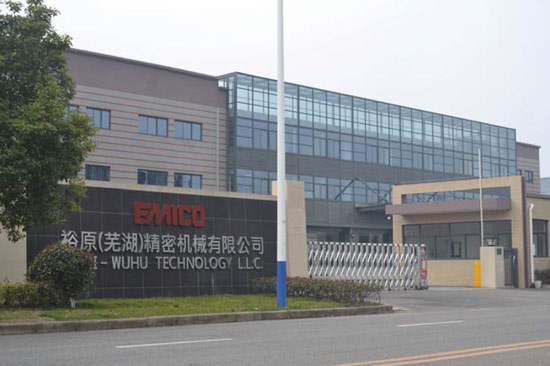
After EMICO first opened its pipeline into the world of ball valve manufacturing in 1984, the company’s high level of product performance rapidly gained acknowledgement from world-class industrial players as well as end users. In 2002, in close collaboration with a well-known Japanese valve manufacturer, EMICO established its second manufacturing base in Shanghai, China and has since been engaged in producing ductile iron gate, global and check valves.
While producing its new line of valve types, EMICO also set high manufacturing standards to align with its Japanese customers’ strict quality requirements. Quality control of each final product is rigidly measured in all aspects, including functionality, leakage and dimensional finish, and each single manufacturing step is also under precise supervision. Choosing the right manufacturing material once again became a matter of vital importance in what shapes a new production line.
Dedicated to the high quality and precision of its valves, EMICO selected the manufacturing approach with ductile iron materials produced by automatic moulding machines. Less brittle than other cast iron, ductile iron, also known as nodular cast iron, does not fracture as easily with impact. Ductile iron valves are known to offer the advantages of wear resistance, high fatigue, shock absorption and good processing performance.
Looking back at the twenty years of collaboration with the Japanese valve manufacturer, in parallel with its continued product portfolio expansion, EMICO has fortified its manufacturing capacities, employed deep learning advanced manufacturing approaches, and continually enhanced its brand influence. Even as the gate, globe, and check valve manufacturing base moved from Shanghai to Wuhu, Anhui province in 2018, EMICO has consistently maintained the same manufacturing approaches, management systems and product quality.
Among a variety of lean manufacturing approaches EMICO has adopted is the One- Piece Flow production method, meaning the one-by-one processing of a product.
“Contrary to the batch production approach, One-Piece Flow emphasises one step at a time and is aimed to achieve a discrete flow of work,” explains Mr Lin. “This approach allows the workforce to stop the production line if one sees a problem, and it certainly helps reduce defect costs, especially when we manufacture bulk orders.”
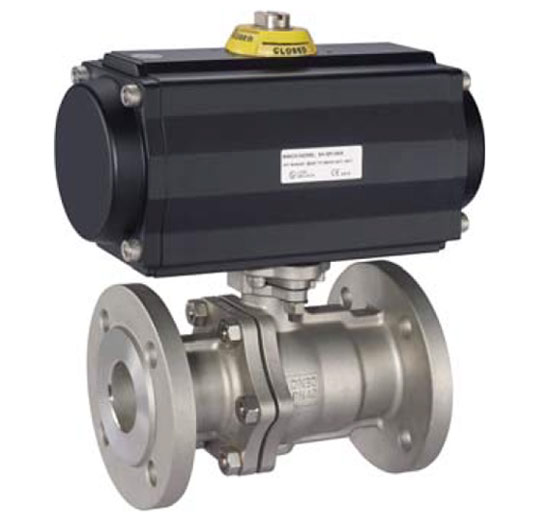
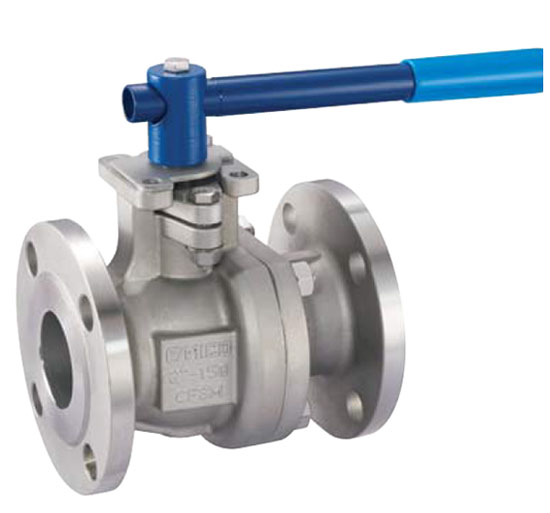
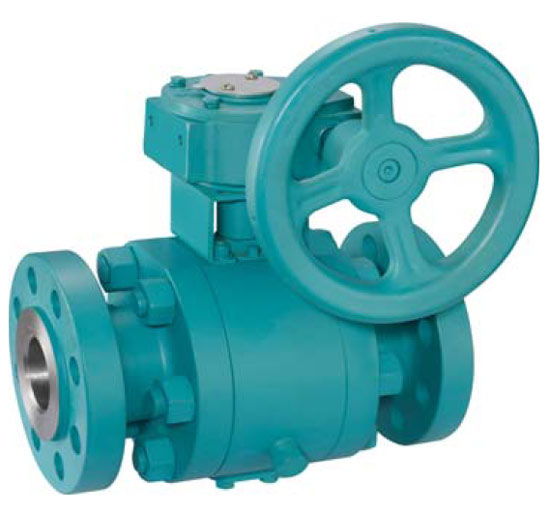
Market recognition
Acknowledged by overseas testing laboratories in the USA, the Netherlands and Australia, EMICO’s partial valve credentials include:
• Fire Safe API 607 Test Certification
• Low-Fugitive Emission Test Certification
• Australian Gas Association AS4617 / AS4629 Class 1 Certification
Meeting various international standards, EMICO has provided services to end-users including:
• Taiwan nuclear power plant (Taiwan)
• CPC Corporation (Taiwan)
• Formosa Petrochemical Corporation (Taiwan)
• A fuel tank refilling station for ExxonMobil at Melbourne Airport (Australia)
• Santos gas producers in Australia (Australia)
• Arabian Industrial Fiber Co. (Saudi Arabia)
• ExxonMobil Shutdown (Singapore)
• CHEVRON detergent expansion project (Singapore)
• PTTGC (Thailand)
• Toshiba Asia Pacific Pte. Ltd. (Malaysia)
• PT Asahimas chemical (Indonesia)
About this Featured Story
This Featured Story is an article from our Valve World Annual Procurement Report 2022 issue. To read other featured stories and many more articles, subscribe to our print magazine. Available in both print and digital formats. DIGITAL MAGAZINE SUBSCRIPTIONS ARE NOW FREE.
“Every week we share a new Featured Story with our Valve World community. Join us and let’s share your Featured Story on Valve World online and in print.”