This article provides an in-depth analysis of essential materials used in pressure relief valve construction, offering valve professionals and engineers critical insights for selecting optimal components to ensure safety, performance and longevity across diverse industrial applications.
By Artur Cardozo Mathias
Pressure relief valves are critical components in many industrial processes, and selecting the right materials for their construction is essential for optimal performance and safety. Different industrial sectors use various fluids with varying levels of corrosivity, necessitating a range of material options for valve construction.
This article examines the materials commonly used in pressure relief valves, focusing on their applications and properties. We will discuss materials for different valve components, including the body, bonnet, internal parts and springs, as well as specific considerations for corrosion resistance and high-temperature applications. While the focus is on pressure relief valves, many of these materials are also applicable to other valve types such as gate, globe, check, ball, plug, butterfly and automatic control valves. By understanding these materials and their applications, valve professionals can make informed decisions to ensure the reliability and efficiency of their pressure relief systems.
Materials for valve body and bonnet
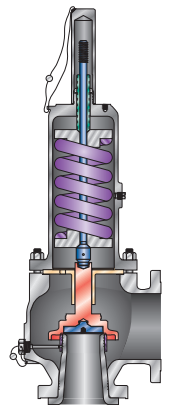
The selection of materials for valve bodies and bonnets depends on the specific application and the fluid properties. Here’s an overview of commonly used materials:
- Cast Iron
- Weldable Cast Steel – B Grading (WCB)
- Carbon steel cast for high temperatures
(WCC) - C5, WC6 and WC9 (alloy steels cast for high temperatures)
- CF8 (cast stainless steel 304) and CF8M (cast stainless steel 316) for moderately corrosive applications
- LCB (carbon steel cast for low temperatures)
- LC3 (alloy steel cast for low temperatures)
For applications with water, steam, compressed air and other less aggressive fluids, cast carbon steel WCB (Weldable Cast Steel – B Grading) serves very well for body and bonnet construction. It’s important to note that components such as the body and bonnet are generally more tolerant
of the corrosive effects of fluids compared to internal components.
For applications with superheated steam, the most commonly used body and bonnet construction materials are C5, WC6 and WC9 (ferritic alloy steels). These chromium and molybdenum-based alloy steels can withstand temperatures as high as 1000°F (538°C), as per ASME B 16.34.
For internal components such as stem, guide and disc holder in high-temperature applications, the most commonly used material is Monel. Monel is suitable for high temperatures as it prevents component locking due to thermal expansion, in addition to extremely corrosive applications.
Materials for internal components
Internal components such as disc, nozzle, guide, disc holder, adjustment rings, adjustment ring locking screw, stem, bellows (when applicable) and spring adjustment screw are typically manufactured from various types of stainless steel. These components require corrosion-resistant materials to prevent movement blockage, which could lead to leaks and valve inoperability.
The materials used for internal components must be at least as corrosion-resistant as those used for the body and bonnet, but never in cast iron or carbon steel. Springs in safety and relief valves use specific materials depending on the application:
- For water, oils, steam, compressed air and other less aggressive fluids: alloy carbon steel AISI 5160 or AISI 6150
- For superheated steam: AISI H12 (tungsten steel) or Inconel® X 750
- For moderately corrosive applications: AISI 302, AISI 316 and AISI 420
- For extremely low temperatures (-450°F to -75°F or -268°C to -60°C): AISI 316
For highly corrosive fluids, materials such as Monel and Hastelloy C are recommended for internal components. All materials used in the construction of safety and relief valves, including body, bonnet, stud and nuts, and internal components, must comply with ASME Code Section II – Part D and ASME Section XIII – 3.3.1.
Types of corrosion in springs
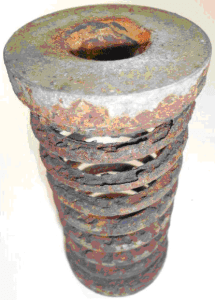
The main types of corrosion found in springs are surface corrosion and stress corrosion. Both can significantly impact valve performance and safety.
Surface corrosion can weaken the spring, reducing the valve’s opening pressure. This weakening can occur when incorrect materials are selected for the application, particularly when exposed to high temperatures and corrosive fluids. This occurs due to a reduction in the wire diameter, which weakens the spring.
Stress corrosion cracking is more difficult to detect before spring failure occurs. To mitigate this risk, manufacturers must select springs with:
- Chemical compatibility with the process fluid
- Correct hardness
- Appropriate heat treatment
These factors affect the spring’s resistance to stress corrosion cracking. It is recommended to replace the spring and/or change its construction material when corrosion has consumed more than 1.5% of the wire diameter. To enhance corrosion resistance, springs can receive a superior surface finish for protection against oxidation.
Resilient seats
Resilient seats are “O” ring sealing rings that enhance valve tightness, allowing for effective sealing at 95% of the valve opening pressure on valves adjusted from 15 psig (1.0 barg). Resilient PTFE seats are recommended for set pressures from 100 psig (6.9 barg). Specifications for resilient seats are recommended for the following applications:
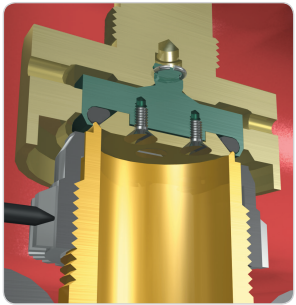
- Fluids that are difficult to confine, such as light hydrocarbon, anhydrous ammonia, helium or hydrogen, and others
- Toxic or flammable gases
- Operating pressure very close to the opening pressure
- Installations subject to vibrations
- Fluids containing solid particulates in suspension
- Applications subject to vacuum
- Fluids that may freeze during relief through the valve, such as certain gases
- Stresses in discharge piping caused by inadequate support
The application of resilient seats is constrained by pressure, fluid temperature, valve nozzle area and chemical compatibility with the process fluid. When the valve opening pressure increases, the nozzle passage area to be selected must be smaller. For processes requiring high opening pressure and high flow capacity, it is advisable to specify, size and install multiple valves with smaller orifices.
Common materials for resilient seating applications include Buna-N, Perbunan, Silicone, Viton, Kalrez, Ethylene Propylene, Neoprene, Nitrile and PTFE. These materials are suitable for temperatures around -150°F to 450°F (-101°C to 232°C), depending on the material, setting pressure and valve nozzle area, while PTFE can be applied at temperatures up to 500°F (260°C). Maximum application temperature varies depending on resilient seat material, nozzle area and valve setting pressure.
For valves with set pressures up to 500 psig (34.5 barg), the elastomer hardness should be 70 Shore. For set pressures between 501 psig and 1500 psig (34.54 barg to 103.42 barg), the elastomer hardness should be 90 Shore.
It is important to note that resilient seats may have reduced lifespan under stress due to degradation caused by temperature, aging or expansion. For fluids containing solid particulates, especially when the resilient seat material cannot withstand the process fluid’s pressure and temperature, and depending on the valve nozzle area, it is recommended to use disc and nozzle seating surfaces coated with Stellite®.
Balanced pressure relief valves with bellows
In applications where the valve discharges into a header, it is recommended to specify a balanced valve with bellows, in addition to nullifying the effects of back pressure on the opening pressure value and flow capacity of the valve, also when the fluid from the header discharge system (discharge closed) or the system itself protected by the valve is corrosive or has a tendency to crystallize, polymerize or corrode the valve body, bonnet and internal components. For fluids with these characteristics, the bellows performs others two main functions:
- Isolating the clearance between the disc holder shaft and the valve guide hole
- Isolating all components above the bellows (housed inside the bonnet)
By using a bellows with an isolation function, components housed inside the bonnet (including the bonnet itself) can be manufactured from materials that are less resistant to corrosion. This approach can significantly reduce the final cost of the valve and installation.
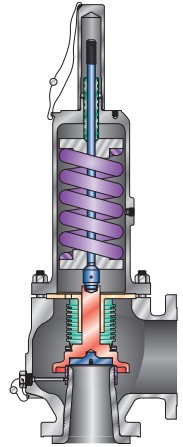
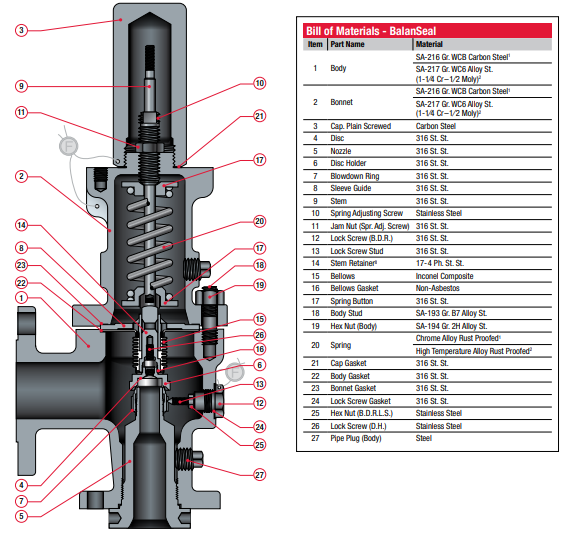
The most common material for bellows construction is AISI 316 L stainless steel. However, it is important to note that the NACE MR 0175 standard requires bellows to be manufactured from Inconel® X-625 for applications involving hydrogen sulphide (H2S).
Recent developments in valve technology have introduced balanced diaphragms made from elastomers as an alternative to traditional metal bellows. These elastomeric diaphragms can offer advantages in certain applications, providing flexibility in design, greater flow capacity and potentially reducing costs.
Construction materials for studs and nuts
The construction materials for studs and nuts that clamp the bonnet to the body are typically specified in accordance with industry standards. Studs are commonly made from ASTM A 193 Gr. B7 material, while nuts are usually ASTM A 194 Gr. 2H. The studs are constructed from AISI 4140 steel, and the nuts from AISI 4130 steel. This difference in materials results in different hardness values between the components, preventing locking between them.
When the body and bonnet are manufactured from corrosion-resistant materials such as CF8 or CF8M, the studs and nuts do not necessarily need to be resistant to fluid corrosion. This is because these components are external to the valve and, in theory, do not come into contact with the process fluid.
However, if the external environment is corrosive, alternative materials may be specified for the studs and nuts. In such cases, ASTM A 193 Gr. B8M for studs and ASTM A 194 Gr. 8M for nuts are commonly used, providing guaranteed corrosion resistance for these external components.
Conclusions
Material selection for pressure relief valve components is critical to ensure safe and reliable operation. All components must meet ASME Section II code requirements and ASME Section XIII – 3.3.1, demonstrate chemical compatibility with the process fluid and comply with pressure and temperature limits.
When choosing materials, it is essential to prioritise corrosion resistance. Corrosion in valves can manifest in various forms, including pitting, component failure and the accumulation of corrosive residues. These issues can interfere with the movement of internal parts and potentially lead to valve malfunction.
The selection of appropriate materials helps prevent:
- Deterioration of valve components
- Blockage of moving parts
- Compromised valve performance
By carefully considering the specific application requirements and potential corrosion mechanisms, engineers can select materials that offer optimal performance and longevity. This approach ensures the pressure relief valve maintains its integrity and functionality throughout its service life, contributing to overall system safety and reliability. Therefore, the user is responsible for providing the process fluid data to the valve manufacturer for the correct selection of its construction materials.
About the author
Artur Cardozo Mathias is an Industrial Mechanical Technician and Chemical Technician, Member of ISA and consultant. He has been active since 1985 in the maintenance, inspection, specification and sizing of valves. With extensive experience in the field, Artur provides training and technical courses to share his knowledge and expertise with others in the industry. He is also the author of the book “Válvulas: Industriais, Segurança e Controle” (Valves: Industrial, Safety and Control), which serves as a valuable resource for professionals working with valves in various applications.
About this Technical Story
This Technical Story is an article from our Valve World Magazine, September 2024 issue. To read other featured stories and many more articles, subscribe to our print magazine. Available in both print and digital formats. DIGITAL MAGAZINE SUBSCRIPTIONS ARE NOW FREE.
“Every week we share a new Technical Story with our Valve World community. Join us and let’s share your Technical Story on Valve World online and in print.”