ePTFE tap is an adaptable, robust material which offers versatility and effectiveness in a range of sealing applications.
By Angelica Pajkovic, Florian Werner, Julia Köder, and Josmar Cristello – Teadit
Expanded polytetrafluoroethylene (ePTFE) tape is a robust and adaptable sealing material. The choice between mono-axial and multi-directional ePTFE tape is a crucial decision that can significantly influence sealing performance. Each type has distinct advantages that cater to specific application needs, making a well-informed selection essential.
Understanding these differences is key, as the correct choice can enhance sealing, minimise maintenance costs and prolong the service life of equipment—factors that are integral to maintaining process safety and reliability.
What are ePTFE tapes
While several industries utilise ePTFE tapes, the benefits of this sealing technology are often overlooked. Although one-piece cut gaskets are an ideal choice in many instances, there are several scenarios where ePTFE tape is the chosen sealing method.
Made from 100% virgin PTFE that has been expanded or stretched in either one or two directions, ePTFE gasket-tapes exhibit outstanding chemical resistance, making them suitable for use with various aggressive chemicals and corrosive substances. Their low friction coefficient reduces wear and allows components to move freely, which is crucial for applications with dynamic parts.
Additionally, ePTFE gasket-tapes are non-reactive and inert, ensuring compatibility with sensitive environments such as food processing or pharmaceuticals where contamination must be avoided.
These tapes, which typically come with a pressure-sensitive adhesive strip on one side, are available in various sizes and spool lengths. They have the ability to conform to irregular surfaces, seal narrow or uneven spaces, and be easily used in flanges in dynamic systems where there’s movement, such as a shaft or stem passing through the flange.
One of their key advantages is that they can be applied without needing to remove components like shafts or stems. Their flexibility allows them to be wrapped around these elements, ensuring a reliable seal without the need for complete disassembly, making it especially convenient for equipment where a shaft passes through the flange.
Given their versatility and effectiveness in various applications, it is essential to consider the different types of ePTFE gasket-tapes available, as well as the unique value that each provides.
Types of tapes
Expanded PTFE gasket-tapes are available in two main styles: mono-axial and multi-directional. Each form has a distinct advantages that makes it suitable for different applications.
Mono-axial ePTFE tape
Mono-axial ePTFE tape, such as Teadit’s 24B Tape, is extremely conformable, making it very easy to install in any flange, including those with complex geometries. Often referred to as joint sealant, its flexibility allows it to be shaped and applied with minimal effort, ensuring a reliable seal in various configurations.
As mono-axial ePTFE tape is expanded in only one direction, it naturally spreads laterally (increases in width) when compressed, typically expanding to 200-300% of its original width. This characteristic should be factored into sizing and installation to ensure a proper fit, as shown in Figure 1. Mono-axial ePTFE gasket tape remains an ideal solution for applications where ease of installation and adaptability are crucial.
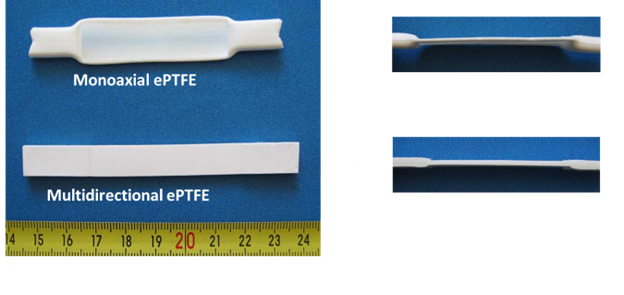
Multi-directional ePTFE tape
Multi-directional ePTFE tape offers excellent strength and stability because it is expanded in two directions. This bi-axial orientation provides more consistent compression without a significant change in width, making it ideal for applications where dimensional stability is crucial. For example, Teadit’s 25BI tape has a unique manufacturing process that results in high tensile strength in both the longitudinal and cross directions. As a result, the tape’s width does not change significantly under compression, see Figure 1. This is in stark contrast to many expanded PTFE tapes.
Glass-lined piping and equipment often have warped surfaces with significant variations that need to be compensated for by the gasket. In these cases, multi-directional ePTFE tape is an excellent solution. Its ability to be layered (shimming) in specific areas of the flange allows it to accommodate variable warping and uneven surfaces, ensuring a reliable seal. Additionally, its resistance to creep at high temperatures makes it ideal for protecting the glass lining and maintaining an effective seal.
Customisation and versatility
One of the primary advantages of ePTFE tape is its versatility in accommodating a wide range of flange shapes and sizes. This reduces the necessity of maintaining an inventory of multiple pre-cut gasket sizes. A single roll of tape can be used for various dimensions and complex configurations. This adaptability is particularly valuable for maintenance engineers, where time constraints are often critical during repairs. For flanges of dynamic applications, such as pumps, where internal components can pose challenges during installation, ePTFE tape provides a highly flexible sealing option. It can be applied without the need to dismantle intricate internal parts, thus significantly reducing downtime.
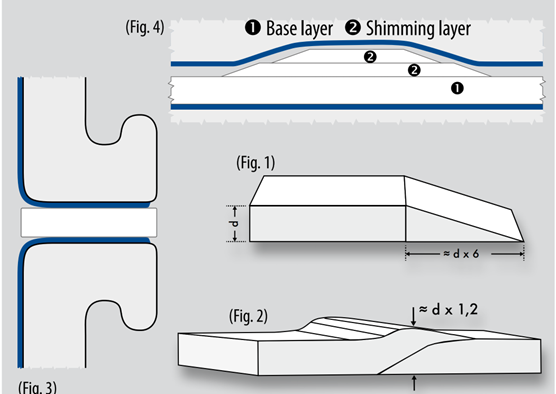
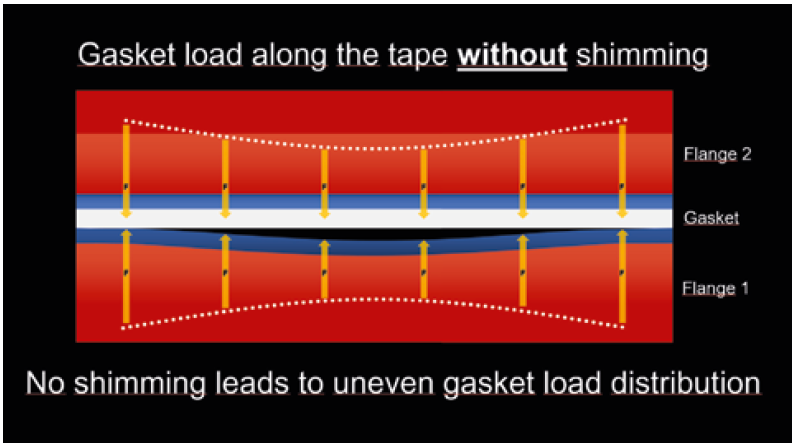
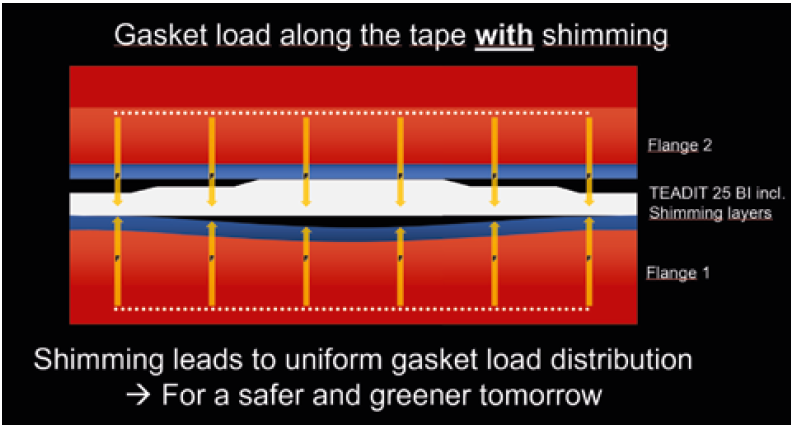
While ePTFE gasket-tape’s unique flexibility greatly enhances its usability in various applications, understanding the installation techniques—particularly the distinctions between mono-axial and multi-directional tape—is also essential for achieving optimal sealing performance.
A closer look at installation processes
Installation Instructions for Mono-axial gasket-tape, such as Teadit style 24B:
- The sealing area must be clean and free of grease. Damaged parts must be repaired or replaced. All bolts and nuts should be well greased.
- Gradually remove the backing paper from the adhesive strip and affix sealant tape inside the bolt circle, beginning at a bolt hole.
- Complete the gasket by overlapping both ends in front of a bolt either crossed (approximately 20 mm, 1 inch – Image 1, Fig. 1) or straight with a cut in skived manner (Image 1, Fig. 1.1).
- Torque bolts in the correct sequence to the desired load. Recommended load: 25 to 30 N/mm2.
- If the sealing surfaces are damaged and uneven, use the next bigger joint sealant tape size.
- For particularly difficult sealing problems (flange rotation, vibrations or similar) two strips of tape can be used (Image 1, Fig. 2).
- To avoid distortion of thin flanges and/ or to avoid damage to stress-sensitive connections, apply Teadit 24B in an irregular pattern as shown in Image 1, Fig. 3.
Installation Instructions for multi-directional tape, such as Teadit 25BI:
- The sealing area must be clean and free from grease. Damaged parts must be repaired or replaced. All bolts and nuts should be well greased.
- Cut the beginning of the tape with a sharp knife in a skived manner (Image 2, Fig. 1).
- Remove the backing paper from the adhesive strip and stick the tape onto the sealing area, beginning at a bolt hole.
- Join the two ends as shown in the sketch (Image 2, Fig. 2). The bolts should be torqued in a star pattern. This should be done in three stages, torquing to approximately 25% of the total required torque value with each round. The fourth and final adjustment should be made in a circular direction to the full torque value.
- Two tape strips can be used for particularly difficult sealing problems (flange rotation, vibrations, or similar) (Image 2, Fig. 3).
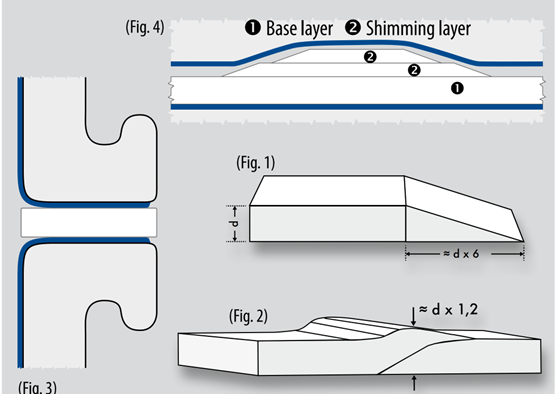
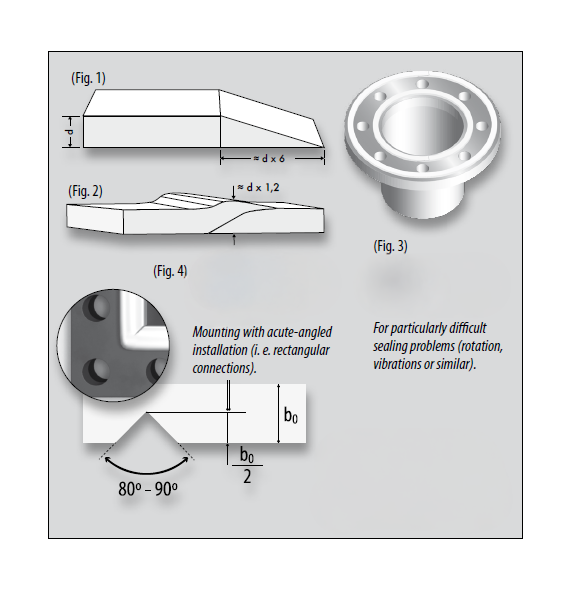
Final thoughts
Expanded PTFE gasket-tape offers significant benefits across various industrial applications, particularly when custom dimensions or emergency repairs are required. The choice between mono-axial and multi-directional ePTFE tape depends on the application’s specific needs.
Mono-axial tape provides flexibility and ease of installation, while multi-directional tape excels in environments where strength and dimensional stability are paramount. By understanding each ePTFE tape’s unique properties, engineers can select the right one for their specific sealing requirements, improving both efficiency and safety.
Reference
1. Installation Manual 25BI.pdf
About the author
Angelica Pajkovic is a Client Specialist at Teadit, with a particular focus on technical content development. Hailing from Toronto, Canada, she has over six years of experience in the industrial industry. In her previous role as Editor- in-Chief at an industrial B2B publishing company, she gained a rounded understanding of the challenges, interests, and business relationships in the industrial sector. For more information, please contact Angelica via email at: angelicap@teadit.com.
About the experts
Florian Werner is an expert in materials, production processes and sealing products, working as Head of Sales and Application Engineering for Teadit Group. Based out of Austria, he holds a Master of Science from the University of Applied Sciences Upper Austria in Material and Processes. With over 15 years of experience in the industry, Florian began his career in several machining and mechanical roles before joining Teadit as Head of R&D Europe. After moving to Head of Application Engineering, he progressed to his current role overseeing both Sales and Engineering.
Josmar Cristello is a Mechanical Engineer with a post-graduate degree in Data Science and Big Data from the Pontifical Catholic University and a Master of Science from the University of Calgary, where his research focused on AI/ML-based leak detection in pipelines. He specialises in energy transition, software development and critical sealing solutions, and he currently works as an applications engineer.
Julia Köder is an Application Engineer at TEADIT International Produktions GmbH. Her responsibilities include providing technical consultation to clients, conducting training sessions and offering support for technical inquiries. Before taking on this role in July 2022, Julia worked as a project engineer in the automotive section, a position she held from October 2019 after completing her master’s degree in Mechanical Engineering.
About this Technical Story
This Technical Story is an article from our Valve World Magazine, February 2025 issue. To read other featured stories and many more articles, subscribe to our print magazine. Available in both print and digital formats. DIGITAL MAGAZINE SUBSCRIPTIONS ARE NOW FREE.
“Every week we share a new Technical Story with our Valve World community. Join us and let’s share your Featured Story on Valve World online and in print.”