ExxonMobil is planning to establish an impressive blue hydrogen hub in the Houston Shipping Channel (Baytown, Texas). Needless to say, the facility will also incorporate carbon capture and storage, according to ExxonMobil one of the largest CCS-projects worldwide.
By Lucien Joppen
ExxonMobil’s plans involve a 10 million tonne per annum CCS-facility, which will form part of wider plans for an up to 100 million tpa CCS hub (projection for 2040) in the Houston Shipping Channel. The production capacity of the blue hydrogen facility would be in the area of 1 billion cubic feet per day.
The US multinational intends to use the blue hydrogen produced by the project as fuel at its Baytown olefins plant, which it claims could reduce the integrated complex’s Scope 1 and 2 CO2 emissions by up to 30 per cent. The company added that surplus hydrogen production and excess storage capacity at the CCS-facility would also be made available to nearby industry.
“Hydrogen has the potential to significantly reduce CO2-emissions in vital sectors of the economy and create valuable, lower-emissions products that support modern life,” said Joe Blommaert, president of ExxonMobil Low Carbon Solutions. “By helping to activate new markets for hydrogen and carbon capture and storage, this project can play an important part in achieving America’s lower-emissions aspirations.”
Cross-industry effort
ExxonMobil labels the production and storage facility as a “game changer” in two ways due
its capacity to reduce CO2-emissions for the company and other large petrochemical players in the area. The proposed CCS hub is also being backed by eleven major petrochemical players in the Houston area.
“The carbon capture and storage facility would mark ExxonMobil’s initial contribution to the Houston CCS hub concept we announced last year”, ExxonMobil’s spokesman stated. “Today, this concept has evolved into a cross-industry effort to capture and store up to 100 million metric tons of CO2 per year by 2040 from Houston-area power plants, refineries and petrochemical facilities, including our Baytown site. Reducing our emissions at Baytown would benefit our customers by lowering the carbon footprint of the products we make there, including the modern polymers found in everything from medical equipment to cell phones and electric cars. We also plan to make this low-carbon hydrogen available to other Houston-area industrial facilities, to help them reduce their emissions. So you can see why this project would be a game changer. It would enable us to reduce our greenhouse gas emissions at Baytown, help our customers reduce their emissions, and provide additional solutions to area industries. We expect to make a final investment decision in two or three years, subject to supportive government policy, necessary regulatory permits and market conditions.”
Range of solutions needed
Hydrogen is regarded to play a pivotal role to reduce greenhouse gas emissions for the hard-to-decarbonize sectors such as the petrochemical industry. The International Energy Agency sees hydrogen and hydrogen-based fuels meeting 10 percent of global energy needs as part of its “Net Zero by 2050” scenario. Along with carbon capture and storage, it will be critical to achieving societal net-zero carbon greenhouse gas emissions goals. “Governments can accelerate investments in these technologies by putting in place supportive policies, such as a price on carbon, which can help reduce costs and build new markets”, ExxonMobil stated. “No single technology will get the world to net zero while maintaining the living standards today’s energy system supports. Experts agree we’ll need a range of solutions, including hydrogen and carbon capture and storage. ExxonMobil has deep expertise in both and looks forward to helping advance these and other technologies to create sustainable solutions that improve quality of life and meet society’s evolving needs.”
Houston CCS hub
In 2021, eleven companies (Calpine, Chevron, Dow, ExxonMobil, INEOS, Linde, LyondellBasell, Marathon Petroleum, NRG Energy, Phillips 66 and Valero) expressed interest in supporting the ‘Houston hydrogen hub’.
If CCS technology is fully implemented at the Houston-area facilities these 11 companies operate, nearly 75 million metric tons of CO2 could be captured and stored per year by 2040. There are ongoing discussions with other companies that have industrial operations in the area to add even more CO2 capture capacity. They could announce their support at a later date and add further momentum toward the city of Houston’s ambitions to be carbon neutral by 2050.
“Houston can achieve our net zero goals by working together, and it’s exciting to see so many companies have already come together to talk about making Houston the world leader in carbon capture and storage,” said Sylvester Turner, Mayor of Houston. “We’re reimagining what it means to be the energy capital of the world, and applying proven technology to reduce emissions is one of the best ways to get started.”
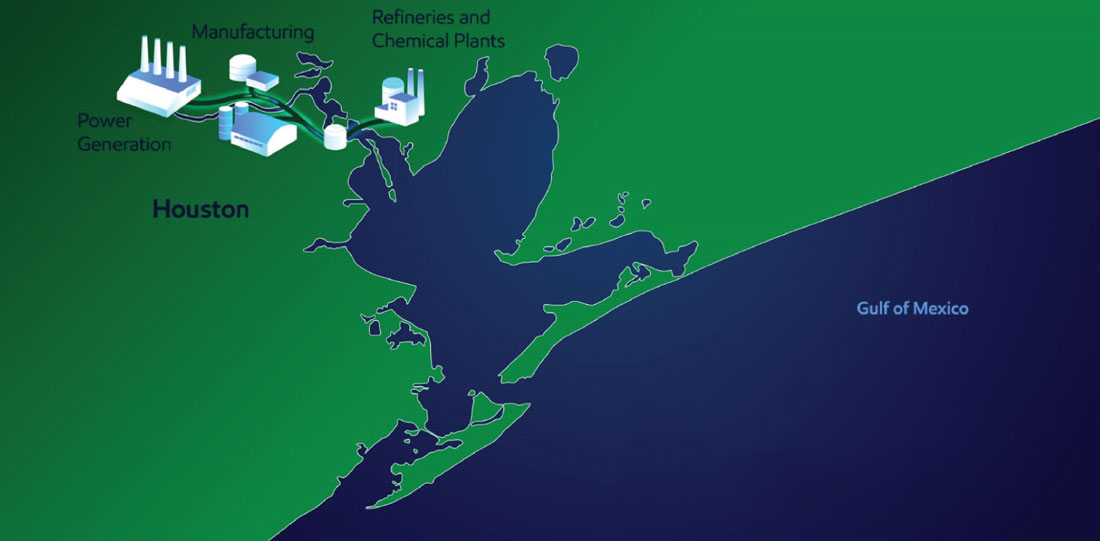
Valve selection: material challenges
Tiny hydrogen atoms can penetrate the crystal structure of solid metal and remain there. This effect leads to increased pressure and internal stresses without any corresponding increase in the strength of the material. Hydrogen absorption can make the metal walls brittle, which may lead to crack formation and eventual failure.
Furthermore, the tensile strength, toughness and ductility of the metal are reduced to a point that can result in violating the elongation-at-break requirement specified in the European Pressure Equipment Directive 2014/68 / EU.
The use of special high-strength materials that often work in other challenging situations, unfortunately does not solve this problem.
On the contrary, these materials are even more vulnerable to hydrogen embrittlement. The lowest sensitivity to hydrogen embrittlement is found in face-centered cubic metal grids such as those in austenitic steel (e.g. 316 / 316L) or aluminum.
But even with these materials, it is still important to avoid other pitfalls. In the case of 316 / 316L, for example, the hydrogen compatibility depends on the nickel content. This dependency is most pronounced between room temperature and approximately -40°C. To account for this effect, a steel with appropriate nickel content must be selected (if available on the market). The stress level may also be lowered through a reduced utilization of the component as done also with unalloyed steels.
It is also important to ensure that non-metallic valve materials such as seals and lubricants are compatible with hydrogen. A list of recommendations can be found in the standards or databases mentioned above (Sandia, ISO / TR, SAE).
Source: AS Schneider, Thomas Weisschuh (2022)
Stepping stone or road block?
Meanwhile, blue hydrogen production has received a lot of criticism. Recently, a peer reviewed article ‘How green is blue hydrogen’ (Howarth/Jacobson, Energy Science and Engi-neering, 2021) concluded that the greenhouse gas footprint of blue hydrogen is more than 20 percent greater than burning natural gas or coal for heat and some 60 percent greater than burning diesel oil for heat. The authors also mentioned that there are concerns about the long-term viability of holding it underground. On the other hand, other research institutes, such as Dutch TNO, view blue hydrogen production as a stepping stone for green hydrogen production. “Green hydrogen is currently not available in large volumes and remains expensive. Blue hydrogen offers a cheaper alternative that prevents emissions because of CCS”, TNO states.
“Blue hydrogen currently holds the better cards for a fast and affordable energy transition. (…) The high cost of the electrolysers makes the technology less attractive for the time being.” Needless to say, natural gas prices have become excessively high due to geopolitical tensions in Eastern Europe. These price fluctuations definitely impact the economical viability of blue hydrogen.”